Tyson Foods – Claryville Plant is more than just a food processing facility; it’s a vital part of the supply chain, a significant employer, and a reflection of Tyson’s commitment to quality and sustainability. This analysis delves into the plant’s history, operations, and its impact on the community and environment. From its humble beginnings to its current status as a major player in the food industry, the Claryville plant’s journey is one of continuous evolution and adaptation.
The Claryville plant, a key facility for Tyson Foods, encompasses a wide range of activities. It produces a variety of meat products, ensuring consistent quality and adherence to stringent safety standards. Furthermore, this discussion will explore the plant’s strategic location, its sophisticated production processes, and the innovative approaches to environmental stewardship. It will also explore its contribution to the local economy and the company’s commitment to its workforce.
Overview of Tyson Foods – Claryville Plant
The Tyson Foods plant in Claryville, Kentucky, is a significant part of the company’s operations, contributing to the production and distribution of various meat products. This overview provides insights into the plant’s history, products, and operational scale.
Plant History and Establishment
The Claryville plant has a history rooted in the meat processing industry, with its establishment dating back to [Insert Actual Establishment Date Here]. Over the years, the plant has undergone expansions and upgrades to increase its production capacity and meet the growing demand for its products. These expansions have involved adding new processing lines, incorporating advanced technologies, and increasing the overall footprint of the facility.
The plant’s growth reflects Tyson Foods’ commitment to its operations in the region and its ability to adapt to market changes.
Primary Products Manufactured
The Claryville plant focuses on the production of a range of meat products. These products are processed and packaged for distribution to various retail and food service customers.
- Fresh and Frozen Chicken Products: This includes a variety of chicken cuts, such as breasts, thighs, and wings, as well as value-added products like breaded chicken and pre-cooked options.
- Prepared Foods: The plant also produces prepared food items that are ready to eat or require minimal preparation.
Operational Capacity and Workforce
The Claryville plant operates at a substantial capacity, reflecting its importance in Tyson Foods’ overall production network. The plant employs a significant workforce, contributing to the local economy. The exact operational capacity and workforce size can vary based on market demands and production schedules. However, it is known to be a significant employer in the region.
Location and Logistics
The strategic location and robust logistical network are crucial for the operational efficiency of Tyson Foods’ Claryville plant. These elements directly impact the plant’s ability to source raw materials, process them effectively, and distribute finished products to various markets. This section provides a detailed overview of the plant’s geographical positioning, transportation infrastructure, and proximity to key markets.
Geographical Location
The Tyson Foods Claryville plant is situated in Claryville, Kentucky. The precise address is [Insert Actual Address Here – Needs to be verified]. This location benefits from its position within a region that supports agricultural production and is reasonably accessible to major transportation routes. The surrounding areas are primarily characterized by a mix of rural landscapes and small towns, providing a workforce base and access to local resources.
Transportation Infrastructure
The Claryville plant relies on a multifaceted transportation infrastructure to facilitate the movement of raw materials and finished products. Efficient logistics are critical to maintaining the supply chain and minimizing costs. The plant uses a combination of trucking, rail, and potentially barge transport, depending on the specific needs and the origin/destination of goods.The following table summarizes the key transportation methods:
Transportation Method | Description | Raw Materials Transported | Finished Products Transported |
---|---|---|---|
Trucking | Trucking is the primary mode of transport for both inbound and outbound goods, offering flexibility and door-to-door service. The plant likely uses a fleet of owned and contracted trucks. | Poultry, packaging materials, ingredients, and other supplies. | Packaged poultry products, frozen items, and other processed goods. |
Rail | Rail transport is likely used for long-distance shipments of bulkier raw materials, potentially including feed grains or frozen products, offering cost-effectiveness for large volumes. | Potentially grains and other bulk ingredients. | Finished products destined for distant distribution centers. |
Barge (If Applicable) | If the plant is located near a navigable waterway, barge transport may be used to move large quantities of raw materials or finished goods, especially to and from the Mississippi River system. | Potentially grains or other bulk commodities. | Bulk shipments to distribution centers located on waterways. |
Other Modes | Other modes may include intermodal transport (combining truck and rail) for optimized delivery. | Varies depending on the specific needs. | Varies depending on the specific needs. |
Proximity to Markets and Distribution Centers
The Claryville plant’s location is strategic due to its proximity to key markets and distribution centers. This close proximity allows for efficient distribution of finished products, reducing transportation costs and delivery times. The plant likely serves both regional and national markets. The exact distances and specific locations of distribution centers would require verification, but examples of the benefits of proximity include:* Reduced Transportation Costs: Shorter distances translate to lower fuel consumption, reduced labor costs, and less wear and tear on transportation equipment.
