Food packing jobs are essential to the food industry, ensuring products reach consumers safely and efficiently. These roles encompass a wide range of tasks, from operating machinery to meticulous quality control, all within diverse environments that can include temperature-controlled facilities and high-speed production lines. Success in these positions hinges on a combination of physical stamina, attention to detail, and adherence to stringent safety protocols.
This comprehensive guide delves into the multifaceted world of food packing, exploring the various roles, required qualifications, and the crucial processes involved. We’ll examine the different types of food products, the technologies employed, and the impact of food packing on the broader supply chain. From entry-level positions to career advancement opportunities, this overview provides valuable insights into this dynamic and critical sector.
Overview of Food Packing Jobs
Food packing jobs are integral to the food industry, encompassing a range of tasks crucial for getting products from processing facilities to consumers. These roles are essential in maintaining food safety, quality, and efficient distribution. They offer a variety of responsibilities and work environments, requiring specific skills and physical capabilities.
Typical Tasks in Food Packing Jobs
The tasks performed in food packing jobs are diverse, covering the entire process of preparing food products for distribution.
- Packaging Food Products: This involves manually or using machinery to place food items into various containers, such as boxes, bags, cans, or trays. This includes ensuring the correct quantity of product is placed in each package and that the packaging is properly sealed.
- Labeling and Coding: Applying labels with product information, including ingredients, nutritional facts, and expiration dates, is a key task. Workers also often apply date codes or lot numbers to ensure traceability and manage inventory.
- Quality Control: Inspecting food products and packaging for defects, such as damage, incorrect labeling, or contamination, is essential. Workers may remove or set aside items that do not meet quality standards.
- Operating and Maintaining Equipment: Some food packing roles involve operating and monitoring machinery, such as filling machines, sealing equipment, and conveyor systems. Basic maintenance, such as cleaning and minor adjustments, may also be required.
- Preparing Shipping Containers: This includes packing packaged food products into larger containers, such as boxes or pallets, for shipment. Workers must follow specific stacking patterns and ensure containers are properly sealed and labeled for transportation.
- Cleaning and Sanitation: Maintaining a clean and sanitary work environment is critical in food packing. This involves regular cleaning of work surfaces, equipment, and the surrounding area to prevent contamination.
Common Work Environments and Conditions
Food packing jobs are typically performed in manufacturing facilities or warehouses, with specific conditions depending on the type of food being handled.
- Temperature-Controlled Environments: Many food packing facilities maintain specific temperature and humidity levels to preserve the quality and safety of food products. This may involve working in refrigerated or climate-controlled environments.
- Fast-Paced Work: Food packing often involves repetitive tasks and tight deadlines to meet production goals. Workers must be able to maintain a consistent pace and focus on accuracy.
- Standing for Extended Periods: Most food packing roles require standing for long periods, often for the duration of a shift.
- Exposure to Noise: Packing facilities can be noisy due to machinery operation and the movement of materials. Workers may be required to wear hearing protection.
- Use of Protective Gear: To ensure food safety and worker safety, employees are typically required to wear protective gear, such as gloves, hairnets, and sometimes aprons or smocks.
- Potential for Lifting and Carrying: Depending on the specific job, workers may need to lift and carry boxes or other containers of food products, sometimes weighing up to 50 pounds or more.
Essential Skills and Physical Requirements
Success in food packing roles depends on a combination of skills and physical capabilities.
- Attention to Detail: Accuracy is paramount in food packing. Workers must be able to identify and correct errors in packaging, labeling, and quality control.
- Hand-Eye Coordination: This skill is essential for operating machinery, handling products, and performing tasks like labeling and sealing.
- Ability to Follow Instructions: Workers must be able to understand and follow written and verbal instructions, including safety procedures and quality control guidelines.
- Teamwork: Food packing often involves working as part of a team. Workers must be able to collaborate with others to achieve production goals.
- Physical Stamina: The ability to stand for extended periods, perform repetitive tasks, and lift and carry moderate weights is essential.
- Manual Dexterity: This includes the ability to use hands and fingers to manipulate small objects and perform tasks like packaging and labeling.
Required Qualifications and Training
Entry-level food packing positions typically have minimal educational prerequisites, emphasizing on-the-job training and a strong work ethic. While specific requirements can vary by employer and location, the focus is generally on practical skills and adherence to safety standards rather than extensive academic qualifications. Certifications, if required, are usually obtained through employer-provided training programs.
Educational Requirements and Certifications
Formal education requirements for food packing roles are generally quite basic. A high school diploma or equivalent, such as a GED, is often preferred but not always mandatory. Employers prioritize candidates who can demonstrate basic literacy and numeracy skills, as these are essential for understanding instructions, labels, and quality control measures. Some companies may require or prefer candidates to have completed vocational training programs related to food handling or manufacturing, although this is less common for entry-level positions.Regarding certifications, the specific requirements vary.
However, common certifications may include:
- Food Handler’s Permit: This is a frequently required certification, demonstrating basic knowledge of food safety practices, including proper hygiene, cross-contamination prevention, and safe food handling techniques. The specifics of the permit (e.g., the issuing authority, the validity period) vary by state or local regulations.
