Food importing USA consulting is a critical field, serving as the gateway for diverse culinary experiences to grace American tables. This involves a multifaceted process, spanning from regulatory compliance and food safety to supply chain management and market analysis. The U.S. market’s appetite for imported goods continues to grow, creating both opportunities and challenges for businesses venturing into this arena.
Understanding the nuances of this process is paramount for success. This comprehensive guide will delve into the intricacies of food importing, offering insights into regulations, best practices, and strategic considerations for businesses seeking to thrive in the U.S. market. We will explore the various aspects of food importing, from initial market research to final product distribution.
Overview of Food Importing to the USA
The United States boasts a vast and complex food import landscape, a critical component of its diverse and abundant food supply. Understanding this intricate system, from the origins of imported goods to their impact on the American economy, is crucial for businesses involved in the food industry. This overview provides a comprehensive look at the current state of food imports into the U.S., detailing key aspects such as source countries, product categories, economic influences, and regulatory oversight.
Major Source Countries and Product Categories
The U.S. imports food from a multitude of countries, with the origin of these imports reflecting global agricultural production and trade dynamics. Several nations consistently rank as leading suppliers, and the types of products imported are equally diverse, catering to American consumer preferences and seasonal demands.
- Canada: Canada is a significant source for a variety of products, including fresh and frozen vegetables, beef, and grains. Its proximity and strong trade relationships with the U.S. contribute to its prominent role.
- Mexico: Mexico is a major supplier of fresh produce, such as tomatoes, avocados, and berries, particularly during the winter months. The country’s agricultural sector is well-suited to meeting U.S. demand.
- European Union: The EU exports a wide range of food products to the U.S., including processed foods, wines, cheeses, and specialty items. The quality and reputation of European food brands are highly valued by American consumers.
- China: China supplies the U.S. with various food products, including processed fruits and vegetables, seafood, and certain ingredients. The volume of imports from China underscores its substantial agricultural capacity and manufacturing capabilities.
- Other Key Players: Other important source countries include Brazil (beef, coffee), India (spices, seafood), and various nations in South America and Southeast Asia, each contributing specific products to the U.S. food supply.
The types of food products imported are extensive, ranging from staples to specialized items.
- Fresh Produce: Fruits and vegetables represent a substantial portion of imports, particularly during off-seasons when domestic production is limited.
- Seafood: The U.S. imports a large amount of seafood, including shrimp, tuna, and salmon, to meet consumer demand and supplement domestic catches.
- Meat and Poultry: Imports of beef, pork, and poultry are essential for the U.S. market, with Canada and Mexico being significant sources.
- Processed Foods: A wide variety of processed foods, including canned goods, snacks, and beverages, are imported to satisfy consumer preferences for diverse tastes and convenience.
- Specialty Products: The U.S. imports specialty products, such as coffee, tea, spices, and ethnic foods, to cater to a diverse population and enhance culinary experiences.
Economic Impact of Food Imports
Food imports have a multifaceted impact on the U.S. economy, affecting job creation, consumer prices, and the overall trade balance. Understanding these economic effects is crucial for assessing the benefits and challenges associated with food imports.
- Job Creation: Food imports support jobs in various sectors, including transportation, warehousing, distribution, and retail. Ports and distribution centers throughout the country create employment opportunities.
- Consumer Prices: Imports can help stabilize or reduce consumer prices by increasing the supply of food and providing competition for domestic producers. This can lead to lower costs for consumers and greater purchasing power. For instance, the availability of imported produce during the winter months keeps prices down, making fresh fruits and vegetables accessible year-round.
- Trade Balance: Food imports contribute to the U.S. trade deficit, as the value of imported food exceeds the value of exported food. However, this trade imbalance is partially offset by exports in other sectors, and it is often viewed as a necessary element of a healthy, diverse economy.
- Impact on Domestic Producers: While imports can benefit consumers, they can also create competition for domestic food producers. Domestic producers may need to adapt by improving efficiency, focusing on specialized products, or seeking government support to remain competitive.
Regulatory Bodies Involved in Overseeing Food Imports
The safety and quality of imported food are of paramount importance, and several regulatory bodies play a critical role in ensuring that imported food meets U.S. standards. These agencies work together to protect public health and ensure that imported products are safe for consumption.
- Food and Drug Administration (FDA): The FDA is the primary regulatory body responsible for overseeing the safety of imported food. It enforces regulations related to food safety, labeling, and ingredient standards. The FDA conducts inspections of foreign food facilities, reviews import entries, and monitors food products for potential hazards. The FDA’s import program is a crucial element of food safety.
- United States Department of Agriculture (USDA): The USDA regulates the import of meat, poultry, and egg products. It conducts inspections of imported products to ensure they meet U.S. standards for safety, quality, and labeling. The USDA also works to prevent the introduction of plant and animal pests and diseases through imported food.
- Customs and Border Protection (CBP): CBP plays a vital role in facilitating the import of food products by enforcing import regulations and collecting duties and taxes. CBP works closely with the FDA and USDA to ensure that imported food complies with all relevant requirements. CBP officers inspect food shipments, verify documentation, and conduct examinations to ensure compliance.
- Other Agencies: Other agencies, such as the Environmental Protection Agency (EPA) and the Centers for Disease Control and Prevention (CDC), also play supporting roles in regulating food imports. The EPA focuses on pesticide residues, while the CDC monitors for foodborne illnesses.
The FDA’s Foreign Supplier Verification Program (FSVP) is a key initiative aimed at ensuring that importers verify that their foreign suppliers are producing food in compliance with U.S. food safety standards.
Regulatory Compliance for Food Imports
Navigating the regulatory landscape is crucial for successfully importing food products into the United States. The Food and Drug Administration (FDA) and the United States Department of Agriculture (USDA) are the primary agencies overseeing food safety and labeling standards. Importers must meticulously adhere to these regulations to ensure their products are safe for consumption and compliant with U.S. law. Failure to comply can result in product detention, rejection, or even legal penalties.
Labeling Requirements
Food labels in the United States must provide specific information to consumers. This information is regulated by both the FDA and the USDA, depending on the food product. Proper labeling ensures consumers have accurate information about the product’s contents, nutritional value, and origin.
- Statement of Identity: The label must clearly and prominently state the common or usual name of the food product. For example, if importing a type of jam, the label should clearly state “Strawberry Jam” or “Apricot Preserve.”
- Net Quantity of Contents: The label must state the net weight, volume, or count of the product in both U.S. customary and metric units. For instance, a can of tomatoes might be labeled as “14.5 ounces (411 grams).”
- Nutrition Facts Panel: This panel provides detailed information about the product’s nutritional content, including calories, fat, carbohydrates, protein, vitamins, and minerals. The format is standardized by the FDA.
- Ingredient List: All ingredients must be listed in descending order of predominance by weight. This includes any additives, colorings, or flavorings. Common allergens must be clearly identified.
- Name and Place of Business of the Manufacturer, Packer, or Distributor: The label must include the name and address of the responsible party. This allows consumers to contact the company with questions or concerns. If the product is imported, the label must indicate the name and address of the importer or distributor.
- Country of Origin: The label must clearly state the country where the food product was manufactured or produced.
- Allergen Information: The Food Allergen Labeling and Consumer Protection Act of 2004 requires clear labeling of the “major food allergens,” including milk, eggs, fish, shellfish, tree nuts, peanuts, wheat, and soybeans. This information must be prominently displayed on the label.