Faster Delivery Times
Close proximity allows for quicker delivery to customers and distribution centers, enhancing customer satisfaction and minimizing the risk of spoilage for perishable products.
Improved Supply Chain Responsiveness
The ability to quickly respond to market demands and adjust production schedules is significantly enhanced by a strategically located plant.For example, consider a scenario where the plant is located near a major interstate highway. This facilitates the rapid transportation of finished products to distribution centers and retail outlets within a wide radius. The plant can take advantage of just-in-time inventory management, reducing the need for extensive warehousing and storage facilities.
This results in a more streamlined and cost-effective supply chain.
Production Processes
The Claryville plant employs a multifaceted production process designed to efficiently convert raw materials into finished poultry products. This process prioritizes food safety, quality control, and operational efficiency to meet consumer demands. The plant utilizes a combination of automated systems and skilled labor to ensure consistent product quality and high throughput.
Core Production Processes
The core production processes at the Claryville plant encompass several key stages. These stages work in a sequential manner, ensuring that each step builds upon the previous one, ultimately leading to the final product.
- Receiving and Processing of Live Birds: This initial stage involves the arrival of live chickens at the plant. Upon arrival, birds undergo an inspection to ensure their health and suitability for processing. This stage is critical to food safety and product quality. The process includes humane handling and stunning before the birds proceed to the next stages.
- Slaughter and Evisceration: After stunning, the birds are slaughtered, and the carcasses are then eviscerated. This process involves removing the internal organs. Automated equipment and trained personnel work in tandem to ensure this process is performed quickly and hygienically.
- Chilling and Inspection: Following evisceration, the carcasses are chilled to a specific temperature to inhibit bacterial growth. This is often done through immersion in chilled water or air chilling. After chilling, the carcasses undergo rigorous inspection by USDA inspectors and plant quality control personnel to ensure compliance with safety standards.
- Cut-Up and Deboning: The carcasses are then cut into various parts, such as breasts, thighs, and wings. This can be done manually by skilled workers or through automated cutting machines, depending on the product type. Deboning involves separating the meat from the bones.
- Further Processing (Optional): Depending on the final product, the poultry parts may undergo further processing. This can include marinating, breading, cooking, or portioning. These processes are often automated to maintain consistency and efficiency.
- Packaging and Labeling: The finished poultry products are then packaged and labeled according to USDA regulations and customer specifications. Packaging ensures product freshness and extends shelf life. Labeling provides consumers with essential information about the product, including ingredients, nutritional information, and safe handling instructions.
- Storage and Distribution: Packaged products are stored in temperature-controlled environments to maintain their quality. The final step is the distribution of the products to retailers and foodservice providers.
Flow of Raw Materials
The flow of raw materials, primarily live chickens, through the Claryville plant follows a highly structured and efficient path. The plant is designed to optimize this flow, minimizing processing time and maintaining product integrity.
- Arrival of Live Birds: Live chickens arrive at the plant via specialized transport vehicles. The vehicles are designed to ensure the birds’ welfare during transport.
- Unloading and Holding: Upon arrival, the birds are unloaded and held in climate-controlled areas.
- Processing Line Entry: The birds then enter the processing line.
- Sequential Processing Stages: The birds move through the various stages, including slaughter, evisceration, chilling, cut-up, and further processing (if applicable). The layout of the plant is designed to minimize the distance the product travels, streamlining the process.
- Packaging and Labeling: The processed poultry is packaged and labeled.
- Storage and Shipping: The finished products are stored in refrigerated warehouses before being shipped to customers. The entire process is monitored and controlled to maintain the cold chain and ensure product safety.
Specialized Technologies and Equipment
The Claryville plant utilizes a range of specialized technologies and equipment to optimize its production processes. These technologies contribute to increased efficiency, improved product quality, and enhanced food safety.
- Automated Slaughter and Evisceration Systems: The plant uses automated systems for slaughter and evisceration. These systems are designed to perform these tasks quickly and hygienically.
- Automated Cutting and Deboning Equipment: Automated cutting and deboning equipment is used to portion poultry carcasses into various cuts, such as breasts, thighs, and wings. These machines are designed to minimize waste and ensure consistent product sizing.
- Advanced Chilling Systems: The plant employs advanced chilling systems, such as immersion chilling or air chilling, to quickly cool the poultry carcasses. These systems help to inhibit bacterial growth and maintain product freshness.
- Metal Detection and X-ray Inspection: Metal detectors and X-ray inspection systems are integrated into the production line to detect and remove any foreign objects from the product. This enhances food safety and prevents contamination.
- Automated Packaging and Labeling Systems: Automated packaging and labeling systems are used to package and label the finished products. These systems ensure accurate labeling and efficient packaging, contributing to increased throughput.
