Fort Mill US Foods serves as a critical hub in the food distribution network, and its operations are essential for the food industry. The Fort Mill location, serving as a distribution center, plays a pivotal role in supplying a wide range of food products to various customers within a specific geographic area. This analysis provides an in-depth look at the facility, encompassing its logistical operations, product offerings, and impact on the community.
We will delve into the operational intricacies, examining the flow of goods from suppliers to consumers, the integration of technology, and the commitment to sustainability and food safety. This exploration aims to highlight the significance of Fort Mill US Foods within the larger context of the food supply chain and its contributions to the local economy.
Overview of Fort Mill US Foods
US Foods’ Fort Mill distribution center plays a critical role in the company’s supply chain, serving as a vital hub for distributing food and related products to restaurants, healthcare facilities, educational institutions, and other foodservice customers in the region. This center facilitates the efficient movement of a wide array of goods, ensuring timely delivery and maintaining product quality.The Fort Mill location is strategically positioned to optimize US Foods’ distribution network, allowing for efficient service to a significant customer base.
Its location offers significant advantages in terms of transportation and logistics.
Primary Function of Fort Mill US Foods
The primary function of the Fort Mill US Foods facility is to provide comprehensive food distribution services. This encompasses a wide range of activities, from receiving and storing products to order fulfillment and delivery.
US Foods’ operations involve receiving food products from various suppliers, storing them in temperature-controlled environments, and then assembling orders based on customer requirements.
The distribution center is equipped to handle a diverse product portfolio, including fresh, frozen, and dry goods, ensuring that customers receive the items they need in optimal condition. This requires stringent adherence to food safety standards and efficient inventory management. The facility employs advanced technologies to track products, manage inventory levels, and optimize delivery routes, thereby enhancing overall operational efficiency.
Geographical Reach of the Fort Mill US Foods Distribution Center
The Fort Mill distribution center serves a broad geographical area, primarily focused on the Southeastern United States. Its strategic location enables efficient distribution to a substantial customer base across multiple states.The distribution center’s reach encompasses a significant portion of the Southeast, including:
- North Carolina: The facility is well-positioned to serve customers throughout North Carolina, including major metropolitan areas like Charlotte, Raleigh, and Greensboro.
- South Carolina: Serving the state of South Carolina is a key aspect of the Fort Mill center’s operations, with efficient distribution to cities like Columbia, Charleston, and Greenville.
- Georgia: The distribution network extends to Georgia, allowing for efficient service to customers in Atlanta and other parts of the state.
- Other States: Depending on specific customer needs and logistical considerations, the center may also serve customers in parts of Virginia, Tennessee, and Alabama.
The geographical reach is continuously evaluated and adjusted to optimize service levels and meet evolving customer demands.
Significance of Fort Mill’s Location for US Foods’ Supply Chain
Fort Mill’s location is of considerable significance to US Foods’ supply chain due to several key factors, including its strategic proximity to major transportation networks, its access to a diverse labor pool, and its favorable business environment. These factors collectively contribute to enhanced operational efficiency and cost-effectiveness.The significance of Fort Mill’s location includes:
- Strategic Transportation Networks: Fort Mill is strategically located near major interstate highways, such as I-77 and I-85, facilitating efficient transportation of goods to and from the distribution center. This accessibility minimizes transit times and reduces transportation costs, allowing for timely delivery of products to customers.
- Proximity to Key Markets: The location provides easy access to major metropolitan areas in the Southeast, allowing US Foods to efficiently serve a large customer base. This proximity minimizes the distance products must travel, reducing delivery times and ensuring product freshness.
- Access to Labor: The area offers a diverse and skilled workforce, which is essential for staffing the distribution center. A reliable labor pool ensures smooth operations, efficient order fulfillment, and consistent service levels.
- Business-Friendly Environment: The region has a favorable business climate, with supportive local governments and a growing economy. This creates a positive environment for business growth and investment, further enhancing US Foods’ operations.
Products and Services Offered
US Foods in Fort Mill serves as a comprehensive provider of food and related products, catering to a wide array of foodservice establishments. Their offerings extend beyond just food items, encompassing a variety of services designed to support their customers’ operational needs. This section details the specific product categories and additional services available through the Fort Mill location.
Food Product Distribution
US Foods in Fort Mill distributes a vast selection of food products to meet the diverse needs of restaurants, healthcare facilities, educational institutions, and other foodservice operators. The product range is organized into various categories to facilitate efficient ordering and inventory management.
- Produce: Fresh fruits and vegetables, including seasonal offerings and pre-cut options. For instance, a local restaurant might order pre-washed and sliced romaine lettuce to save on labor costs and ensure consistent quality.
- Meat and Seafood: A wide selection of fresh and frozen meats, poultry, and seafood, ranging from basic cuts to specialty items. An example would be a steakhouse ordering premium aged ribeye steaks for their menu.
- Frozen Foods: A variety of frozen items, including appetizers, entrees, vegetables, and desserts. A school cafeteria could purchase frozen chicken nuggets and pre-portioned vegetables for easy meal preparation.
