Tyson Foods Council Bluffs stands as a significant cornerstone of the Iowa economy, a hub of food production with a rich history and far-reaching influence. This piece offers an in-depth look at the plant’s operations, its impact on the local community, and its contributions to the broader food industry. We will explore the plant’s journey, from its initial establishment to its current standing as a major employer and economic driver.
The following sections will delve into the plant’s history, product lines, operational scale, and its profound effect on Council Bluffs. We’ll also examine the plant’s role in job creation, economic contributions, community engagement, sustainability initiatives, and technological advancements. Furthermore, we will address operational challenges, labor relations, regulatory compliance, and the intricacies of its supply chain.
Overview of Tyson Foods Council Bluffs Plant
The Tyson Foods plant in Council Bluffs, Iowa, represents a significant component of the company’s overall operations and a major contributor to the local economy. This overview provides insight into the plant’s historical development, its primary activities, and its operational scale.
Plant History
The Tyson Foods Council Bluffs plant has a history rooted in the evolution of the meatpacking industry in the region. Initially, the facility may have started under a different name or ownership, but it was eventually acquired or integrated into the Tyson Foods network. The plant’s growth and development often mirror the broader trends within the meat processing sector, including technological advancements, changes in consumer demand, and shifts in agricultural practices.
The exact date of establishment and the plant’s initial form can be researched through historical archives and industry publications, offering a more detailed account of its early operations and the factors that shaped its evolution.
Primary Product Lines and Processing Focus
The Council Bluffs plant specializes in processing specific types of protein products. It’s highly probable that the plant focuses on beef processing, potentially handling the slaughtering, cutting, and packaging of beef products. The plant’s product lines may include:
- Fresh beef cuts, such as steaks, roasts, and ground beef.
- Processed beef products, like pre-packaged ground beef or beef for further processing into items such as sausages or prepared meals.
- By-products from beef processing, which can be used in various industries.
The plant’s processing focus is on efficiency and adherence to strict quality and safety standards. The plant is designed to handle a high volume of livestock, converting them into marketable products for both retail and foodservice markets. This focus often requires specialized equipment and skilled labor.
Operational Scale
The Tyson Foods Council Bluffs plant operates on a substantial scale, reflecting the company’s position as a major player in the meat industry.
- Employee Count: The plant employs a significant workforce, potentially numbering in the thousands. The exact employee count fluctuates based on production demands, seasonality, and economic conditions. The size of the workforce underscores the plant’s importance as a major employer in the Council Bluffs area.
- Production Capacity: The plant’s production capacity is considerable, with the ability to process a large number of animals per day or week. Production capacity is a key metric for assessing the plant’s operational efficiency and its ability to meet market demands. It would be measured in terms of the number of animals processed, or the volume of product produced.
The operational scale is further reflected in the size of the facility itself, including the land area occupied by the plant, the number of buildings, and the types of machinery and equipment used in the processing operations.
Economic Impact on Council Bluffs
The Tyson Foods plant in Council Bluffs plays a significant role in the local economy, providing substantial employment opportunities and contributing significantly to the city’s financial well-being. Its presence fosters growth in related businesses and generates considerable tax revenue, making it a cornerstone of the community’s economic landscape.
Contribution to Local Employment Opportunities
The Tyson Foods plant is a major employer in Council Bluffs, offering a wide range of jobs, from production line workers to administrative and management positions. These employment opportunities are crucial for the city’s residents, providing stable incomes and contributing to a lower unemployment rate. The plant’s consistent demand for labor supports families and fuels local spending, stimulating economic activity across various sectors.
Impact on the Local Economy
The plant’s operations have a ripple effect throughout the local economy. The consistent demand for goods and services from the plant supports a network of suppliers, including transportation companies, packaging providers, and maintenance services. This creates additional jobs and generates revenue for businesses within the Council Bluffs area and beyond. Furthermore, the plant’s tax contributions are a vital source of funding for essential city services, such as infrastructure improvements, public safety, and education.
