Food can dimensions are more than just measurements; they’re the foundation upon which the entire food packaging industry is built. From the humble can of soup to the towering tin of coffee, the precise size and shape of these containers dictate everything from manufacturing efficiency to consumer experience. This exploration delves into the intricacies of food can dimensions, unraveling their significance, standard sizes, measurement techniques, and the myriad factors that influence them.
We’ll examine the various units of measurement, explore common can sizes using a responsive HTML table, and discuss the critical role dimensions play in ensuring product safety, quality, and optimal performance on automated packaging lines. Furthermore, the discussion will encompass the impact of food processing methods, can materials, labeling requirements, and regulatory considerations, all of which shape the dimensions of the food cans we see on store shelves.
Introduction to Food Can Dimensions
Food can dimensions refer to the precise measurements that define the size and shape of food containers. These dimensions are crucial for various aspects of the food industry, including manufacturing, packaging, storage, transportation, and consumer convenience. Accurate and standardized dimensions ensure efficient production processes, optimal product preservation, and compliance with industry regulations.Precise can dimensions are essential because they affect everything from filling equipment compatibility to shelf space utilization.
Incorrect dimensions can lead to operational inefficiencies, product damage, and potential safety hazards. Understanding and adhering to these dimensions is therefore fundamental for businesses involved in food production and distribution.
Units of Measurement
The measurement of food can dimensions typically employs a combination of imperial and metric units, often used concurrently to accommodate global standards and manufacturing processes. The common units are essential for clear communication and standardization within the industry.
- Inches (in): Primarily used in the United States, can dimensions are often expressed in inches, particularly in older manufacturing standards. Fractional inches, such as 3 1/16 inches, are common.
- Millimeters (mm): The metric system is widely adopted globally, and can dimensions are frequently specified in millimeters. This provides a more precise and standardized approach.
- Diameter and Height: The key dimensions are typically the diameter of the can’s base and the overall height of the can.
- Customary Notation: In some regions, particularly within the US food industry, a specific notation is employed. This is often in the format of “inches and sixteenths,” where a can might be described as “307 x 409.” The first three digits represent the diameter in inches and sixteenths (307 = 3 7/16 inches), and the last three digits represent the height in inches and sixteenths (409 = 4 9/16 inches).
Critical Importance of Precise Dimensions
The accuracy of food can dimensions has significant implications across the entire food supply chain. From the initial manufacturing process to the consumer’s experience, precise dimensions contribute to operational efficiency, product safety, and consumer satisfaction.
- Manufacturing and Filling: Automated filling machines are designed to work with specific can sizes. Deviations from these dimensions can cause jams, spills, and inaccurate fill levels, leading to product waste and reduced production efficiency.
- Seaming and Sealing: The seaming process, which creates an airtight seal between the can body and the lid, relies on precise can dimensions. Incorrect dimensions can result in faulty seals, potentially compromising the product’s shelf life and safety.
- Labeling: Label dimensions must precisely match the can’s surface area. Inaccurate dimensions can lead to misaligned or improperly affixed labels, affecting product presentation and potentially obscuring critical information such as ingredients and nutritional facts.
- Storage and Transportation: Standardized can dimensions allow for efficient stacking and storage, maximizing warehouse space. During transportation, consistent dimensions enable secure palletization and minimize the risk of damage.
- Shelf Space Optimization: Retailers optimize shelf space by considering can dimensions. Consistent dimensions facilitate efficient product display and inventory management, improving product visibility and sales.
- Consumer Safety and Convenience: Consistent dimensions are essential for easy opening, handling, and storage by consumers. Accurate dimensions ensure that the product fits standard can openers and is easily stored in pantries or refrigerators.
- Regulation Compliance: Food can dimensions often influence the net weight and volume of the product, which must comply with regulations set by governmental agencies, such as the Food and Drug Administration (FDA) in the United States.
Standard Can Sizes and Types
Understanding standard can sizes and types is crucial for food manufacturers, retailers, and consumers. These standards ensure efficient production, distribution, and consumer convenience. Adherence to these dimensions facilitates compatibility with canning equipment, shelf space optimization, and portion control. The dimensions directly influence the volume of food a can can hold, affecting both cost and consumer perception.
Common Food Can Sizes, Food can dimensions
A variety of standardized can sizes exist, each designed to accommodate different food products and serving sizes. The diameter and height are the key measurements that define a can’s capacity. These dimensions are often expressed in inches, using a three-digit system (e.g., 307 x 409). The first digit represents inches, the second and third digits represent sixteenths of an inch.