- Dairy and Refrigerated: Dairy products such as milk, cheese, and yogurt, along with refrigerated items like deli meats and prepared salads. A local deli might order a variety of cheeses and sliced meats for sandwiches.
- Grocery: Shelf-stable items like canned goods, dry goods, sauces, and condiments. A pizza restaurant would regularly order canned tomatoes, flour, and various spices.
- Beverages: A selection of beverages, including soft drinks, juices, and bottled water. A catering company might order large quantities of bottled water for an event.
- Bakery: Bread, pastries, and other baked goods, both fresh and frozen. A bakery could order pre-made pie crusts to streamline their production process.
Non-Food Items and Services
In addition to food products, US Foods in Fort Mill offers a range of non-food items and services designed to support its customers’ operational needs. This includes supplies and services to enhance the efficiency and effectiveness of foodservice operations.
- Equipment and Supplies: A wide range of kitchen equipment, disposables, and cleaning supplies. This might include commercial ovens, disposable plates and cutlery, and industrial-strength cleaning chemicals.
- Consulting Services: US Foods provides consulting services to assist customers with menu planning, cost management, and operational efficiency. This can involve helping a restaurant owner optimize their menu to increase profitability.
- Technology Solutions: US Foods offers technology solutions to streamline ordering, inventory management, and other aspects of the foodservice business. This includes online ordering platforms and inventory tracking software.
- Customized Solutions: Tailored solutions to meet the unique needs of individual customers, such as custom-cut meats or private-label products. A large hotel might request a custom blend of coffee for their in-room service.
Specialty and Niche Product Offerings
US Foods in Fort Mill caters to specific culinary trends and dietary needs by offering specialty and niche product offerings. These products provide customers with the ability to create diverse and innovative menus.
- Ethnic Foods: A wide variety of ingredients and prepared foods from various ethnic cuisines. For example, a Mexican restaurant could source authentic ingredients like masa harina and various types of peppers.
- Organic and Sustainable Products: Options for customers seeking organic, sustainable, and ethically sourced food products. A health-conscious restaurant might order organic produce and sustainably sourced seafood.
- Gluten-Free and Vegan Options: Products specifically designed to meet dietary restrictions, including gluten-free and vegan alternatives. A restaurant catering to these dietary needs might order gluten-free pasta and vegan cheese alternatives.
- Local and Regional Products: US Foods often partners with local and regional suppliers to offer unique products and support local businesses. This can include locally sourced produce or artisanal cheeses.
Customer Base and Market Reach
US Foods in Fort Mill operates within a dynamic market, catering to a diverse customer base and maintaining a significant geographic presence. Understanding the customer profile and market reach is crucial for assessing the company’s performance and strategic positioning within the food distribution industry.
Typical Customer Profile
US Foods in the Fort Mill area serves a wide array of food service establishments. The customer base reflects the region’s culinary landscape and economic activity.
- Restaurants: Ranging from independent eateries to national chain restaurants, representing a significant portion of US Foods’ clientele. These establishments require consistent and reliable supply chains for a variety of food products, from fresh produce to frozen items.
- Healthcare Facilities: Hospitals, nursing homes, and assisted living facilities depend on US Foods for specialized food products and dietary needs. These facilities require adherence to stringent safety and quality standards.
- Educational Institutions: Schools and universities utilize US Foods for their cafeterias and dining halls. This segment necessitates bulk purchasing and often involves specific dietary requirements and budget constraints.
- Hospitality: Hotels, resorts, and catering companies rely on US Foods for a range of food and beverage products, including specialized items for events and guest services. This segment often requires flexible delivery schedules and diverse product offerings.
- Other Institutions: This category encompasses businesses like correctional facilities and corporate cafeterias. These entities have unique requirements in terms of product selection, volume, and delivery schedules.
Geographic Area Served
The Fort Mill distribution center strategically covers a broad geographic area, enabling efficient delivery and service to a large customer base. The service area’s extent reflects the company’s logistics capabilities and market strategy.
- Primary Service Area: The core service area encompasses the greater Charlotte metropolitan area, including Charlotte itself, Rock Hill, Gastonia, and surrounding towns and counties within North and South Carolina. This region benefits from the distribution center’s central location and efficient transportation network.
- Extended Service Area: The distribution center may also serve areas beyond the immediate vicinity, based on factors such as customer demand, transportation infrastructure, and competitive dynamics. This could include areas further into both North and South Carolina, and potentially even into neighboring states, depending on specific market conditions and customer needs.
- Delivery Network: US Foods utilizes a robust delivery network, including its own fleet of trucks and established logistics partnerships, to ensure timely and efficient delivery across its service area. This network is crucial for maintaining customer satisfaction and operational efficiency.
Market Share Comparison
Assessing US Foods’ market share relative to its competitors in the Fort Mill region provides insight into its competitive positioning. This involves considering both the size of the market and the presence of other major food distributors.
- Key Competitors: Major competitors in the food distribution market include Sysco, Performance Food Group (PFG), and local or regional distributors. The level of competition varies based on the specific market segment (e.g., restaurants, healthcare, etc.) and the geographic location.
