Tyson Foods Pottsville PA is more than just a food processing plant; it’s a significant economic engine and community presence. This exploration delves into the heart of this facility, uncovering its history, production processes, and the profound impact it has on the local landscape. From its humble beginnings to its current status as a major employer, we’ll examine the intricacies of its operations and its role in the Pottsville community.
Our journey will cover various aspects, including the products manufactured, employment opportunities, safety protocols, and environmental considerations. We’ll also investigate the company’s supply chain, labor relations, and recent developments shaping its future. This comprehensive overview provides a detailed understanding of Tyson Foods’ Pottsville location and its multifaceted contributions.
Overview of Tyson Foods Pottsville, PA
Tyson Foods’ facility in Pottsville, Pennsylvania, represents a significant component of the company’s broader processing network. The plant’s operations contribute substantially to the local economy and the overall food supply chain. This overview will delve into the facility’s history, its primary production focus, and the scale of its workforce.
History of the Pottsville Facility
The Pottsville, PA, Tyson Foods facility has a history rooted in the evolution of the poultry processing industry. While specific founding dates and initial ownership structures might vary across different sources, the facility has been a consistent presence in the community for many years. The plant has adapted to meet evolving consumer demands and industry standards over time, reflecting changes in processing technologies and food safety regulations.
The facility’s longevity highlights its importance in the local economic landscape and its ability to integrate with advancements in the food processing sector.
Primary Products Manufactured
The Pottsville plant specializes in the production of poultry products, catering to both retail and foodservice markets. The facility is primarily focused on processing chicken, transforming raw materials into a range of consumer-ready items.
Obtain recommendations related to everglades food web that can assist you today.
- Chicken Nuggets: A core product line includes chicken nuggets, a popular item for both children and adults. Production involves shaping, breading, and cooking chicken to meet consistent quality standards.
- Chicken Patties: The facility produces chicken patties, a versatile product used in sandwiches and other meal applications.
- Breaded Chicken: Breaded chicken products, such as tenders and fillets, are also a significant part of the production. These items undergo breading and cooking processes to achieve the desired texture and flavor profiles.
- Raw Chicken Products: In addition to cooked items, the plant likely processes and prepares raw chicken products, such as whole chickens, parts, and cuts, for distribution.
Approximate Number of Employees
The Pottsville Tyson Foods plant is a major employer in the region. The workforce size fluctuates based on production demands and seasonal factors. While exact figures are proprietary and subject to change, the plant typically employs a substantial number of workers. Estimates suggest that the facility employs several hundred people. This employment contributes significantly to the local economy.
The jobs at the plant range from skilled positions in processing and maintenance to roles in administration and logistics.
Operations and Processes
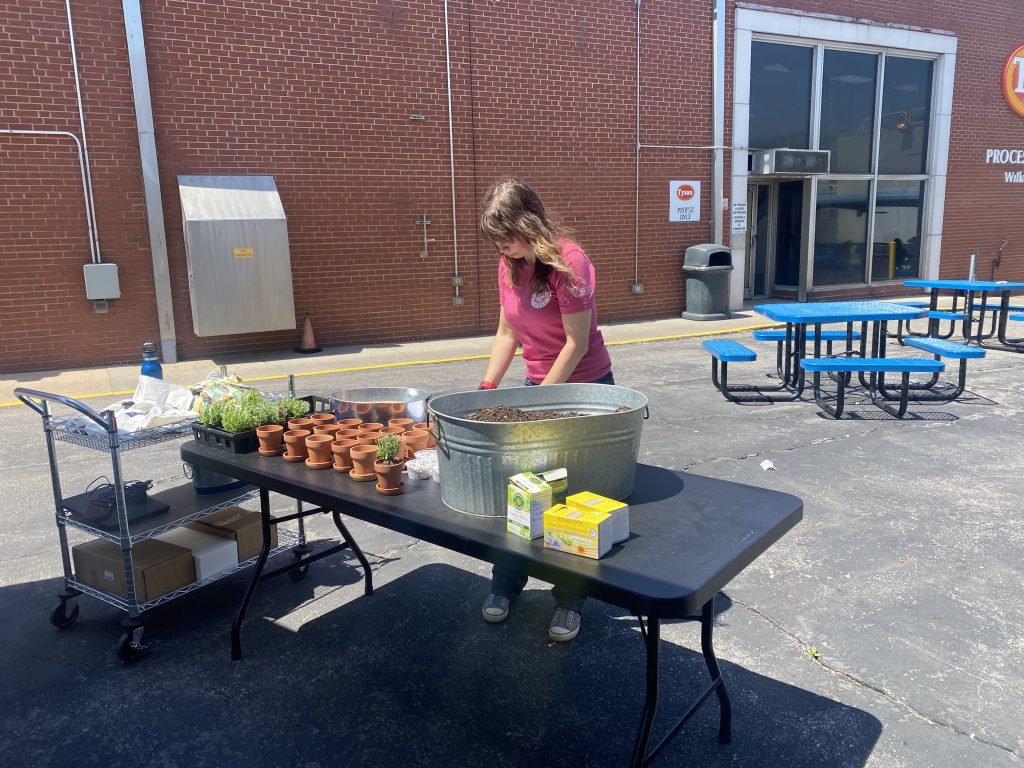
The Tyson Foods plant in Pottsville, Pennsylvania, is a significant operation focused on poultry processing. The facility’s efficiency and adherence to stringent standards are critical to its success. This section Artikels the key operational aspects, including the production process, quality control measures, and waste management practices employed at the Pottsville location.