Ingredient Standards
The FDA and USDA have established standards for the ingredients used in food products. These standards ensure that ingredients are safe, properly used, and accurately represented on the label. Importers must be aware of these standards to avoid importing products with prohibited or non-compliant ingredients.
- Food Additives: The FDA regulates the use of food additives, which are substances added to food to enhance its flavor, color, texture, or preservation. All food additives must be approved by the FDA and used within specified limits.
- Color Additives: Color additives are also regulated by the FDA. Only approved color additives can be used in food products. These additives must be safe and used in accordance with FDA regulations.
- GRAS (Generally Recognized As Safe) Substances: Certain substances are considered “generally recognized as safe” (GRAS) by qualified experts. These substances do not require premarket approval by the FDA. However, the use of GRAS substances must still comply with FDA regulations.
- Prohibited Substances: The FDA prohibits the use of certain substances in food products. Importers must ensure that their products do not contain any prohibited substances.
- Standards of Identity: The FDA has established standards of identity for certain food products, such as jams, jellies, and canned fruits. These standards specify the ingredients, processing methods, and labeling requirements for these products.
Safety Protocols
Food safety is a paramount concern for the FDA and USDA. Importers must implement robust safety protocols to ensure that their products are safe for consumption and free from contamination. These protocols include measures to prevent foodborne illnesses and to protect against intentional adulteration.
- Food Safety Modernization Act (FSMA): The FSMA is a landmark food safety law that significantly enhanced the FDA’s authority to regulate the food supply. Importers must comply with FSMA regulations, including the Foreign Supplier Verification Program (FSVP) and the Preventive Controls for Human Food rule.
- Preventive Controls: Importers must implement preventive controls to identify and address potential hazards in their food products. These controls may include measures to prevent contamination, control allergens, and ensure proper sanitation.
- Hazard Analysis and Critical Control Points (HACCP): HACCP is a systematic approach to food safety that identifies and controls hazards at critical points in the food production process. While not always mandatory, HACCP plans are often recommended or required for specific food products.
- Traceability: Importers must be able to trace their food products back to their source. This allows for rapid identification and removal of contaminated products in the event of a foodborne illness outbreak.
- Good Manufacturing Practices (GMPs): GMPs are a set of guidelines for the proper manufacturing, processing, packing, and holding of food products. Importers must ensure that their foreign suppliers adhere to GMPs.
Checklist for Importers: FDA and USDA Requirements
This checklist provides a summary of key requirements for food importers to ensure compliance with FDA and USDA regulations. It’s important to consult the latest regulations and seek expert advice to ensure full compliance.
Requirement | Description | Compliance Steps |
---|---|---|
Facility Registration | Foreign food facilities that manufacture, process, pack, or hold food for human or animal consumption in the U.S. must register with the FDA. | Register the facility with the FDA. This includes providing the facility’s name, address, and contact information. |
Prior Notice | Prior notice of imported food shipments must be provided to the FDA. | Submit prior notice to the FDA before the food arrives in the U.S. This notice includes information about the product, the shipper, and the importer. |
Labeling Compliance | Food labels must comply with all FDA and USDA labeling requirements. | Ensure that all labels meet the requirements for statement of identity, net quantity of contents, nutrition facts panel, ingredient list, allergen information, name and address of the responsible party, and country of origin. |
FSVP Compliance | Importers must verify that their foreign suppliers are producing food in compliance with U.S. food safety standards. | Develop and implement a Foreign Supplier Verification Program (FSVP). This includes conducting hazard analysis, evaluating supplier performance, and conducting on-site audits. |
Preventive Controls | Importers must ensure that their products are manufactured under preventive controls to address potential hazards. | Verify that the foreign supplier has implemented preventive controls to prevent food safety hazards. This may include reviewing the supplier’s food safety plan and conducting inspections. |
Ingredient Standards | Ensure all ingredients meet FDA and USDA standards. | Verify all ingredients are approved for use and comply with all regulations regarding additives, colorings, and prohibited substances. |
Permits and Licenses | Obtain any necessary permits or licenses. | Determine if any specific permits or licenses are required for the imported food product. |
Recordkeeping | Maintain records of all import activities, including documentation of compliance with FDA and USDA regulations. | Maintain accurate records of all import activities, including supplier information, test results, and any corrective actions taken. |
Permits and Licenses
Obtaining the necessary permits and licenses is a crucial step in the food importation process. The specific requirements vary depending on the type of food product and the country of origin. Importers should research the specific requirements for their products well in advance of importing them.
- FDA Permits and Licenses: While the FDA does not require permits or licenses for most food imports, certain products, such as those containing certain food additives or color additives, may require pre-market approval.
- USDA Permits and Licenses: The USDA regulates the import of certain agricultural products, such as meat, poultry, and eggs. Importers of these products must obtain the necessary permits and licenses from the USDA’s Food Safety and Inspection Service (FSIS).
- Other Agencies: Depending on the product, other federal agencies may also be involved in the import process. For example, the U.S. Fish and Wildlife Service regulates the import of certain seafood products.
- State and Local Regulations: In addition to federal regulations, importers must also comply with state and local regulations. These regulations may vary depending on the state or locality where the food product is being imported.
Example: An importer of fresh mangoes from Mexico must ensure compliance with FDA regulations regarding produce safety, labeling, and prior notice. While no specific permit is required from the FDA, the importer must ensure the mangoes are free from pesticides exceeding established residue limits. The importer must also comply with USDA regulations if the mangoes are subject to any quarantine restrictions due to plant pests or diseases.
The importer will need to provide prior notice to the FDA before the shipment arrives in the U.S.
Food Safety Standards and Procedures: Food Importing Usa Consulting
The safety of imported food products in the United States is paramount, ensuring public health and consumer confidence. The Food and Drug Administration (FDA) plays a crucial role in establishing and enforcing rigorous food safety standards for imported goods. These standards are designed to prevent foodborne illnesses, ensure the quality of food products, and protect the integrity of the food supply chain.
Compliance with these regulations is not just a legal requirement but also a critical aspect of building trust with consumers and maintaining a successful import business.
Explore the different advantages of simply nourish source cat food that can change the way you view this issue.
FDA Food Safety Standards
The FDA enforces a comprehensive set of food safety standards, primarily through the Food Safety Modernization Act (FSMA) and Hazard Analysis and Critical Control Points (HACCP) principles. These regulations mandate preventive controls and proactive measures throughout the food supply chain, from farm to table.FSMA significantly modernized food safety regulations, shifting the focus from responding to contamination to preventing it. Key aspects of FSMA include:
- Preventive Controls for Human Food: Requires food facilities to implement written food safety plans, including hazard analysis, preventive controls, monitoring procedures, corrective actions, and verification activities. These plans must identify potential hazards and Artikel steps to control them.
- Preventive Controls for Animal Food: Similar to human food, this rule establishes preventive controls for animal food facilities.
- Produce Safety Rule: Sets standards for the safe growing, harvesting, packing, and holding of produce. It addresses potential hazards like agricultural water, biological soil amendments, and worker health and hygiene.
- Foreign Supplier Verification Program (FSVP): Importers are responsible for verifying that their foreign suppliers are producing food in a manner that meets U.S. food safety standards. This includes conducting hazard analyses, evaluating supplier performance, and taking corrective actions when necessary.