For example, 307 translates to 3 and 7/16 inches. This standardized system allows for clear communication and accurate manufacturing. The following table illustrates common can sizes and their typical applications:
Can Size (Diameter x Height) | Approximate Volume (Fluid Ounces) | Typical Food Products | Notes |
---|---|---|---|
211 x 200 | 8 | Vegetables (e.g., green beans, peas), Fruits (e.g., peaches) | Often used for single-serving portions. |
300 x 407 | 14.5 – 15 | Fruits (e.g., peaches, pears), Vegetables (e.g., corn, beans), Soups | A common size for family-sized servings. |
307 x 409 | 16 – 17 | Fruits (e.g., peaches, pears), Vegetables (e.g., corn, beans), Soups | Similar to 300 x 407, but with a slightly larger capacity. |
401 x 411 | 28 – 29 | Vegetables (e.g., tomatoes, beans), Fruits (e.g., fruit cocktail), Soups | A larger size suitable for multiple servings. |
603 x 700 | 105 – 108 | Institutional foods, large quantities of vegetables and fruits, often for foodservice applications | Used for large-scale food preparation and storage. |
Can Types and Dimensional Relationships
The type of can construction significantly influences its dimensions and overall functionality. There are primarily two main types: two-piece and three-piece cans. Each type has unique manufacturing processes and dimensional implications.
Two-piece cans are typically made from a single piece of metal, usually aluminum or steel. The body and bottom are formed from a single sheet, with the top sealed on afterward. The absence of a side seam makes them structurally stronger, often resulting in slightly thinner walls. This can potentially lead to a slightly larger internal volume for a given external dimension, which can be beneficial for certain products.
Three-piece cans, the older and more common type, consist of three separate pieces: the body, the top, and the bottom. The body is a cylindrical piece of metal, with a side seam that is either soldered, welded, or cemented. The top and bottom are then seamed onto the body. The presence of the side seam introduces a potential weak point.
The seaming process itself, however, has become highly refined and can withstand considerable pressure. The side seam also influences the precise dimensions and can sometimes require slightly larger external dimensions to accommodate the seam, compared to two-piece cans of the same internal volume. The choice between two-piece and three-piece cans depends on factors like the food product, desired shelf life, cost, and manufacturing capabilities.
Measuring Food Can Dimensions
Accurate measurement of food can dimensions is crucial for various aspects of the food industry, including manufacturing, quality control, and regulatory compliance. Precise measurements ensure proper fit within packaging machinery, consistent product volume, and adherence to labeling standards. This section Artikels the necessary tools and procedures for achieving reliable and consistent measurements.
Tools and Instruments for Measuring Can Dimensions
The following tools are commonly employed to measure food can dimensions with accuracy. Proper calibration and maintenance of these instruments are essential for reliable results.
- Digital Calipers: Digital calipers provide highly accurate measurements of both diameter and height. They typically offer a resolution of 0.01 mm (0.0005 inches) or better. They are easy to read and can often convert between metric and imperial units. A digital display eliminates the potential for parallax error, which can occur with analog instruments.
- Vernier Calipers: Vernier calipers, also known as dial calipers, are a more traditional option. They are manually read, offering similar accuracy to digital calipers, though readings require a degree of user interpretation. Proper technique is important to minimize reading errors.
- Micrometers: Micrometers are designed for highly precise measurements, especially for smaller dimensions. They are particularly useful for measuring the thickness of can components like the can body or the end seam. Micrometers offer very fine resolution, often to the nearest 0.001 mm (0.00005 inches).
- Height Gauges: Height gauges are used to measure the overall height of the can, including the end seams. They are especially useful for measuring the “double seam” height, a critical dimension for can integrity. Height gauges can be either digital or analog.
- Measurement Standards: Reference standards, such as calibrated gauge blocks or rings, are essential for verifying the accuracy of the measurement tools. Regular calibration of the instruments against known standards ensures their continued reliability.
Procedure for Measuring Can Diameter and Height
Correct measurement techniques are vital for obtaining accurate and reproducible results. The following procedures should be followed when measuring can diameter and height.
- Diameter Measurement:
- Tool Selection: Select either digital or vernier calipers. Ensure the calipers are clean and free from any damage.
- Calibration Check: Before measurement, close the caliper jaws and verify that the reading is zero. If not, adjust the caliper accordingly.
- Measurement Points: Measure the diameter at multiple points around the can, typically at 90-degree or 120-degree intervals, to account for any slight variations in roundness. This is especially important for drawn cans.
- Application: Position the can between the caliper jaws, ensuring the jaws are perpendicular to the can’s surface. Close the jaws gently but firmly until they contact the can surface.
- Reading: Record the diameter reading from the digital display or the vernier scale.
- Repeat: Repeat the measurement at least three times at different points around the can to obtain an average diameter.
- Height Measurement:
- Tool Selection: Use a height gauge or digital calipers.
- Base Placement: Place the can on a flat, stable surface.
- Measurement Points: Position the height gauge’s measuring face on the top of the can end.
- Alignment: Ensure the height gauge is perpendicular to the base and the can end.
- Application: Gently lower the height gauge until it contacts the top of the can.
- Reading: Record the height measurement from the digital display or the scale.
- Repeat: Repeat the measurement several times and calculate the average height. When measuring the double seam height, the height gauge should measure from the top of the can end to the bottom of the double seam.