Estimated Annual Economic Contribution
The following table provides an estimated breakdown of the Tyson Foods plant’s annual economic contribution to Council Bluffs. These figures are approximate and based on industry averages and publicly available data; however, they serve to illustrate the significant impact of the plant.
Category | Estimated Annual Value | Description | Source/Basis |
---|---|---|---|
Employment Wages & Salaries | $150 – $200 million | Total wages and salaries paid to employees, including benefits. | Based on average industry wages for similar plants and estimated employee count. |
Local Supplier Spending | $50 – $75 million | Expenditures on goods and services from local businesses. | Estimates based on industry averages for supplier relationships. |
Tax Revenue (Property & Sales) | $5 – $10 million | Property taxes paid on the plant and sales tax generated by employee spending and plant operations. | Based on assessed property value and local tax rates, plus estimated sales tax contributions. |
Indirect Economic Impact | $25 – $50 million | Impact on the local economy through increased spending by employees, and related business growth. | Using multipliers commonly applied to the manufacturing sector. |
Community Involvement and Sustainability Initiatives
Tyson Foods’ Council Bluffs plant is deeply committed to being a responsible corporate citizen, actively engaging with the local community and implementing robust sustainability practices. These initiatives reflect a commitment to both the well-being of the surrounding area and the preservation of environmental resources. The plant’s approach encompasses various outreach programs, partnerships, and a dedication to reducing its environmental footprint.
Community Outreach Programs and Partnerships
The Council Bluffs plant actively fosters strong relationships within the local community through various outreach programs and collaborative partnerships. These efforts aim to support local organizations, promote educational opportunities, and contribute to the overall quality of life in the region.
- Food Donations: The plant regularly donates surplus food products to local food banks and hunger relief organizations, such as the Food Bank for the Heartland. This ensures that nutritious food reaches individuals and families in need within the Council Bluffs community. This aligns with Tyson Foods’ broader commitment to fighting food insecurity.
- Educational Partnerships: The plant collaborates with local schools and educational institutions to provide educational opportunities and support for students. This may include plant tours, internships, and scholarship programs designed to encourage interest in the food industry and related fields.
- Community Events: Tyson Foods participates in and sponsors various community events, such as local festivals, fairs, and charity runs. This involvement helps to build relationships with residents and demonstrates a commitment to supporting local initiatives that promote community spirit.
- Volunteer Programs: Employees are encouraged to volunteer their time and skills to support local charities and community projects. Tyson Foods often organizes and supports employee volunteer events, providing opportunities for employees to give back to the community.
Sustainability Practices
Tyson Foods’ Council Bluffs plant is dedicated to minimizing its environmental impact through a variety of sustainability practices. These practices focus on resource conservation, waste reduction, and responsible environmental stewardship. The plant continually seeks ways to improve its sustainability performance and reduce its carbon footprint.
- Water Conservation: The plant implements water-efficient technologies and practices to reduce water consumption. This may include the use of water recycling systems, efficient cleaning processes, and monitoring programs to identify and address water leaks.
- Waste Reduction and Recycling: The plant has established comprehensive waste reduction and recycling programs to minimize waste sent to landfills. This includes recycling paper, plastics, and other materials, as well as composting food waste when feasible.
- Energy Efficiency: The plant utilizes energy-efficient equipment and practices to reduce energy consumption. This includes the use of LED lighting, energy-efficient refrigeration systems, and optimization of operational processes to minimize energy waste.
- Renewable Energy: Tyson Foods is exploring the use of renewable energy sources at its facilities, including the potential for solar power installations. This initiative aims to reduce the plant’s reliance on fossil fuels and lower its carbon emissions.
- Sustainable Sourcing: The plant prioritizes sourcing raw materials from sustainable and responsible suppliers. This includes promoting animal welfare, reducing deforestation, and supporting environmentally friendly farming practices.