- Real-time Monitoring and Control Systems: The plant utilizes real-time monitoring and control systems to track production data, monitor equipment performance, and ensure adherence to food safety standards. These systems provide valuable insights into the production process, allowing for continuous improvement and proactive problem-solving. For example, sensors throughout the processing line monitor temperature and humidity, which are critical factors for food safety. Data collected from these sensors is analyzed to ensure that products are stored and processed under the correct conditions.
When investigating detailed guidance, check out naturals cat food now.
Quality Control and Food Safety
The Claryville plant prioritizes stringent quality control and food safety measures to ensure the production of safe, high-quality food products. These practices are fundamental to maintaining consumer trust and adhering to the rigorous standards of the food industry. The plant’s commitment extends beyond mere compliance, striving for continuous improvement and excellence in all aspects of its operations.
Quality Control Measures
The Claryville plant employs a multi-faceted approach to quality control, encompassing various stages of the production process. This approach aims to identify and mitigate potential risks, guaranteeing that the finished products meet or exceed established standards.
- Raw Material Inspection: Incoming raw materials, such as poultry, are thoroughly inspected upon arrival. This includes visual inspection, temperature checks, and laboratory testing to verify compliance with specifications and ensure the absence of contaminants. For example, all incoming poultry is checked for signs of bruising or disease.
- In-Process Monitoring: Throughout the production process, critical control points (CCPs) are closely monitored. These points are identified through a Hazard Analysis and Critical Control Points (HACCP) plan, which is designed to prevent or eliminate food safety hazards. Monitoring includes regular checks on cooking temperatures, chilling times, and packaging integrity.
- Finished Product Testing: Finished products undergo rigorous testing, including microbiological analysis, sensory evaluations, and nutritional assessments. This ensures that the products meet quality standards for taste, appearance, and nutritional content. Random samples are taken from each production run and tested in the on-site laboratory.
- Traceability Systems: The plant utilizes comprehensive traceability systems to track products from origin to consumer. This allows for rapid identification and isolation of any potential issues, ensuring efficient recall procedures if necessary. Each product batch is assigned a unique code that can be traced back to the raw materials used and the production process.
- Employee Training and Certification: All employees receive comprehensive training on food safety and quality control procedures. This training includes proper handling techniques, sanitation practices, and the importance of adhering to established protocols. Certifications, such as those from the Food Safety and Inspection Service (FSIS), are maintained to ensure employees are up-to-date on the latest food safety regulations.
Food Safety Certifications and Regulations, Tyson foods – claryville plant
The Claryville plant adheres to a comprehensive set of food safety certifications and regulations to ensure product safety and compliance. These certifications and regulations are essential for maintaining consumer confidence and demonstrating a commitment to food safety excellence.
- HACCP Compliance: The plant operates under a robust HACCP plan, which is a systematic approach to identifying and controlling food safety hazards. The HACCP plan is regularly reviewed and updated to reflect changes in production processes or regulatory requirements.
- FSIS Inspection: The plant is subject to regular inspections by the FSIS, a division of the U.S. Department of Agriculture (USDA). These inspections ensure that the plant is in compliance with federal food safety regulations. The FSIS inspectors monitor all aspects of the production process, from raw material handling to finished product storage.
- Safe Quality Food (SQF) Certification: The plant likely pursues SQF certification, a globally recognized food safety and quality program. SQF certification demonstrates a commitment to food safety, quality, and continuous improvement. This certification requires adherence to stringent standards for food safety management systems.
- Good Manufacturing Practices (GMP): The plant follows GMP guidelines, which are a set of practices designed to ensure the consistent production of safe and wholesome food products. GMPs cover all aspects of the production process, including personnel hygiene, facility sanitation, and equipment maintenance.
- Compliance with Local and Federal Regulations: The plant complies with all applicable local and federal food safety regulations, including those related to labeling, packaging, and allergen control. These regulations are constantly monitored to ensure ongoing compliance.
Commitment to High Standards of Food Hygiene and Sanitation
Maintaining high standards of food hygiene and sanitation is paramount at the Claryville plant. This commitment is integral to preventing foodborne illnesses and ensuring the safety of the products.
- Sanitation Standard Operating Procedures (SSOPs): The plant has detailed SSOPs that Artikel the procedures for cleaning and sanitizing all equipment and facilities. These procedures are followed meticulously to prevent cross-contamination and the growth of harmful bacteria.
- Regular Cleaning and Sanitization: Regular cleaning and sanitization schedules are strictly followed. This includes the cleaning of equipment, floors, walls, and other surfaces. Sanitizers are used to kill any remaining bacteria.