- Forklift Certification: In environments where forklifts or other powered industrial trucks are used for moving materials, employees may need to obtain a forklift certification. This involves completing a training program and passing a practical assessment to ensure safe operation of the equipment.
- Hazard Analysis and Critical Control Points (HACCP) Certification: For roles involving quality control or supervision, some employers may require HACCP certification. This demonstrates an understanding of the principles of HACCP, a systematic approach to identifying and controlling food safety hazards.
On-the-Job Training
New hires in food packing positions can expect comprehensive on-the-job training provided by the employer. This training is designed to familiarize employees with specific tasks, equipment, and company procedures. The duration and intensity of training can vary depending on the complexity of the role and the specific products being handled.The training program typically covers the following areas:
- Company Policies and Procedures: New employees will receive detailed information on company policies, including attendance, break times, dress code, and communication protocols.
- Product Knowledge: Trainees will learn about the specific food products being handled, including their characteristics, shelf life, and any special handling requirements.
- Equipment Operation: Employees will be trained on the safe and efficient operation of any equipment used in the packing process, such as scales, labeling machines, sealing equipment, and conveyor systems. This training will include proper setup, operation, and basic troubleshooting.
- Packaging Techniques: Trainees will be instructed on proper packaging techniques, including how to select the correct packaging materials, how to assemble and seal packages, and how to label products accurately.
- Quality Control: Employees will be trained on quality control procedures, including how to inspect products for defects, how to identify and report any issues, and how to maintain product quality throughout the packing process.
- Safety Procedures: A significant portion of the training will focus on safety procedures, including proper lifting techniques, the use of personal protective equipment (PPE), and emergency procedures.
Training often includes a combination of classroom instruction, hands-on practice, and supervised work. New hires are typically paired with experienced employees or supervisors who provide guidance and feedback. Continuous training and refresher courses may also be provided to ensure employees stay up-to-date on best practices and any changes in procedures. For example, a large food processing plant might conduct weekly safety meetings, and a smaller facility might offer quarterly refresher courses on food handling.
Safety Protocols and Regulations
Safety is paramount in food packing environments, and employees must be aware of and adhere to numerous safety protocols and regulations. These protocols are in place to protect employees from injury and to ensure the safety and integrity of the food products.Key safety protocols and regulations include:
- Personal Protective Equipment (PPE): Employees are required to wear appropriate PPE, which may include hairnets, gloves, aprons, safety glasses, and closed-toe shoes. The specific PPE requirements will depend on the specific tasks being performed and the nature of the food products. For example, workers handling raw meat will likely be required to wear more extensive PPE than those packing dry goods.
- Hand Hygiene: Strict hand hygiene practices are essential to prevent the spread of bacteria and other contaminants. Employees are required to wash their hands frequently and thoroughly, especially before starting work, after breaks, and after handling potentially contaminated materials.
- Food Safety Protocols: Employees must follow all food safety protocols, including proper handling and storage of food products, prevention of cross-contamination, and adherence to temperature control guidelines. This is crucial to prevent foodborne illnesses.
- Equipment Safety: Employees must be trained on the safe operation of all equipment and machinery. This includes following lockout/tagout procedures during maintenance, using safety guards and shields, and reporting any equipment malfunctions promptly.
- Ergonomics: To prevent musculoskeletal injuries, employees must be trained on proper lifting techniques and ergonomic practices. This includes using mechanical aids for heavy lifting, arranging workstations to minimize repetitive motions, and taking regular breaks.
- Emergency Procedures: Employees must be familiar with emergency procedures, including evacuation routes, fire safety protocols, and first aid procedures. Regular drills and training are often conducted to ensure employees are prepared for emergencies.
- Hazard Communication: Employees must be informed about any hazardous chemicals or materials used in the workplace, including their potential hazards and how to handle them safely. This information is typically provided through Safety Data Sheets (SDS).
- Regulatory Compliance: Food packing facilities are subject to various regulations, such as those enforced by the Food and Drug Administration (FDA) or the Food Safety and Inspection Service (FSIS). Employees must be aware of these regulations and follow all applicable procedures to ensure compliance. For example, adherence to allergen labeling regulations is critical to protect consumers.
The Food Packing Process
The food packing process is a critical stage in the food supply chain, ensuring product safety, preservation, and efficient distribution. This process transforms raw ingredients into consumer-ready products, maintaining quality and extending shelf life. From the initial receipt of materials to the final shipment, each step must be carefully controlled to meet stringent hygiene and quality standards.
Steps in a Typical Food Packing Process
The food packing process is a multi-stage operation designed to protect, preserve, and present food products. The sequence of steps is crucial for maintaining food safety and quality.
- Receiving Raw Materials: This initial step involves the inspection and acceptance of raw ingredients or components used in food production. Quality checks are performed to ensure compliance with safety and quality standards. Temperature control is often a critical factor, especially for perishable items.
- Preparation and Processing: Raw materials undergo processing, which might include cleaning, cutting, cooking, or mixing. This step prepares the ingredients for the next stage.
- Filling: The processed food is filled into its primary packaging, such as cans, jars, pouches, or trays. Accurate filling is essential to ensure the correct portion size and prevent waste.
- Sealing: The primary packaging is sealed to create an airtight and tamper-evident barrier. This protects the food from contamination, spoilage, and moisture loss. The sealing method varies depending on the packaging type.
