Food manufacturing jobs near me represent a vital segment of local economies, offering a diverse range of opportunities. This industry is experiencing consistent growth and stability, driven by the constant demand for food products. Employment rates in this sector remain relatively strong, and understanding the local landscape is key to finding the right fit. The industry offers numerous roles, from production line workers to specialized technicians, making it a dynamic field for those seeking employment.
This guide will explore the process of finding food manufacturing jobs, highlighting various roles, required skills, and the application process. We’ll delve into preparing your resume, navigating interviews, and understanding company culture. Furthermore, we will discuss career advancement, location-specific considerations, and salary expectations. Whether you’re a seasoned professional or just starting your career journey, this information will help you navigate the local food manufacturing job market effectively.
The Local Food Manufacturing Landscape
Food manufacturing jobs are crucial components of local economies, providing essential employment opportunities and contributing significantly to regional economic stability. These roles span a wide range of skill levels, from entry-level production positions to specialized roles in food science and engineering. The industry’s presence supports local suppliers, transportation networks, and related services, creating a ripple effect that benefits the broader community.The food manufacturing industry demonstrates consistent growth and resilience, even during economic downturns.
Demand for food remains constant, driving a need for continuous production and innovation. This inherent stability makes the sector an attractive option for job seekers and investors alike. Technological advancements, evolving consumer preferences, and a growing global population continue to fuel expansion and create new opportunities.
Employment Rates and Trends in the Food Manufacturing Sector
Employment rates in the food manufacturing sector generally remain stable or experience modest growth, reflecting the industry’s essential nature. Several factors contribute to this stability, including the consistent demand for food products and the ongoing need for efficient production and distribution.For instance, data from the Bureau of Labor Statistics (BLS) often reveals employment trends. While specific numbers fluctuate, the sector typically shows a lower rate of job loss compared to more volatile industries.
These trends highlight the importance of the food manufacturing industry to local and national economies.
- Example: Consider a hypothetical city with a major food processing plant. Even during a recession, this plant might reduce production slightly but rarely shuts down entirely. This consistent operation provides a safety net for local employment, unlike sectors like construction or tourism, which are more susceptible to economic cycles.
- Trend Analysis: Examining historical employment data often shows that food manufacturing jobs are less sensitive to external economic factors compared to other sectors. For example, during the 2008 financial crisis, many industries experienced significant layoffs, while food manufacturing maintained a relatively stable employment level.
- Technological Impact: The adoption of automation and advanced manufacturing technologies in food processing has created new job roles, often requiring specialized skills. This includes positions related to robotics, data analysis, and quality control, contributing to the sector’s evolution and ongoing relevance.
Consider this formula: Stability in food manufacturing = (Constant demand for food) + (Technological innovation) + (Adaptability to consumer trends).
Common Job Roles in Food Manufacturing
The food manufacturing industry offers a variety of roles, each contributing to the process of transforming raw ingredients into the products consumers enjoy. Understanding these different positions is crucial for anyone seeking employment in this sector. The responsibilities and required skills vary depending on the specific role, but all positions play a vital part in ensuring food safety, quality, and efficiency.
Production Worker Responsibilities
Production workers are the backbone of food manufacturing, directly involved in the processing and packaging of food products. Their tasks are critical to maintaining the production flow and ensuring that products meet quality standards.The duties of a Production Worker typically include:
- Operating and monitoring machinery used in food processing, such as mixers, ovens, and packaging equipment.
- Following established procedures and guidelines to ensure food safety and quality, including proper sanitation and hygiene practices.
- Inspecting products for defects and ensuring they meet specified standards.
- Packaging and labeling finished products according to established procedures.
- Maintaining a clean and organized work environment, adhering to safety protocols.
- Performing basic equipment maintenance and reporting any malfunctions to supervisors.
- Weighing and measuring ingredients accurately.
Quality Control Specialist Duties, Food manufacturing jobs near me
Quality Control Specialists are essential in maintaining the safety and quality of food products. They are responsible for monitoring and evaluating the production process to ensure that products meet established standards and comply with regulations.The duties of a Quality Control Specialist include:
- Conducting regular inspections of production areas, equipment, and products to identify potential issues.
- Performing laboratory tests on raw materials, in-process products, and finished goods to assess quality parameters such as pH, moisture content, and microbial levels.
- Analyzing data and preparing reports on quality control findings, identifying trends and recommending corrective actions.
- Ensuring compliance with food safety regulations and industry standards, such as HACCP (Hazard Analysis and Critical Control Points).
- Investigating customer complaints related to product quality and recommending solutions.
- Calibrating and maintaining quality control equipment.
- Collaborating with production and other departments to address quality issues and improve processes.
Food Processing Technician Role and Skills
Food Processing Technicians are skilled professionals who operate and maintain the complex machinery used in food manufacturing. They play a key role in ensuring efficient and effective production processes.The role of a Food Processing Technician encompasses a range of responsibilities and requires a specific skill set:
- Operating and troubleshooting food processing equipment, including machinery for mixing, cooking, extruding, and packaging.
- Performing routine maintenance and repairs on equipment to minimize downtime.
- Monitoring process parameters, such as temperature, pressure, and flow rates, to ensure optimal performance.
- Making adjustments to equipment settings to maintain product quality and consistency.
- Following established procedures and safety protocols.
- Maintaining accurate records of equipment performance and process parameters.
- Working with engineers and other specialists to optimize production processes.
Required skills for this role include:
- Mechanical aptitude and the ability to understand and operate complex machinery.
- Strong problem-solving skills and the ability to troubleshoot equipment malfunctions.
- Knowledge of food processing principles and techniques.
- Ability to read and interpret technical manuals and blueprints.
- Attention to detail and the ability to follow instructions accurately.
- Strong communication and teamwork skills.
Comparison of Entry-Level Positions
The following table compares and contrasts three entry-level positions within the food manufacturing industry, highlighting their key responsibilities and required skills. This information can assist job seekers in understanding the differences between roles and identifying the best fit for their skills and interests.
Position | Key Responsibilities | Required Skills |
---|---|---|
Production Worker | Operating machinery, inspecting products, packaging, and maintaining a clean work environment. | Ability to follow instructions, attention to detail, physical stamina, and basic mechanical aptitude. |
Quality Control Specialist | Inspecting products, conducting laboratory tests, analyzing data, and ensuring compliance with regulations. | Analytical skills, attention to detail, knowledge of food safety regulations, and laboratory experience. |
Food Processing Technician | Operating and maintaining processing equipment, monitoring process parameters, and troubleshooting malfunctions. | Mechanical aptitude, problem-solving skills, ability to read technical manuals, and knowledge of food processing principles. |
Required Skills and Qualifications
The food manufacturing industry demands a specific blend of skills and qualifications to ensure the production of safe, high-quality food products. This section Artikels the essential skills, how to showcase them, and the significance of certifications for various roles within this sector. Understanding these requirements is crucial for anyone seeking employment in food manufacturing.
Essential Skills for Food Manufacturing Jobs
Food manufacturing roles necessitate a combination of technical and soft skills. These skills contribute to efficient production, adherence to safety regulations, and effective teamwork.
- Technical Skills: These are job-specific abilities. They include operating machinery, understanding food processing techniques, and performing quality control checks. Specific examples include:
- Machine operation and maintenance: Proficiency in operating and troubleshooting various types of food processing equipment, such as mixers, fillers, and packaging machines.
- Food safety and sanitation: Knowledge of sanitation procedures, including cleaning and sanitizing equipment and work areas, and adherence to food safety regulations (e.g., GMPs).