Importance of Consistent Measurement Techniques
Maintaining consistent measurement techniques is critical for ensuring data reliability and comparability across different measurements, operators, and locations. Inconsistent practices can lead to significant errors, affecting product quality and safety.
- Standardized Procedures: Establish and follow standardized measurement procedures. This includes specifying the type of instrument, the number of measurements, the points of measurement, and the method of reading the instrument.
- Operator Training: Train all personnel involved in measuring can dimensions on the standardized procedures and the proper use of the measurement instruments. Regular training and refresher courses can help maintain consistency.
- Regular Calibration and Maintenance: Regularly calibrate all measurement instruments using traceable standards. Implement a schedule for instrument maintenance, including cleaning, lubrication, and repair.
- Documentation: Document all measurement procedures, results, and calibration records. This provides a clear audit trail and allows for the identification of any measurement inconsistencies.
- Statistical Process Control (SPC): Implement SPC techniques to monitor the variation in can dimensions over time. This helps identify any trends or shifts in the process that could lead to out-of-specification cans. For example, if a can manufacturer notices a gradual increase in can height measurements over several production runs, they can investigate the cause and make necessary adjustments to prevent the production of cans outside of acceptable tolerance levels.
Factors Influencing Can Dimensions
Several factors significantly impact the dimensions of food cans, ranging from the food processing techniques employed to the materials used in the can’s construction and even the requirements for labeling. Understanding these influences is critical for ensuring product safety, optimizing manufacturing processes, and meeting consumer expectations. The interplay of these factors determines the final size, shape, and overall functionality of the food can.
Food Processing Methods and Their Impact
The methods used to process food within a can have a direct effect on the can’s dimensions. These processes often involve elevated temperatures and pressures, which can stress the can’s structure.Retorting and sterilization are common methods, and each impacts the can differently:
- Retorting: This process involves heating sealed cans in a pressurized environment, typically using steam. The high temperatures and pressures are necessary to kill microorganisms and ensure food safety. The internal pressure generated during retorting can cause the can to expand slightly. Manufacturers design cans to withstand these pressures, and the dimensions must accommodate the anticipated expansion without compromising the can’s integrity or the seal.
- Sterilization: Similar to retorting, sterilization aims to eliminate microorganisms. The process involves exposing the filled and sealed can to high temperatures for a specific duration. The effects on can dimensions are comparable to retorting, with potential expansion due to internal pressure. The can material and design must be robust enough to prevent deformation or failure during sterilization.
The degree of expansion and the subsequent dimensional changes depend on factors such as the can’s internal volume, the food’s composition, and the specific temperature and pressure parameters of the processing method.
Effects of Can Materials on Size and Shape
The material from which a food can is constructed plays a vital role in determining its size, shape, and overall structural integrity. The two primary materials used are steel and aluminum, each with distinct properties that influence can dimensions.
- Steel: Steel cans are known for their strength and durability, making them suitable for a wide range of food products, especially those requiring robust packaging. Steel cans can withstand high pressures and temperatures during processing and handling. The dimensions of steel cans can be optimized for efficient stacking and transportation. Steel cans are also highly recyclable.
- Aluminum: Aluminum cans are lightweight and corrosion-resistant, making them ideal for products that require a lighter package. Aluminum cans are often used for beverages and certain food products. The material’s malleability allows for various shapes and designs. Aluminum’s lower density compared to steel results in a can that can be thinner, potentially affecting overall dimensions and allowing for more efficient storage and transport.
The choice of material also affects the manufacturing process. Steel cans are typically formed using a three-piece construction (body, top, and bottom), while aluminum cans are often drawn or formed in a single piece. These differences in manufacturing can influence the precision and tolerances of the can’s dimensions.
Influence of Labeling Requirements
Labeling requirements significantly impact the final dimensions of food cans. These requirements, mandated by regulatory bodies, dictate the information that must be displayed on the can, including product name, ingredients, nutritional information, and manufacturer details.
- Label Size and Placement: The size of the label directly affects the can’s overall height and circumference. Larger labels, required for more detailed information, necessitate a larger can surface area. The placement of the label, whether a full wrap-around or a smaller panel, influences the can’s shape and the dimensions needed to accommodate the label without obscuring important information.
- Legal Requirements: Food labeling regulations often specify minimum font sizes and the amount of space required for certain information. These regulations indirectly influence the can’s dimensions, as manufacturers must ensure there is sufficient space on the label to meet these requirements.
- Aesthetic Considerations: While not strictly regulatory, the aesthetic appeal of the label and the can’s overall design can influence dimensions. Manufacturers may choose can shapes and sizes that enhance the visual presentation of the product, thereby influencing the can’s overall dimensions to create a product that stands out on shelves.
The need to accommodate labeling requirements is a critical factor in the design process. Manufacturers must balance the need for adequate labeling space with considerations for product volume, manufacturing efficiency, and consumer appeal.