- Labeling and Coding: Packaging is labeled with essential information, including product name, ingredients, nutritional facts, allergen information, expiration dates, and barcodes. Coding, such as batch numbers, is applied for traceability.
- Secondary Packaging: Individual packaged items are often grouped into secondary packaging, such as boxes, cartons, or shrink wrap. This provides additional protection during handling and transportation and facilitates easier handling.
- Quality Control: Throughout the process, quality control checks are performed to ensure that products meet established standards for weight, appearance, seal integrity, and labeling accuracy.
- Palletizing and Warehousing: Secondary packaged products are often placed on pallets for efficient handling and storage. Palletized goods are then moved to a warehouse for storage under controlled conditions.
- Shipping: The final step involves preparing the packaged food for shipment to distribution centers, retailers, or directly to consumers. This may involve loading onto trucks, ships, or other transportation methods.
Packing Methods
Packing methods vary based on the product, production volume, and budget. Each method presents specific advantages and disadvantages.
The table below compares automated and manual packing methods:
Packing Method | Description | Advantages | Disadvantages |
---|---|---|---|
Automated Packing | This method uses machinery to perform various packing tasks, such as filling, sealing, labeling, and palletizing. |
|
|
Manual Packing | This method relies on human workers to perform packing tasks. |
|
|
Semi-Automated Packing | This method combines automated and manual processes, such as using machines for filling and sealing while human workers handle labeling and inspection. |
|
|
Robotic Packing | This method utilizes robots to handle various packing tasks, such as picking and placing products, loading packaging, and palletizing. |
|
|
Common Packing Materials
A wide variety of materials are used for food packing, each with its own properties and applications. The choice of material depends on the food product’s characteristics, desired shelf life, and the need for protection.
- Cardboard: This is a versatile and cost-effective material commonly used for secondary packaging, such as boxes and cartons. Cardboard provides excellent protection during shipping and handling. Recycled cardboard options are widely available, supporting sustainability efforts. For example, cereal boxes and frozen pizza boxes are common examples of cardboard packaging.
- Plastic: Plastic packaging comes in various forms, including films, trays, bottles, and containers. It offers excellent barrier properties, protecting food from moisture, oxygen, and other contaminants. Common examples include PET bottles for beverages, plastic wrap for produce, and plastic containers for yogurt. Polypropylene (PP) is often used for microwavable food containers.
- Specialized Films: These films are designed to extend shelf life and preserve food quality. They often incorporate multiple layers with specific barrier properties. For instance, modified atmosphere packaging (MAP) films are used to control the gas composition within the package, slowing down spoilage and extending shelf life. Vacuum packaging films are used to remove oxygen, which inhibits the growth of aerobic bacteria and extends the shelf life of meat and other perishable foods.
- Glass: Glass is a non-reactive and recyclable material often used for packaging foods such as jams, sauces, and pickles. Glass provides excellent barrier properties and maintains the flavor and aroma of the food. Glass jars are a popular choice for preserving foods at home and in commercial settings.
- Metal: Metal cans are commonly used for preserving food for extended periods. They provide excellent protection against light, oxygen, and physical damage. Canned vegetables, fruits, and soups are classic examples of metal packaging.
- Aluminum Foil: Aluminum foil is used for wrapping food items and for creating flexible packaging such as pouches and stand-up bags. It provides a barrier against light, oxygen, and moisture. It’s often used in the packaging of snacks and ready-to-eat meals.
Safety and Hygiene in Food Packing
Food safety and hygiene are paramount in the food packing industry, directly impacting consumer health and the reputation of food businesses. Strict adherence to regulations and protocols is not merely a suggestion but a legal and ethical imperative. Maintaining a safe and hygienic environment throughout the packing process is crucial to prevent contamination, spoilage, and the spread of foodborne illnesses.
Failure to prioritize these aspects can lead to severe consequences, including product recalls, legal penalties, and irreparable damage to brand trust.
Importance of Food Safety Regulations and Standards
Food safety regulations and standards provide a framework for the safe handling, processing, and packaging of food products. These regulations are established by governmental and international organizations to protect public health and ensure the integrity of the food supply. They encompass various aspects, from the sourcing of raw materials to the final packaging and labeling of the product. Compliance with these standards is non-negotiable and forms the foundation of a responsible food packing operation.
- Hazard Analysis and Critical Control Points (HACCP): HACCP is a systematic preventive approach to food safety from biological, chemical, and physical hazards in production processes that can cause the finished product to be unsafe. It identifies potential hazards at specific points (critical control points) in the food production process and establishes control measures to prevent or minimize those hazards. For example, a critical control point might be the temperature of a refrigerated storage unit.
For descriptions on additional topics like food scraps crossword, please visit the available food scraps crossword.
If the temperature rises above a certain level, it could lead to bacterial growth and food spoilage. Regular monitoring and corrective actions are crucial to maintain food safety.
- Good Manufacturing Practices (GMP): GMP Artikels the basic operational and environmental conditions necessary for producing safe, wholesome food products. GMP covers a wide range of areas, including personnel hygiene, facility design and maintenance, equipment sanitation, and pest control. For instance, GMP guidelines would mandate regular handwashing, the use of appropriate cleaning agents, and the prevention of cross-contamination between raw and cooked foods.