- Accredited Third-Party Certification: Allows accredited third-party auditors to conduct food safety audits and issue certifications, which can facilitate compliance with FSMA.
HACCP is a systematic approach to identifying and controlling food safety hazards. It focuses on preventing hazards rather than relying on end-product testing.
- Hazard Analysis: Identifying potential biological, chemical, and physical hazards that could occur in the food production process.
- Critical Control Points (CCPs): Identifying points in the process where control is essential to prevent or eliminate a food safety hazard.
- Critical Limits: Establishing maximum or minimum values that must be met at each CCP.
- Monitoring Procedures: Implementing procedures to monitor CCPs and ensure critical limits are met.
- Corrective Actions: Establishing procedures to be followed when a critical limit is not met.
- Verification Procedures: Establishing procedures to verify that the HACCP plan is working effectively.
- Record-Keeping: Maintaining records of all aspects of the HACCP plan.
Food Safety Inspection of Imported Products
Conducting a thorough food safety inspection of imported products involves several key steps, ensuring compliance with FDA regulations and the safety of the food supply. These inspections can be conducted by the FDA itself, or by qualified third-party auditors.The inspection process typically includes:
- Document Review: Reviewing import documentation, including the bill of lading, commercial invoices, packing lists, and certificates of analysis. This verifies that the product meets labeling requirements and complies with all relevant regulations.
- Facility Inspection (when applicable): Visiting the foreign supplier’s facility to assess its food safety practices. This involves evaluating the facility’s sanitation, pest control, employee hygiene, and adherence to HACCP principles.
- Product Sampling and Testing: Collecting samples of the imported product for laboratory analysis. This testing may include microbiological analysis, chemical analysis, and allergen testing.
- Labeling Review: Ensuring that the product labels comply with FDA labeling requirements, including accurate ingredient lists, nutrition facts panels, and allergen statements.
- Supplier Verification: Evaluating the foreign supplier’s food safety program and verifying that it meets U.S. standards, especially under the FSVP rule. This might include reviewing the supplier’s HACCP plan, audit reports, and corrective action plans.
- Review of FSVP Records: Reviewing the importer’s records related to the FSVP, to ensure they are conducting the necessary hazard analyses, supplier evaluations, and verification activities.
If violations are found during an inspection, the FDA may take several actions, including issuing a warning letter, detaining the product, or refusing entry into the United States. Repeated violations can lead to more severe penalties, such as import alerts or facility closures.
Common Food Safety Violations and Consequences
Several common food safety violations can lead to product detention, rejection, or other penalties. Importers must be vigilant in ensuring compliance to avoid these issues.The following table Artikels common violations and their potential consequences:
Violation | Description | Potential Consequences | Preventive Measures |
---|---|---|---|
Adulteration | Food is contaminated with harmful substances, such as pathogens, chemicals, or foreign objects. | Product detention, refusal of entry, recall, civil or criminal penalties. | Implement robust supplier verification programs, conduct thorough testing, and maintain strict sanitation practices. |
Misbranding | Incorrect or misleading labeling, including inaccurate ingredient lists, nutritional information, or allergen statements. | Product detention, refusal of entry, relabeling requirements, civil penalties. | Ensure compliance with FDA labeling regulations, review labels carefully, and verify all information. |
Lack of FSVP Compliance | Failure to verify that foreign suppliers meet U.S. food safety standards, as required by the FSVP rule. | Product detention, refusal of entry, warning letters, import alerts. | Develop and implement a comprehensive FSVP, including hazard analysis, supplier evaluations, and verification activities. |
Unsanitary Conditions | Food is produced or handled in unsanitary conditions, posing a risk of contamination. | Product detention, refusal of entry, facility inspection, potential for facility closure. | Implement and maintain strict sanitation procedures, conduct regular inspections, and train employees on proper hygiene practices. |
Consulting Services for Food Importers
Navigating the complexities of food importation into the USA can be challenging. From regulatory hurdles to supply chain management, businesses often require specialized expertise. Consulting services offer tailored solutions to streamline the import process, minimize risks, and ensure compliance. Hiring a consultant can provide invaluable support, saving time, resources, and potentially preventing costly mistakes.
Types of Consulting Services
Food importers have access to a variety of consulting services designed to address specific needs. These services can be broadly categorized to provide comprehensive support throughout the import process.
- Regulatory Compliance Consulting: This service focuses on ensuring adherence to all FDA regulations, including labeling requirements, food safety standards (like FSMA), import alerts, and detention procedures. Consultants in this area help importers understand and implement the necessary processes to meet legal obligations.
- Supply Chain Management Consulting: Optimizing the movement of goods from origin to the consumer is crucial. This type of consulting covers areas such as supplier selection, logistics, warehousing, transportation, and inventory management. The goal is to create a more efficient and cost-effective supply chain.
- Market Research Consulting: Understanding the target market is essential for success. Market research consultants provide insights into consumer preferences, market trends, competitor analysis, and potential opportunities. This information helps importers make informed decisions about product selection, pricing, and marketing strategies.
- Food Safety Auditing and Training: Maintaining high food safety standards is paramount. Consultants offer services such as conducting food safety audits to assess compliance with FSMA and other regulations, and providing training to staff on food safety practices, HACCP implementation, and recall procedures.
- Customs Brokerage and Import Documentation Assistance: While many importers work directly with customs brokers, some consultants offer support in navigating the complexities of customs clearance, including preparing import documentation, ensuring accurate tariff classifications, and dealing with customs inspections.
Benefits of Hiring a Consultant
Engaging a consultant provides several advantages for food importers. These benefits translate into improved efficiency, reduced risk, and enhanced profitability.
- Expertise and Specialized Knowledge: Consultants possess in-depth knowledge of food import regulations, industry best practices, and market dynamics. Their expertise allows them to identify potential challenges and develop effective solutions.
- Reduced Risk of Non-Compliance: Failure to comply with FDA regulations can result in product detention, fines, and even legal action. Consultants help importers navigate the complex regulatory landscape, minimizing the risk of non-compliance and associated penalties.
- Improved Efficiency and Cost Savings: By streamlining processes, optimizing supply chains, and avoiding costly mistakes, consultants can help importers improve efficiency and reduce operational costs.
- Access to Industry Networks: Consultants often have established relationships with industry professionals, including customs brokers, freight forwarders, and suppliers. This network can be invaluable in facilitating the import process.
- Focus on Core Business: Outsourcing import-related tasks to a consultant allows importers to focus on their core business activities, such as product development, marketing, and sales.
Consulting Service Packages Comparison
Consulting firms typically offer various service packages tailored to meet the specific needs and budgets of food importers. The following table provides a comparison of hypothetical service packages, illustrating the different levels of support available and their associated costs. Note that prices are estimates and can vary based on the consultant’s experience, the complexity of the import process, and the scope of services.