- Reducing Food Waste: The plant actively works to minimize food waste throughout its operations, from production to packaging. This includes optimizing production processes, improving inventory management, and donating surplus food to reduce waste and address food insecurity.
- Wastewater Treatment: The plant has a wastewater treatment facility to treat water used in the production process. This facility ensures that the water is cleaned and meets all regulatory requirements before being released back into the environment.
Charitable Contributions and Sponsorships
The Council Bluffs plant actively supports various charitable organizations and community initiatives through financial contributions and sponsorships. These contributions help to address critical needs in the community and support local organizations that provide valuable services.
- Financial Donations: The plant provides financial donations to local charities and non-profit organizations. These donations support a wide range of causes, including food security, education, healthcare, and community development.
- Sponsorships: The plant sponsors local events and programs that benefit the community. This may include sponsorships of youth sports teams, community festivals, and fundraising events for local charities.
- Employee Giving Programs: Tyson Foods often facilitates employee giving programs, where employees can contribute to charitable causes through payroll deductions or company-matched donations.
- Disaster Relief: The plant may provide assistance to local communities in the event of natural disasters or other emergencies. This can include donations of food, water, and financial support to help those affected by the disaster. For example, after a significant flooding event in Council Bluffs, the plant may provide food and resources to relief efforts.
Operational Challenges and Solutions
The Tyson Foods Council Bluffs plant, like any large-scale food processing facility, faces a variety of operational challenges. These challenges can range from fluctuating labor markets and supply chain disruptions to stringent food safety regulations. Addressing these issues effectively is critical to maintaining production efficiency, ensuring product quality, and upholding consumer trust. This section examines specific challenges faced by the plant and the strategies employed to overcome them.
Labor Management and Workforce Stability
The food processing industry is often characterized by demanding work environments, which can contribute to high employee turnover rates. Council Bluffs is no exception, and Tyson Foods has to work to keep a stable and motivated workforce.
- Recruitment and Retention: Attracting and retaining qualified workers is a primary challenge. The plant utilizes several strategies to combat this. This includes offering competitive wages and benefits packages, including health insurance, retirement plans, and paid time off. Additionally, the plant invests in employee development programs, such as skills training and leadership opportunities, to foster career growth and improve employee satisfaction.
- Workplace Environment: Creating a positive and safe work environment is crucial. Tyson Foods focuses on employee safety through comprehensive safety programs, regular training, and the implementation of safety protocols. Furthermore, the company actively seeks employee feedback and uses it to improve workplace conditions and address any concerns.
- Automation and Technology: Implementing automation technologies can reduce reliance on manual labor, improving efficiency and reducing the physical demands placed on employees. The plant has adopted automated systems for tasks such as packaging, labeling, and some aspects of processing, improving efficiency and reducing the need for repetitive manual labor.
Supply Chain Resilience, Tyson foods council bluffs
Disruptions in the supply chain can significantly impact production schedules and profitability. These disruptions can arise from various factors, including weather events, transportation issues, and geopolitical instability.
- Diversification of Suppliers: Tyson Foods mitigates supply chain risks by diversifying its supplier base. This strategy ensures that the plant is not overly reliant on a single source for key ingredients and materials. Having multiple suppliers provides flexibility and allows the plant to quickly switch to alternative sources in case of disruptions.
- Inventory Management: Efficient inventory management is essential to minimize the impact of supply chain delays. The plant uses sophisticated inventory management systems to monitor stock levels, forecast demand, and optimize ordering schedules. This allows them to maintain an adequate supply of raw materials and packaging materials, minimizing the risk of production stoppages.
- Strategic Partnerships: Building strong relationships with key suppliers is a priority. These partnerships can provide access to information, preferential treatment, and collaborative problem-solving. Tyson Foods works closely with its suppliers to anticipate potential challenges, such as seasonal fluctuations in supply, and to develop contingency plans.
Food Safety and Regulatory Compliance
Food safety is paramount in the food processing industry. The Council Bluffs plant operates under a strict regulatory framework designed to protect consumers.