- Food Safety Modernization Act (FSMA): In the United States, the Food Safety Modernization Act (FSMA) represents a significant shift in food safety regulation. It emphasizes a preventative approach to food safety, giving the Food and Drug Administration (FDA) more authority to regulate the food industry. FSMA requires food facilities to implement comprehensive food safety plans that identify potential hazards and establish preventive controls. This includes hazard analysis, preventive controls, monitoring, corrective actions, and verification.
- International Organization for Standardization (ISO) Standards: ISO 22000 is an international standard that specifies the requirements for a food safety management system. It combines elements of HACCP and GMP to provide a comprehensive framework for ensuring food safety throughout the food chain. Compliance with ISO 22000 demonstrates a commitment to food safety and can enhance a company’s credibility and market access.
Personal Protective Equipment (PPE) Required for Food Packing Jobs
Personal Protective Equipment (PPE) is essential for protecting food packing workers from potential hazards and preventing contamination of food products. The specific PPE requirements may vary depending on the type of food being packed and the specific tasks involved, but certain items are generally considered standard. Proper use and maintenance of PPE are critical to its effectiveness.
- Hairnets or Caps: These are essential to contain hair and prevent it from falling into food products, which can be a source of contamination. The hairnets or caps should be worn correctly to ensure that all hair is covered.
- Gloves: Gloves protect both the worker and the food. They prevent direct contact between hands and food, reducing the risk of contamination from bacteria or other microorganisms. Different types of gloves are used depending on the task, such as latex, nitrile, or vinyl. Gloves should be changed frequently, especially after handling raw materials or after any potential contamination.
- Aprons or Protective Clothing: Aprons or other protective clothing are worn to protect workers’ clothing from spills and splashes, preventing cross-contamination. The material should be easy to clean and sanitize.
- Face Masks: In certain environments, face masks may be required to prevent the spread of respiratory droplets, which could contaminate food. This is particularly important during activities that involve close contact with food products or potential sources of contamination.
- Safety Glasses or Goggles: These protect the eyes from splashes, dust, and other hazards. Safety glasses or goggles are essential when working with cleaning chemicals or in environments where debris may be present.
- Closed-Toe Shoes: Closed-toe shoes, often with non-slip soles, are crucial for safety in the food packing environment. They protect the feet from potential hazards, such as dropped objects or slippery surfaces.
Consequences of Failing to Adhere to Food Safety and Hygiene Protocols
Failing to adhere to food safety and hygiene protocols can have severe and far-reaching consequences, affecting consumer health, business reputation, and legal standing. These consequences can range from minor inconveniences to catastrophic events that can jeopardize the survival of a food packing company.
- Foodborne Illness Outbreaks: The most direct consequence of poor food safety practices is the occurrence of foodborne illness outbreaks. Contaminated food can cause a wide range of illnesses, from mild discomfort to severe, life-threatening conditions. These outbreaks can lead to hospitalizations, long-term health complications, and even fatalities.
- Product Recalls: When a food product is found to be contaminated or poses a health risk, a product recall is often necessary. Recalls are costly and disruptive, involving the removal of products from shelves, the investigation of the source of contamination, and the implementation of corrective actions. A recall can significantly damage a company’s reputation and erode consumer trust.
- Legal Penalties and Fines: Food safety violations can result in significant legal penalties and fines. Regulatory agencies, such as the FDA in the United States, have the authority to issue warnings, impose fines, and even shut down food packing facilities that fail to comply with food safety regulations. The severity of the penalties depends on the nature and severity of the violations.
- Damage to Brand Reputation: A food safety incident can have a devastating impact on a company’s brand reputation. Negative publicity, consumer distrust, and loss of market share can result from a single incident. It can take years to rebuild a damaged reputation, and some companies may never fully recover.
- Loss of Business: Ultimately, failing to prioritize food safety and hygiene can lead to the loss of business. Consumers are increasingly aware of food safety issues and are likely to switch to brands they perceive as safer and more reliable. Food packing companies that consistently fail to meet food safety standards may lose contracts, face boycotts, and eventually go out of business.