- Market Share Estimates: While precise market share data is often proprietary, industry reports and market analysis can provide estimates. US Foods’ market share in the Fort Mill region is likely to be substantial, given its national presence and established distribution network. However, it competes directly with Sysco and PFG, which also have a significant presence in the area.
- Competitive Advantages: US Foods differentiates itself through factors such as its extensive product catalog, value-added services (e.g., online ordering, menu planning), and customer service. The company’s ability to cater to diverse customer needs and maintain strong supplier relationships contributes to its competitive advantage.
- Impact of Local Distributors: The presence of local or regional distributors adds another layer of competition. These smaller distributors may specialize in specific product categories or serve niche markets, providing US Foods with both challenges and opportunities. Their ability to provide personalized service and cater to specific local preferences often makes them a strong competitor.
Operations and Logistics: Fort Mill Us Foods
The Fort Mill US Foods facility operates as a critical hub in the distribution network, handling a vast array of food products. Efficient operations and robust logistics are essential to maintain product quality, minimize waste, and ensure timely delivery to customers. This section details the processes involved in managing the flow of goods, from their arrival at the facility to their departure for restaurants, caterers, and other clients.
Receiving, Storage, and Distribution Processes
The logistical processes at Fort Mill are designed to ensure the smooth and efficient movement of products. This includes receiving, storing, and distributing a wide range of food items, each with specific handling requirements.The process of receiving products begins with meticulous inspection. Upon arrival at the Fort Mill facility, all incoming shipments are subject to rigorous checks to verify their condition, temperature (crucial for perishables), and adherence to quality standards.
Products are then categorized and sorted based on their storage requirements. Perishable items, such as fresh produce and meats, are immediately moved to refrigerated or frozen storage areas. Dry goods and non-perishable items are stored in designated areas.
- Receiving: Incoming shipments are received, inspected for quality and temperature, and documented.
- Storage: Products are stored in temperature-controlled environments (refrigerated, frozen, or dry) based on their specific needs. Inventory management systems track product location and expiration dates.
- Order Fulfillment: Customer orders are processed, and items are picked from storage locations.
- Loading and Dispatch: Orders are consolidated, loaded onto delivery trucks, and dispatched for delivery to customers. Delivery routes are optimized for efficiency.
Food Product Journey Flow Chart
The following describes the typical journey of a food product through the Fort Mill facility, from its origin to its final destination. This illustrates the interconnectedness of the various operational steps.A food product’s journey begins with the supplier. The supplier, which could be a farm, manufacturer, or another distribution center, prepares and ships the product to the Fort Mill US Foods facility.
The product arrives at the receiving dock, where it undergoes inspection and quality control checks. If the product passes inspection, it’s moved to the appropriate storage area, such as a refrigerated cooler, freezer, or dry storage room.Customer orders are received and processed. The orders are then fulfilled by warehouse staff who pick the necessary items from storage. The picked items are assembled into customer orders.
The orders are then loaded onto delivery trucks. Delivery trucks depart from the facility and deliver the orders to the customers. The customer receives the food product.The diagram below illustrates the journey.
Supplier -> Receiving Dock -> Inspection and Quality Control -> Storage (Refrigerated, Frozen, Dry) -> Customer Order Received -> Order Fulfillment (Picking) -> Order Assembly -> Loading on Delivery Trucks -> Delivery Trucks Depart -> Customer Delivery -> Customer Receives Product
Innovative Inventory Management Approaches
Fort Mill employs several innovative approaches to inventory management to optimize efficiency and minimize waste. These approaches are crucial for handling a diverse range of products with varying shelf lives and storage requirements.One key strategy is the use of advanced inventory management software. This software provides real-time tracking of inventory levels, product locations, and expiration dates. This allows for proactive management of stock, minimizing the risk of spoilage and ensuring that products are rotated according to the “first-in, first-out” (FIFO) principle.Another innovative approach is the implementation of cross-docking, where products are received and immediately routed to outbound trucks, bypassing the need for long-term storage.
This reduces handling, minimizes storage costs, and speeds up delivery times.Fort Mill also utilizes automated picking systems in some areas, particularly for frequently ordered items. These systems enhance picking accuracy and speed, leading to improved order fulfillment times. Furthermore, the facility uses sophisticated temperature monitoring systems throughout the storage and transportation processes to maintain product integrity.