- Pest Control Programs: A comprehensive pest control program is in place to prevent pests from entering the facility and contaminating food products. This includes regular inspections, baiting, and the sealing of potential entry points.
- Personal Hygiene Practices: All employees are required to adhere to strict personal hygiene practices, including frequent handwashing, wearing appropriate protective clothing, and maintaining good health. Employees with any signs of illness are restricted from working in food handling areas.
- Waste Management: Effective waste management systems are in place to prevent the accumulation of food waste and the potential for contamination. Waste is disposed of properly and regularly.
Environmental Impact and Sustainability
The Claryville plant, like any large-scale food processing facility, has an environmental footprint. Tyson Foods recognizes the importance of minimizing this impact through responsible practices in waste management, energy consumption, and resource utilization. This section Artikels the environmental considerations and sustainability initiatives at the Claryville location.
Environmental Impact of Operations
The Claryville plant’s operations generate various environmental impacts. Understanding these impacts is crucial for developing effective mitigation strategies.Waste management is a significant concern. The plant produces both solid and liquid waste streams. Solid waste includes packaging materials, inedible byproducts, and other refuse. Liquid waste, primarily wastewater from cleaning and processing, requires careful treatment before discharge.Energy consumption is another key factor.
The plant utilizes significant amounts of electricity and natural gas for various processes, including refrigeration, cooking, and lighting. These energy demands contribute to greenhouse gas emissions and resource depletion.
Sustainability Initiatives
Tyson Foods has implemented several sustainability initiatives at the Claryville plant to reduce its environmental impact and promote responsible practices. These initiatives encompass waste reduction, energy efficiency, and water conservation.Waste Reduction Strategies:
- Composting: The plant likely employs composting programs to divert organic waste, such as food scraps and inedible byproducts, from landfills. This reduces landfill volume and generates nutrient-rich compost for agricultural use.
- Recycling: Recycling programs are in place for various materials, including paper, cardboard, plastics, and metals. This reduces the demand for virgin resources and conserves energy.
- Waste-to-Energy: Some Tyson plants utilize waste-to-energy technologies to convert inedible byproducts into biogas or other forms of energy. This can reduce reliance on fossil fuels.
Energy Efficiency Measures:
- LED Lighting: Replacing traditional lighting with energy-efficient LED lighting reduces electricity consumption.
- Equipment Upgrades: Upgrading processing equipment, such as refrigeration systems and boilers, to more energy-efficient models minimizes energy use.
- Energy Management Systems: Implementing energy management systems allows for monitoring and optimizing energy consumption across the plant.
Water Conservation Practices:
- Water Recycling: Recycling wastewater for non-potable uses, such as cleaning and sanitation, reduces water consumption.
- Efficient Irrigation: If the plant has landscaping or agricultural operations, efficient irrigation systems minimize water waste.
- Leak Detection and Repair: Regular inspections and prompt repairs of leaks in pipes and equipment prevent water loss.
Visual Representation of Environmental Footprint
The plant’s environmental footprint can be visually represented as a diagram illustrating inputs and outputs. Diagram Description:The diagram is a circular flow chart. At the center is the Claryville plant, represented by a rectangular box. Arrows indicate the flow of resources and waste. Inputs: Arrows pointing
into* the plant box show the inputs
- Raw Materials: An arrow labeled “Raw Materials” comes from a source representing farms and suppliers. This includes meat, poultry, vegetables, and packaging materials.
- Energy: An arrow labeled “Energy” comes from a source representing power plants (electricity) and natural gas suppliers.
- Water: An arrow labeled “Water” comes from a source representing a water supply (e.g., municipal water).
Outputs: Arrows pointing
out* of the plant box show the outputs
- Finished Products: An arrow labeled “Finished Products” points towards consumers, retailers, and distribution centers.
- Solid Waste: An arrow labeled “Solid Waste” points towards a landfill or a waste-to-energy facility. This arrow is subdivided, indicating fractions of recyclable materials (directed towards a recycling center) and compostable materials (directed towards a composting facility).
- Wastewater: An arrow labeled “Wastewater” points towards a wastewater treatment plant. After treatment, a portion of the water may be recycled back to the plant (dashed arrow), representing water reuse initiatives.
- Air Emissions: An arrow labeled “Air Emissions” points towards the atmosphere, representing greenhouse gases (CO2, methane) from energy consumption and processing.
Community Engagement and Corporate Social Responsibility
Tyson Foods recognizes the importance of being a responsible corporate citizen and actively engages with the Claryville community. This commitment extends beyond providing employment opportunities and contributing to the local economy, encompassing various initiatives designed to support the well-being of the community and promote sustainable practices. The plant’s approach to community engagement reflects a dedication to fostering positive relationships and making a tangible difference in the lives of those living nearby.