Technology and Automation in Food Packing
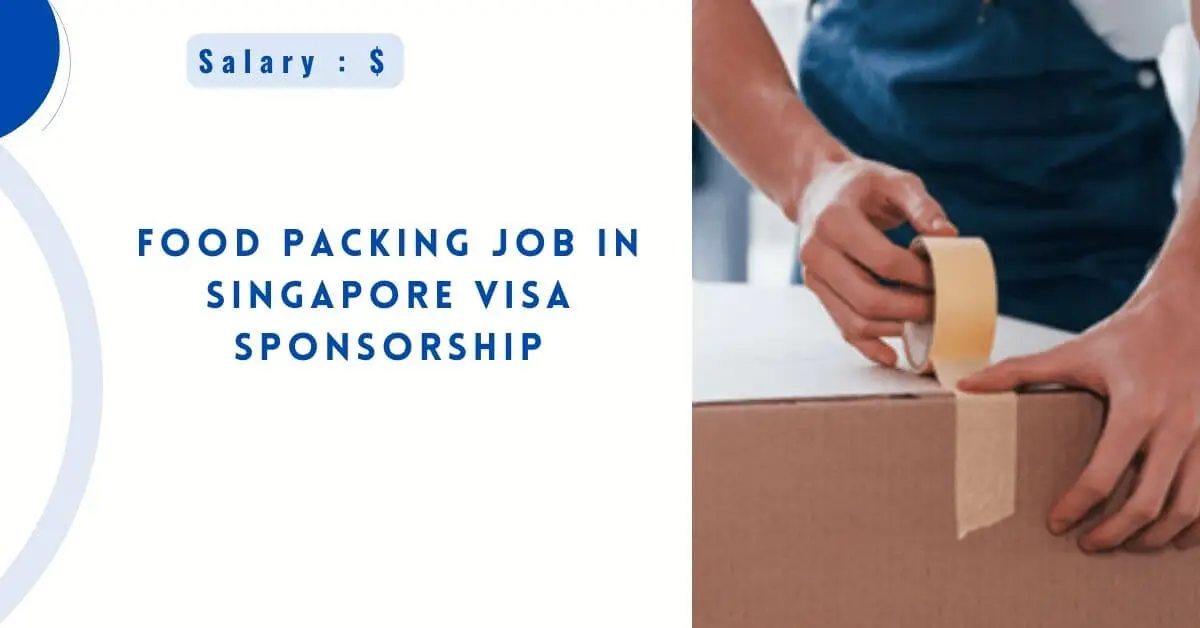
The food packing industry has undergone a significant transformation, largely driven by technological advancements and automation. These changes have dramatically impacted efficiency, safety, and the overall quality of packaged food products. From simple machinery to sophisticated robotics, technology has reshaped every aspect of the process, leading to greater precision, speed, and reduced labor costs.
Automation’s Impact on Food Packing Processes
Automation has revolutionized food packing processes, evolving from basic mechanical systems to highly integrated, computer-controlled operations. Early automation involved the introduction of conveyor belts and basic filling machines. These systems increased packing speeds compared to purely manual processes. Over time, more sophisticated technologies, such as programmable logic controllers (PLCs), were integrated, enabling automated control of various functions like weighing, labeling, and sealing.
Today, advanced systems incorporate robotics, vision systems, and artificial intelligence (AI) for tasks such as product sorting, inspection, and packaging. This evolution has resulted in higher throughput, reduced human error, and improved product consistency.
Advantages and Disadvantages of Automated Versus Manual Packing
Comparing automated and manual food packing reveals distinct advantages and disadvantages for each approach.
- Automated Packing Advantages: Automated systems offer several benefits, including increased speed and throughput. They can operate continuously, 24/7, leading to higher production volumes. Automation reduces labor costs and minimizes the potential for human error, resulting in consistent product quality. Automated systems also improve workplace safety by reducing the need for manual handling of heavy or repetitive tasks. Furthermore, they can handle complex packaging designs and maintain strict hygiene standards.
- Automated Packing Disadvantages: The initial investment for automated systems is substantial, requiring significant capital expenditure. These systems can be inflexible and difficult to adapt to changes in product size or packaging design. Maintenance and repair costs can be high, and downtime due to malfunctions can disrupt production. Moreover, automation may lead to job displacement, impacting the workforce.
- Manual Packing Advantages: Manual packing offers flexibility and adaptability, allowing for quick changes in product type or packaging design. It is cost-effective for small-scale operations or products with irregular shapes. Manual packing provides employment opportunities and allows for close inspection of products, enabling the identification of defects that automated systems might miss.
- Manual Packing Disadvantages: Manual packing is slower and less efficient than automated processes, leading to lower production volumes. It is labor-intensive, increasing labor costs. Human error is more likely, potentially resulting in inconsistencies in product quality. Manual processes are often less hygienic and may pose safety risks due to repetitive tasks or the handling of heavy items.
Advanced Technologies Used in Food Packing
Advanced technologies are transforming food packing, improving efficiency and precision. These technologies include robotic arms, vision systems, and advanced control systems.
- Robotic Arms: Robotic arms are increasingly used for various food packing tasks, such as picking and placing products, loading and unloading packaging materials, and palletizing finished goods. They are particularly effective in handling delicate or irregularly shaped items that are difficult for humans to handle efficiently. For example, in a bakery, robotic arms can precisely place pastries into trays, reducing product damage and increasing speed.
A common type of robotic arm is the articulated robot, which mimics a human arm’s movements, allowing for flexibility and precision in handling a variety of products.
- Vision Systems: Vision systems use cameras and image processing software to inspect products for defects, verify package integrity, and ensure proper labeling. These systems can identify issues such as incorrect fill levels, damaged packaging, or missing labels. They can also sort products based on size, shape, or color. For example, a vision system can inspect individual fruit pieces on a conveyor belt, rejecting any that are bruised or damaged.
This improves product quality and reduces waste.
- Advanced Control Systems: These systems, often based on PLCs and supervisory control and data acquisition (SCADA) systems, manage and monitor all aspects of the packing process. They control the speed of conveyor belts, the operation of filling machines, and the sealing of packages. SCADA systems provide real-time data on production rates, machine performance, and product quality. This data can be used to optimize the process, identify potential problems, and improve overall efficiency.