Service Package | Description | Deliverables | Estimated Price (USD) |
---|---|---|---|
Basic Compliance Package | Focused on fundamental regulatory compliance. Suitable for importers with a basic understanding of import regulations. | Review of product labeling, basic FDA registration assistance, and guidance on import requirements. | $2,500 – $5,000 |
Comprehensive Compliance Package | Provides in-depth support for regulatory compliance, including FSMA implementation and supply chain review. Ideal for businesses needing more extensive support. | Detailed compliance audit, development of a food safety plan, supplier verification guidance, and training on FSMA requirements. | $7,500 – $15,000 |
Supply Chain Optimization Package | Focuses on streamlining the supply chain to reduce costs and improve efficiency. Suitable for importers looking to optimize logistics and sourcing. | Supply chain assessment, recommendations for supplier selection, logistics optimization plan, and negotiation support. | $10,000 – $25,000 |
Full-Service Import Management Package | Offers comprehensive support for all aspects of food importation, from regulatory compliance to supply chain management and market research. Best suited for importers needing end-to-end assistance. | Includes all services from the Comprehensive Compliance and Supply Chain Optimization packages, plus market research, customs brokerage support, and ongoing monitoring. | $30,000 – $75,000+ (depending on scope and duration) |
Import Documentation and Logistics
Navigating the complexities of import documentation and logistics is crucial for the smooth and compliant entry of food products into the United States. Accurate paperwork and efficient transportation are essential to avoid delays, penalties, and potential rejection of shipments. This section details the required documentation, customs clearance procedures, and the typical import logistics process.
Required Import Documentation
The successful import of food products necessitates a comprehensive set of documents to satisfy U.S. Customs and Border Protection (CBP) and other relevant agencies. These documents provide vital information about the goods, their origin, and their compliance with U.S. regulations. Failure to provide accurate and complete documentation can lead to significant delays, fines, and even the denial of entry.
- Bill of Lading (or Air Waybill): This document serves as a receipt for the goods, a contract of carriage, and a title of ownership. It includes details such as the shipper, consignee, port of loading, port of discharge, and a description of the goods, including quantity, weight, and dimensions. The bill of lading is essential for customs clearance and for claiming the goods upon arrival.
- Commercial Invoice: The commercial invoice is a detailed record of the transaction between the seller and the buyer. It includes a description of the goods, the quantity, the unit price, the total value, the terms of sale (e.g., FOB, CIF), and the payment terms. The commercial invoice is used to determine the value of the goods for customs duties and to verify the accuracy of the transaction.
- Packing List: The packing list provides a detailed breakdown of the contents of each package within the shipment. It specifies the type and quantity of each item, the dimensions and weight of each package, and any identifying marks or numbers. The packing list is essential for customs officials to verify the contents of the shipment and for the importer to track and manage the goods.
- Certificate of Origin: This document certifies the country in which the goods were produced. It is required to determine eligibility for preferential duty rates under free trade agreements and to comply with country-of-origin labeling requirements. Certificates of origin are typically issued by a government agency or a recognized chamber of commerce in the exporting country.
- FDA Prior Notice: For food products regulated by the Food and Drug Administration (FDA), a prior notice must be submitted electronically to the FDA before the shipment arrives in the U.S. This notice provides the FDA with advance information about the shipment, including the product type, the manufacturer, the importer, and the anticipated arrival date. Failure to submit a prior notice can result in the shipment being held or refused entry.
- FDA Food Facility Registration: If the food product is manufactured, processed, packed, or stored in a facility that is subject to FDA registration, the facility must be registered with the FDA. The registration number must be provided on the import documents.
- Other Certificates/Permits: Depending on the specific food product, additional certificates or permits may be required. For example, products containing meat, poultry, or eggs require inspection certificates from the U.S. Department of Agriculture (USDA). Products containing alcohol require permits from the Alcohol and Tobacco Tax and Trade Bureau (TTB).
Customs Clearance and Inspection Procedures
The customs clearance process involves several steps to ensure that imported food products meet all U.S. regulatory requirements. This process typically involves the submission of required documentation, the payment of duties and taxes, and the potential inspection of the goods by CBP and/or the FDA. Delays in this process can significantly impact the timely delivery of goods.
- Entry Filing: The importer or their customs broker must file an entry with CBP electronically. The entry includes the required documentation, such as the bill of lading, commercial invoice, and certificate of origin.
- Duty and Tax Payment: The importer is responsible for paying any applicable duties, taxes, and fees. The amount of duties depends on the type of product, its country of origin, and any applicable trade agreements.
- Examination and Inspection: CBP and/or the FDA may examine and inspect the imported food products to verify compliance with U.S. regulations. This may involve a physical examination of the goods, sampling for laboratory analysis, and a review of the accompanying documentation.
- Release of Goods: If the shipment is found to be compliant, CBP will release the goods, allowing them to be transported to their final destination. If any violations are found, the shipment may be detained, rejected, or subject to penalties.
Typical Import Logistics Process Flowchart
The import logistics process involves a series of interconnected steps, from the origin of the goods to their final destination. A well-defined process is crucial for efficiency, cost control, and compliance. The following flowchart illustrates the typical steps involved:
Origin:
Exporter prepares goods, obtains necessary export documentation (e.g., export license, packing list).
Shipping & Transportation:
Goods are transported to the port of loading (e.g., by truck, rail).
Freight forwarder arranges for shipping (e.g., ocean freight, air freight), books cargo space, and prepares the bill of lading.
Goods are loaded onto the vessel or aircraft.
U.S. Customs Clearance:
Goods arrive at the U.S. port of entry.
Importer (or customs broker) files entry documents with CBP, including the bill of lading, commercial invoice, and other required documents.
CBP reviews the documents and may inspect the goods.
Importer pays duties, taxes, and fees.
FDA Prior Notice is submitted (if applicable).
FDA may inspect the goods, including sampling and laboratory analysis.CBP releases the goods.
Delivery to Final Destination:
Goods are transported from the port of entry to the importer’s warehouse or distribution center (e.g., by truck, rail).
Importer receives the goods and inspects them for damage or discrepancies.
Goods are distributed to retailers, restaurants, or consumers.
Example: A company importing olive oil from Italy follows this process. They first obtain the oil from a producer, prepare export documentation, and arrange for shipping. The oil is transported by sea to a U.S. port, where the importer’s customs broker handles the customs clearance process. This includes submitting the commercial invoice, bill of lading, and certificate of origin to CBP.
The importer pays the applicable duties and taxes. The FDA may inspect the shipment. Upon release, the oil is transported to the importer’s warehouse and then distributed to retailers.
Supply Chain Management and Sourcing
Building a robust and efficient supply chain is critical for successful food importing into the USA. This involves careful planning, strategic partnerships, and diligent execution to ensure the timely and safe delivery of products. A well-managed supply chain minimizes risks, reduces costs, and enhances the overall competitiveness of the importer.
Strategies for Building a Reliable and Efficient Food Import Supply Chain
Developing a resilient and streamlined supply chain requires a multifaceted approach, encompassing strategic planning, robust communication, and proactive risk management. Implementing these strategies will help food importers navigate the complexities of international trade and maintain a consistent flow of high-quality products.
- Supplier Selection and Vetting: The foundation of a reliable supply chain lies in choosing the right suppliers. This involves thorough due diligence, including assessing their production capabilities, food safety practices, and adherence to international standards.
- Contract Negotiation: Establish clear contracts with suppliers that Artikel expectations regarding product quality, delivery schedules, pricing, and dispute resolution mechanisms. Include clauses addressing potential disruptions such as natural disasters or political instability.
- Logistics Management: Optimize transportation routes, select reliable shipping partners, and implement tracking systems to monitor the movement of goods from origin to destination. Consider utilizing different modes of transport (sea, air, land) to mitigate risks and optimize costs.