- Ingredient handling and processing: Ability to accurately measure and combine ingredients according to recipes and processing specifications, understanding of different processing methods like cooking, baking, and preservation techniques.
- Quality control and assurance: Skills in performing quality checks, analyzing product samples, and identifying deviations from specifications.
- Basic computer skills: Use of computer systems for data entry, inventory management, and process control.
- Soft Skills: These interpersonal and professional attributes are essential for workplace success. They facilitate teamwork, communication, and problem-solving. Important soft skills include:
- Teamwork and collaboration: Ability to work effectively with colleagues, communicate clearly, and contribute to a positive team environment.
- Communication: Clear and concise written and verbal communication skills to convey information, report issues, and follow instructions.
- Problem-solving: Ability to identify and resolve issues related to production, equipment, or quality.
- Attention to detail: Meticulousness in following procedures, ensuring accuracy, and identifying potential problems.
- Physical stamina: Ability to stand for long periods, lift moderate weights, and perform repetitive tasks.
- Time management: Ability to manage time effectively and meet production deadlines.
Highlighting Relevant Skills on a Resume
Effectively presenting your skills on a resume is crucial for attracting the attention of potential employers. Tailoring your resume to each job application and using action verbs can significantly improve your chances.
Here’s how to effectively highlight your skills:
- Use a skills section: Create a dedicated section to list both technical and soft skills. Use s from the job description.
- Quantify your accomplishments: Whenever possible, quantify your achievements with numbers or data. For example, instead of saying “Improved production efficiency,” say “Improved production efficiency by 15% through process optimization.”
- Use action verbs: Start each bullet point with a strong action verb to describe your responsibilities and accomplishments. Examples include “Operated,” “Maintained,” “Inspected,” “Collaborated,” and “Resolved.”
- Tailor your resume: Customize your resume for each job application. Highlight the skills and experiences that are most relevant to the specific role.
- Provide examples: Include specific examples of how you’ve used your skills in previous roles or projects.
Importance of Certifications for Different Roles
Certifications are essential for demonstrating competence and commitment to food safety and quality. The specific certifications required vary depending on the role and responsibilities.
Here’s a comparison of certification importance for different roles:
Role | Typical Certifications | Importance |
---|---|---|
Production Worker | Food Handler Certification, Basic Food Safety | High: Demonstrates understanding of basic food safety principles and hygiene practices. |
Quality Control Technician | HACCP Certification, Food Safety Certifications, Internal Auditing | Very High: Ensures the ability to implement and maintain food safety programs, and perform audits. |
Supervisor/Manager | HACCP Certification, Food Safety Certifications, Leadership Certifications | Very High: Demonstrates leadership skills and understanding of food safety management systems. |
Maintenance Technician | Food Safety Certifications, Relevant Trade Certifications (e.g., electrical, mechanical) | High: Ensures equipment maintenance does not compromise food safety. |
Certifications such as HACCP (Hazard Analysis and Critical Control Points) are critical for roles involved in food safety management. HACCP certification demonstrates a comprehensive understanding of food safety principles and the ability to implement effective control measures. Food handler certifications are generally required for all employees involved in food handling to ensure basic hygiene practices.
Steps for Obtaining Relevant Certifications
Obtaining relevant certifications involves several steps, including training, examination, and ongoing education.
- Identify Required Certifications: Research the specific certifications required for the roles you are interested in. This information is often found in job descriptions or by contacting potential employers.
- Choose a Training Provider: Select a reputable training provider that offers the required certifications. Ensure the provider is accredited and the training meets industry standards.
- Complete the Training: Attend the training sessions and actively participate in the learning process. Take detailed notes and ask questions to ensure a thorough understanding of the material.
- Pass the Examination: Successfully pass the examination required for the certification. Prepare for the exam by reviewing the training materials and practicing with sample questions.
- Maintain Certification: Many certifications require ongoing education or recertification to maintain their validity. Stay updated on industry best practices and renew your certifications as required.
Preparing Your Application
Crafting a compelling application is crucial for securing a food manufacturing position. This section provides guidance on tailoring your resume and cover letter, highlighting relevant experience, and showcasing your skills effectively to capture the attention of potential employers. A well-prepared application demonstrates your understanding of the industry and your suitability for the role.
Tailoring Your Resume and Cover Letter
The key to a successful application lies in customization. Generic resumes and cover letters often fail to resonate with hiring managers. Instead, carefully tailor each document to align with the specific requirements and s Artikeld in the job description. This demonstrates your genuine interest in the role and your understanding of the company’s needs.* Resume Customization: Begin by thoroughly reviewing the job description.
Identify the key skills, qualifications, and responsibilities mentioned. Then, revise your resume to emphasize your relevant experience and skills, using s from the job posting. Quantify your accomplishments whenever possible, providing concrete examples of your achievements. For example, instead of stating “Improved efficiency,” write “Increased production efficiency by 15% through the implementation of a new process.”
Cover Letter Customization
Your cover letter provides an opportunity to elaborate on your resume and explain why you are a good fit for the specific role and company. Research the company’s values, mission, and recent news. Address the hiring manager by name, if possible. Clearly state the position you are applying for and how your skills and experience align with the job requirements.
Highlight your most relevant accomplishments and explain how you can contribute to the company’s success.
Action Verbs for Your Resume
Using strong action verbs can significantly enhance your resume, making your accomplishments more impactful and engaging. These verbs should be used to describe your responsibilities and achievements in past roles.Here are some examples of effective action verbs:* For Process Improvement: Analyzed, Optimized, Streamlined, Implemented, Enhanced, Improved, Refined, Standardized.
For Production and Operations
Operated, Maintained, Monitored, Controlled, Inspected, Coordinated, Supervised, Trained.
For Quality Control
Inspected, Verified, Tested, Evaluated, Assessed, Ensured, Complied, Adhered.
For Teamwork and Collaboration
Collaborated, Assisted, Supported, Communicated, Liaised, Coordinated, Facilitated, Partnered.
For Problem-Solving
Resolved, Addressed, Corrected, Investigated, Diagnosed, Identified, Recovered, Troubleshooted.
Highlighting Relevant Experience
Even if your experience isn’t directly in food manufacturing, you can still demonstrate your suitability for the role by highlighting transferable skills and relevant experiences. Focus on skills that are valuable in a food manufacturing environment, such as attention to detail, problem-solving, teamwork, and adherence to safety protocols.* Identify Transferable Skills: Consider your past roles and identify skills that are applicable to food manufacturing.
For example, experience in retail might demonstrate your ability to handle customer service, manage inventory, and work under pressure. Experience in a warehouse could showcase your understanding of logistics, inventory management, and safety procedures.
Quantify Your Achievements
Whenever possible, quantify your achievements to demonstrate your impact. For example, instead of stating “Managed inventory,” write “Managed inventory, reducing waste by 10% and improving stock accuracy.”
Tailor Your Application
Adjust your resume and cover letter to emphasize the skills and experiences that are most relevant to the specific job requirements.
Provide Context
When describing your experience, provide context to help the hiring manager understand how your skills and experiences relate to the food manufacturing industry.
In my previous role at [Previous Company], I was responsible for [Relevant Responsibility], which required a high degree of attention to detail and adherence to strict protocols. While not directly in food manufacturing, this experience has equipped me with a strong understanding of [Relevant Skill, e.g., quality control procedures, process optimization] and the ability to [Relevant Achievement, e.g., identify and resolve issues efficiently]. I am confident that these skills are highly transferable and will allow me to quickly contribute to the success of your team at [Company Name].