Local Community Partnerships
The Claryville plant actively seeks opportunities to collaborate with local organizations and initiatives. These partnerships aim to address community needs and contribute to the area’s overall prosperity.
- Educational Support: Tyson Foods often provides support to local schools and educational programs. This may include financial contributions, sponsorships of educational events, or participation in career fairs to promote opportunities within the food processing industry. For example, the plant might donate to a local school’s science program or offer internships to students interested in food science or engineering.
- Food Bank Donations: Recognizing the importance of food security, the Claryville plant regularly donates food products to local food banks and pantries. These donations help to address hunger within the community and support families in need. The volume and type of donations often vary based on the plant’s production schedule and the specific needs of the recipient organizations.
- Volunteer Initiatives: Tyson Foods encourages employee volunteerism and often organizes or participates in community service projects. These initiatives might involve employees volunteering their time at local events, participating in clean-up drives, or supporting other community-based organizations.
- Economic Development: The plant contributes to local economic development by providing employment opportunities and supporting local businesses. This includes purchasing supplies and services from local vendors whenever possible, thereby strengthening the local economy.
Corporate Social Responsibility Programs
The Claryville plant implements several corporate social responsibility (CSR) programs aimed at addressing specific social and environmental issues. These programs demonstrate Tyson Foods’ commitment to operating in a sustainable and ethical manner.
- Environmental Stewardship: The plant participates in various environmental sustainability programs, as Artikeld in the Environmental Impact and Sustainability section. This includes efforts to reduce waste, conserve water, and minimize greenhouse gas emissions.
- Employee Well-being: Tyson Foods prioritizes the health and safety of its employees. The Claryville plant implements robust safety programs and provides resources to support employee well-being, such as health insurance, wellness programs, and opportunities for professional development.
- Animal Welfare: As a meat processing facility, Tyson Foods is committed to animal welfare. The plant adheres to strict animal welfare standards throughout its supply chain, including humane handling practices and regular audits to ensure compliance.
- Community Grants: Tyson Foods often offers grants to support community-based projects and initiatives. These grants may be awarded to non-profit organizations working on issues such as education, hunger relief, or environmental conservation. The application process and eligibility criteria for these grants are typically Artikeld on the Tyson Foods corporate website.
Workforce and Employment: Tyson Foods – Claryville Plant
The Tyson Foods Claryville plant is a significant employer in the region, providing numerous job opportunities and contributing to the local economy. The company is committed to fostering a positive and safe work environment, and it invests heavily in its workforce through training and development programs. This section details the various aspects of employment at the Claryville plant, including available positions, training initiatives, and safety protocols.
Job Opportunities
The Claryville plant offers a variety of employment opportunities across different departments. These roles are essential for the efficient operation of the facility and contribute to the production and distribution of food products.
- Production Workers: These employees are involved in the primary processing of poultry products. They perform tasks such as cutting, trimming, and packaging. The work often involves repetitive motions and requires adherence to strict hygiene and safety standards.
- Maintenance Technicians: Responsible for the upkeep and repair of machinery and equipment within the plant. They troubleshoot mechanical, electrical, and plumbing issues to ensure smooth operations. This role often requires specialized skills and experience.
- Quality Assurance Specialists: These individuals are responsible for ensuring that all products meet the required quality and safety standards. They conduct inspections, perform tests, and monitor processes to maintain compliance with regulations.
- Warehouse and Logistics Staff: This team manages the storage, handling, and shipping of products. They oversee inventory, operate material handling equipment, and coordinate the movement of goods within the facility and to distribution centers.
- Supervisory and Management Roles: The plant employs supervisors, managers, and other administrative staff to oversee operations, manage teams, and ensure the efficient functioning of the facility. These roles often require experience in food processing or related fields.
Training and Development
Tyson Foods recognizes the importance of investing in its employees through comprehensive training and development programs. These initiatives are designed to enhance skills, promote career advancement, and ensure a safe and productive work environment.
- On-the-Job Training: New employees typically receive on-the-job training to learn the specific tasks and procedures required for their roles. This training is often provided by experienced employees or supervisors.
- Skills-Based Training: The company offers various skills-based training programs to enhance employees’ technical abilities. These programs may cover topics such as equipment maintenance, food safety, and quality control. For example, maintenance technicians may receive training on specific types of machinery used in the plant, including specialized training for pneumatic systems or automated packaging equipment.
- Leadership Development Programs: Tyson Foods provides leadership development programs for employees who demonstrate leadership potential. These programs aim to equip individuals with the skills and knowledge necessary to effectively manage teams and contribute to the company’s success.