Career Progression in Food Packing
The food packing industry offers a variety of career advancement opportunities for dedicated and skilled individuals. Entry-level positions can serve as a foundation for climbing the career ladder, leading to supervisory, management, and even specialized roles. Continuous learning, the acquisition of new skills, and a commitment to excellence are key to progressing within this dynamic sector.
Potential Career Paths, Food packing jobs
Numerous career paths are available within the food packing industry, extending beyond the initial entry-level roles. These pathways provide opportunities for individuals to specialize in specific areas and take on increasing responsibilities.
- Line Worker/Packer: This is the foundational role, responsible for tasks such as assembling packaging, filling containers, and inspecting products. This role is crucial for understanding the fundamental processes within the food packing environment.
- Quality Control Inspector: Individuals in this role focus on ensuring product quality, adherence to safety standards, and compliance with regulations. They may conduct inspections, perform tests, and document findings.
- Machine Operator: Machine operators are responsible for the efficient operation and maintenance of packaging machinery, ensuring smooth production and minimizing downtime.
- Team Lead/Supervisor: With experience, individuals can progress to supervisory roles, overseeing a team of packers and ensuring production targets are met. They are responsible for training, scheduling, and performance management.
- Production Manager: Production managers oversee the entire food packing process, from raw materials to finished goods. They are responsible for optimizing efficiency, managing budgets, and ensuring quality control.
- Warehouse Manager: Warehouse managers oversee the storage and distribution of food products, ensuring efficient inventory management and adherence to safety regulations.
- Maintenance Technician: Maintenance technicians are responsible for the upkeep and repair of packaging equipment, minimizing downtime and ensuring the smooth operation of the production line.
- Food Scientist/Technologist: In larger organizations, food scientists or technologists may be involved in research and development, product innovation, and quality assurance.
Skills and Experience for Advancement
Advancing to supervisory or management roles in food packing requires a combination of practical experience and specific skills. Demonstrating leadership qualities, problem-solving abilities, and a commitment to continuous improvement are essential for career progression.
- Technical Skills: A strong understanding of food packing processes, machinery operation, and quality control procedures is essential.
- Leadership Skills: The ability to motivate, train, and manage a team effectively is crucial for supervisory roles. This includes conflict resolution, delegation, and performance management.
- Communication Skills: Effective communication is vital for interacting with team members, supervisors, and other departments. This includes both written and verbal communication.
- Problem-Solving Skills: The ability to identify and resolve production issues, equipment malfunctions, and quality control problems is highly valued.
- Analytical Skills: Analyzing data, identifying trends, and making informed decisions based on production metrics are important for optimizing efficiency and improving performance.
- Regulatory Knowledge: Understanding and adhering to food safety regulations, such as those established by the Food and Drug Administration (FDA), is critical.
- Experience: Relevant experience in food packing, coupled with a proven track record of performance and a willingness to learn, is often a prerequisite for advancement.
Typical Career Ladder
A typical career ladder within the food packing industry illustrates the progression from entry-level positions to more senior roles. This visual representation helps individuals understand the potential pathways for advancement and the skills and experience required at each stage.
Career Ladder Illustration:
This illustration shows a vertical structure with levels representing different roles. The base level represents the entry-level position and the top level represents the highest management position.
Level 1: Entry-Level Positions
- Food Packer/Line Worker: This is the starting point, where individuals learn the basics of food packing, packaging, and handling.
Level 2: Experienced Roles
- Quality Control Inspector: Focused on inspecting products and ensuring quality standards.
- Machine Operator: Responsible for operating and maintaining packaging machinery.
Level 3: Supervisory Roles
- Team Lead/Supervisor: Supervises a team of packers, ensuring efficient operations and adherence to standards.
Level 4: Management Roles
- Production Manager: Oversees the entire production process, including planning, scheduling, and quality control.
- Warehouse Manager: Manages the storage and distribution of food products.
Level 5: Senior Management Roles
- Plant Manager/General Manager: Responsible for the overall operation of the food packing facility.
Lateral Movement: The career ladder also allows for lateral movement. For example, a skilled Machine Operator could move to a Maintenance Technician role, or a Quality Control Inspector could specialize in a particular area, such as allergen control.
Finding and Applying for Food Packing Jobs
Securing a food packing position involves a strategic approach to job searching, application preparation, and interview performance. This section provides guidance on each of these crucial aspects to help you navigate the job market effectively.
Searching for Job Openings
Effectively searching for food packing positions requires utilizing various online and offline resources. Consider the following strategies to maximize your chances of finding suitable opportunities:
- Online Job Boards: Regularly check popular job boards like Indeed, LinkedIn, Glassdoor, and local job portals specific to your region. Use s such as “food packer,” “food production worker,” “packaging associate,” and include location-based terms (e.g., “food packing jobs in [city]”).
- Company Websites: Visit the career pages of food processing and manufacturing companies directly. Many companies post job openings on their own websites, sometimes before they appear on broader job boards.
- Staffing Agencies: Contact staffing agencies specializing in the food industry. These agencies often have access to a wider range of job openings and can assist with the application process.
- Networking: Inform your friends, family, and acquaintances about your job search. Personal connections can sometimes lead to job opportunities that are not widely advertised.
- Local Resources: Check with local community centers, employment offices, and trade schools for job postings and assistance.