Production Process
The production process at Tyson Foods Pottsville involves several stages, transforming raw poultry into a variety of finished products. This integrated process ensures quality control and efficient resource utilization.The typical production process at the Pottsville plant follows these key steps:
- Arrival and Inspection of Raw Materials: Live chickens arrive at the plant and undergo initial inspection. This includes checks for health and compliance with animal welfare standards. The birds are then weighed and sorted.
- Processing: The chickens are then processed, including stunning, slaughtering, defeathering, evisceration, and washing. This stage adheres to strict hygiene and safety protocols.
- Further Processing (Optional): Depending on the product, the poultry may undergo further processing, such as cutting, deboning, marinating, breading, or cooking. This step determines the final product type (e.g., chicken breasts, nuggets, or whole chickens).
- Packaging and Labeling: Processed poultry is packaged and labeled according to product specifications and regulatory requirements. Packaging helps to preserve freshness and maintain product integrity.
- Quality Control Checks: Throughout the production process, quality control checks are performed at various points to ensure product safety and adherence to quality standards.
- Storage and Distribution: Finished products are stored in refrigerated or frozen storage areas before being distributed to retailers and food service providers. Proper temperature control is essential for maintaining product quality and safety.
Quality Control Measures
Maintaining high quality and food safety is a paramount concern at the Tyson Foods Pottsville plant. A multi-faceted quality control system is implemented to ensure product integrity and consumer safety.The plant employs several quality control measures:
- Supplier Audits: Tyson Foods conducts audits of its suppliers to ensure that raw materials meet the required quality and safety standards. This includes verifying animal welfare practices and adherence to food safety regulations.
- In-Process Monitoring: Continuous monitoring occurs at various stages of production, including temperature control, equipment sanitation, and employee hygiene. This helps to identify and address potential issues early in the process.
- Laboratory Testing: The plant’s on-site laboratory conducts microbiological, chemical, and physical tests on raw materials, in-process products, and finished goods. These tests verify product safety and compliance with regulatory standards.
- HACCP Implementation: The Hazard Analysis and Critical Control Points (HACCP) system is implemented to identify and control potential hazards throughout the production process. This includes monitoring critical control points and implementing corrective actions when necessary.
- Employee Training: Employees receive comprehensive training on food safety, hygiene, and quality control procedures. This training helps to ensure that all employees understand their roles in maintaining product quality and safety.
- Traceability Systems: Tyson Foods utilizes traceability systems to track products from origin to consumer. This allows for quick identification and recall of products in the event of a safety concern.
Waste Management and Sustainability Initiatives
Tyson Foods Pottsville is committed to environmental sustainability and responsible waste management. The plant employs various methods to minimize its environmental impact and conserve resources.The waste management and sustainability initiatives include:
- Wastewater Treatment: The plant has a wastewater treatment system to treat water used in the production process before it is discharged. This system removes contaminants and ensures that the discharged water meets environmental regulations. An example would be the implementation of an advanced wastewater treatment system with anaerobic digestion to recover biogas.