- Inventory Management: Implement efficient inventory management practices to minimize storage costs and reduce the risk of spoilage. Use techniques such as Just-In-Time (JIT) inventory or First-In, First-Out (FIFO) to maintain freshness and minimize waste.
- Risk Management: Develop a comprehensive risk management plan to address potential disruptions such as food safety incidents, natural disasters, political instability, and economic fluctuations. This plan should include contingency measures and insurance coverage.
- Technology Integration: Leverage technology to improve supply chain visibility, communication, and efficiency. Implement tools such as Enterprise Resource Planning (ERP) systems, supply chain management software, and track-and-trace technologies.
Methods for Identifying and Vetting Potential Suppliers in Foreign Countries
Identifying and thoroughly vetting potential suppliers is a crucial step in ensuring the quality, safety, and reliability of food imports. This process involves a combination of research, on-site inspections, and ongoing monitoring to minimize risks and build strong, trustworthy partnerships.
- Online Research: Conduct thorough online research to identify potential suppliers. Utilize industry directories, trade associations, and online marketplaces to find companies that meet specific criteria.
- Trade Shows and Events: Attend international food trade shows and events to meet potential suppliers in person, assess their products, and gather information about their operations.
- Supplier Questionnaires: Develop detailed questionnaires to gather information about a supplier’s production processes, food safety practices, certifications, and financial stability.
- On-Site Audits: Conduct on-site audits of potential suppliers’ facilities to assess their compliance with food safety standards, quality control procedures, and overall operational efficiency.
- Third-Party Certifications: Verify that potential suppliers hold relevant third-party certifications, such as those from the Global Food Safety Initiative (GFSI), which demonstrate their commitment to food safety and quality. Examples include BRCGS, FSSC 22000, and SQF.
- Reference Checks: Contact existing customers or partners of potential suppliers to gather feedback on their performance, reliability, and customer service.
- Sample Testing: Request samples of the product and have them tested by an independent laboratory to verify their quality, safety, and compliance with US regulations.
Importance of Traceability and Transparency in the Food Import Supply Chain
Traceability and transparency are fundamental principles in the modern food import supply chain. They enable consumers to track the origin of their food, help regulators to identify and address food safety issues, and allow businesses to manage risks effectively. Implementing robust traceability systems builds consumer trust and protects brand reputation.
- Enhanced Food Safety: Traceability allows for the rapid identification and containment of food safety issues, such as contamination or allergens, by tracing the product back to its source.
- Consumer Trust and Confidence: Transparency builds consumer trust by providing information about the origin, ingredients, and production processes of food products. Consumers are increasingly demanding this information.
- Efficient Recall Management: In the event of a food safety incident, traceability systems enable businesses to quickly identify affected products and implement targeted recalls, minimizing the impact on consumers and the company.
- Supply Chain Efficiency: Traceability improves supply chain efficiency by providing real-time visibility into the movement of goods, allowing for better inventory management and reduced waste.
- Regulatory Compliance: Traceability systems help food importers comply with regulations such as the Food Safety Modernization Act (FSMA), which requires comprehensive record-keeping and traceability measures.
Market Research and Product Development
Understanding the US market is crucial for the success of any imported food product. This section focuses on how to effectively conduct market research to identify consumer demand, capitalize on current food trends, and learn from successful examples in the industry. This knowledge will empower importers to make informed decisions about product selection, marketing, and overall strategy.
Identifying Consumer Demand Through Market Research
Conducting thorough market research is essential for understanding consumer preferences, identifying unmet needs, and assessing the viability of imported food products. This involves several key steps.
- Defining the Target Audience: Determine the specific demographic and psychographic characteristics of the intended consumers. This includes factors such as age, income, lifestyle, dietary preferences, and cultural background. For example, a gourmet olive oil importer might target affluent consumers interested in healthy eating and authentic Mediterranean cuisine.
- Analyzing Existing Market Data: Utilize publicly available data from sources like the US Department of Agriculture (USDA), the Food and Drug Administration (FDA), and market research firms to understand market size, growth trends, and competitive landscape. Industry reports often provide valuable insights into consumer behavior and product performance.
- Conducting Primary Research: Gather firsthand information through surveys, focus groups, and interviews. Surveys can gauge consumer interest in specific products, price sensitivity, and preferred distribution channels. Focus groups allow for in-depth exploration of consumer attitudes and perceptions. Interviews with retailers and distributors can provide valuable insights into market demands and potential challenges.
- Analyzing Competitor Activities: Evaluate the strengths and weaknesses of existing products and brands in the market. Identify successful marketing strategies, pricing models, and distribution channels. This analysis can help importers differentiate their products and identify opportunities for competitive advantage.
- Testing and Validation: Before launching a product, consider conducting taste tests and pilot programs to gather feedback from potential consumers. This feedback can be used to refine product formulations, packaging, and marketing messages. For example, a new line of imported vegan snacks could be tested at a local farmers market to gauge consumer interest and identify areas for improvement.
Current Food Trends in the US Market Relevant to Importers
The US food market is dynamic, with consumer preferences constantly evolving. Importers need to stay abreast of current trends to ensure their products are relevant and appealing to consumers.
- Plant-Based Foods: The demand for plant-based alternatives to meat, dairy, and other animal products continues to grow. This trend is driven by concerns about health, environmental sustainability, and animal welfare. Importers of plant-based ingredients, snacks, and prepared meals can capitalize on this trend.
- Clean Labeling: Consumers are increasingly seeking foods with minimal ingredients, natural flavors, and no artificial additives. Transparency in labeling is also important. Importers should prioritize products with simple, recognizable ingredients and clear labeling information.
- Functional Foods: Foods that offer specific health benefits beyond basic nutrition are gaining popularity. This includes products enriched with vitamins, minerals, probiotics, and other functional ingredients. Examples include beverages with added electrolytes or snacks with added fiber.
- Global Flavors: Consumers are becoming more adventurous in their culinary explorations, seeking authentic flavors from around the world. This presents opportunities for importers of ethnic foods, spices, and sauces. Consider the popularity of Korean, Mexican, and Mediterranean cuisines.
- Convenience and Snacking: Busy lifestyles have fueled demand for convenient, ready-to-eat foods and snacks. This includes grab-and-go meals, single-serve portions, and healthy snacking options. Importers can target this trend with innovative packaging and product formats.
- Sustainable and Ethical Sourcing: Consumers are increasingly concerned about the environmental and social impact of their food choices. They are looking for products that are sustainably sourced, ethically produced, and support fair trade practices. Importers should prioritize sourcing from suppliers that meet these standards.
Successful Imported Food Products and Their Marketing Strategies, Food importing usa consulting
Examining successful examples can provide valuable insights into effective marketing strategies and product development.
- Haribo Gummy Bears: Haribo, a German confectionery company, has successfully marketed its gummy bears in the US for decades. Their marketing strategy focuses on creating a fun, playful brand image. The use of colorful packaging, memorable advertising campaigns, and partnerships with retailers has helped them achieve widespread brand recognition.
- Perrier Sparkling Water: Perrier, a French brand of sparkling water, has positioned itself as a premium, sophisticated beverage. Their marketing strategy emphasizes the product’s natural origins, refreshing taste, and stylish image. This is achieved through elegant packaging, targeted advertising campaigns, and partnerships with upscale restaurants and retailers.