Preparing a Resume and Cover Letter
Your resume and cover letter are critical for making a positive first impression. They should highlight relevant skills and experience in a clear and concise manner.
- Resume Content:
- Contact Information: Include your full name, phone number, email address, and LinkedIn profile (optional).
- Summary/Objective (Optional): A brief statement highlighting your key skills and career goals. Tailor this to the specific job you are applying for.
- Work Experience: List your previous jobs in reverse chronological order. For each role, include the company name, job title, dates of employment, and a bulleted list of responsibilities and accomplishments. Quantify your accomplishments whenever possible (e.g., “Packed an average of 150 units per hour”).
- Skills: Create a separate section for relevant skills. Include both hard skills (e.g., operating packaging machinery, quality control) and soft skills (e.g., teamwork, attention to detail, time management).
- Education: List your educational background, including the name of the institution, degree/diploma earned, and dates of attendance.
- Cover Letter:
- Personalization: Address the hiring manager by name if possible. Research the company and tailor your cover letter to the specific job requirements.
- Introduction: Clearly state the position you are applying for and where you found the job posting.
- Body Paragraphs: Highlight your relevant skills and experience, providing specific examples of how you have demonstrated those skills in previous roles. Explain why you are interested in the company and the food packing industry.
- Closing: Reiterate your interest in the position and thank the hiring manager for their time and consideration. Include a call to action, such as stating that you are available for an interview.
- Formatting and Proofreading: Use a clean and professional format for both your resume and cover letter. Proofread carefully for any grammatical errors or typos.
Preparing for Common Interview Questions
The interview is your opportunity to showcase your qualifications and personality. Preparing for common interview questions can significantly increase your confidence and improve your performance.
- Behavioral Questions: These questions assess your past behavior to predict future performance. Use the STAR method (Situation, Task, Action, Result) to structure your answers.
For example: “Tell me about a time you had to work as part of a team to meet a tight deadline.”
- Situational Questions: These questions present hypothetical scenarios to assess your problem-solving skills and decision-making abilities.
For example: “How would you handle a situation where you noticed a product was improperly sealed?”
- Technical Questions: These questions assess your knowledge of food packing processes and equipment.
For example: “Describe the steps involved in the food packing process.”
- Common Interview Questions:
- “Why are you interested in this food packing position?”
- “What experience do you have that makes you a good fit for this role?”
- “Describe your experience with quality control.”
- “How do you handle repetitive tasks?”
- “Are you comfortable working in a fast-paced environment?”
- “Do you have any experience with operating packaging machinery?”
- “What are your strengths and weaknesses?”
- “Why should we hire you?”
- “Do you have any questions for us?” (Prepare a few questions to show your interest in the company and the role.)
- Preparing for the Interview:
- Research the Company: Learn about the company’s products, values, and recent news.
- Practice Your Answers: Prepare answers to common interview questions and practice them aloud.
- Prepare Questions to Ask: Prepare a few thoughtful questions to ask the interviewer. This demonstrates your interest and engagement.
- Dress Professionally: Dress neatly and appropriately for the interview.
- Arrive on Time: Plan your route and arrive at the interview location a few minutes early.
- Be Enthusiastic: Show your enthusiasm for the position and the company.
- Follow Up: Send a thank-you note or email to the interviewer after the interview.
The Impact of Food Packing on the Supply Chain
Food packing is an indispensable component of the food supply chain, acting as a critical link between production, distribution, and consumption. Its influence extends beyond mere containment, significantly impacting efficiency, safety, and sustainability within the entire system. Effective food packing ensures that products reach consumers in optimal condition, minimizing waste and preserving quality.
The Role of Food Packing in the Overall Food Supply Chain
Food packing serves a multitude of crucial functions within the food supply chain. It acts as a protective barrier, a facilitator of transportation, and a communicator of essential information to both retailers and consumers. The design and implementation of food packing directly affect the efficiency and effectiveness of the chain.
The Importance of Efficient and Effective Packing in Minimizing Food Waste
Efficient and effective packing plays a pivotal role in minimizing food waste, a significant concern in the modern food industry. By extending shelf life, protecting against damage, and enabling optimal storage conditions, packing reduces the likelihood of spoilage and loss throughout the supply chain.
- Extending Shelf Life: Packing methods such as modified atmosphere packaging (MAP) and vacuum sealing are designed to inhibit the growth of microorganisms and slow down enzymatic reactions, thereby extending the shelf life of perishable goods. For example, MAP can significantly increase the shelf life of fresh produce, reducing waste at retail and consumer levels.
- Protecting Against Damage: Packing provides a physical barrier against damage during transportation and handling. This is particularly crucial for fragile items like fruits, vegetables, and baked goods. Robust packing materials, such as corrugated cardboard and protective inserts, prevent bruising, crushing, and other forms of damage that can render food inedible.
- Optimizing Storage Conditions: Packing can help maintain optimal storage conditions for food products. This includes controlling temperature, humidity, and light exposure. For instance, refrigerated packing and insulated containers are essential for preserving the quality of frozen foods and temperature-sensitive items during transit.
“Approximately one-third of the food produced for human consumption is lost or wasted globally, which amounts to about 1.3 billion tons per year.”
Food and Agriculture Organization of the United Nations (FAO).