The Interview Process
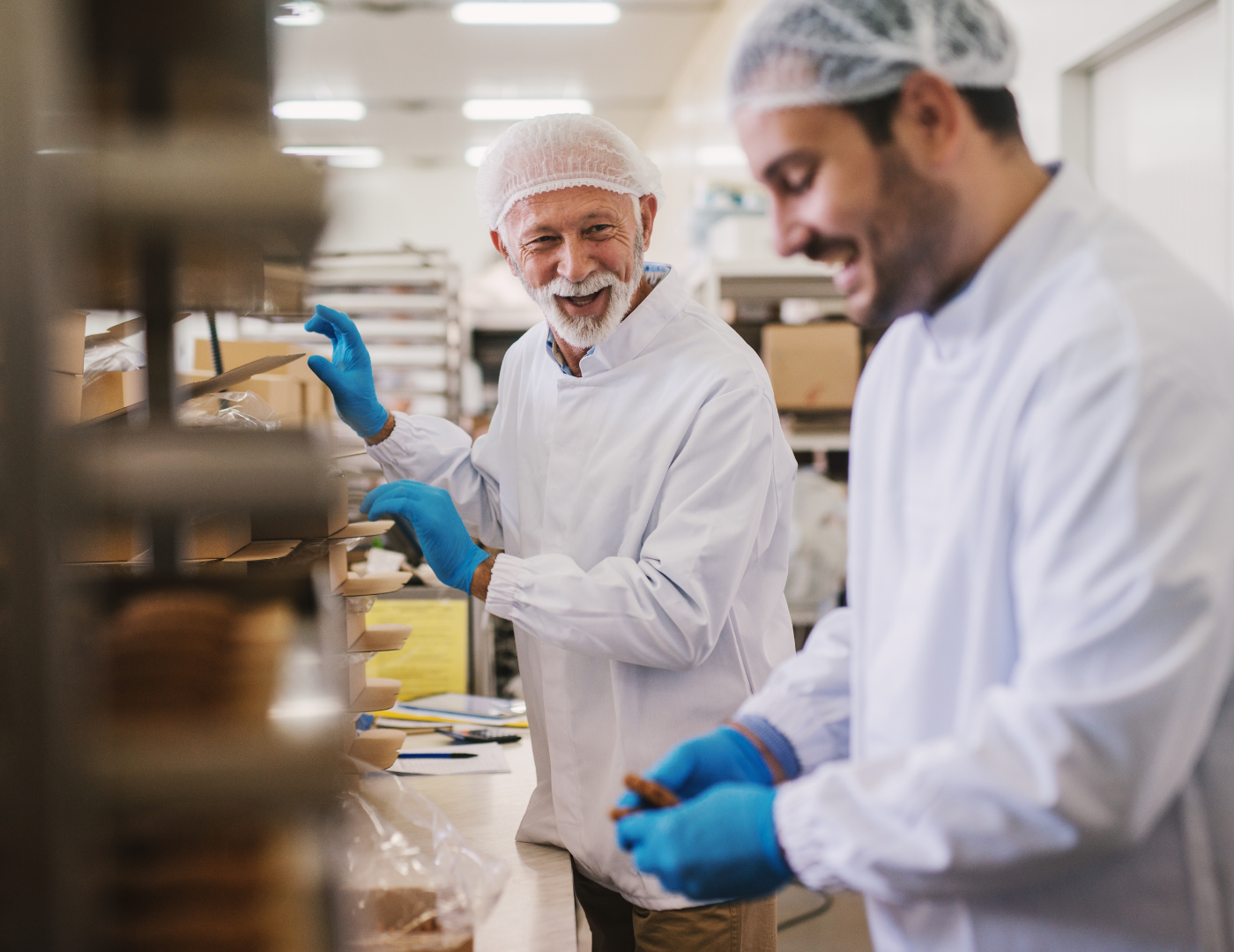
The interview is a crucial step in securing a food manufacturing job. It’s your opportunity to showcase your skills, experience, and personality to potential employers. This section will provide you with insights into common interview questions, preparation tips for plant tours, and strategies for addressing questions related to safety and working in a fast-paced environment.
Common Interview Questions Asked in Food Manufacturing
Understanding the types of questions you might encounter during a food manufacturing interview can significantly boost your confidence. Employers often assess your technical abilities, problem-solving skills, and ability to work as part of a team.
- Tell me about yourself: This is a common icebreaker, but don’t just reiterate your resume. Briefly highlight your relevant experience and skills, focusing on how they align with the job requirements. For example, “I have three years of experience in food processing, specializing in quality control and adhering to strict safety standards. My background includes operating and maintaining equipment, ensuring product consistency, and collaborating with team members to meet production goals.”
- Why are you interested in this position/company?: Research the company thoroughly. Show your enthusiasm by mentioning specific aspects of their products, values, or reputation that appeal to you. For instance, “I am particularly impressed by [Company Name]’s commitment to sustainable practices and its reputation for producing high-quality [product type]. This role aligns perfectly with my career goals, as I am eager to contribute to a company that prioritizes both product excellence and environmental responsibility.”
- Describe your experience with food safety regulations: Be prepared to discuss your understanding of HACCP, GMP, and other relevant regulations. Provide specific examples of how you have applied these principles in previous roles. You could say, “In my previous role, I was responsible for implementing and monitoring HACCP plans. I regularly conducted sanitation audits, identified potential hazards, and implemented corrective actions to ensure compliance with food safety standards.
For example, during a recent inspection, I identified a potential cross-contamination risk and immediately implemented a new cleaning protocol to mitigate the issue.”
- How do you handle stressful situations?: Food manufacturing can be demanding. Employers want to know how you manage pressure. Describe a time when you faced a challenging situation and how you resolved it. “In a previous role, we experienced a sudden equipment malfunction that threatened to halt production. I quickly assessed the situation, identified the root cause of the problem, and collaborated with the maintenance team to implement a temporary solution while we waited for the replacement parts.
This prevented a significant production delay and minimized the impact on our customers.”
- Describe your experience with [specific equipment or process]: Tailor your response to the specific requirements of the job. If the job involves operating a particular machine, highlight your experience with similar equipment or processes. For example, “I have extensive experience operating and maintaining [specific equipment]. I am proficient in [list specific skills, e.g., troubleshooting, calibration, and preventative maintenance]. In my previous role, I was responsible for optimizing the performance of [specific equipment], resulting in a [quantifiable result, e.g., 10% increase in efficiency].”
- What are your salary expectations?: Research industry standards for similar roles in your area. Be prepared to provide a salary range rather than a fixed number. You could say, “Based on my research and experience, I am looking for a salary in the range of $[X] to $[Y]. However, I am open to discussing this further based on the specific responsibilities and benefits offered.”
Tips on How to Prepare for a Plant Tour
Plant tours are often part of the interview process, providing a firsthand look at the work environment. Proper preparation can leave a positive impression on the interviewer.
- Research the Company’s Products and Processes: Before the tour, familiarize yourself with the company’s product line and manufacturing processes. This demonstrates your genuine interest and allows you to ask informed questions.
- Dress Appropriately: Wear closed-toe shoes and long pants or a skirt, if appropriate. Avoid loose clothing or jewelry that could pose a safety hazard. Dress in business casual attire unless specifically instructed otherwise.
- Follow Instructions: Pay close attention to any instructions provided by your tour guide. This includes safety protocols, designated pathways, and any restrictions on photography or note-taking.