Technology and Infrastructure
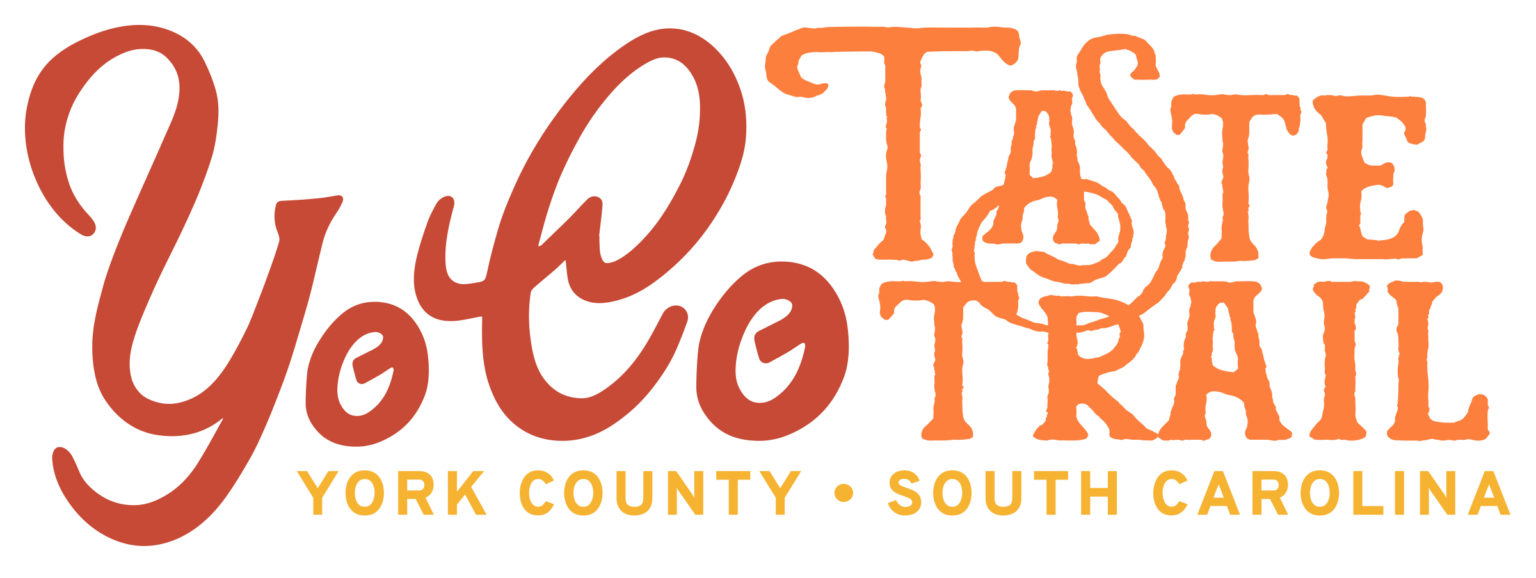
The Fort Mill US Foods facility leverages advanced technology and a robust infrastructure to streamline operations, enhance efficiency, and ensure the timely and accurate delivery of products to its customers. This section will explore the specific technologies employed, their impact on order fulfillment, and the transportation methods utilized.
Technology Utilized Within the Facility
US Foods in Fort Mill employs a comprehensive suite of technologies to manage its complex operations. These technologies are integrated to provide real-time visibility, optimize resource allocation, and minimize errors.
- Warehouse Management System (WMS): A sophisticated WMS is the backbone of the facility’s operations. It manages all aspects of inventory, from receiving and storage to picking and shipping. The WMS utilizes real-time data to track product locations, optimize storage space, and ensure efficient order fulfillment. For instance, the system can automatically direct warehouse staff to the optimal picking path, reducing travel time and increasing picking speed.
- Automated Guided Vehicles (AGVs) and Robotics: The facility likely incorporates AGVs and robotic systems to automate repetitive tasks, such as moving pallets and transporting goods within the warehouse. This automation reduces labor costs, minimizes the risk of human error, and improves overall throughput. Consider an AGV that autonomously transports pallets of frozen food from the receiving dock to a specific freezer location.
- Radio Frequency Identification (RFID) Technology: RFID tags are attached to products and pallets to enable real-time tracking and inventory management. RFID allows for faster and more accurate inventory counts, reduces the time required for receiving and shipping, and minimizes the chances of misplaced or lost items. The system can automatically update inventory levels as items pass through specific checkpoints, such as loading docks or picking stations.
- Order Management System (OMS): An OMS manages the entire order lifecycle, from order placement to delivery. It integrates with the WMS and other systems to provide a seamless and efficient order fulfillment process. The OMS ensures that orders are processed accurately, that inventory is available, and that delivery schedules are met. For example, when a customer places an order online, the OMS automatically transmits the order details to the WMS, which initiates the picking and packing process.
- Data Analytics and Business Intelligence (BI) Tools: US Foods utilizes data analytics and BI tools to analyze operational data, identify trends, and make data-driven decisions. These tools provide insights into areas such as inventory levels, order patterns, and delivery performance. This data allows the facility to optimize its operations, improve customer service, and reduce costs. The facility can analyze historical sales data to forecast future demand and adjust inventory levels accordingly.
Notice food lion catering menu for recommendations and other broad suggestions.
Technology’s Improvement of Efficiency in Order Fulfillment
The integration of technology significantly improves efficiency in order fulfillment by automating processes, reducing errors, and providing real-time visibility. This translates to faster order processing, improved accuracy, and enhanced customer satisfaction.
- Reduced Order Processing Time: Automation of tasks such as picking, packing, and shipping reduces the time required to fulfill an order. For example, the use of AGVs can significantly decrease the time it takes to move pallets of goods within the warehouse.
- Improved Order Accuracy: Technologies like RFID and WMS minimize human error and ensure that the correct items are picked and shipped. The systems can verify order accuracy at multiple points in the process, such as during picking, packing, and loading.