Dimensional Tolerances and Standards
In the manufacturing of food cans, maintaining precise dimensions is crucial for ensuring proper sealing, filling, and compatibility with packaging equipment. However, absolute precision is unattainable in any manufacturing process. This is where dimensional tolerances come into play, defining the acceptable range of variation for each can dimension. Adhering to these tolerances is essential for maintaining product quality, preventing manufacturing defects, and ensuring consumer safety.
Dimensional Tolerances in Can Manufacturing
Dimensional tolerances represent the permissible variation in the dimensions of a food can. These tolerances are established to accommodate the inherent variability in the manufacturing processes and the materials used. They define the upper and lower limits within which a specific dimension must fall to be considered acceptable. Tight tolerances demand more precise manufacturing processes and stricter quality control measures, leading to potentially higher production costs.
Conversely, wider tolerances may reduce manufacturing costs but could compromise can performance and functionality.The following factors contribute to dimensional variations:
- Material Properties: The thickness, composition, and consistency of the metal sheets used in can manufacturing can influence the final dimensions.
- Manufacturing Processes: Variations in cutting, forming, welding, and seaming processes can introduce dimensional deviations.
- Equipment Calibration: Inaccurate calibration of machinery can lead to dimensional errors.
- Environmental Factors: Temperature and humidity can affect the dimensions of both the metal and the can components.
Industry Standards for Can Dimensions
Several industry standards and organizations provide guidelines and specifications for food can dimensions. These standards ensure interchangeability, compatibility with filling and sealing equipment, and consumer safety. Some of the prominent standards include:
- The Can Manufacturers Institute (CMI): The CMI, an industry association, publishes technical manuals and guidelines that address can dimensions and tolerances.
- The Food and Drug Administration (FDA): While the FDA does not directly set dimensional standards, it regulates food safety and labeling, indirectly influencing can dimensions to ensure product integrity and accurate labeling.
- International Organization for Standardization (ISO): ISO standards, such as those related to packaging materials, provide globally recognized guidelines for can dimensions and quality control.
These standards specify dimensions for various can sizes and types, including:
- Can Diameter: The outer diameter of the can body.
- Can Height: The overall height of the can, including the end closures.
- End Dimensions: The diameter and profile of the can ends, crucial for sealing.
- Seam Dimensions: The dimensions of the double seam, which is the critical seal between the can body and the end closures.
For example, a standard 303×406 can (common for vegetables) might have the following specifications:
Dimension | Nominal Value | Tolerance |
---|---|---|
Diameter | 3.03 inches | ± 0.005 inches |
Height | 4.06 inches | ± 0.010 inches |
These are illustrative values; actual tolerances vary based on the specific can type, manufacturer, and industry standards.
Consequences of Exceeding Dimensional Tolerances
Exceeding the specified dimensional tolerances can lead to a range of problems, affecting product quality, manufacturing efficiency, and consumer safety.
- Sealing Issues: Variations in can dimensions, particularly in the seam dimensions, can compromise the integrity of the seal, leading to leaks, spoilage, and potential contamination.
- Filling Problems: Cans that are not within the specified dimensions may not fit properly on filling lines, causing spills, reduced filling accuracy, and production downtime.
- Equipment Malfunctions: Cans outside of tolerance can damage or jam filling, seaming, and labeling equipment.
- Product Damage: Incorrect dimensions can affect the stacking and handling of cans, leading to denting, crushing, or other forms of damage during storage and transportation.
- Regulatory Non-Compliance: Cans that do not meet industry standards may fail to comply with food safety regulations, potentially leading to product recalls and legal liabilities.
- Reduced Shelf Life: Inadequate sealing due to dimensional issues can lead to premature spoilage, shortening the product’s shelf life.
The following is an example of how exceeding tolerance can lead to issues.
If the can diameter is too large, it may not fit within the seaming machine, resulting in an incomplete seal. Conversely, if the can height is too short, the can may not be filled to the correct level, affecting the product’s weight and appearance.
The Role of Dimensions in Packaging Equipment
The precise dimensions of food cans are not merely cosmetic; they are fundamental to the efficient operation of the machinery that fills, seams, and transports them. These dimensions dictate the design parameters of the equipment, impacting everything from the speed of production to the integrity of the final product. Understanding this relationship is critical for manufacturers seeking to optimize their packaging processes and minimize downtime.
Can Dimensions and Filling and Seaming Machines
The dimensions of a food can are critical determinants of how filling and seaming machines function. These machines are engineered with specific tolerances to handle cans of varying sizes, but deviations from these tolerances can lead to significant operational issues.
- Filling Machine Compatibility: Filling machines are designed to dispense a precise volume of product into each can. The can’s diameter and height directly influence the filling head’s design and the mechanism used to measure and dispense the product. For example, a can with a larger diameter might require a different filling head configuration than a can with a smaller diameter to ensure consistent and accurate filling.
The internal volume calculation is based on the can dimensions.