- Ask Relevant Questions: Prepare a few thoughtful questions to ask during the tour. Focus on aspects of the production process, equipment, or company culture that interest you. For example, “What is the company’s approach to continuous improvement in the production process?” or “What are the opportunities for professional development within the company?”
- Observe and Take Notes (If Permitted): Pay attention to the cleanliness, organization, and efficiency of the plant. If allowed, take notes on your observations and any questions that arise.
- Demonstrate Enthusiasm and Respect: Show genuine interest in the company and its operations. Be polite and respectful to all employees you encounter.
Demonstrating Your Understanding of Safety Protocols and Procedures
Safety is paramount in food manufacturing. Interviewers will assess your knowledge and commitment to safety protocols.
- Highlight Your Knowledge of Safety Regulations: Be prepared to discuss your understanding of relevant safety regulations, such as OSHA standards and company-specific safety policies. For example, “I am familiar with OSHA regulations and understand the importance of following safety protocols to prevent accidents and injuries. In my previous role, I actively participated in safety training programs and consistently adhered to all safety guidelines.”
- Provide Specific Examples of Safety Practices: Offer specific examples of how you have implemented safety procedures in the past. For example, “In my previous role, I was responsible for conducting pre-shift safety checks on equipment, ensuring that all safety guards were in place and functioning correctly. I also participated in regular safety audits and identified potential hazards, such as trip hazards or improper labeling, and took immediate action to correct them.”
- Emphasize Your Commitment to Reporting Safety Concerns: Demonstrate your willingness to report any safety concerns or potential hazards you observe. “I believe that open communication is crucial for maintaining a safe work environment. I would never hesitate to report any safety concerns to my supervisor or the safety department. I am committed to taking immediate action to address any potential hazards.”
- Describe Your Experience with Personal Protective Equipment (PPE): Be prepared to discuss your experience with PPE, such as gloves, safety glasses, and hearing protection. Explain how you have used PPE to protect yourself and others from hazards. For example, “I am proficient in using various types of PPE, including gloves, safety glasses, and hearing protection. I understand the importance of wearing the correct PPE for each task and ensuring that it is properly fitted and maintained.
I have always made sure that I used the correct PPE in my past jobs.”
- Discuss Your Understanding of Hazard Communication: Demonstrate your understanding of hazard communication, including the importance of proper labeling, material safety data sheets (MSDS), and chemical handling procedures. “I am familiar with hazard communication standards and understand the importance of properly labeling chemicals and using MSDS to identify potential hazards. I have always followed the proper procedures for handling chemicals, including wearing the appropriate PPE and storing them in a safe location.”
Handling Questions About Your Ability to Work in a Fast-Paced Environment
Food manufacturing often involves tight deadlines and high production volumes. Interviewers will assess your ability to thrive in a fast-paced environment.
- Provide Examples of Your Ability to Manage Time and Prioritize Tasks: Describe situations where you have successfully managed multiple tasks simultaneously and met deadlines. For example, “In my previous role, I was responsible for managing multiple production lines, each with its own set of deadlines and requirements. To stay organized, I used a scheduling system to prioritize tasks and allocate resources effectively. I was able to consistently meet production targets and minimize downtime by using the correct system.”
- Highlight Your Adaptability and Problem-Solving Skills: Food manufacturing can be unpredictable. Demonstrate your ability to adapt to changing priorities and solve problems quickly. “During a recent production run, we encountered an unexpected equipment malfunction that threatened to delay the entire process. I quickly assessed the situation, identified the root cause of the problem, and worked with the maintenance team to implement a temporary solution. I also adjusted our production schedule to minimize the impact on our customers.”
- Emphasize Your Ability to Work Under Pressure: Describe how you have handled stressful situations and maintained your composure. For example, “I thrive in fast-paced environments. I have found that staying calm and focused is crucial for making good decisions under pressure. I often use techniques like taking deep breaths and breaking down complex tasks into smaller, more manageable steps to stay focused.”
- Demonstrate Your Teamwork Skills: Explain how you collaborate with others to achieve common goals, especially during busy periods. “I am a strong team player and believe that effective communication and collaboration are essential for success in a fast-paced environment. In my previous role, I worked closely with other team members to ensure that all production targets were met. I always offered support and assistance to my colleagues, especially during peak periods.”
- Discuss Your Commitment to Continuous Improvement: Highlight your willingness to learn new skills and improve your performance. “I am always looking for ways to improve my efficiency and effectiveness. I am open to learning new skills and techniques that can help me work more productively. I believe that continuous improvement is essential for success in any fast-paced environment.”
Company Culture and Work Environment
Understanding the company culture and work environment is crucial when considering a food manufacturing job. This knowledge helps prospective employees assess whether a particular company aligns with their values and preferences, impacting job satisfaction and overall well-being. This section will delve into the typical work environment, benefits, and safety measures prevalent in food manufacturing facilities.
Typical Work Environment in a Food Manufacturing Facility
The work environment in a food manufacturing facility is often fast-paced and production-driven. Employees typically work in a controlled environment, often temperature-regulated to maintain food safety and quality. Depending on the specific role, the environment may involve standing for extended periods, repetitive motions, and the use of machinery.The physical layout of a facility usually includes:
- Production Lines: Where food products are assembled, processed, and packaged. These lines can be highly automated, with workers overseeing machinery or performing specific tasks along the line.
- Processing Areas: Dedicated to cooking, mixing, or otherwise preparing food ingredients.
- Packaging and Labeling Areas: Where products are prepared for distribution, including labeling and sealing.
- Warehouse and Storage: Where raw materials and finished goods are stored, often requiring adherence to strict temperature and humidity controls.
- Quality Control Labs: Where samples are tested for safety, quality, and adherence to regulatory standards.
Hygiene and cleanliness are paramount in food manufacturing. Employees are expected to adhere to strict hygiene protocols, including wearing appropriate protective gear such as hairnets, gloves, and sometimes, protective clothing. The work environment is subject to regular cleaning and sanitation procedures to prevent contamination. Noise levels can vary depending on the equipment used, and in some areas, hearing protection may be required.
Shift work, including evenings, weekends, and holidays, is common to maintain continuous production.
Benefits Offered by Different Companies
Benefits packages vary considerably between food manufacturing companies, and are a significant factor in attracting and retaining employees. These packages can include a combination of financial and non-financial incentives. Companies often offer competitive salaries, health insurance, and retirement plans.Beyond these core benefits, many companies also offer:
- Paid Time Off (PTO): Includes vacation time, sick leave, and holidays. The amount of PTO varies based on tenure and company policy.
- Health Insurance: Covering medical, dental, and vision care. Plans may include options for employees and their families.
- Retirement Plans: Often in the form of 401(k) plans, with or without company matching contributions.
- Life Insurance: Providing financial protection to beneficiaries in the event of an employee’s death.
- Disability Insurance: Offering income replacement if an employee becomes disabled and unable to work.
- Employee Assistance Programs (EAPs): Providing confidential counseling and support services for personal and work-related issues.
- Wellness Programs: Promoting employee health through initiatives such as gym memberships, health screenings, and wellness challenges.
- Training and Development: Opportunities for employees to enhance their skills and advance their careers.
- Employee Discounts: Discounts on company products or services.
Workplace Safety Measures and Procedures
Workplace safety is a top priority in food manufacturing due to the inherent risks associated with machinery, chemicals, and the handling of food products. Companies implement various safety measures and procedures to protect employees from injury and illness.Common safety measures include:
- Personal Protective Equipment (PPE): Employees are required to wear appropriate PPE, such as safety glasses, gloves, hairnets, and steel-toed boots.
- Machine Guarding: Machines are equipped with guards to prevent contact with moving parts.