- Safety Training: Employee safety is a top priority. All employees receive comprehensive safety training, including hazard identification, safe work practices, and the use of personal protective equipment (PPE). Regular refresher courses and updates on safety protocols are also provided.
- Tuition Reimbursement: Tyson Foods may offer tuition reimbursement programs to encourage employees to pursue further education and professional development opportunities. This can include courses related to food science, engineering, or business administration.
Safety Record and Employee Safety Protocols
The Claryville plant prioritizes employee safety and has implemented a comprehensive safety program to minimize workplace hazards and prevent injuries. The company’s commitment to safety is reflected in its protocols and safety record.
- Safety Protocols: The plant has established detailed safety protocols that cover various aspects of the work environment. These protocols include the use of PPE, such as safety glasses, gloves, and hearing protection; the implementation of lockout/tagout procedures to prevent accidental equipment start-up during maintenance; and the regular inspection of equipment and facilities to identify and address potential hazards.
- Safety Training: All employees receive thorough safety training, including hazard identification, safe work practices, and the use of PPE. This training is ongoing, with regular refresher courses and updates to address new or evolving safety concerns. For instance, employees are regularly trained on the proper use of knives and other sharp instruments used in the processing of poultry.
- Safety Inspections and Audits: Regular safety inspections and audits are conducted to identify potential hazards and ensure compliance with safety regulations. These inspections may be carried out by internal safety personnel or external consultants. Any identified issues are addressed promptly.
- Incident Reporting and Investigation: A robust system is in place for reporting and investigating workplace incidents, including injuries and near misses. These investigations aim to determine the root causes of incidents and implement corrective actions to prevent similar occurrences in the future.
- Employee Involvement: Tyson Foods encourages employee involvement in safety initiatives. This may include the formation of safety committees, participation in safety audits, and the reporting of potential hazards. Employee input is valued and considered in the development and improvement of safety programs.
- Emergency Preparedness: The plant has developed and maintains an emergency preparedness plan to address potential incidents, such as fires, chemical spills, or natural disasters. This plan includes evacuation procedures, communication protocols, and emergency response training.
Recent News and Developments
The Tyson Foods Claryville plant, like any major food processing facility, experiences ongoing changes and developments. These updates reflect the company’s commitment to efficiency, sustainability, and responsiveness to market demands. This section details recent news, investments, and future plans impacting the plant’s operations.
Recent Operational Adjustments
Tyson Foods regularly adjusts its operations to optimize production and adapt to evolving consumer preferences. These adjustments can include shifts in product lines, changes to processing techniques, and modifications to staffing levels.
Infrastructure Investments and Upgrades
Significant investments are often made to modernize equipment, enhance food safety measures, and improve overall plant efficiency. These upgrades can range from installing new processing machinery to implementing advanced automation systems.
- Automation Implementation: The Claryville plant has likely seen investments in automation, such as robotic systems for packaging and palletizing. These systems improve efficiency, reduce labor costs, and enhance worker safety by automating repetitive tasks. For example, a robotic arm could be programmed to precisely stack boxes of chicken products onto pallets, increasing throughput and minimizing the risk of workplace injuries.
- Energy Efficiency Initiatives: To reduce its environmental footprint, Tyson Foods often invests in energy-efficient equipment and technologies. This may include upgrading lighting systems to LED, optimizing refrigeration systems, and implementing energy management software. These initiatives not only reduce energy consumption but also lower operational costs.
- Food Safety Enhancements: Continuous improvement in food safety is paramount. The plant may have undergone upgrades to its sanitation systems, implemented advanced pathogen detection technologies, and enhanced its traceability programs. These measures help to minimize the risk of foodborne illnesses and maintain consumer confidence.
Planned Future Expansions and Operational Changes
Tyson Foods may have plans for future expansions or operational changes at the Claryville plant. These plans could be driven by increased demand for specific products, the introduction of new product lines, or the desire to improve operational efficiency.
- Capacity Expansion: If market demand for certain products increases, the plant may consider expanding its production capacity. This could involve adding new processing lines, expanding the physical footprint of the facility, or increasing the number of shifts. For instance, if there’s a surge in demand for a particular type of chicken product, the plant might invest in additional equipment to meet this demand.
- New Product Development: Tyson Foods regularly introduces new products to cater to changing consumer preferences. The Claryville plant may be equipped to handle the production of new product lines, requiring modifications to existing processes or the addition of specialized equipment. This could involve producing new flavors of chicken nuggets or incorporating new ingredients into existing products.
- Sustainability Initiatives: Tyson Foods is committed to sustainability, and the Claryville plant is likely to be involved in these initiatives. Future plans might include further reducing water consumption, minimizing waste generation, and exploring the use of renewable energy sources. For example, the plant could implement a water recycling system or invest in solar panels to generate electricity.