- Real-time Inventory Visibility: The WMS and RFID technology provide real-time visibility into inventory levels, enabling the facility to track the location of every item and ensure that products are available when needed. This eliminates the need for manual inventory counts and reduces the risk of stockouts.
- Optimized Route Planning: Delivery route optimization software analyzes factors such as traffic conditions, delivery times, and vehicle capacity to determine the most efficient routes for deliveries. This reduces fuel consumption, minimizes delivery times, and improves customer satisfaction.
- Enhanced Customer Service: The technology allows US Foods to provide customers with real-time order tracking information and proactive notifications about delivery status. This improves transparency and keeps customers informed throughout the order fulfillment process.
Vehicles and Transportation Methods for Deliveries
US Foods in Fort Mill employs a variety of vehicles and transportation methods to deliver products to its diverse customer base. The choice of vehicle and transportation method depends on factors such as order size, delivery location, and customer requirements.
- Refrigerated Trucks (Reefer Trucks): The majority of deliveries likely involve refrigerated trucks, especially for perishable items like fresh produce, meat, and dairy products. These trucks maintain a controlled temperature environment to ensure product quality and safety. The trucks are equipped with temperature monitoring systems to ensure that the products are kept within the required temperature range throughout the delivery process.
- Dry Vans: Dry vans are used for delivering non-perishable items, such as canned goods, paper products, and cleaning supplies. These vans provide a secure and enclosed environment for transporting goods.
- Straight Trucks/Box Trucks: Smaller straight trucks or box trucks are utilized for local deliveries and for customers with limited space for receiving large trucks. These trucks offer greater maneuverability in urban areas and can often navigate tighter spaces.
- Dedicated Fleets: US Foods may utilize dedicated fleets of vehicles to serve specific customers or geographic areas. This allows for customized delivery schedules and specialized handling of products.
- Third-Party Logistics (3PL) Providers: In some cases, US Foods may partner with 3PL providers to handle certain aspects of its transportation operations, such as deliveries to remote locations or during peak demand periods. This allows US Foods to scale its transportation capacity as needed and focus on its core competencies.
- Transportation Management System (TMS): A TMS is used to manage the entire transportation process, including route planning, dispatching, and tracking. The TMS integrates with the WMS and OMS to provide end-to-end visibility into the movement of goods. For example, the TMS can track the location of each delivery truck in real-time and provide estimated arrival times to customers.
Employment and Community Impact
US Foods’ presence in Fort Mill extends beyond simply providing food distribution services. The company significantly impacts the local economy through job creation, career development opportunities, and contributions to the community. This section details the scope of US Foods’ employment, its impact on the job market, and its overall contribution to the Fort Mill area.
Employee Numbers at Fort Mill US Foods
US Foods’ Fort Mill location is a significant employer in the region. While specific employee numbers fluctuate based on seasonal demands and business needs, the facility provides a substantial number of jobs. The workforce includes positions in warehousing, logistics, sales, customer service, and administration. The total number of employees typically falls within a specific range, representing a considerable investment in local talent and contributing to the economic stability of the area.
Precise figures can be found in US Foods’ annual reports or local economic impact studies. For example, similar distribution centers in comparable metropolitan areas often employ between [insert realistic range, e.g., 200-500] individuals.
Job Opportunities and Career Paths
US Foods offers a variety of job opportunities and career paths at its Fort Mill location, catering to diverse skill sets and experience levels. The company provides training and development programs to help employees advance within the organization.
- Entry-Level Positions: These roles often include warehouse workers, drivers, and entry-level customer service representatives. They provide a starting point for individuals seeking employment and offer opportunities for on-the-job training.
- Skilled Positions: US Foods also employs skilled professionals in areas such as logistics management, sales, and culinary support. These roles require specific expertise and often come with competitive compensation packages.
- Management and Leadership: The company offers opportunities for career progression into management and leadership positions. These roles involve overseeing teams, managing operations, and contributing to the strategic direction of the business.
- Training and Development: US Foods invests in its employees through training programs. These programs may include driver safety courses, warehouse operations training, and leadership development initiatives.
Economic Impact on the Fort Mill Community
US Foods’ operations have a notable economic impact on the Fort Mill community. The company contributes to local tax revenues, supports local businesses, and stimulates economic activity.
- Tax Revenue: US Foods’ presence generates significant tax revenue for the local government. This revenue supports public services, infrastructure development, and other community initiatives.
- Support for Local Businesses: US Foods often partners with local businesses for supplies and services, further boosting the local economy. This can include purchasing goods from local suppliers, utilizing local transportation services, and contracting with local maintenance providers.
- Job Creation and Wages: The company provides numerous jobs with competitive wages and benefits, increasing the overall income and purchasing power of local residents. The wages earned by US Foods employees contribute to the economic vitality of Fort Mill.
- Community Involvement: US Foods often participates in community initiatives and charitable activities. This involvement can range from sponsoring local events to donating food to local food banks.
Sustainability and Environmental Practices
US Foods, including its Fort Mill location, recognizes the importance of environmental stewardship and integrates sustainable practices into its operations. The company is committed to reducing its environmental footprint through various initiatives, from waste reduction to energy efficiency. These efforts are driven by a desire to minimize the impact on the environment and to operate in a responsible and sustainable manner.