- Rendering: Non-edible byproducts from poultry processing are sent to a rendering facility. These byproducts are processed into valuable products such as animal feed, pet food ingredients, and biofuels.
- Solid Waste Reduction: The plant implements programs to reduce solid waste generation, including recycling programs for paper, cardboard, plastic, and metal. Efforts are also made to reduce packaging materials.
- Energy Conservation: Tyson Foods invests in energy-efficient equipment and practices to reduce energy consumption. This includes using LED lighting, optimizing refrigeration systems, and implementing energy management programs.
- Water Conservation: Water conservation measures are implemented throughout the plant, such as using water-efficient equipment and implementing water reuse systems where possible.
- Composting: Organic waste, such as food scraps and yard waste, is composted to create a nutrient-rich soil amendment.
Impact on the Local Community: Tyson Foods Pottsville Pa
Tyson Foods’ presence in Pottsville, PA, has significantly shaped the local community, influencing its economic landscape, social programs, and overall development. Understanding this impact requires examining the company’s contributions, community engagement, and the challenges and opportunities it presents.
Economic Impact of Tyson Foods on Pottsville, PA
The economic impact of Tyson Foods in Pottsville is multifaceted, primarily driven by job creation and local spending. This has a ripple effect throughout the community, influencing various sectors.Tyson Foods is a significant employer in the Pottsville area, providing a substantial number of jobs. This employment base supports local families and contributes to the tax base of the community. The presence of a large employer like Tyson Foods can also attract related businesses, such as transportation and logistics companies, further boosting employment opportunities.Local spending is another key component of Tyson Foods’ economic impact.
The company’s operations necessitate the purchase of goods and services from local vendors, supporting other businesses in the area. Employees of Tyson Foods also contribute to local spending, patronizing restaurants, stores, and other establishments, thus stimulating the local economy.
Community Involvement Programs Compared
Tyson Foods, like other large employers in the Pottsville area, engages in community involvement programs. Comparing these initiatives reveals the varying approaches to corporate social responsibility.Tyson Foods often supports local initiatives related to food security, education, and community development. These efforts may include donations to food banks, sponsorships of school programs, and participation in local events.Other large employers in the area, such as healthcare providers and educational institutions, also have community involvement programs.
These may focus on healthcare access, scholarships, and community outreach activities. Comparing these programs provides a broader understanding of the corporate social responsibility landscape in Pottsville.For instance, a healthcare provider might offer free health screenings and wellness programs, while an educational institution might sponsor after-school programs or provide resources for local schools. Tyson Foods’ community involvement programs can be assessed against these other initiatives to gauge their scope and impact.
Challenges and Opportunities Presented by Tyson Foods
The presence of Tyson Foods in Pottsville presents both challenges and opportunities for the community. Navigating these aspects is crucial for the sustainable development of the area.One of the main challenges is managing the environmental impact of the company’s operations. Large-scale food processing facilities can have environmental consequences, such as wastewater discharge and air emissions. Addressing these concerns requires implementing sustainable practices and adhering to environmental regulations.Another challenge involves managing the impact on local infrastructure.
Increased traffic, demand for utilities, and other infrastructure needs are associated with a large employer like Tyson Foods. Effective planning and investment in infrastructure are crucial to mitigate these impacts.The opportunities presented by Tyson Foods include economic growth, job creation, and community development initiatives. The company’s presence can also attract investment and stimulate innovation in the area.Furthermore, Tyson Foods can collaborate with local organizations to address community needs and promote sustainable development.
For example, partnering with local educational institutions to offer training programs can improve the skills of the local workforce.
Employment and Career Opportunities
Tyson Foods in Pottsville, PA, offers a range of employment and career advancement opportunities within its processing facility. The company provides various roles, from entry-level positions to specialized roles, fostering a work environment that encourages employee growth and development. This section will Artikel the job types available, the skills required, training programs offered, and potential career paths for employees.
Available Job Types and Skill Requirements
The Tyson Foods facility in Pottsville offers a diverse range of positions, each with specific skill requirements. These roles contribute to the overall production and operational efficiency of the plant.
- Production Workers: These are entry-level positions involving tasks such as processing, packaging, and inspecting food products.
- Skills: Ability to follow instructions, attention to detail, ability to work in a fast-paced environment, and physical stamina.
- Maintenance Technicians: Responsible for maintaining and repairing machinery and equipment.