Find out further about the benefits of street food festival that can provide significant benefits.
- Hazard Analysis and Critical Control Points (HACCP): Tyson Foods adheres to the HACCP system, a systematic approach to identifying and controlling food safety hazards. This involves identifying potential hazards at each stage of the production process, establishing critical control points (CCPs) where hazards can be prevented or controlled, setting critical limits for each CCP, monitoring CCPs, taking corrective actions when deviations occur, verifying the effectiveness of the HACCP plan, and maintaining detailed records.
- Compliance with Regulations: The plant is subject to oversight by the U.S. Department of Agriculture (USDA) and the Food Safety and Inspection Service (FSIS). Regular inspections are conducted to ensure compliance with all applicable regulations. Tyson Foods maintains a comprehensive food safety management system that meets or exceeds industry standards.
- Traceability and Recall Procedures: The plant has robust traceability systems to track products from origin to distribution. In the event of a food safety issue, these systems allow for rapid identification and isolation of affected products, minimizing the potential for consumer harm. They also have established recall procedures that are practiced regularly to ensure they can be executed effectively and efficiently.
Adaptation and Innovation
The Tyson Foods Council Bluffs plant has demonstrated an ability to adapt to changing circumstances and embrace innovation. The plant continuously invests in new technologies and process improvements to enhance efficiency, improve food safety, and reduce its environmental footprint.
- Investment in Technology: The plant has invested in advanced technologies, such as automated processing equipment, data analytics, and robotics. These investments have improved production efficiency, reduced labor costs, and enhanced food safety. For example, automated vision systems are used to inspect products for defects, ensuring that only high-quality products are shipped to consumers.
- Process Optimization: The plant continually seeks ways to optimize its production processes. This includes streamlining workflows, reducing waste, and improving energy efficiency. For instance, they may implement lean manufacturing principles to eliminate waste and improve efficiency throughout the production process.
- Employee Training and Development: Tyson Foods recognizes that its employees are its most valuable asset. The plant provides ongoing training and development opportunities to ensure that employees have the skills and knowledge needed to perform their jobs effectively. This includes training on food safety, quality control, and the operation of new technologies.
Technological Advancements at the Plant
Tyson Foods’ Council Bluffs plant has consistently integrated cutting-edge technologies to optimize its operations and maintain its position as a leader in the food processing industry. These advancements span various areas, from automation in processing lines to sophisticated data analytics for quality control and resource management. The adoption of these technologies reflects Tyson’s commitment to efficiency, food safety, and sustainability.
Automation in Processing and Packaging
The Council Bluffs plant has embraced automation to enhance efficiency and precision in its processing and packaging procedures. This includes the use of robotic systems for tasks such as deboning, trimming, and packaging, which not only increases throughput but also minimizes the risk of human error and improves worker safety. Automated guided vehicles (AGVs) are also employed to transport materials within the plant, streamlining logistics and reducing labor costs.
- Robotic Systems: Robotic arms and automated machinery perform repetitive tasks with high accuracy and speed. For example, robots can sort and package products, significantly increasing the speed and consistency of these processes compared to manual labor.
- Automated Guided Vehicles (AGVs): AGVs transport materials between different areas of the plant, optimizing the flow of goods and reducing the need for manual handling. This improves efficiency and minimizes the risk of accidents.
- Automated Inspection Systems: These systems use advanced sensors and imaging technology to detect defects and ensure product quality. For instance, X-ray inspection systems are used to identify bone fragments in processed meat products, ensuring food safety.
Data Analytics and Predictive Maintenance
The plant leverages data analytics to monitor and optimize various aspects of its operations, including production efficiency, energy consumption, and equipment performance. Predictive maintenance programs utilize sensor data and machine learning algorithms to anticipate equipment failures, allowing for proactive maintenance and minimizing downtime. Real-time data analysis also supports improved decision-making in areas such as inventory management and supply chain optimization.