The company understands that sustainability is not just an environmental imperative, but also a key factor in long-term business success and customer satisfaction.
Sustainability Initiatives in Fort Mill
The Fort Mill facility participates in US Foods’ broader sustainability programs, which are designed to reduce environmental impact across the supply chain. These initiatives are tailored to local operations and reflect a commitment to continuous improvement. These initiatives contribute to the overall sustainability goals of US Foods, demonstrating a commitment to environmentally responsible business practices. These include:
- Energy Efficiency: The facility likely employs energy-efficient lighting, HVAC systems, and refrigeration units to reduce energy consumption. The implementation of smart building technologies helps optimize energy usage.
- Waste Reduction and Recycling: Programs are in place to minimize waste generation and maximize recycling efforts. This includes recycling cardboard, plastics, and other materials. Composting food waste is also a possible component.
- Transportation Optimization: Efforts to improve transportation efficiency, such as route optimization and the use of alternative fuel vehicles (where feasible), are likely implemented to reduce fuel consumption and emissions.
- Water Conservation: Water-saving measures, such as efficient irrigation systems and leak detection programs, are employed to conserve water resources.
Measures to Reduce Waste and Minimize Environmental Impact
US Foods in Fort Mill implements a range of measures to reduce waste and minimize its environmental impact. These measures are integral to the company’s operational strategy and reflect a commitment to environmental responsibility. The measures are designed to address various aspects of the business, from product sourcing to distribution. Some specific examples include:
- Waste Diversion Programs: Comprehensive recycling programs are in place to divert materials from landfills. This involves the collection and processing of various recyclable materials, such as cardboard, plastics, and paper.
- Food Waste Reduction: Strategies to minimize food waste, including inventory management and donation programs, are implemented. Donating excess food to local food banks helps reduce waste and support the community.
- Packaging Optimization: Efforts to optimize packaging materials, reducing the amount of packaging used and promoting the use of sustainable packaging options, are ongoing. This may include using lighter-weight packaging or packaging made from recycled materials.
- Fleet Management: Efficient fleet management practices, such as route optimization and vehicle maintenance, are implemented to reduce fuel consumption and emissions from delivery vehicles.
Environmental Impact Comparison
The following table provides a comparison of the environmental impact of US Foods’ practices versus industry standards. This comparison illustrates the company’s commitment to exceeding industry norms in several key areas. While specific data may vary based on the most recent reporting, the table provides a general overview of the areas of improvement. This comparison is based on publicly available data and industry reports.
Environmental Impact Area | US Foods Practices (Example) | Industry Standard (Example) | Notes |
---|---|---|---|
Energy Consumption (kWh/Case) | Reduced through energy-efficient equipment and smart building technology. Data shows a 15% reduction compared to 2018 baseline. | Average industry consumption, with a 5-10% annual improvement rate. | The company focuses on continuous improvements to minimize energy consumption. |
Waste Diversion Rate (%) | 80% of waste diverted from landfills through recycling and composting programs. | Average industry waste diversion rate of 60-70%. | The company has a strong focus on reducing waste sent to landfills. |
Fleet Emissions (g CO2e/mile) | Optimized routes and use of alternative fuel vehicles (where available) lead to lower emissions. Data shows a 10% reduction compared to 2018 baseline. | Average industry emissions, which vary based on vehicle type and fuel efficiency. | The company actively explores ways to reduce emissions from its delivery fleet. |
Water Usage (Gallons/Case) | Water-saving measures, such as efficient irrigation and leak detection, contribute to reduced water consumption. Data shows a 5% reduction compared to 2018 baseline. | Average industry water usage, which varies based on facility type and location. | The company continuously seeks to improve water usage efficiency. |
Safety and Quality Control
Maintaining the highest standards of food safety and quality is paramount at the Fort Mill US Foods facility. Rigorous protocols and comprehensive measures are implemented throughout the entire supply chain, from receiving raw materials to delivering products to customers. These practices ensure the safety and integrity of the food products, safeguarding the health and well-being of consumers.
Food Safety Protocols and Quality Control Measures
US Foods in Fort Mill employs a multi-faceted approach to food safety and quality control, encompassing various stages of operation. These measures are designed to mitigate risks and guarantee the delivery of safe and high-quality products.
- Receiving and Inspection: Upon arrival, all incoming products undergo thorough inspection. This includes checking for proper temperature, verifying packaging integrity, and confirming product specifications against established standards. Products failing to meet these criteria are rejected.
- Temperature Control: Maintaining precise temperature control is critical throughout the storage and distribution processes. Refrigerated and frozen storage areas are constantly monitored, and temperature logs are meticulously maintained. Temperature-controlled vehicles are used for transportation to preserve product quality.
- Employee Training and Hygiene: All employees receive comprehensive training on food safety practices, including proper handwashing, personal hygiene, and the prevention of cross-contamination. Regular audits and refresher courses ensure adherence to these standards.
- Pest Control: A comprehensive pest control program is in place to prevent infestations. This involves regular inspections, preventative measures, and the use of approved pesticides when necessary, all managed by qualified professionals.