- Banza Chickpea Pasta: Banza, an American company that imports chickpea flour from Italy, has successfully created a healthier alternative to traditional pasta. Their marketing strategy emphasizes the product’s high protein and fiber content, gluten-free nature, and delicious taste. This is achieved through strong branding, targeted advertising, and partnerships with health-conscious consumers.
- Tate’s Bake Shop Cookies: Tate’s Bake Shop, known for its thin and crispy cookies, has expanded its presence from a small bake shop to a nationally recognized brand. Their marketing strategy highlights the cookies’ homemade quality, simple ingredients, and delicious taste. This is achieved through premium packaging, placement in upscale grocery stores, and collaborations with food bloggers and influencers.
These examples demonstrate the importance of understanding the target market, developing a strong brand identity, and utilizing effective marketing strategies to achieve success in the US food market.
Risk Management in Food Importing
Navigating the complexities of food importation requires a proactive approach to risk management. The global nature of the food supply chain exposes importers to a multitude of potential challenges, from unforeseen disruptions to regulatory hurdles. A robust risk management strategy is not merely an optional extra; it is a critical component of a successful and sustainable food import business. This section Artikels the key risks, mitigation strategies, and real-world examples to help importers safeguard their operations.
Potential Risks Associated with Food Importation
The food import business is susceptible to a variety of risks that can significantly impact profitability, reputation, and consumer safety. Identifying these potential pitfalls is the first step in developing an effective risk management plan.
- Supply Chain Disruptions: Global events, natural disasters, and geopolitical instability can severely disrupt the flow of goods. These disruptions can lead to delays, shortages, and increased transportation costs. For example, a volcanic eruption in Iceland in 2010 grounded flights across Europe, significantly impacting the import of perishable goods from various regions.
- Currency Fluctuations: The value of the US dollar relative to the currency of the exporting country can fluctuate, affecting the cost of goods. A weakening dollar increases import costs, reducing profit margins, while a strengthening dollar can offer a competitive advantage.
- Product Recalls: Food safety incidents can lead to costly product recalls, damage brand reputation, and result in legal liabilities. Contamination, mislabeling, or undeclared allergens are common causes of recalls. The 2008 peanut butter Salmonella outbreak in the US is a stark example of the devastating consequences of a food safety crisis.
- Changes in Trade Regulations: Import regulations, tariffs, and quotas are subject to change, often without much notice. These changes can impact the cost of importing, the types of products that can be imported, and the required documentation.
- Damage or Loss of Goods: Products can be damaged or lost during transportation, storage, or handling. This can be due to improper packaging, inadequate temperature control, or accidents. Perishable goods are particularly vulnerable.
- Supplier Issues: Problems with suppliers, such as inconsistent quality, inability to meet demand, or unethical practices, can disrupt the supply chain and damage the importer’s reputation.
- Counterfeit Products: The risk of importing counterfeit products, which may not meet safety standards or be of the quality expected, is a significant concern.
- Political and Economic Instability: Political instability or economic downturns in the exporting country can disrupt production, increase costs, and create uncertainty.
Risk Mitigation Plan for Importers
Developing a comprehensive risk mitigation plan involves proactive measures to address the identified risks. This plan should be regularly reviewed and updated to reflect changing circumstances.
- Diversify Suppliers: Avoid relying on a single supplier or geographic region. Diversifying suppliers reduces the impact of disruptions and provides options if one supplier faces challenges.
- Implement Stringent Quality Control: Establish rigorous quality control procedures at every stage of the supply chain, from sourcing to arrival. This includes supplier audits, product testing, and inspection of shipments.
- Secure Insurance Coverage: Obtain comprehensive insurance coverage to protect against financial losses from various risks, including product damage, cargo loss, and liability claims.
- Use Hedging Strategies: Employ financial instruments, such as forward contracts or currency options, to mitigate the impact of currency fluctuations.
- Maintain Strong Relationships with Suppliers: Cultivate strong relationships with suppliers based on trust and transparency. This facilitates communication, problem-solving, and proactive risk management.
- Stay Informed of Regulatory Changes: Monitor changes in import regulations, tariffs, and quotas. This requires staying abreast of industry news, participating in trade organizations, and consulting with legal and regulatory experts.
- Develop a Recall Plan: Create a detailed product recall plan that Artikels procedures for identifying, isolating, and removing unsafe products from the market. This plan should include communication strategies for consumers and regulatory agencies.
- Conduct Thorough Market Research: Research the market thoroughly before importing any product. This will help to identify potential risks, understand consumer demand, and ensure compliance with local regulations.
- Use Technology: Utilize technology, such as track-and-trace systems and data analytics, to monitor the supply chain, identify potential issues, and improve efficiency.
- Build Buffer Stock: Maintain buffer stock of critical products to mitigate the impact of supply chain disruptions.
Case Study: Food Import-Related Crisis and Lessons Learned
The following case study illustrates the impact of a food import-related crisis and highlights the crucial lessons learned.
Case: In 2015, a major US food importer of frozen shrimp from Southeast Asia faced a crisis when the FDA issued a warning about the presence of antibiotic residues in the imported product. The importer was forced to recall a significant amount of product, resulting in substantial financial losses and reputational damage. The FDA’s findings triggered investigations into the importer’s quality control procedures and supplier relationships.
Lessons Learned:
- Supplier Audits are Crucial: The importer’s reliance on third-party certifications, without conducting its own thorough supplier audits, proved insufficient. Regular, on-site audits of suppliers are necessary to verify compliance with food safety standards.
- Testing and Monitoring: The importer’s testing protocols were inadequate, failing to detect the antibiotic residues. Regular, comprehensive product testing is essential to ensure that imported products meet regulatory requirements.
- Traceability is Key: The importer struggled to trace the source of the contaminated shrimp, hindering the recall process. Implementing a robust track-and-trace system is critical for quickly identifying and isolating affected products.
- Crisis Communication: The importer’s initial response to the crisis was slow and ineffective, further damaging its reputation. A well-defined crisis communication plan, with clear messaging and designated spokespersons, is essential for managing public perception and mitigating reputational harm.