- Seaming Machine Functionality: Seaming machines create an airtight seal by interlocking the can body, end, and cover. The can’s dimensions, especially the flange dimensions (the part of the can body that is folded over during the seaming process) and the curl of the end, must be precisely matched to the seaming chuck and rollers. Incorrect dimensions can result in incomplete seams, leaks, or even machine jams.
- Impact on Production Speed: Can dimensions affect the speed at which the filling and seaming machines can operate. Machines are often calibrated for a specific range of can sizes. Significant deviations from the designed dimensions can slow down the process. If a machine is set for a specific can height and a can slightly taller is introduced, the seaming process might be compromised, or the machine might need to be stopped for recalibration.
Further details about yaya foods slovenia is accessible to provide you additional insights.
- Tolerance Considerations: Equipment manufacturers specify tolerances for can dimensions. Exceeding these tolerances can cause the equipment to malfunction. For instance, a can with a slightly larger diameter than specified may not fit properly in the seaming chuck, preventing a proper seal. Similarly, variations in the can height can affect the filling accuracy.
Can Dimensions and Conveyor Systems
Conveyor systems are the arteries of a packaging line, transporting cans between different stages of the process. The dimensions of the cans directly influence the design and operation of these systems.
- Conveyor Width and Spacing: The width of the conveyor belt and the spacing between the guide rails are determined by the can’s diameter. These parameters must be adjusted to ensure that the cans move smoothly without tipping or jamming. For example, a wider can would necessitate a wider conveyor belt and wider spacing between the guide rails to accommodate the can’s dimensions.
- Conveyor Speed and Stability: The height of the can influences the conveyor’s stability. Taller cans have a higher center of gravity and are more prone to tipping, especially at higher conveyor speeds or during turns. Manufacturers must consider these factors when designing the conveyor system to ensure that cans remain upright and stable throughout the process.
- Accumulation and Buffer Systems: Can dimensions impact the design of accumulation tables and buffer systems. These systems are used to temporarily store cans to maintain a consistent flow to downstream equipment. The size and configuration of these systems must be able to accommodate the can’s dimensions to prevent bottlenecks or delays.
- Sensor and Detection Systems: The dimensions of the cans affect the placement and calibration of sensors used to detect can presence, count cans, or check for defects. The sensor’s effective range and positioning are designed based on the can’s size and shape. A can that is shorter than anticipated may not trigger the sensor, leading to production errors.
Impact of Incorrect Can Dimensions on Automated Packaging Lines
Incorrect can dimensions can create significant problems in automated packaging lines, resulting in decreased efficiency, product waste, and costly downtime. A practical scenario can illustrate the impact of these issues.Consider a food processing plant that packages diced tomatoes. The plant uses a high-speed automated packaging line that includes filling machines, seaming machines, and a labeling system. The line is designed to handle standard 303 x 406 cans (3 3/16 inches diameter, 4 6/16 inches height).
If a batch of cans with incorrect dimensions is introduced into the line, the following problems can arise:
- Filling Machine Malfunction: If the cans are slightly taller than the standard dimension, the filling machine’s filling heads may not be able to reach the can opening properly, leading to underfilling or spillage. If the can’s diameter is smaller, the filling heads might not seal effectively against the can’s opening, causing product leakage.
- Seaming Machine Failure: Cans with incorrect flange dimensions may not seam correctly. The seaming chuck and rollers may not be able to create a tight, airtight seal. This can lead to defective cans that leak or spoil, resulting in product waste and potential health hazards. This could mean the plant would need to shut down the line to perform quality checks.
- Conveyor System Disruptions: If the cans are wider than the standard dimensions, they may jam on the conveyor system, causing a complete stoppage of the line. Taller cans may become unstable and tip over, causing further disruptions.
- Labeling Issues: If the can dimensions are incorrect, the labels may not adhere properly. The labeling machine is designed to apply labels of a specific size to cans of a specific diameter and height. If the can’s dimensions are different, the labels may be misaligned, wrinkled, or detached, resulting in product defects and aesthetic issues.
This scenario highlights the critical role of can dimensions in maintaining the efficiency and reliability of automated packaging lines. Precise dimensional control is essential to ensure the smooth operation of the equipment, the quality of the packaged product, and the overall profitability of the food processing operation.
Dimension Related Terminology
Understanding the specific terminology associated with food can dimensions is crucial for accurate communication, effective manufacturing, and ensuring compatibility with packaging equipment. This section defines key terms and provides a comprehensive glossary to aid in navigating the complexities of can dimensions.
Definition of Key Terms
Several fundamental terms are essential for describing food can dimensions. These terms precisely define the critical measurements that dictate a can’s size and shape.
- End Diameter: This refers to the outside diameter of the can’s end, also known as the can’s top or bottom. It’s the measurement across the circular end of the can. This measurement is critical for determining the size of the can’s closure and its compatibility with sealing equipment.
- Body Diameter: The body diameter is the outside diameter of the cylindrical portion of the can. It’s the measurement across the main, straight-walled section of the can. This dimension is crucial for determining the can’s overall volume and its fit within shipping containers and retail displays.