- Lockout/Tagout Procedures: To ensure that equipment is properly de-energized and isolated during maintenance and repairs.
- Hazard Communication Programs: Providing employees with information about the chemicals they work with, including safety data sheets (SDS).
- Emergency Procedures: Including evacuation plans, fire drills, and first-aid training.
- Ergonomics Programs: To minimize the risk of musculoskeletal disorders caused by repetitive motions or awkward postures.
- Regular Inspections and Audits: To identify and correct potential safety hazards.
- Employee Training: On safety procedures, hazard recognition, and the proper use of equipment.
These measures are often guided by regulations from agencies like the Occupational Safety and Health Administration (OSHA). Compliance with these regulations is essential for ensuring a safe work environment. Companies often have dedicated safety teams that oversee these programs and provide training to employees.
Comparison of Benefits Offered by Various Food Manufacturing Companies
The following table provides a hypothetical comparison of benefits offered by three different food manufacturing companies. This is an illustrative example and does not represent actual company offerings.
Benefit | Company A | Company B | Company C |
---|---|---|---|
Salary | Competitive, based on experience | Above Average, with performance bonuses | Entry-level, with opportunities for advancement |
Health Insurance | Comprehensive, with employee and family coverage | High-deductible plan with Health Savings Account (HSA) | Basic plan, with options to upgrade at employee cost |
Retirement Plan | 401(k) with 4% company match | 401(k) with 6% company match and profit sharing | 401(k) plan only |
Paid Time Off (PTO) | 15 days per year, increasing with tenure | 20 days per year | 10 days per year |
Life Insurance | Company-paid policy | Company-paid policy with options for additional coverage | Optional, at employee cost |
Disability Insurance | Short-term and long-term disability coverage | Short-term disability coverage only | None |
Employee Assistance Program (EAP) | Yes | Yes | No |
Wellness Program | Gym membership reimbursement | Wellness challenges and health screenings | None |
Training and Development | On-the-job training and tuition reimbursement | Opportunities for leadership development | Limited |
Employee Discounts | Discount on company products | Discount on company products and partner retailers | None |
Training and Career Advancement
The food manufacturing industry offers a variety of training programs and career advancement opportunities for individuals at all levels. From entry-level positions to management roles, there are pathways for professional growth and development. Investing in training and pursuing continuous learning is crucial for long-term success in this dynamic sector.
Training Programs for New Employees
Many food manufacturing companies provide comprehensive training programs to onboard new employees and equip them with the necessary skills and knowledge. These programs typically cover a range of topics designed to ensure employees understand their roles and contribute effectively to the production process.
- Orientation and Onboarding: This initial phase introduces new hires to the company culture, safety protocols, and overall operational procedures. It often includes facility tours, introductions to key personnel, and explanations of company policies.
- Job-Specific Training: Employees receive hands-on training tailored to their specific job responsibilities. This may involve learning how to operate machinery, follow production procedures, perform quality control checks, and maintain equipment. For example, a line worker might be trained on operating a filling machine, while a sanitation worker would be trained on proper cleaning and sanitization techniques.
- Safety Training: Safety is paramount in food manufacturing. Training programs emphasize workplace safety, including the use of personal protective equipment (PPE), hazard identification, and emergency procedures. Companies adhere to stringent safety regulations, such as those set by OSHA (Occupational Safety and Health Administration) in the United States, to minimize risks.
- Food Safety and Hygiene Training: Employees are educated on food safety regulations, hygiene practices, and the prevention of contamination. This includes understanding Good Manufacturing Practices (GMPs), Hazard Analysis and Critical Control Points (HACCP) principles, and allergen control.
- Equipment Operation and Maintenance: Training on the operation, maintenance, and troubleshooting of machinery is a key component for many roles. This ensures efficient production and minimizes downtime. This could involve learning how to calibrate scales, adjust conveyor belts, or perform basic preventative maintenance.
- Cross-Training: Some companies offer cross-training programs to provide employees with skills in multiple areas. This increases flexibility and allows employees to take on different roles as needed.
Opportunities for Career Progression
The food manufacturing industry offers numerous avenues for career advancement. Employees who demonstrate dedication, acquire new skills, and take initiative can move up the ranks and assume greater responsibilities. Career progression often depends on performance, experience, and the pursuit of further education or training.
- Promotions: Employees can be promoted to positions with increased responsibility and higher pay. This could involve moving from a line worker to a team lead, supervisor, or production manager.
- Skill Development: Acquiring new skills, such as advanced machinery operation, quality control techniques, or supervisory skills, can lead to career advancement.
- Education and Certifications: Pursuing relevant certifications (e.g., HACCP certification, food safety certifications) or obtaining a degree or diploma in a related field (e.g., food science, engineering, management) can significantly enhance career prospects.
- Lateral Moves: Employees may also move laterally within the company to gain experience in different departments or roles. This can broaden their skill set and prepare them for future promotions.
- Management Training Programs: Some companies offer management training programs designed to develop leadership skills and prepare employees for management roles.
Seeking Opportunities for Professional Development
Proactive individuals can actively seek opportunities for professional development to enhance their skills and advance their careers. This involves identifying areas for improvement, pursuing relevant training, and networking within the industry.
- Identify Skill Gaps: Assess current skills and identify areas where improvement is needed. This can involve self-assessment, feedback from supervisors, or analyzing job descriptions for desired roles.
- Seek Training Programs: Participate in company-sponsored training programs, workshops, seminars, and online courses.
- Pursue Certifications: Obtain relevant certifications to demonstrate expertise in specific areas, such as food safety, quality control, or equipment operation.
- Further Education: Consider pursuing a degree or diploma in a related field, such as food science, engineering, or business administration.
- Mentorship and Networking: Seek mentorship from experienced professionals in the industry and build a professional network by attending industry events, joining professional organizations, and connecting with colleagues.
- Performance Reviews: Actively participate in performance reviews and discuss career goals with supervisors. Use feedback to identify areas for improvement and create a development plan.
- Stay Updated on Industry Trends: Keep abreast of the latest industry trends, technologies, and regulations by reading industry publications, attending conferences, and participating in online forums.
Potential Career Paths within the Industry
The food manufacturing industry offers a diverse range of career paths, each with its own set of responsibilities and requirements. These paths can lead to various levels of responsibility and management.
- Production Worker: Operates machinery, assembles products, and performs tasks on the production line.
- Line Lead/Supervisor: Oversees a team of production workers, ensuring efficient operations and adherence to quality standards.
- Quality Control Technician: Conducts inspections, tests, and analyses to ensure product quality and compliance with regulations.
- Food Scientist/Technologist: Develops new food products, improves existing formulas, and researches food processing techniques.
- Maintenance Technician: Maintains and repairs machinery and equipment to ensure smooth production operations.
- Packaging Specialist: Oversees the packaging process, ensuring proper labeling, sealing, and protection of products.
- Warehouse/Logistics Manager: Manages the storage, inventory, and distribution of raw materials and finished products.
- Production Manager: Oversees the entire production process, including planning, scheduling, and resource allocation.
- Plant Manager: Responsible for the overall operation of a food manufacturing plant, including production, quality control, and safety.
- Research and Development (R&D) Manager: Leads the R&D department, overseeing the development of new products and processes.
- Supply Chain Manager: Manages the flow of raw materials and finished products, ensuring efficient and cost-effective operations.
Location-Specific Considerations: Food Manufacturing Jobs Near Me
Understanding the local landscape is crucial when searching for food manufacturing jobs. Your geographic location significantly impacts job availability, transportation options, cost of living, and the specific companies you can consider. This section provides guidance on navigating these location-specific factors to increase your chances of success.