Labeling and Packaging Requirements
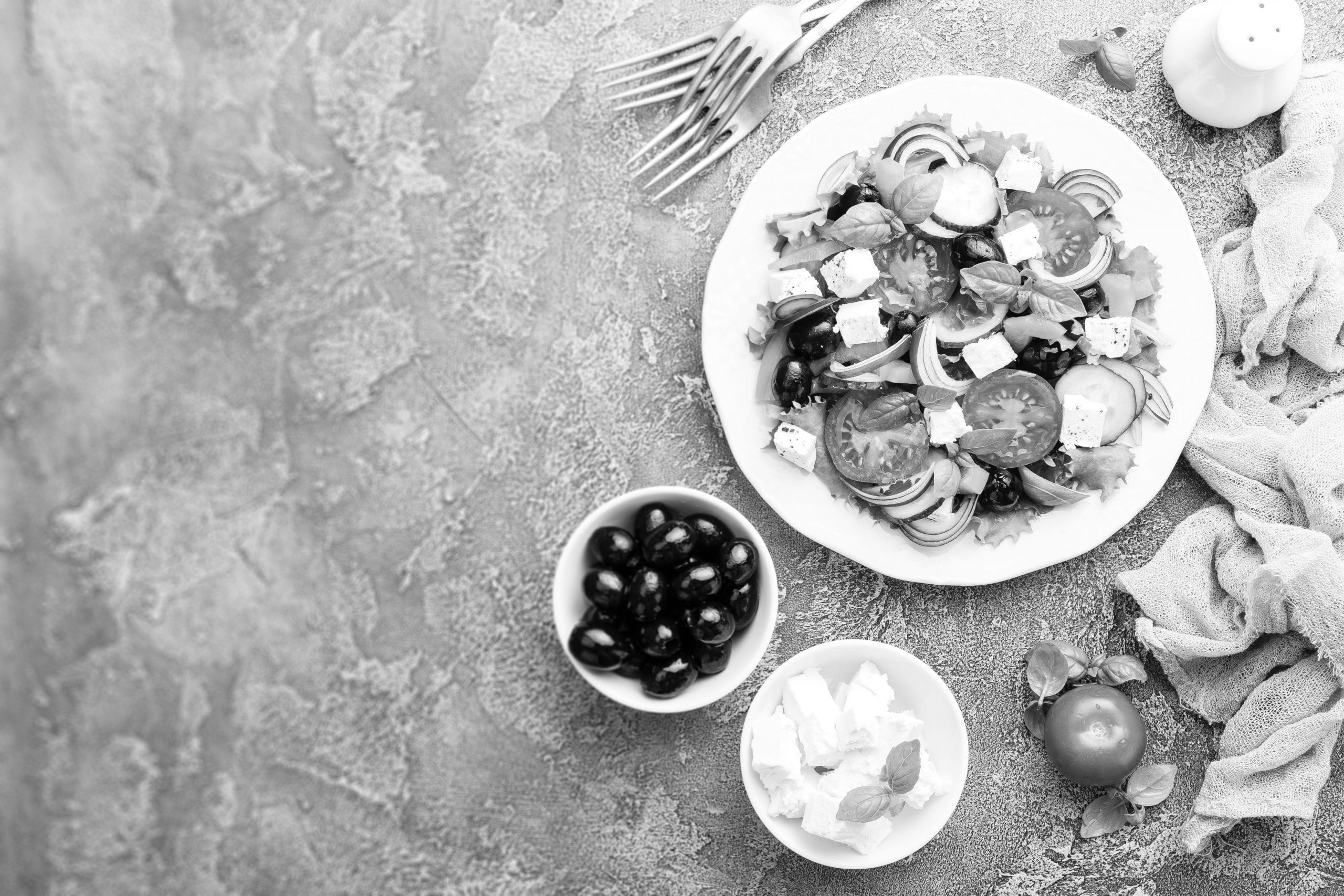
Importing food into the United States necessitates strict adherence to labeling and packaging regulations enforced by the Food and Drug Administration (FDA). These requirements are in place to ensure consumers have access to accurate information regarding the food they consume and that the food is safe and properly preserved. Non-compliance can lead to product detention, rejection, or even legal action.
Specific Labeling Requirements
Food labels in the U.S. must convey a wealth of information to consumers. These requirements are multifaceted and aim to promote transparency and informed consumer choices.
- Statement of Identity: The label must clearly and prominently state the common or usual name of the food product. This helps consumers easily identify what the product is. For example, instead of “Product X,” the label should say “Strawberry Yogurt” or “Canned Tuna in Water.”
- Net Quantity of Contents: The label must declare the net quantity of the food in terms of weight, measure, or numerical count. This information must be placed in a conspicuous location on the principal display panel, using both U.S. Customary System and metric units. For instance, a can of tomatoes might state “Net Wt. 14.5 oz (411g).”
- Nutrition Facts Panel: This panel provides detailed information about the nutritional content of the food. It includes serving size, calories, total fat, saturated fat, trans fat, cholesterol, sodium, total carbohydrates, dietary fiber, total sugars (including added sugars), protein, vitamin D, calcium, iron, and potassium. The FDA provides a standardized format for the Nutrition Facts panel to ensure consistency and ease of understanding.
- Ingredient List: All ingredients must be listed in descending order of predominance by weight. This allows consumers to identify all components of the food product, including additives, preservatives, and flavorings. For example, if a product contains sugar, it should be listed if sugar is the most abundant ingredient, followed by other ingredients in order of their weight.
- Allergen Labeling: The Food Allergen Labeling and Consumer Protection Act (FALCPA) mandates that food labels clearly identify the presence of the “major food allergens.” These allergens include milk, eggs, fish (e.g., bass, flounder, cod), Crustacean shellfish (e.g., crab, lobster, shrimp), tree nuts (e.g., almonds, walnuts, pecans), peanuts, wheat, and soybeans. The allergen information must be declared either within the ingredient list or in a “Contains” statement immediately following the ingredient list.
For example, a product containing milk would need to either list “milk” within the ingredient list or include a “Contains: Milk” statement.
- Name and Place of Business of the Food Manufacturer, Packer, or Distributor: The label must include the name and address of the manufacturer, packer, or distributor of the food product. This information allows consumers to contact the responsible party if they have any questions or concerns about the product.
- Country of Origin: The label must clearly state the country of origin of the food product. This information is crucial for consumers who may prefer products from specific countries. This requirement is enforced by U.S. Customs and Border Protection (CBP) and the FDA.
- Special Dietary Claims: If the food product makes any special dietary claims (e.g., “low-fat,” “gluten-free,” “organic”), it must meet specific FDA requirements and be accurately substantiated. For example, a product labeled “gluten-free” must contain less than 20 parts per million of gluten.
- Lot Number or Code: While not always mandatory, lot numbers or codes are often included on food labels for traceability purposes. These codes help manufacturers identify and track products in case of recalls or other issues.
Examples of Compliant and Non-Compliant Food Labels
Understanding the nuances of compliant and non-compliant labels is crucial for successful food imports. Here are a few examples:
Compliant Label Example:
Imagine a label for a jar of strawberry jam.
Principal Display Panel: “Strawberry Jam”
Nutrition Facts Panel: Shows serving size, calories, fat, carbohydrates, sugars, protein, and vitamins/minerals in the FDA-required format.
Ingredient List: Strawberries, Sugar, Corn Syrup, Pectin, Citric Acid.
Allergen Statement: None (if the product does not contain any of the major allergens).
Net Quantity: Net Wt. 10 oz (283g)
Manufacturer Information: “Manufactured for: ABC Foods, Anytown, USA”
Country of Origin: Product of USA
Non-Compliant Label Example:
Consider a label for a similar strawberry jam that is non-compliant.
Issue 1: The “Nutrition Facts” panel is missing or incomplete (e.g., does not list the amount of trans fat or added sugars). This is a significant violation.
Issue 2: The ingredient list is not in descending order of predominance. For example, if sugar is the most abundant ingredient, but strawberries are listed first. This is a violation of ingredient listing regulations.
Issue 3: The allergen statement is missing or incomplete. For example, if the jam contains wheat, but the label doesn’t declare it. This violates FALCPA.
Issue 4: The net quantity is missing or in an incorrect format (e.g., only shows metric units). This is a violation of the net quantity regulations.
Issue 5: The country of origin is missing. This is a violation of the country of origin labeling regulations.
Ensuring Packaging Meets FDA Standards
Food packaging plays a vital role in food safety and preservation. The FDA has specific regulations to ensure packaging materials are safe and do not contaminate the food.
- Material Safety: Packaging materials must be safe for their intended use and not contain any substances that could migrate into the food and pose a health risk. The FDA evaluates packaging materials based on their composition and potential for migration.