- Flange Height: The flange height is the height of the flange, which is the outward-curved rim at the top and bottom of the can. The flange is essential for providing a sealing surface for the can ends and for facilitating the seaming process.
- Overall Height: This refers to the total height of the can, measured from the bottom of the can to the top of the can, including the height of the flanges and the body. It’s a critical dimension for determining the can’s capacity and its compatibility with filling and labeling equipment.
Glossary of Common Terminology
A comprehensive understanding of food can dimensions requires familiarity with a range of terms beyond the basic definitions. This glossary provides a consolidated reference for common terminology.
- Can Height: Equivalent to overall height.
- Can Body: The cylindrical portion of the can, excluding the ends and flanges.
- Can End: The top or bottom of the can, typically a circular metal disk.
- Chime: The curved transition area between the can body and the flange. It reinforces the can’s structure.
- Double Seam: The hermetic seal created by interlocking the can end and the can body flange. This is a critical process for food preservation.
- Headspace: The empty space left in the can after filling and sealing. This space allows for thermal expansion during processing and prevents can deformation. The ideal headspace is often determined by the product being packaged.
- Lid: Synonymous with can end.
- Necked-in Can: A can where the body diameter is smaller than the end diameter. This design can improve stacking and storage efficiency.
- Panel: The flat or slightly curved surface of the can body, often used for labeling.
- Seam: The area where the can end and body are joined. This is a critical point for the integrity of the package.
- Shoulder: The point where the can body transitions to the flange.
- Tolerances: The permissible variations in dimensions. Strict adherence to tolerances is crucial for ensuring proper sealing and equipment compatibility.
- Vacuum: The negative pressure within the sealed can. Vacuum helps to maintain the can’s shape and prevents spoilage by inhibiting microbial growth.
Impact of Dimensions on Labeling and Design
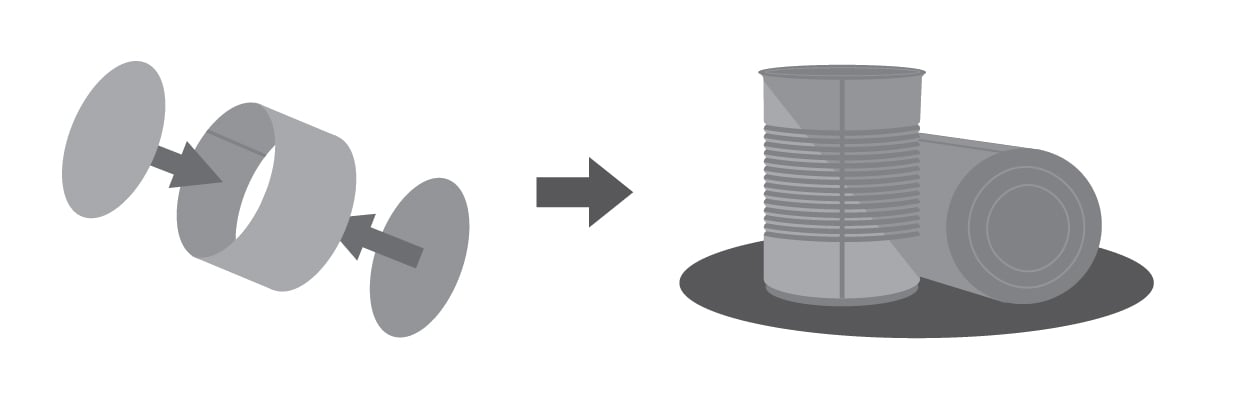
The dimensions of a food can are not just about containing the product; they significantly impact how that product is presented to consumers. From the size and shape of the label to the overall aesthetic design, can dimensions dictate the visual identity and branding potential of the product. Understanding this relationship is crucial for effective marketing and shelf appeal.
Label Size and Shape Influenced by Can Dimensions
The physical dimensions of a can directly determine the available surface area for labeling. The height and diameter of the can, along with any curvature, dictate the size and shape of the label that can be applied. This, in turn, affects the amount of information that can be displayed, the size of the graphics, and the overall visual impact.The label must wrap smoothly around the can without wrinkling or gaps, and it must fit within the can’s specified dimensions.
The label’s height is limited by the can’s height, minus a small allowance at the top and bottom for the can’s seams. The label’s circumference is determined by the can’s diameter.The shape of the can, whether cylindrical, rectangular, or another form, will also dictate the shape of the label. Cylindrical cans allow for wraparound labels, while rectangular cans might require labels on multiple faces.
Packaging Graphics Influenced by Can Dimensions
Can dimensions heavily influence the design of packaging graphics, affecting the visual hierarchy, branding elements, and overall aesthetic appeal. Designers must consider the available space, the curvature of the can, and the desired message when creating the graphics.The dimensions affect:
- Visual Hierarchy: Designers must prioritize information based on label size. Larger cans offer more space for complex designs and multiple elements.