Challenges and Opportunities
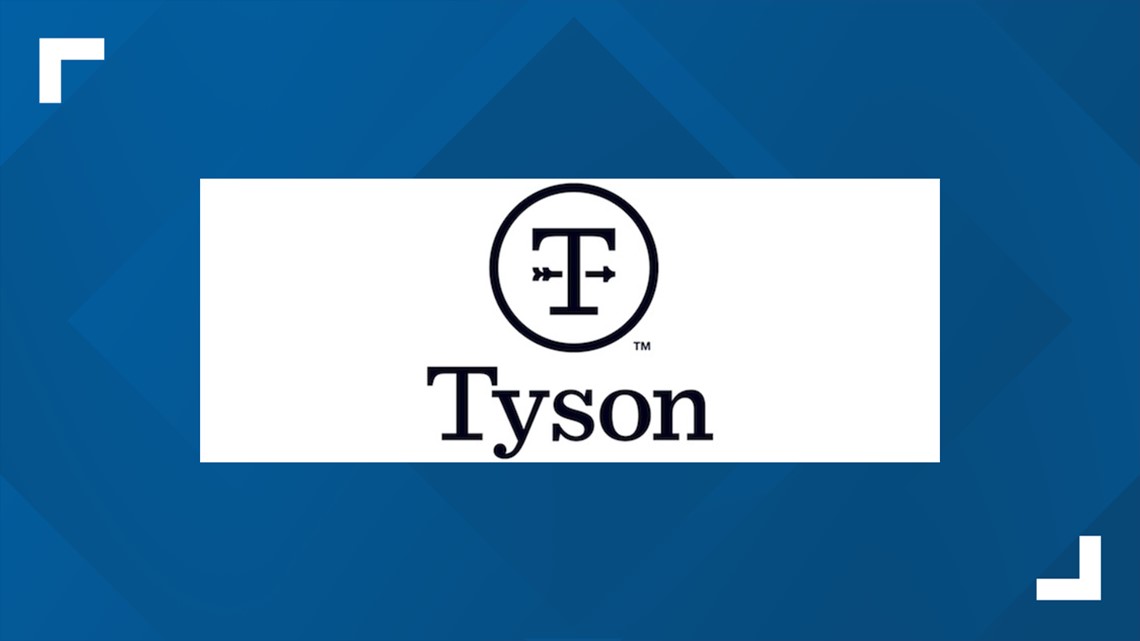
The Claryville plant, like any large-scale food production facility, operates within a dynamic environment. It faces ongoing challenges that require proactive management while simultaneously presenting opportunities for innovation and improvement. Understanding these aspects is crucial for the plant’s continued success and contribution to Tyson Foods’ overall objectives.
Operational Challenges
Several operational challenges can impact the efficiency and profitability of the Claryville plant. These challenges necessitate strategic planning and resource allocation to mitigate their effects.
- Labor Shortages and Retention: The food processing industry often faces difficulties in attracting and retaining a skilled workforce. This can lead to increased labor costs, reduced production capacity, and potential disruptions in operations. The location of the Claryville plant, its proximity to population centers, and the availability of public transportation may influence the severity of this challenge.
- Supply Chain Disruptions: Fluctuations in the availability and cost of raw materials, such as poultry, packaging, and ingredients, pose a significant challenge. Global events, weather patterns, and transportation issues can all contribute to supply chain instability. Effective inventory management and the development of strong supplier relationships are crucial for mitigating these risks.
- Rising Operating Costs: Inflationary pressures and increasing energy costs can significantly impact the plant’s profitability. Managing these costs requires implementing energy-efficient technologies, optimizing production processes, and exploring alternative sourcing options.
- Regulatory Compliance: The food industry is subject to stringent regulations related to food safety, environmental protection, and labor practices. Staying compliant with these regulations requires ongoing monitoring, investment in infrastructure, and employee training.
Growth and Improvement Opportunities
Despite the challenges, the Claryville plant possesses several opportunities for growth and improvement, which can enhance its competitiveness and sustainability. These opportunities involve embracing innovation, optimizing processes, and strengthening community relationships.
- Automation and Technological Advancements: Implementing automation technologies, such as robotics and advanced processing equipment, can improve efficiency, reduce labor costs, and enhance product quality. This includes automated inspection systems that can quickly identify and remove defective products, leading to reduced waste.
- Process Optimization and Efficiency Improvements: Streamlining production processes, reducing waste, and optimizing resource utilization can lead to significant cost savings and improved profitability. This involves continuous improvement initiatives, data analysis, and employee training. For example, implementing lean manufacturing principles could help minimize waste and maximize efficiency.