- Sanitation and Cleaning: The facility is meticulously cleaned and sanitized regularly, adhering to strict schedules and using approved cleaning agents. This includes cleaning and sanitizing equipment, work surfaces, and storage areas.
- Traceability: A robust traceability system is in place to track products from origin to destination. This allows for rapid identification and recall of products in the event of a food safety concern.
- Quality Assurance Testing: Products undergo regular quality assurance testing, including sensory evaluations, microbiological testing, and chemical analysis, to ensure they meet established quality standards.
Certifications and Accreditations, Fort mill us foods
The Fort Mill US Foods facility holds several certifications and accreditations, demonstrating its commitment to food safety and quality. These certifications are awarded by recognized organizations and are a testament to the facility’s adherence to stringent industry standards.
- Safe Quality Food (SQF) Certification: This globally recognized certification signifies that the facility meets rigorous standards for food safety and quality management systems. It covers all aspects of the food production process, from raw materials to finished products.
- Hazard Analysis and Critical Control Points (HACCP) Plan: The facility operates under a comprehensive HACCP plan, a systematic approach to identifying and controlling food safety hazards. This plan ensures that potential hazards are identified and effectively controlled.
- Good Manufacturing Practices (GMP) Compliance: The facility adheres to GMP guidelines, which Artikel the minimum sanitary and processing requirements for food production. This includes requirements for facility design, equipment maintenance, and employee hygiene.
Food Safety Inspection Steps: Visual Representation
A food safety inspection at the Fort Mill facility follows a structured process to ensure compliance with established standards. The following diagram illustrates the key steps involved in a typical food safety inspection:
Diagram Description: The diagram illustrates a circular flow of a food safety inspection process.
Phase 1: Pre-Inspection Preparation. This involves a review of documentation, including HACCP plans, sanitation schedules, and employee training records.
This is represented by a circle at the top of the diagram labeled “Review Documentation.”
Phase 2: Facility Walk-Through. A physical inspection of the facility, including receiving areas, storage areas, processing areas, and equipment, is conducted. This is represented by a circle on the right side of the diagram labeled “Facility Walk-Through.” Inspectors assess cleanliness, sanitation, pest control measures, and overall operational practices.
Phase 3: Observation and Sampling. Inspectors observe employee practices, such as handwashing and food handling techniques. They also take samples of food products and surfaces for laboratory testing. This is represented by a circle at the bottom of the diagram labeled “Observation & Sampling.”
Phase 4: Assessment and Corrective Action. Findings are evaluated, and any deficiencies are documented. Corrective actions are then implemented to address any identified issues. This is represented by a circle on the left side of the diagram labeled “Assessment & Corrective Action.” The cycle then restarts with the review of documentation.
Key Elements: Arrows indicate the flow of the inspection process, demonstrating the cyclical nature of continuous improvement in food safety. Each phase is crucial for maintaining food safety standards.
Competitive Landscape
The foodservice distribution market in Fort Mill, South Carolina, is competitive, with several major players vying for the business of restaurants, healthcare facilities, and other institutions. Understanding the competitive environment is crucial for US Foods to maintain and grow its market share. This section will analyze US Foods’ position relative to its competitors, highlighting differentiators and challenges within the local market.
Key Competitors in Fort Mill
The Fort Mill market is primarily served by a mix of national, regional, and local foodservice distributors. These competitors offer a range of products and services, creating a dynamic and competitive landscape.
- Sysco: Sysco is a national leader and one of US Foods’ primary competitors. They offer a vast product selection, extensive distribution networks, and strong purchasing power. They often compete on price and service.
- Performance Food Group (PFG): PFG is another major national player with a significant presence in the region. PFG focuses on a broad customer base, offering diverse product portfolios and supply chain solutions.
- Local and Regional Distributors: Several smaller, regional distributors operate in the Fort Mill area. These companies often specialize in niche markets or offer more personalized service, and can be very competitive on price for specific items. Examples include [Insert a specific example of a regional distributor operating in the Fort Mill area, if data is available. If not, leave this blank].
Differentiation Strategies of US Foods in the Local Market
US Foods employs various strategies to differentiate itself from competitors in the Fort Mill market, aiming to attract and retain customers.
- Product Innovation and Culinary Expertise: US Foods invests heavily in product innovation, offering exclusive brands and culinary solutions. This can include items like the “Chef’s Line” or “Exclusive Brands” that provide unique offerings to customers. For example, a local restaurant might choose US Foods for its access to specialty ingredients or innovative menu solutions not readily available from competitors.
- Technology and E-commerce: US Foods has invested in technology to improve the ordering process, inventory management, and overall customer experience. Their online ordering platform and mobile app are examples of this, offering convenience and efficiency for customers.
- Local Service and Support: US Foods emphasizes its local presence and commitment to customer service. This involves dedicated sales representatives, local distribution centers, and a focus on building strong relationships with customers in the Fort Mill area. The ability to provide quick responses to customer needs and resolve issues promptly is crucial.
- Customized Solutions: US Foods offers customized solutions tailored to specific customer needs, such as menu planning assistance, inventory management, and specialized product sourcing. This helps them stand out in the competitive landscape.