- Branding Elements: The size and placement of logos, brand names, and taglines are all influenced by the available surface area. A taller can may allow for a more prominent logo.
- Image Resolution and Detail: The larger the label surface, the higher the image resolution that can be used without compromising clarity. Smaller cans may require simplified graphics.
- Color and Contrast: Dimensions can influence the choice of colors and contrast. Smaller labels may benefit from bold, simple designs, while larger labels can accommodate more complex color palettes and gradients.
For example, a tall, thin can of gourmet olives might feature a sophisticated design with a prominent logo and detailed imagery of olives, highlighting the premium nature of the product. In contrast, a shorter, wider can of soup might use bold colors and simple graphics to quickly communicate the product’s flavor and brand identity on a crowded shelf.
Visual Description of a Complementary Can Label
Consider a standard 307×409 can (3.07 inches diameter, 4.09 inches height) containing diced tomatoes. The label design should be optimized to visually complement these dimensions:The label is a wraparound design. The background color is a rich, deep red, evocative of ripe tomatoes.* Top Section: Occupies approximately 15% of the label’s height. It features the brand name in a clean, sans-serif font in a bright white color, ensuring high legibility.
Beneath the brand name is a smaller tagline, “Freshly Diced,” in a slightly more stylized font, also in white.* Central Section: Takes up roughly 60% of the label. A high-resolution, close-up photograph of freshly diced tomatoes is centered here. The tomatoes are arranged in a visually appealing way, showcasing their vibrant color and texture. The photograph is slightly blurred around the edges to create a sense of depth and focus.* Bottom Section: Accounts for the remaining 25% of the label.
It contains the product description “Diced Tomatoes,” the net weight information, and a small, stylized graphic of a tomato plant. The text is in a smaller, consistent font size and color (white) to ensure readability without overwhelming the central image. The graphic reinforces the freshness and natural ingredients of the product.The label’s design takes advantage of the can’s cylindrical shape, allowing for a seamless visual experience.
The colors and graphics are chosen to attract attention on the shelf and communicate the quality and freshness of the diced tomatoes. The layout prioritizes key information while creating an aesthetically pleasing and informative package.
Regulatory Considerations and Dimensions: Food Can Dimensions
Food can dimensions are not merely about aesthetics or convenience; they are intricately linked to food safety regulations globally. These regulations are in place to protect consumers from health risks associated with improperly packaged food products. Understanding how can dimensions align with these regulations is crucial for manufacturers to ensure product safety, compliance, and market access.
Food Safety Regulations and Can Dimensions
Food safety regulations directly influence can dimensions, primarily concerning the prevention of foodborne illnesses and the maintenance of product integrity. These regulations establish standards for can materials, sealing processes, and headspace to minimize the risk of spoilage, contamination, and chemical reactions that could compromise the food’s safety and quality.
Role of Dimensions in Product Fill and Headspace
The dimensions of a food can directly affect the product fill volume and the headspace—the empty space between the food and the can lid. Proper fill and headspace are critical for several reasons:
- Thermal Processing: Adequate headspace is essential during thermal processing (e.g., canning) to allow for expansion of the food during heating. Insufficient headspace can lead to can deformation or even bursting, while excessive headspace can compromise the vacuum seal and increase the risk of spoilage.
- Oxygen Control: Headspace helps control oxygen levels within the can. Excess oxygen can accelerate food spoilage and oxidation, affecting the product’s flavor, color, and nutritional value.
- Sealing Integrity: Precise dimensions ensure that the can lid and body can be properly sealed, creating a hermetic seal that prevents the entry of microorganisms and external contaminants.
Headspace is typically expressed as a percentage of the can’s total volume. For example, a standard can might require a headspace of 5-10% to allow for proper processing and maintain seal integrity.
Regulations Related to Can Dimensions in Different Regions
Different regions worldwide have specific regulations regarding can dimensions and food packaging. These regulations are often enforced by government agencies to ensure consumer safety and fair trade practices.
- United States: The Food and Drug Administration (FDA) regulates food packaging, including can dimensions, under the Federal Food, Drug, and Cosmetic Act. Regulations address can materials, sealing requirements, and headspace specifications. The FDA also provides guidance on good manufacturing practices (GMPs) for the food industry, which indirectly influence can dimensions by setting standards for processing and packaging.
- European Union: The European Food Safety Authority (EFSA) provides scientific advice on food safety, including packaging materials. EU regulations, such as those concerning food contact materials, set standards for can materials and their potential migration into food. Regulations on labeling also indirectly affect can dimensions, requiring manufacturers to accurately state the net weight or volume of the product.
- Canada: The Canadian Food Inspection Agency (CFIA) enforces regulations related to food safety and packaging. These regulations cover can materials, labeling requirements, and product fill. The CFIA often aligns with international standards and guidelines to facilitate trade.
- Codex Alimentarius: The Codex Alimentarius Commission, a joint program of the Food and Agriculture Organization of the United Nations (FAO) and the World Health Organization (WHO), develops international food standards, including those related to packaging. These standards serve as a reference for national regulations and promote harmonization of food safety practices globally.