- Barrier Properties: Packaging must provide an adequate barrier to protect the food from environmental contaminants such as oxygen, moisture, and light, which can affect food quality and shelf life. For example, airtight packaging is essential for preserving the freshness of many food products.
- Tamper-Evident Packaging: The FDA requires tamper-evident packaging for certain food products to protect against intentional contamination. This includes features like seals, bands, or other devices that provide evidence if the package has been opened or tampered with.
- Good Manufacturing Practices (GMP): Packaging operations must adhere to GMP to prevent contamination. This includes proper sanitation, personnel hygiene, and control of packaging materials.
- Indirect Food Additives: Packaging materials are considered indirect food additives. Any substance used in the packaging must be approved by the FDA for its intended use and must not exceed allowable levels of migration into the food.
- Specific Packaging Requirements for Certain Foods: Some food products have specific packaging requirements. For example, low-acid canned foods must be packaged in hermetically sealed containers and processed to ensure commercial sterility.
Example: A food importer bringing in canned peaches must ensure the cans are made of food-grade metal, properly sealed to prevent spoilage, and meet the FDA’s standards for thermal processing to eliminate harmful microorganisms. The cans also need to be free of lead or other harmful contaminants. The labels must adhere to all the labeling requirements, including the product’s name, ingredients, and nutrition facts.
Example: Consider the case of imported olive oil. The packaging (typically a glass or PET bottle) must be designed to protect the oil from light and oxygen, which can cause it to degrade. The label must include the country of origin, the net content, and any relevant health claims. The bottle must be made of a food-grade material, and any colorants used in the bottle or label must be approved for food contact.
Key Formula: Compliance = Accurate Labeling + Safe Packaging + Adherence to GMPs.
Cost Analysis and Pricing Strategies
Understanding the financial implications of importing food products is crucial for success in the U.S. market. A thorough cost analysis and the development of effective pricing strategies are essential to ensure profitability and competitiveness. This section Artikels the various cost components, methods for calculating landed costs, and approaches to pricing imported food items.
Import Costs
Importing food products involves a range of costs beyond the initial purchase price. These expenses must be carefully considered to accurately determine the total cost and ultimately, the profitability of the product.
- Product Cost: This is the initial cost of the food product from the supplier, including the raw materials, manufacturing, and any associated packaging costs.
- Shipping Costs: Transportation of goods from the origin country to the U.S. involves various expenses. These include:
- Ocean Freight: The cost of shipping goods by sea, typically the most cost-effective option for large quantities.
- Air Freight: A faster, but more expensive, option for smaller quantities or perishable goods requiring rapid delivery.
- Inland Transportation: Costs associated with moving goods from the port of entry to the final destination.
- Freight Insurance: Protects against loss or damage during transit.
- Customs Duties and Fees: These are imposed by the U.S. government on imported goods. They include:
- Tariffs: Taxes on imported goods, the rate varies depending on the product and the country of origin.
- Merchandise Processing Fee (MPF): A fee charged by U.S. Customs and Border Protection (CBP) for processing import entries. The MPF is a percentage of the value of the goods, subject to a minimum and maximum charge.
- Harbor Maintenance Fee (HMF): A fee assessed on the value of commercial cargo that is loaded or unloaded at U.S. ports.
- Insurance: Protecting the food products against damage, loss, or theft during shipping and storage is essential.
- Marine Insurance: Covers goods during ocean transport.
- Warehouse Insurance: Protects goods while stored in a warehouse.
- Inspection and Testing Fees: Food products may be subject to inspection and testing by the FDA or other regulatory agencies. These costs can vary depending on the type of product and the testing requirements.
- Storage and Handling: Costs associated with storing the food products in a warehouse, including rent, utilities, and labor.
- Import Documentation and Brokerage Fees: Fees charged by customs brokers for preparing and submitting the necessary import documentation.
- Currency Exchange Rate Fluctuations: Changes in exchange rates can impact the cost of imported goods. Hedging strategies can be employed to mitigate this risk.
- Other Costs: Other potential costs include:
- Legal Fees: For legal advice on import regulations and compliance.
- Marketing and Sales Expenses: Costs associated with promoting and selling the imported food products.
- Financing Costs: Interest on loans used to finance the import transaction.
Calculating Landed Cost
The landed cost is the total cost of a product once it has arrived at the buyer’s door. It is a critical metric for determining profitability and setting competitive prices. Accurate calculation of landed cost is essential for informed decision-making. The landed cost includes the product cost, shipping costs, insurance, customs duties and fees, and any other expenses incurred in bringing the product to the U.S.
market.
Landed Cost = Product Cost + Shipping Costs + Insurance + Customs Duties & Fees + Other Costs
For example, a food importer purchases 1,000 cases of olive oil from Italy for $10 per case ($10,000 total). Shipping costs are $2 per case ($2,000 total), insurance is $0.10 per case ($100 total), customs duties are 5% of the product value ($500), and other fees total $200.
Landed Cost = $10,000 (Product Cost) + $2,000 (Shipping) + $100 (Insurance) + $500 (Customs) + $200 (Other) = $12,800
The landed cost per case is $12.80 ($12,800 / 1,000 cases).
Pricing Strategies
Developing effective pricing strategies is crucial for ensuring profitability and market competitiveness. Several approaches can be used, and the best strategy will depend on factors such as the product, target market, and competition.
- Cost-Plus Pricing: This is a straightforward approach where a markup is added to the landed cost to determine the selling price.
Selling Price = Landed Cost + Markup
The markup is typically a percentage of the landed cost and should cover all operating expenses and desired profit. For instance, if the landed cost of a product is $12.80 per unit, and the importer desires a 25% markup, the selling price would be $16.00 ($12.80 + ($12.80
– 0.25)). - Value-Based Pricing: This strategy focuses on the perceived value of the product to the customer. The price is set based on what customers are willing to pay, which can be higher than cost-plus pricing if the product offers unique benefits or features. This approach requires a deep understanding of the target market and their preferences.
For example, a gourmet imported cheese with a strong reputation might command a higher price than a similar cheese from a less well-known source, reflecting its perceived value.
- Competitive Pricing: This involves setting prices based on the prices of competitors. This strategy is suitable in markets where there are many similar products. The importer needs to analyze competitor pricing and position their product accordingly.
For example, if several importers sell a particular type of canned tuna, the importer may need to match or slightly undercut competitor prices to gain market share.
- Premium Pricing: This involves setting a high price to convey a sense of quality and exclusivity. This strategy is often used for luxury food products or those with unique attributes. This strategy requires a strong brand image and a target market willing to pay a premium.
For example, an importer of rare, organic, and ethically sourced coffee beans might use premium pricing to reflect the product’s high quality and exclusivity.
- Discount Pricing: Offering discounts can be used to attract customers, clear out excess inventory, or respond to competitive pressures. Discount pricing should be used strategically to avoid eroding profit margins.
For example, offering a temporary discount on a product to boost sales during a specific promotional period or to clear out inventory before the expiration date.
Closure
In conclusion, food importing USA consulting is an intricate yet rewarding endeavor. By adhering to stringent regulations, prioritizing food safety, and implementing robust supply chain strategies, businesses can successfully navigate the import landscape. This guide provides a foundational understanding of the key elements involved, equipping importers with the knowledge necessary to thrive in the competitive U.S. market and bring a world of flavors to American consumers.