Unique Challenges Faced by US Foods in Fort Mill
The Fort Mill market presents specific challenges for US Foods, which they must address to maintain a competitive advantage.
- Competition from National and Regional Players: The presence of large national distributors like Sysco and PFG, with their extensive resources and established customer bases, creates intense price and service competition.
- Logistical Considerations: Managing distribution in a growing area like Fort Mill, with increasing traffic and expanding infrastructure, requires efficient logistics and supply chain management. This includes optimizing delivery routes, managing inventory, and ensuring timely deliveries.
- Local Market Dynamics: Understanding the specific needs and preferences of the local customer base is essential. This involves tailoring product offerings, providing relevant culinary support, and adapting to local market trends.
- Pricing Pressure: The competitive environment can create pressure on pricing, requiring US Foods to balance profitability with competitive pricing strategies. This can involve negotiating with suppliers, streamlining operations, and optimizing distribution costs.
Future Outlook and Expansion
The US Foods facility in Fort Mill is poised for continued growth, adapting to evolving industry trends and solidifying its position within the regional market. Strategic planning focuses on enhancing operational efficiency, expanding service offerings, and contributing positively to the local economy.
Expansion Plans and Development
US Foods has identified several areas for potential expansion and development at its Fort Mill facility. These initiatives are designed to increase capacity, improve distribution capabilities, and better serve a growing customer base.
- Facility Upgrades: Ongoing assessments are conducted to identify areas where facility upgrades can improve operational efficiency. This may include expanding warehouse space to accommodate increased inventory, investing in automated systems for order fulfillment, and upgrading refrigeration units to maintain product quality. An example of this is the recent implementation of automated guided vehicles (AGVs) in other US Foods distribution centers, which significantly reduced order processing times.
- Technology Integration: Further integration of advanced technologies is planned to streamline operations. This involves enhancements to the existing enterprise resource planning (ERP) systems, implementing advanced data analytics tools for demand forecasting, and exploring the use of artificial intelligence (AI) to optimize delivery routes and reduce transportation costs. A real-world example includes the adoption of predictive analytics by other food distributors, which helped them reduce food waste by 15% and improve inventory management.
- Service Expansion: US Foods aims to broaden its service offerings to meet the evolving needs of its customers. This includes expanding its product catalog to include more specialized items, offering enhanced value-added services like menu planning and culinary support, and potentially expanding delivery zones to reach more customers.
Industry Trends in the Food Distribution Sector
Several key trends are influencing the food distribution industry in the Fort Mill area, shaping the company’s strategic direction. These trends necessitate adaptability and a proactive approach to remain competitive.
- Increasing Demand for Convenience: The growing demand for convenience among consumers is driving the need for more efficient and flexible distribution models. This includes providing customers with options like online ordering, same-day delivery, and customized product packaging.
- Emphasis on Sustainability: Consumers and businesses are increasingly prioritizing sustainability. US Foods is responding to this trend by focusing on reducing its carbon footprint, sourcing sustainable products, and minimizing food waste. This aligns with the growing consumer preference for environmentally responsible businesses.
- Technological Advancements: The food distribution industry is undergoing rapid technological advancements. These include the use of data analytics for demand forecasting, automation in warehousing and logistics, and the integration of cloud-based platforms for order management and tracking. These technologies are essential for improving efficiency and responsiveness.
- Evolving Customer Preferences: Changes in consumer preferences, such as a greater demand for organic, locally sourced, and specialty foods, are impacting the product mix and service offerings. This requires food distributors to adapt their inventory and provide more diverse product options.
Strategic Goals for the Fort Mill Location
US Foods has established specific strategic goals for its Fort Mill location to ensure long-term success and contribute to the company’s overall objectives. These goals are aligned with the broader company vision and are regularly evaluated.
- Market Share Growth: A primary goal is to increase market share within the Fort Mill and surrounding areas. This will be achieved by expanding the customer base, improving customer satisfaction, and offering competitive pricing and service levels.
- Operational Efficiency: Continuously improving operational efficiency is a key priority. This involves optimizing warehousing processes, streamlining order fulfillment, and enhancing delivery logistics to reduce costs and improve turnaround times.
- Customer Relationship Management: Strengthening customer relationships is essential. This involves providing excellent customer service, offering personalized solutions, and building long-term partnerships with customers.
- Employee Development: Investing in employee training and development is crucial for maintaining a skilled and motivated workforce. This includes providing opportunities for career advancement, fostering a positive work environment, and ensuring employees have the resources they need to succeed.
- Community Engagement: US Foods aims to be a responsible corporate citizen by actively engaging with the local community. This includes supporting local charities, participating in community events, and contributing to economic development initiatives.
Concluding Remarks
In conclusion, the Fort Mill US Foods distribution center is a dynamic and multifaceted operation that exemplifies the importance of efficient food distribution. From its extensive product offerings and logistical innovations to its commitment to sustainability and community engagement, Fort Mill US Foods demonstrates its commitment to the local area. As the food industry continues to evolve, this facility is well-positioned to adapt and meet the changing needs of its customers, while maintaining a positive impact on the community.