- Skills: Mechanical aptitude, troubleshooting skills, knowledge of electrical and pneumatic systems, and ability to read technical manuals. Experience with Computerized Maintenance Management Systems (CMMS) is often beneficial.
- Quality Assurance Specialists: These professionals ensure that products meet quality and safety standards.
- Skills: Knowledge of food safety regulations, analytical skills, attention to detail, and ability to perform quality control tests. A background in food science or a related field is often preferred.
- Supervisors and Team Leaders: These positions involve overseeing production teams, managing workflows, and ensuring that production targets are met.
- Skills: Leadership abilities, communication skills, problem-solving skills, ability to motivate and manage a team, and knowledge of production processes.
- Logistics and Warehouse Staff: These employees manage the flow of materials and finished goods.
- Skills: Organizational skills, inventory management, experience with warehouse management systems, and the ability to operate material handling equipment (e.g., forklifts).
Training and Development Programs
Tyson Foods invests in its employees through various training and development programs designed to enhance skills and support career advancement. These programs aim to improve employee performance, ensure adherence to safety standards, and provide opportunities for professional growth.
- On-the-Job Training: New employees receive hands-on training to learn the specific tasks associated with their roles. This training is often provided by experienced employees or supervisors.
- Safety Training: Comprehensive safety training is provided to all employees to ensure a safe working environment and compliance with safety regulations. This includes training on hazard recognition, personal protective equipment (PPE), and emergency procedures.
- Skills-Based Training: Training programs are offered to enhance specific skills, such as equipment maintenance, quality control, and supervisory skills. These programs may involve classroom instruction, online modules, and practical exercises.
- Leadership Development Programs: Tyson Foods provides leadership development programs for employees who aspire to management or supervisory roles. These programs focus on developing leadership skills, communication skills, and team management techniques.
- Tuition Reimbursement: Tyson Foods may offer tuition reimbursement to employees who pursue further education or training related to their jobs or career goals. This benefit encourages employees to enhance their skills and advance their careers.
Sample Career Path for an Entry-Level Position, Tyson foods pottsville pa
An entry-level position at the Tyson Foods Pottsville plant can serve as a stepping stone to a rewarding career. Here is a sample career path for a Production Worker:
Stage 1: Entry-Level Production Worker
This is the starting point, involving tasks such as processing and packaging products. Employees learn the basics of the production process and company procedures.
Stage 2: Experienced Production Worker/Team Lead (after 1-2 years)
After gaining experience and demonstrating proficiency, employees may be promoted to a more senior production role or a team lead position.
This may involve additional responsibilities, such as training new employees or overseeing a small team.
Stage 3: Production Supervisor (after 3-5 years)
With further experience and leadership skills, employees can advance to a Production Supervisor role. This position involves managing a team, ensuring production targets are met, and maintaining quality standards.
Stage 4: Production Manager/Plant Management (5+ years)
Experienced supervisors with strong leadership skills and a deep understanding of the production process can advance to Production Manager or other plant management roles.
These positions involve overall responsibility for production operations and may include strategic planning and resource management.
This career path is illustrative, and individual advancement will depend on performance, skills development, and the availability of opportunities within the organization. Opportunities for advancement may also involve lateral moves to other departments, such as Quality Assurance or Maintenance, depending on an employee’s skills and interests.
The company’s commitment to training and development provides employees with the tools they need to advance along these career paths.
Safety and Regulations
The safety of employees and the surrounding community is a paramount concern at the Tyson Foods plant in Pottsville, PA. This commitment is reflected in the comprehensive safety protocols, rigorous regulatory compliance, and ongoing training programs implemented throughout the facility. Maintaining a safe working environment is not only a legal requirement but also a fundamental value that underpins all operational activities.
Safety Protocols and Procedures
Tyson Foods Pottsville has established a robust safety management system designed to mitigate risks and prevent workplace incidents. This system incorporates a multi-faceted approach, including proactive hazard identification, comprehensive training, and continuous improvement initiatives.
- Hazard Identification and Control: Regular safety audits, inspections, and near-miss reporting systems are in place to identify potential hazards. These hazards are then addressed through engineering controls (e.g., equipment modifications), administrative controls (e.g., revised work procedures), and personal protective equipment (PPE).