- Predictive Maintenance: Sensors monitor equipment performance, and data analysis predicts potential failures. This allows for scheduled maintenance, reducing downtime and extending the lifespan of machinery. For example, analyzing vibration data from motors can identify potential bearing failures before they cause a shutdown.
- Process Optimization: Real-time data from production lines is analyzed to identify bottlenecks and inefficiencies. This information is used to adjust production parameters and optimize workflows.
- Quality Control: Data analytics are used to monitor product quality throughout the production process. This includes analyzing data from sensors and inspection systems to identify and address any deviations from quality standards.
Impact on Efficiency and Product Quality
These technological advancements have resulted in significant improvements in both efficiency and product quality at the Council Bluffs plant. Automation has increased production throughput, reduced labor costs, and minimized the risk of errors. Data analytics have improved process control, leading to more consistent product quality and reduced waste. These improvements contribute to Tyson’s ability to provide high-quality products at competitive prices.
“The integration of advanced technologies has been transformative for our Council Bluffs plant. Automation has increased our production capacity, and data analytics allows us to make informed decisions that improve product quality and reduce waste. We are constantly looking for new ways to leverage technology to enhance our operations.”
Labor Relations and Workforce
Tyson Foods’ Council Bluffs plant recognizes the importance of its workforce and the dynamics of labor relations. The company strives to foster a positive and productive work environment, balancing the needs of its employees with the operational demands of a large-scale food processing facility. This section provides insights into the plant’s labor relations, employee benefits, training programs, work environment, and employee demographics.
Union Presence
The Council Bluffs plant operates with a unionized workforce. The specific union representing the employees is the United Food and Commercial Workers (UFCW) Local 230. This union represents the workers and negotiates collective bargaining agreements that address wages, benefits, and working conditions. These agreements provide a framework for labor relations, ensuring fair treatment and promoting employee rights. The presence of the union plays a significant role in shaping the plant’s labor policies and fostering a structured environment for addressing employee concerns and grievances.
Employee Benefits
Tyson Foods offers a comprehensive benefits package to its employees at the Council Bluffs location. These benefits are designed to support employees’ well-being and provide financial security.
- Healthcare: Employees have access to medical, dental, and vision insurance plans. These plans typically include options for both individual and family coverage.
- Retirement: Tyson Foods provides retirement savings plans, such as a 401(k), allowing employees to save for their future. The company may offer matching contributions to help employees grow their retirement savings.
- Paid Time Off: Employees receive paid time off, including vacation, sick leave, and holidays. The amount of paid time off varies based on length of service and employment status.
- Life Insurance and Disability Coverage: The company provides life insurance and disability coverage to protect employees and their families in the event of unexpected circumstances.
- Employee Assistance Program (EAP): An EAP is available to employees and their families, offering confidential counseling and support services for various personal and work-related issues.
Training Programs
Tyson Foods invests in comprehensive training programs to equip its employees with the skills and knowledge necessary to perform their jobs effectively and safely. These programs also contribute to employee development and career advancement opportunities.
- Onboarding Training: New employees participate in onboarding training to familiarize themselves with the company’s policies, safety procedures, and job-specific responsibilities. This initial training is crucial for ensuring a smooth transition into the workplace.
- Safety Training: Safety is a top priority at the Council Bluffs plant. Employees receive ongoing safety training to prevent workplace accidents and ensure compliance with safety regulations. This training covers topics such as hazard recognition, proper use of equipment, and emergency procedures.
- Skills-Based Training: The plant offers skills-based training programs to enhance employees’ technical abilities. These programs may cover topics such as food processing techniques, equipment operation, and quality control procedures.
- Leadership Development: For employees interested in career advancement, leadership development programs are available. These programs focus on developing leadership skills, such as communication, problem-solving, and team management.
- Cross-Training: Employees may have the opportunity for cross-training to learn different job functions within the plant. This helps to increase their versatility and provides opportunities for career growth.