Addressing Location-Specific Factors
Considering location-specific factors allows for a more informed job search. These factors can significantly affect your daily life and career choices.
- Transportation: Assess transportation options. Proximity to public transit or the need for a personal vehicle impacts commuting time and expenses. Consider factors such as traffic patterns and the availability of ride-sharing services. For example, if you live in a city with a robust public transportation system, you might be able to access more job opportunities outside your immediate neighborhood compared to living in a rural area where a car is essential.
- Cost of Living: Research the cost of living in your area. Housing, food, transportation, and healthcare expenses vary widely by location. Websites like Numbeo or Zillow can help you compare costs between different cities. Understanding the cost of living helps you assess the salary needed to maintain a comfortable lifestyle. For instance, a job paying $60,000 in a high-cost-of-living city might feel less lucrative than a job paying $50,000 in a lower-cost-of-living area.
- Housing: Determine the availability and affordability of housing near potential workplaces. The proximity of housing can greatly impact your commute and work-life balance. Explore different neighborhoods to find areas that offer a balance of affordability, safety, and convenience.
- Local Amenities: Consider the availability of local amenities, such as grocery stores, restaurants, and recreational facilities. These factors contribute to your overall quality of life and can influence your decision to accept a job offer.
Local Food Manufacturing Companies with Strong Reputations
Identifying reputable local food manufacturing companies is an essential step in your job search. These companies often offer better benefits, career growth opportunities, and a more stable work environment. Researching companies in your area will provide you with valuable insights.
The following examples illustrate how to find reputable companies:
- Online Research: Use online search engines and company review websites like Glassdoor, Indeed, and LinkedIn to research local food manufacturing companies. Look for companies with positive employee reviews, good ratings, and a history of stability.
- Networking: Connect with people in the food manufacturing industry through LinkedIn, professional organizations, or industry events. Networking can provide you with valuable insights into company cultures and reputations.
- Local Business Directories: Consult local business directories, chambers of commerce websites, and industry publications to identify food manufacturing companies in your area.
- Example: In a city like Chicago, known for its food processing industry, consider companies such as Conagra Brands, Kraft Heinz, or Archer Daniels Midland (ADM). In smaller cities or regions, look for well-established regional or local brands.
Resources for Understanding Local Labor Market Trends
Understanding local labor market trends is crucial for making informed decisions about your job search. These trends can provide insights into the demand for food manufacturing workers, salary expectations, and the skills that are in high demand.
- Government Agencies: Consult the U.S. Bureau of Labor Statistics (BLS) for national and regional employment data. State and local workforce development agencies also provide valuable information on local labor market trends.
- Industry Associations: Explore resources from industry associations such as the Food Processing Suppliers Association (FPSA) or the Institute of Food Technologists (IFT). These organizations often publish reports and data on industry trends.
- Local Newspapers and Business Publications: Read local newspapers and business publications to stay informed about job growth, company expansions, and industry developments in your area.
- Online Job Boards: Monitor online job boards like Indeed, LinkedIn, and Monster for information on job postings, salary ranges, and the skills employers are seeking.
- Example: If BLS data indicates a projected growth in food processing jobs in your state, it suggests a positive outlook for your job search. Local news reports about a new food manufacturing plant opening in your city can indicate increased job opportunities.
Impact of Geographic Location on Job Availability
Your geographic location directly impacts the availability of food manufacturing jobs. Certain regions have a higher concentration of food processing facilities due to factors such as access to raw materials, transportation infrastructure, and a skilled workforce.
- Regional Specialization: Some regions specialize in specific types of food manufacturing. For example, the Midwest is a major hub for meatpacking and dairy processing, while California is known for fruit and vegetable processing.
- Proximity to Raw Materials: Food manufacturing companies often locate near sources of raw materials to reduce transportation costs. Consider locations near agricultural areas, such as farms and orchards.
- Transportation Infrastructure: Access to transportation infrastructure, such as highways, railroads, and ports, is crucial for food manufacturing. Companies often locate in areas with efficient transportation networks.
- Availability of a Skilled Workforce: Regions with a skilled workforce in food processing, including food scientists, engineers, and production workers, tend to attract more food manufacturing companies.
- Example: If you live in an agricultural region, such as the Central Valley of California, you may find more job opportunities in fruit and vegetable processing compared to a region with less agricultural activity. Similarly, living near a major port or rail hub could provide access to companies involved in food distribution and logistics.
Salary and Benefits
Understanding the compensation and benefits landscape is crucial when exploring food manufacturing job opportunities. This section provides insights into average salary ranges, benefit packages, and the importance of negotiation to ensure you receive a competitive offer.
Average Salary Ranges for Food Manufacturing Positions
Salary levels in food manufacturing vary significantly based on factors such as job title, experience, location, and the size of the employing company. Entry-level positions typically command lower salaries, while roles requiring specialized skills or management responsibilities offer higher compensation.
Discover how fussy cat dry food has transformed methods in this topic.
- Entry-Level Production Workers: These roles often involve tasks like packaging, labeling, and operating basic machinery. The average annual salary can range from $28,000 to $35,000.
- Food Processing Technicians: Technicians often work with more complex equipment and may be responsible for quality control. Salaries can range from $35,000 to $50,000 annually.
- Supervisors and Team Leads: These positions oversee production teams and ensure efficient operations. Salaries generally fall between $45,000 and $65,000 per year.
- Quality Assurance/Quality Control (QA/QC) Specialists: QA/QC professionals are responsible for maintaining food safety and quality standards. Their salary typically ranges from $50,000 to $75,000 annually.
- Food Scientists and Technologists: Professionals in this field research and develop new food products and processes. Depending on experience and education, their salaries can range from $60,000 to over $100,000 per year.
- Plant Managers: Plant managers oversee all aspects of a food manufacturing facility, including production, maintenance, and personnel. Salaries can range from $80,000 to $150,000 or more, depending on the plant’s size and complexity.
Comparison of Benefits Packages Offered by Different Employers
Benefits packages are a significant component of overall compensation, and they can vary considerably between employers. These packages often include health insurance, retirement plans, paid time off, and other perks that enhance the employee experience.
- Health Insurance: Most employers offer health insurance, which may include medical, dental, and vision coverage. The level of coverage and the portion of the premium paid by the employer vary. Some companies offer health savings accounts (HSAs) or flexible spending accounts (FSAs) to help employees manage healthcare costs.
- Retirement Plans: Retirement plans, such as 401(k) plans, are common. Many employers offer matching contributions to encourage employees to save for retirement.
- Paid Time Off (PTO): PTO includes vacation time, sick leave, and holidays. The amount of PTO offered depends on the company’s policies and the employee’s length of service.
- Other Benefits: Other potential benefits include life insurance, disability insurance, employee assistance programs (EAPs), tuition reimbursement, and employee discounts on company products. Some companies also offer bonuses, profit-sharing plans, and opportunities for professional development.
Importance of Negotiating Salary and Benefits
Negotiating your salary and benefits is a critical step in securing the best possible employment package. Researching industry standards, understanding your worth, and clearly communicating your needs are essential for a successful negotiation.
- Research: Before negotiations, research the average salary range for the position and your experience level in your location. Websites like Glassdoor, Salary.com, and the Bureau of Labor Statistics can provide valuable data.
- Know Your Worth: Evaluate your skills, experience, and accomplishments. Quantify your achievements whenever possible. This will strengthen your position during negotiations.