The Role of Food Packing in Maintaining Product Quality and Freshness
Beyond waste reduction, food packing is crucial for maintaining product quality and freshness, impacting consumer satisfaction and the economic viability of the food industry. The choice of packing materials and methods directly influences the sensory attributes and nutritional value of the food product.
- Barrier Protection: Packing acts as a barrier against external factors that can degrade food quality. This includes moisture, oxygen, light, and contaminants. For example, airtight packing prevents oxidation, which can lead to rancidity in fats and oils.
- Maintaining Sensory Attributes: Packing helps preserve the sensory qualities of food, such as taste, aroma, texture, and appearance. For instance, the use of transparent packing allows consumers to visually assess the product’s quality, while aroma-barrier packing prevents the loss of volatile flavor compounds.
- Preserving Nutritional Value: Packing can help preserve the nutritional value of food by protecting it from degradation caused by light, oxygen, and other environmental factors. For example, packing fortified foods in opaque containers helps prevent the degradation of vitamins and other sensitive nutrients.
Future Trends in Food Packing
The food packing industry is constantly evolving, driven by consumer demand, technological advancements, and environmental concerns. Several emerging trends are poised to significantly reshape the industry, impacting everything from materials and processes to sustainability and supply chain efficiency. Understanding these trends is crucial for professionals in food packing to remain competitive and adaptable.
Emerging Trends in Food Packing
Several key trends are reshaping the food packing landscape. These trends reflect a shift towards greater efficiency, sustainability, and consumer convenience.
- Sustainable Packaging: This involves using materials that minimize environmental impact. This includes reducing packaging weight, using recycled or renewable materials, and designing packaging for recyclability or compostability.
- Smart Packaging: Smart packaging utilizes technologies like sensors and indicators to monitor product freshness, temperature, and other crucial factors. This can help reduce food waste and improve consumer safety.
- E-commerce Driven Packaging: The growth of online food sales is driving the need for packaging that can withstand shipping and handling, while also maintaining product quality and freshness.
- Personalized Packaging: There is a growing trend toward personalized packaging, which allows for customization based on consumer preferences, dietary needs, and even demographic data.
- Active and Intelligent Packaging: This involves packaging that actively interacts with the food product to extend shelf life, enhance safety, and improve quality. Examples include oxygen scavengers and antimicrobial films.
Impact of Trends on the Food Packing Industry
These trends are having a profound impact on various aspects of the food packing industry, from material selection and manufacturing processes to supply chain management and consumer perception.
- Material Innovation: The demand for sustainable packaging is driving innovation in materials. This includes the development of bio-based plastics, paper-based alternatives, and innovative recycling technologies. For example, companies are increasingly using mushroom packaging, made from agricultural waste, as a sustainable alternative to polystyrene.
- Process Optimization: Food packing companies are investing in new technologies and processes to improve efficiency, reduce waste, and enhance sustainability. This includes automation, lean manufacturing principles, and the adoption of closed-loop systems.
- Supply Chain Transformation: The need for greater transparency and traceability is leading to changes in supply chain management. Companies are using technologies like blockchain to track products from origin to consumer, ensuring food safety and authenticity.
- Consumer Engagement: Consumers are becoming more environmentally conscious and are demanding sustainable and transparent packaging. Companies are responding by communicating their sustainability efforts and providing consumers with information about packaging materials and recyclability.
Biodegradable Packaging and its Implications
Biodegradable packaging represents a significant shift towards environmental sustainability. This type of packaging is designed to break down naturally, reducing waste and minimizing the environmental footprint of food products.
The global biodegradable packaging market is projected to reach $113.4 billion by 2027, growing at a CAGR of 15.6% from 2020 to 2027.
- Benefits of Biodegradable Packaging: Biodegradable packaging offers several advantages, including reduced landfill waste, decreased reliance on fossil fuels, and lower greenhouse gas emissions. It can also contribute to soil health when composted.
- Types of Biodegradable Materials: A variety of materials are used in biodegradable packaging, including plant-based plastics (PLA), cellulose-based films, and starch-based materials. These materials can be derived from corn, sugarcane, and other renewable resources.
- Challenges and Considerations: While biodegradable packaging offers significant benefits, there are also challenges. These include higher costs compared to traditional packaging, the need for proper composting infrastructure, and potential limitations in terms of barrier properties and shelf life. The effectiveness of biodegradation can also depend on environmental conditions, such as temperature and humidity.
- Future Potential: The future of biodegradable packaging is promising, with ongoing research and development focused on improving material performance, reducing costs, and expanding the range of applications. Governments and regulatory bodies are also playing a role by promoting the use of sustainable packaging and providing incentives for companies to adopt biodegradable alternatives. For example, the European Union’s Single-Use Plastics Directive aims to reduce plastic waste by banning certain single-use plastic items and promoting the use of more sustainable alternatives.
Summary
In conclusion, food packing jobs offer a vital link in the journey of food from production to consumption. This industry is constantly evolving, driven by technological advancements and a growing emphasis on sustainability. Whether you’re seeking an entry-level position or aiming for a leadership role, understanding the nuances of food packing is key to a successful career. The future of food packing promises exciting innovations, making it a field ripe with opportunity for those who are prepared to embrace change and contribute to a more efficient and sustainable food system.