For example, a canned vegetable product intended for sale in both the US and the EU must comply with both FDA and EFSA regulations. This often means carefully selecting can materials that meet both sets of requirements, ensuring appropriate headspace for thermal processing, and accurately labeling the product with the correct net weight or volume, which is directly dependent on can dimensions.
Non-compliance can result in product recalls, legal penalties, and damage to brand reputation.
Future Trends in Food Can Dimensions
The food can industry is constantly evolving, driven by consumer preferences, technological advancements, and a growing emphasis on sustainability. These factors are poised to significantly influence the dimensions and design of food cans in the coming years, leading to more efficient, eco-friendly, and consumer-centric packaging solutions.
Lightweighting and Sustainable Materials
The drive to reduce environmental impact is pushing manufacturers to explore lightweighting strategies and sustainable materials. This involves optimizing can dimensions to minimize material usage while maintaining structural integrity and food safety.
- Reduced Wall Thickness: Advancements in metal forming and coating technologies enable the production of cans with thinner walls, using less metal without compromising strength. This leads to a reduction in material consumption and transportation costs. For example, some manufacturers are already producing steel cans with wall thicknesses reduced by up to 15% compared to older designs.
- Alternative Materials: The use of alternative materials like aluminum and bioplastics, although currently facing challenges with cost and recyclability, could become more prevalent. Research is ongoing to develop biodegradable polymers suitable for food packaging, potentially leading to cans that are compostable or readily recyclable.
- Optimized Can Shapes: The shape of a can can significantly impact material usage. Cylindrical cans, the standard, may see modifications. Research into alternative shapes that can provide similar or better structural integrity with less material, such as cans with textured surfaces or slightly tapered designs, is increasing.
- Recycling Initiatives: Can dimensions will be increasingly designed with recyclability in mind. This includes simplifying can construction to make it easier to separate materials during recycling and reducing the use of labels and coatings that can contaminate the recycling stream.
Technological Advancements in Can Design and Manufacturing
Technological progress is transforming every aspect of the food can industry, from the design process to the manufacturing methods. These advancements are allowing for greater precision, customization, and efficiency in can production, which can ultimately impact dimensions.
- 3D Printing: Rapid prototyping using 3D printing allows for faster development and testing of new can designs. Manufacturers can quickly create and evaluate different shapes, sizes, and features before committing to large-scale production, accelerating the innovation cycle and facilitating optimization of dimensions.
- Finite Element Analysis (FEA): FEA software enables engineers to simulate the stresses and strains on a can under various conditions, such as internal pressure, stacking, and transportation. This allows for precise optimization of can dimensions and wall thickness, ensuring structural integrity while minimizing material usage.
- Advanced Manufacturing Techniques: New manufacturing techniques, such as hydroforming and laser welding, are improving the precision and efficiency of can production. Hydroforming allows for the creation of complex can shapes with tight tolerances, while laser welding provides stronger and more precise seams, reducing the risk of leakage and allowing for thinner materials.
- Smart Packaging: Integrating sensors and digital technologies into food cans is a growing trend. These “smart cans” could monitor factors like temperature and pressure, providing real-time information about the product’s condition. This could lead to changes in can dimensions to accommodate the electronics and sensors, while ensuring that the food product is safe and of high quality.
Evolving Dimensions to Meet Consumer Demands
Consumer preferences are driving changes in the food can industry, including the dimensions and designs of the packaging. These demands are leading to more convenient, portion-controlled, and visually appealing food cans.
- Portion Control: Single-serve and smaller can sizes are becoming increasingly popular, catering to consumers who are seeking convenience and portion control. This trend is particularly noticeable in the markets for soups, ready-to-eat meals, and pet food.
- Enhanced Aesthetics: The appearance of food cans is becoming increasingly important, with consumers expecting attractive and informative packaging. This is leading to the development of cans with improved printing capabilities, textured surfaces, and innovative shapes, all of which can impact the overall dimensions and design.
- Easy-Open Features: Consumers demand easy-open cans, which are accessible and user-friendly. This is driving innovation in can end designs, with features such as easy-peel lids and ring pulls. These features can influence the overall height and diameter of the can, as well as the design of the lid.
- Customization and Personalization: There is a growing demand for customized and personalized packaging, particularly in niche markets. This could involve cans with unique shapes, sizes, and labeling options. Technological advancements, such as digital printing, are making it easier to produce customized cans at scale.
Last Point
In conclusion, food can dimensions are a critical component in the food industry, influencing everything from production processes to consumer appeal. From understanding the impact of dimensional tolerances to navigating the evolving landscape of sustainability and consumer demands, the insights gained provide a comprehensive understanding of the vital role that dimensions play in shaping the future of food packaging. As technology advances and consumer preferences shift, the dimensions of food cans will continue to evolve, highlighting the need for ongoing innovation and a commitment to precision in the world of food packaging.