- Be Prepared to Discuss Benefits: Determine which benefits are most important to you, such as health insurance, retirement contributions, or paid time off. Be prepared to discuss your needs and preferences with the employer.
- Be Confident and Professional: Approach the negotiation with confidence and a professional demeanor. Be clear about your salary expectations and the benefits you are seeking.
- Be Willing to Compromise: While it’s important to advocate for your needs, be prepared to compromise. You may not get everything you want, but you can often reach an agreement that meets your most important priorities.
“According to the U.S. Bureau of Labor Statistics, the median annual wage for food scientists and technologists was $79,130 in May 2023. The median wage is the wage at which half the workers in an occupation earned more than that amount and half earned less. The lowest 10 percent earned less than $46,870, and the highest 10 percent earned more than $138,380.”
Finding and Contacting Recruiters
Finding the right job in food manufacturing can be significantly streamlined by connecting with specialized recruiters. These professionals have established networks within the industry and can provide access to opportunities that might not be publicly advertised. Building relationships with recruiters can also offer valuable insights into the current job market and improve your application process.
Online Platforms and Agencies for Food Manufacturing Recruitment
Several online platforms and recruitment agencies concentrate on food manufacturing jobs. Utilizing these resources can dramatically improve your chances of finding suitable employment.
- LinkedIn: LinkedIn is a powerful professional networking platform where you can search for recruiters specializing in food manufacturing. You can also join relevant groups and connect with hiring managers directly. Many companies and recruiters actively post job openings on LinkedIn.
- Indeed: Indeed is a broad job search engine that allows you to filter by industry and location. You can search for “food manufacturing recruiter” or specific job titles to find relevant postings.
- Specialized Recruitment Agencies: Many recruitment agencies focus exclusively on the food and beverage industry. These agencies often have a deep understanding of the sector’s needs and can connect you with niche roles. Examples include Agri-Food Recruiters, FoodGrads, and other regional agencies.
- Company Websites: Many large food manufacturing companies have dedicated career pages on their websites. These pages may list open positions and provide contact information for their internal recruiters.
Crafting an Effective Outreach Message to a Recruiter
When reaching out to a recruiter, it’s essential to create a concise and compelling message that highlights your relevant skills and experience. A well-crafted outreach message significantly increases the likelihood of a response and a potential interview.
Subject: Food Manufacturing Professional – [Your Name]
[Specific Role/Area of Interest]
Your outreach message should include a brief introduction, highlighting your relevant experience and skills, and clearly stating your job search objectives.
- Personalize Your Message: Address the recruiter by name and mention something specific about their agency or their recent activity on LinkedIn. This demonstrates that you’ve done your research.
- Highlight Relevant Experience: Briefly summarize your experience in food manufacturing, focusing on the skills and accomplishments most relevant to the types of roles the recruiter typically handles.
- State Your Objectives: Clearly state the types of roles you are seeking, your desired location, and your availability.
- Attach Your Resume: Always include your resume as an attachment. Make sure it is up-to-date and tailored to food manufacturing roles.
- Express Enthusiasm: Conclude by expressing your interest in learning more about potential opportunities and thanking the recruiter for their time.
Building Relationships with Recruiters
Building and maintaining relationships with recruiters is a long-term strategy that can yield significant benefits throughout your career. Consistent engagement and professionalism are key to cultivating a positive and productive relationship.
- Be Responsive: Respond promptly to any communication from the recruiter, whether it’s an email, phone call, or LinkedIn message.
- Provide Updates: Keep the recruiter informed of any changes in your job search status, such as interviews, job offers, or changes in your availability.
- Be Professional: Always maintain a professional demeanor in your interactions with the recruiter, even if you are not currently seeking a job.
- Network: Attend industry events and conferences where recruiters may be present. This provides an opportunity to meet them in person and build rapport.
- Provide Referrals: If you know of other qualified candidates who are looking for jobs in food manufacturing, consider referring them to the recruiter. This can strengthen your relationship.
Information to Include in a Recruiter Inquiry
Providing comprehensive and relevant information in your initial inquiry allows the recruiter to assess your suitability for available roles and provide more targeted assistance. A thorough inquiry saves time and increases the likelihood of a successful placement.
When contacting a recruiter, include the following information:
- Your Contact Information: Include your full name, phone number, email address, and LinkedIn profile URL.
- Your Resume: Always attach your most up-to-date resume in a widely compatible format (e.g., PDF or DOCX).
- Job Search Objectives: Clearly state the types of roles you are interested in, such as production supervisor, quality control manager, or food scientist.
- Desired Location: Specify your preferred geographic locations for employment, including cities, regions, or states.
- Salary Expectations: Provide your salary expectations or range, which helps the recruiter match you with appropriate opportunities. Research industry standards to make your expectations realistic.
- Availability: Indicate your availability to start a new position.
- Skills and Experience Summary: Briefly summarize your key skills and experience, highlighting your most relevant accomplishments in food manufacturing.
- Certifications and Licenses: List any relevant certifications or licenses, such as HACCP certification, food safety certifications, or specialized training.
Safety Protocols and Regulations
Food manufacturing environments prioritize stringent safety protocols and regulations to protect both employees and consumers. Adherence to these guidelines is paramount, ensuring the production of safe, high-quality food products and minimizing workplace hazards. Understanding and implementing these measures is crucial for anyone seeking a role in this industry.
Common Safety Protocols in Food Manufacturing
A comprehensive approach to safety is essential in food manufacturing, encompassing various protocols designed to mitigate risks. These protocols are consistently applied across different stages of the production process.
- Personal Protective Equipment (PPE): Mandatory use of PPE, including hairnets, gloves, aprons, safety glasses, and sometimes specialized footwear, to prevent contamination and protect employees from hazards. For example, employees handling raw meat must wear cut-resistant gloves.
- Sanitation and Hygiene Practices: Rigorous cleaning and sanitization procedures for equipment, workstations, and the entire facility to eliminate potential foodborne pathogens. This includes regular cleaning schedules and the use of approved sanitizers.
- Hazard Analysis and Critical Control Points (HACCP): A systematic approach to identifying and controlling hazards that could cause food safety risks. HACCP plans are specific to each food manufacturing process and include critical control points (CCPs) where hazards can be prevented or eliminated.
- Lockout/Tagout Procedures: Procedures to ensure that machinery is properly shut down and de-energized before maintenance or repair to prevent accidental start-up and injury. This involves locking out power sources and attaching tags to alert workers that the equipment is out of service.
- Emergency Procedures: Established protocols for handling emergencies such as fires, chemical spills, and equipment malfunctions. This includes evacuation plans, first aid procedures, and contact information for emergency services.
- Preventive Maintenance: Regular inspection and maintenance of equipment to prevent breakdowns and ensure safe operation. This helps to identify and address potential hazards before they cause accidents.
Regulations Related to Food Safety and Handling
Numerous regulations govern food safety and handling, ensuring that food products are safe for consumption and that the manufacturing process adheres to strict standards. These regulations are enforced by various government agencies.
- Food and Drug Administration (FDA): The FDA is responsible for regulating food safety in the United States. It sets standards for food labeling, ingredients, and manufacturing processes. The FDA also conducts inspections of food manufacturing facilities to ensure compliance with regulations.
- Food Safety Modernization Act (FSMA): FSMA, enacted in 2011, significantly modernized food safety regulations in the United States. It shifted the focus from responding to contamination to preventing it. Key provisions include preventive controls for human food, preventive controls for animal food, and foreign supplier verification programs.