Work Environment and Employee Demographics
The work environment at the Tyson Foods Council Bluffs plant is characterized by a fast-paced, production-oriented atmosphere. The plant operates 24 hours a day, seven days a week, to meet the high demand for its products. The work involves standing for extended periods, working with machinery, and handling food products.The employee demographics at the plant are diverse, reflecting the community in which it is located.
The workforce includes individuals from various ethnic and cultural backgrounds. The plant employs a significant number of workers from the local area, as well as individuals who have relocated to Council Bluffs for employment opportunities. While specific demographic data can fluctuate, the plant’s workforce generally reflects the diversity of the region.
Regulatory Compliance and Inspections
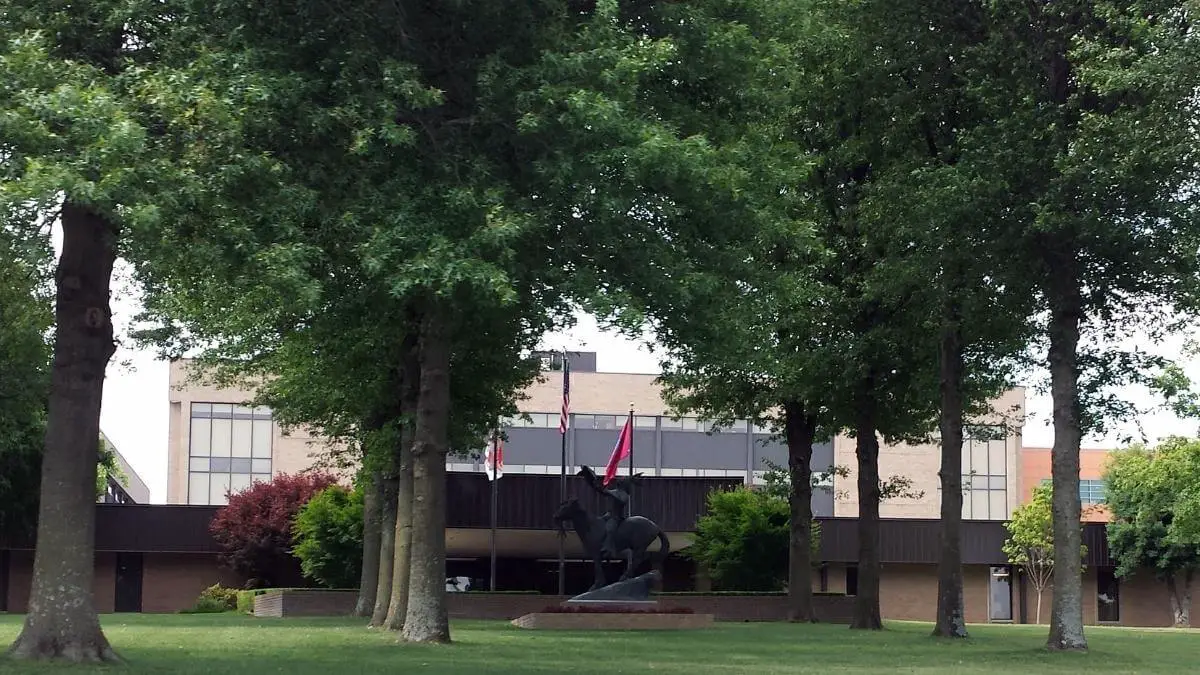
The Tyson Foods Council Bluffs plant operates under a stringent regulatory framework designed to ensure food safety, worker safety, and environmental responsibility. Compliance with these regulations is critical to the plant’s continued operation and its commitment to producing high-quality products. Regular inspections by various regulatory bodies are a key component of this compliance process.
Regulatory Bodies Overseeing Operations
Several governmental agencies and organizations play a role in overseeing the Tyson Foods Council Bluffs plant’s operations. These bodies enforce regulations related to food safety, worker safety, and environmental protection.