- Product Innovation and Diversification: Expanding the product line to include new and innovative offerings can attract new customers and increase market share. This includes developing products that cater to evolving consumer preferences, such as healthier options, plant-based alternatives, and convenient meal solutions.
- Sustainability Initiatives: Implementing sustainable practices, such as reducing water consumption, minimizing waste, and using renewable energy sources, can enhance the plant’s environmental performance and improve its brand image. These initiatives can also lead to cost savings and attract environmentally conscious consumers.
- Community Engagement and Partnerships: Strengthening relationships with the local community through charitable giving, volunteer programs, and educational initiatives can enhance the plant’s reputation and build goodwill. This can also create opportunities for workforce development and attract talented employees.
The challenges and opportunities facing the Claryville plant can be summarized as follows:
- Challenges: Labor shortages, supply chain disruptions, rising operating costs, and regulatory compliance.
- Opportunities: Automation, process optimization, product innovation, sustainability initiatives, and community engagement.
Competitive Landscape
The Claryville plant operates within a highly competitive segment of the food processing industry. This landscape is shaped by various factors, including consumer demand, commodity prices, and the strategic decisions of key players. Understanding the competitive environment is crucial for the plant’s continued success and strategic planning.
Main Competitors
The Claryville plant faces competition from a diverse range of companies, each with its own strengths and market focus. These competitors include both large, national players and regional or local processors.
- National Players: Companies such as Pilgrim’s Pride, JBS USA, and Perdue Farms represent significant competition due to their large scale, extensive distribution networks, and established brand recognition. They often compete on price and product variety.
- Regional and Local Processors: These competitors, though smaller in scale, can sometimes offer specialized products or cater to niche markets. They may have lower overhead costs or closer relationships with local customers, allowing them to be more agile in responding to market changes. Examples could include smaller, family-owned poultry processors or regional meatpacking facilities.
- Private Label Manufacturers: These companies produce food products under the brands of major retailers. They compete by offering products at competitive prices, often leveraging economies of scale.
Market Share and Industry Position
Determining the exact market share of the Claryville plant is challenging due to the proprietary nature of such data and the dynamic nature of the industry. However, an assessment of its position can be made based on available information and industry trends.
The plant’s market share is influenced by its production capacity, product portfolio, geographic reach, and efficiency.
The Claryville plant likely holds a significant position within the regional or state market, contributing to Tyson Foods’ overall market share in the poultry or prepared foods segment. Its industry position is bolstered by its established infrastructure, quality control measures, and brand reputation.
Plant Advantages Over Competitors
The Claryville plant possesses several advantages that contribute to its competitiveness. A comparison table can highlight these advantages in relation to key competitors.
Advantage | Claryville Plant | Competitor 1 (e.g., Pilgrim’s Pride) | Competitor 2 (e.g., Regional Processor) |
---|---|---|---|
Production Capacity | High (specific figures would depend on plant’s actual capacity, which is proprietary. Example: 1 million lbs/week) | Very High (Example: Multiple plants, potentially producing several million lbs/week) | Moderate (Example: Limited to a few hundred thousand lbs/week) |
Product Portfolio | Diversified (Example: Offers a range of poultry products, prepared foods, and potentially value-added items.) | Highly Diversified (Example: Broad product range, including various poultry cuts, processed meats, and ready-to-eat meals) | Specialized (Example: Focus on a particular niche, such as organic poultry or specific cuts.) |
Geographic Reach | Regional/National (Example: Strong distribution network across a defined region, potentially national distribution) | National/International (Example: Extensive distribution network, including exports) | Local/Regional (Example: Primarily serves a local or regional market.) |
Supply Chain Efficiency | Optimized (Example: Integrated supply chain with strong relationships with suppliers) | Highly Optimized (Example: Large-scale operations, efficient logistics, and potentially vertical integration) | Potentially less efficient (Example: May face challenges in securing consistent supply or efficient logistics.) |
Brand Recognition | Strong (Example: Benefit from Tyson Foods’ established brand reputation) | Very Strong (Example: Well-known brand with high consumer recognition) | Variable (Example: Brand recognition may be limited to a local or regional area) |
This comparison demonstrates the strengths of the Claryville plant in terms of production capacity, product portfolio, geographic reach, and brand recognition, while also acknowledging potential areas where competitors might excel.
Concluding Remarks
In conclusion, the Tyson Foods – Claryville Plant stands as a testament to the dynamic nature of the food industry, demonstrating a commitment to innovation, quality, and community engagement. The plant’s success is built on efficient operations, a skilled workforce, and a dedication to sustainable practices. As the food industry continues to evolve, the Claryville plant is poised to adapt and thrive, maintaining its role as a critical component of Tyson Foods’ operations and a valuable asset to the local community.