- Good Manufacturing Practices (GMP): GMP regulations establish minimum requirements for methods, facilities, and controls used in manufacturing, processing, and packing of food products. GMPs cover a wide range of areas, including personnel hygiene, facility design, equipment maintenance, and pest control.
- Hazard Analysis and Critical Control Points (HACCP) Regulations: Specific regulations related to HACCP are in place to ensure that food manufacturers implement and maintain HACCP plans to control food safety hazards. These plans are often tailored to the specific food product and manufacturing process.
- State and Local Health Regulations: In addition to federal regulations, state and local health departments also have their own regulations regarding food safety and handling. These regulations may address issues such as food handler permits, restaurant inspections, and the handling of specific types of food.
Demonstrating Compliance with Safety Guidelines
Demonstrating compliance with safety guidelines involves a proactive and multifaceted approach. This includes training, documentation, and continuous monitoring.
- Employee Training: Comprehensive training programs are essential to ensure that employees understand and can implement safety protocols. Training should cover topics such as proper hygiene practices, PPE usage, hazard identification, and emergency procedures. Training should be provided regularly and updated as needed.
- Standard Operating Procedures (SOPs): Detailed SOPs should be developed for all critical processes in the food manufacturing facility. SOPs provide step-by-step instructions on how to perform tasks safely and consistently. These documents should be readily available to employees and regularly reviewed and updated.
- Regular Inspections and Audits: Routine inspections and audits are crucial to identify and correct any safety violations. These can be conducted internally or by third-party auditors. Inspection reports should be documented and used to implement corrective actions.
- Documentation and Recordkeeping: Maintaining accurate records of all safety-related activities, including training, inspections, audits, and corrective actions, is critical. This documentation provides evidence of compliance with regulations and can be used to identify areas for improvement.
- Continuous Improvement: Safety is an ongoing process, and food manufacturers should continuously seek ways to improve their safety performance. This can involve implementing new technologies, refining procedures, and soliciting feedback from employees.
Importance of Adhering to Safety Procedures
Adhering to safety procedures is of utmost importance in food manufacturing, impacting both employee well-being and consumer safety. Failure to do so can have serious consequences.
- Preventing Foodborne Illness: Adherence to safety protocols is the primary defense against foodborne illnesses. Proper hygiene, sanitation, and hazard control measures minimize the risk of contamination, protecting consumers from foodborne pathogens.
- Protecting Employee Health and Safety: Safety procedures protect employees from workplace hazards, such as cuts, burns, chemical exposure, and musculoskeletal injuries. Implementing these measures creates a safe and healthy work environment.
- Maintaining Product Quality and Integrity: Safety protocols contribute to maintaining the quality and integrity of food products. By preventing contamination and spoilage, these procedures ensure that products meet consumer expectations and regulatory requirements.
- Avoiding Legal and Financial Consequences: Non-compliance with food safety regulations can result in significant legal and financial penalties, including fines, product recalls, and lawsuits. Adhering to safety procedures helps to mitigate these risks.
- Protecting Brand Reputation: Food safety incidents can severely damage a company’s brand reputation. Adhering to safety procedures helps to build and maintain consumer trust, protecting the company’s long-term success. A well-known example is the peanut butter recall of 2008-2009, which caused significant damage to the company’s reputation and resulted in substantial financial losses due to salmonella contamination.
The Future of Food Manufacturing Jobs
The food manufacturing industry is undergoing a significant transformation, driven by technological advancements and evolving consumer demands. This evolution is reshaping the roles available, the skills required, and the overall landscape of the sector. Understanding these changes is crucial for anyone considering a career in food manufacturing, as well as for those already working in the field.
Automation and Technology’s Impact
Automation and technology are rapidly changing the nature of food manufacturing jobs. These advancements are leading to increased efficiency, improved safety, and the ability to produce food at a larger scale.* Robotics and Automated Systems: Robots are increasingly used for tasks such as packaging, labeling, and palletizing. Automated systems control various processes, from mixing ingredients to monitoring temperature and pressure.
Data Analytics and Predictive Maintenance
Data analytics tools analyze data collected from sensors and machinery to predict potential equipment failures and optimize production processes. This minimizes downtime and increases efficiency.
Artificial Intelligence (AI) and Machine Learning (ML)
AI and ML are being employed for tasks such as quality control, optimizing recipes, and managing supply chains. These technologies can identify patterns and make decisions more quickly and accurately than humans in some cases.
3D Food Printing
This technology allows for the creation of customized food products, opening up new possibilities for food manufacturing. For example, restaurants can offer unique dishes tailored to individual dietary needs.
Emerging Trends in the Industry
Several key trends are shaping the future of food manufacturing. These trends are impacting the types of products being produced, the methods used, and the skills required.* Personalized Nutrition: The demand for foods tailored to individual dietary needs and preferences is increasing. This includes products for specific health conditions, allergies, and lifestyle choices.
Plant-Based Foods
The popularity of plant-based meat and dairy alternatives continues to grow, driving innovation in ingredient sourcing, processing techniques, and product development.
Sustainable Practices
Consumers are increasingly concerned about the environmental impact of food production. This is leading to a focus on sustainable sourcing, reduced waste, and eco-friendly packaging.
Transparency and Traceability
Consumers want to know where their food comes from and how it is made. This trend is driving the adoption of technologies that provide greater transparency and traceability throughout the supply chain.
E-commerce and Direct-to-Consumer Models
The growth of online food sales is changing the way food manufacturers reach consumers. This is creating new opportunities for smaller businesses and direct-to-consumer brands.
Skills in Demand in the Future
The skills required for food manufacturing jobs are evolving. While traditional skills remain important, new skills are becoming increasingly valuable.* Technical Skills: Proficiency in operating and maintaining automated equipment, understanding data analytics, and working with AI and ML systems will be in high demand.
Problem-Solving and Critical Thinking
The ability to analyze data, identify problems, and develop solutions is crucial for optimizing production processes and troubleshooting issues.
Adaptability and Continuous Learning
The food manufacturing industry is constantly changing, so the ability to adapt to new technologies and learn new skills is essential.
Food Science and Technology Expertise
A strong understanding of food science principles, processing techniques, and food safety regulations will be necessary for developing and producing safe and high-quality food products.
Supply Chain Management
Knowledge of supply chain logistics, inventory management, and procurement will be important for ensuring efficient operations and minimizing costs.
A Futuristic Food Manufacturing Facility
Imagine a state-of-the-art food manufacturing facility, a beacon of efficiency and innovation. The facility is largely automated, with robots and AI-powered systems handling many of the tasks. Massive vertical farms are integrated within the building, providing fresh, locally sourced ingredients. Sensors monitor every aspect of the production process, from ingredient quality to packaging integrity. Data analytics tools continuously optimize operations, predicting potential issues before they arise.
3D food printers create customized meals, catering to individual dietary needs. The facility is powered by renewable energy sources, minimizing its environmental footprint. The workforce is highly skilled, with specialists in robotics, data science, and food technology collaborating to create a sustainable and efficient food production system. This futuristic facility represents the direction in which the food manufacturing industry is heading, a blend of technology, sustainability, and consumer-centricity.
Final Thoughts
In conclusion, securing food manufacturing jobs near me involves understanding the industry’s nuances, preparing a strong application, and navigating the interview process effectively. By focusing on essential skills, certifications, and the specific demands of the local market, job seekers can significantly improve their chances of success. The future of this industry is bright, and those who are adaptable, safety-conscious, and embrace technological advancements will be well-positioned for long-term career growth.
With diligent preparation and a proactive approach, you can find a fulfilling career in this essential sector.