- United States Department of Agriculture (USDA): The USDA’s Food Safety and Inspection Service (FSIS) is the primary regulatory body overseeing the plant’s food safety practices. FSIS inspectors are present daily at the plant to ensure compliance with federal regulations related to meat and poultry processing, including sanitation, Hazard Analysis and Critical Control Points (HACCP) plans, and labeling.
- Occupational Safety and Health Administration (OSHA): OSHA is responsible for ensuring worker safety and health. The agency conducts inspections to identify and address workplace hazards, ensuring compliance with safety standards, including those related to machinery, personal protective equipment, and hazard communication.
- Environmental Protection Agency (EPA): The EPA oversees environmental regulations, including those related to wastewater discharge, air emissions, and waste management. The Council Bluffs plant must comply with the Clean Water Act, the Clean Air Act, and other relevant environmental regulations.
- Iowa Department of Natural Resources (IDNR): The IDNR often works in conjunction with the EPA and enforces state-level environmental regulations. The IDNR may conduct inspections related to wastewater treatment, air quality, and solid waste disposal.
Frequency and Types of Inspections
The Council Bluffs plant undergoes a variety of inspections to ensure ongoing compliance with all applicable regulations. The frequency and type of inspection vary depending on the regulatory body and the specific area being inspected.
- USDA/FSIS Inspections: FSIS inspectors are present at the plant on a daily basis. They conduct continuous inspections of the production process, including carcass inspection, sanitation procedures, and adherence to HACCP plans. In addition to daily inspections, FSIS may conduct more comprehensive audits and reviews periodically.
- OSHA Inspections: OSHA inspections are conducted periodically, often triggered by employee complaints, reported injuries, or scheduled compliance audits. Inspections may focus on specific areas of the plant, such as the processing lines, maintenance areas, or cold storage facilities.
- EPA and IDNR Inspections: Environmental inspections by the EPA and IDNR are conducted on a scheduled basis, typically at least annually, but may occur more frequently. These inspections focus on wastewater treatment systems, air emission controls, and waste management practices.
Process for Addressing and Resolving Inspection Findings
The Tyson Foods Council Bluffs plant has established procedures for addressing and resolving any findings or violations identified during inspections. These procedures are designed to ensure prompt corrective action and prevent recurrence.
- Identification of Findings: During an inspection, inspectors will document any observations of non-compliance with regulations. These findings may be documented in the form of notices of violation, inspection reports, or other official communications.
- Response and Corrective Action: The plant management team is responsible for responding to inspection findings. This typically involves investigating the root cause of the issue, developing a corrective action plan, and implementing the necessary changes.
- Documentation and Record Keeping: All corrective actions taken are documented, including the date of the action, the specific steps taken, and the results of the action. This documentation is essential for demonstrating compliance and for tracking the effectiveness of corrective actions.
- Verification and Follow-up: Regulatory agencies may conduct follow-up inspections to verify that corrective actions have been implemented and that the issues have been resolved. The plant must maintain ongoing monitoring and verification processes to ensure continued compliance.
- Examples of Corrective Actions: Corrective actions can vary depending on the nature of the violation. For example, if a sanitation violation is identified by the USDA, the plant might implement more frequent cleaning and sanitizing procedures. If an OSHA violation is identified, the plant might provide additional employee training or modify safety procedures.
Raw Materials and Supply Chain: Tyson Foods Council Bluffs
The Tyson Foods Council Bluffs plant’s operations are heavily reliant on a robust and efficient supply chain to ensure a consistent flow of raw materials. This intricate network is crucial for maintaining production levels and meeting consumer demand. Sourcing and managing these materials presents unique challenges that the plant actively addresses.
Plant’s Supply Chain Overview
The Council Bluffs plant’s supply chain is a complex, multi-faceted system designed to bring in large quantities of raw materials, primarily livestock, and convert them into a variety of processed meat products. The supply chain operates across several states, and even internationally, depending on specific needs.
- Livestock Sources: The primary raw material is livestock, mainly cattle and hogs. These animals are sourced from a network of farms and ranches located throughout the Midwest, including Iowa, Nebraska, Kansas, and other surrounding states. Tyson works with both independent farmers and larger agricultural operations.
- Grain and Feed: The plant requires significant amounts of grain, particularly corn and soybeans, for animal feed. These are sourced from local and regional agricultural suppliers, contributing to the economic vitality of the area.
- Packaging Materials: A diverse range of packaging materials is required, including plastic films, cardboard boxes, and labeling materials. These are procured from various suppliers, often located in the Midwest and across the United States, to ensure product safety and shelf-life.
- Processing Ingredients: Various ingredients, such as seasonings, spices, and preservatives, are sourced from specialized suppliers, often through long-term contracts to guarantee consistent quality and availability.
Challenges Related to Sourcing Raw Materials
Sourcing raw materials is not without its challenges. The plant must navigate market fluctuations, logistical hurdles, and potential disruptions to maintain a stable supply.
- Price Volatility: The prices of livestock and grain are subject to market forces, including weather patterns, global demand, and geopolitical events. These fluctuations can impact the plant’s operational costs and profitability. For example, a severe drought in the Midwest can significantly increase corn prices, subsequently affecting the cost of animal feed and the overall cost of production.
- Transportation and Logistics: Efficient transportation is critical to the timely delivery of raw materials. The plant relies on a network of trucks and potentially rail to transport livestock and other materials. Weather events, such as severe snowstorms or floods, can disrupt transportation schedules, leading to potential shortages.
- Disease Outbreaks: Outbreaks of animal diseases, such as bovine spongiform encephalopathy (BSE) or African swine fever (ASF), can have a significant impact on the availability of livestock. Stringent biosecurity measures and proactive disease management are crucial for mitigating these risks.
- Sustainability and Ethical Sourcing: Increasingly, consumers and stakeholders are demanding sustainably sourced products. The plant must address concerns related to animal welfare, environmental impact, and responsible sourcing practices.
Illustration: Journey of Raw Materials to the Plant
Imagine a detailed illustration depicting the journey of raw materials, specifically cattle, to the Tyson Foods Council Bluffs plant.The illustration would be a multi-panel depiction showing the entire process. The first panel shows a vast, green pasture under a bright sky. Cattle graze peacefully, representing the initial stage. The next panel transitions to a loading scene, where the cattle are being carefully loaded onto specialized livestock trailers.
The trailers are large, enclosed vehicles designed for the safe and comfortable transport of animals. These trucks are painted with the Tyson Foods logo.The following panel depicts the journey itself. The livestock trailers are shown traveling on a highway, passing through rural landscapes and towns. The trailers are connected to powerful semi-trucks, indicating the long distances the raw materials travel.
The image would include details such as road signs, other vehicles, and weather conditions to add realism.The next panel shows the arrival at the Council Bluffs plant. The trailers are entering the facility through a designated receiving area. The plant’s large buildings and infrastructure are visible in the background. This area would show detailed unloading procedures and the transfer of cattle to the processing facility.The final panel focuses on the unloading and initial processing of the cattle within the plant.
This panel would feature workers in protective gear overseeing the process, alongside specialized machinery designed for handling and preparing the animals for further processing. The illustration would also show the movement of the processed material within the plant. This panel would depict the various stages involved in the transformation of raw materials into finished products, showcasing the integration of technology and human labor.
The image would clearly show the movement of materials throughout the different stages of the process, including initial inspection, slaughter, and preliminary cuts.
Outcome Summary
In conclusion, Tyson Foods Council Bluffs represents more than just a food processing plant; it’s a vital component of the local ecosystem. From its contributions to employment and economic growth to its commitment to sustainability and community involvement, the plant plays a pivotal role. Understanding the complexities of its operations, the challenges it faces, and the innovations it embraces provides valuable insight into the future of food production and its impact on communities.
The plant continues to evolve and adapt, ensuring its enduring presence in Council Bluffs and beyond.