- Employee Training: All employees receive thorough training on safety procedures relevant to their specific job tasks. This training includes hazard communication, lockout/tagout procedures, forklift operation, and emergency response protocols. Refresher training is provided regularly to reinforce safe work practices and address any changes in procedures or equipment.
- Personal Protective Equipment (PPE): The use of appropriate PPE is mandatory throughout the plant. This includes, but is not limited to, safety glasses, hearing protection, gloves, and slip-resistant footwear. PPE requirements are specific to each work area and are strictly enforced.
- Emergency Preparedness: The plant has comprehensive emergency response plans in place, including fire drills, evacuation procedures, and first aid protocols. Employees are trained in emergency procedures, and emergency equipment, such as fire extinguishers and first aid kits, are readily available and regularly inspected.
- Safety Committees: Employee involvement in safety is encouraged through the formation of safety committees. These committees are responsible for conducting safety inspections, investigating incidents, and recommending improvements to safety programs.
Regulatory Environment and Compliance
The Tyson Foods Pottsville plant operates within a heavily regulated environment, adhering to federal, state, and local regulations. Compliance with these regulations is essential for maintaining a safe and compliant operation.
- Occupational Safety and Health Administration (OSHA): The plant is subject to OSHA regulations, which mandate safe working conditions. OSHA conducts regular inspections to ensure compliance with safety standards. Non-compliance can result in citations and penalties.
- Pennsylvania Department of Environmental Protection (DEP): The DEP oversees environmental regulations related to air and water quality, waste management, and other environmental aspects of the plant’s operations. Compliance with DEP regulations is crucial for minimizing environmental impact.
- Food Safety and Inspection Service (FSIS): As a meat processing facility, the plant is subject to FSIS inspection and oversight to ensure the safety and wholesomeness of its products. FSIS inspectors regularly monitor processing procedures and sanitation practices.
- Inspections and Audits: The plant undergoes regular inspections by OSHA, DEP, and FSIS, as well as internal audits to ensure compliance with all applicable regulations and company policies.
- Recordkeeping: Comprehensive records are maintained to document safety training, inspections, incidents, and corrective actions. These records are essential for demonstrating compliance and identifying areas for improvement.
Common Safety Violations and Corrective Actions
The following table Artikels some common safety violations that might occur in a food processing facility like the Tyson Foods plant in Pottsville, along with the typical corrective actions taken to address them.
Safety Violation | Description | Potential Hazards | Corrective Action |
---|---|---|---|
Lack of Machine Guarding | Failure to adequately guard moving parts of machinery, such as belts, gears, and blades. | Entrapment, amputation, lacerations. | Install or improve machine guarding; provide employee training on machine safety; conduct regular inspections of machine guarding. |
Improper Lockout/Tagout Procedures | Failure to properly de-energize and lock out equipment during maintenance or servicing. | Electrocution, crushing, burns. | Implement and enforce lockout/tagout procedures; provide employee training on lockout/tagout; conduct regular audits of lockout/tagout practices. |
Slip, Trip, and Fall Hazards | Presence of wet floors, cluttered walkways, or uneven surfaces. | Slips, trips, and falls leading to injuries. | Implement a housekeeping program; provide slip-resistant footwear; repair or replace damaged flooring; install warning signs. |
Lack of Personal Protective Equipment (PPE) | Failure to wear required PPE, such as safety glasses, gloves, or hearing protection. | Eye injuries, hand injuries, hearing loss. | Enforce PPE requirements; provide appropriate PPE; provide employee training on PPE usage; conduct regular inspections to ensure PPE is worn. |
Products and Distribution
The Pottsville, PA, Tyson Foods facility plays a crucial role in the company’s supply chain, producing a variety of food products and ensuring their efficient distribution to consumers. This section details the specific products manufactured at the plant, the distribution network utilized, and the packaging and labeling processes employed to maintain product quality and brand integrity.
Specific Brands and Product Lines
The Pottsville plant focuses on producing a selection of Tyson Foods’ well-known brands and product lines. The facility’s output primarily supports the company’s retail and foodservice segments.
- Chicken Products: The plant is a significant producer of various chicken products. These include:
- Breaded chicken patties.
- Chicken nuggets.
- Fully cooked chicken strips.
- Brand Affiliations: Products manufactured in Pottsville often bear the Tyson brand name, as well as other affiliated brands.
Distribution Network
Tyson Foods employs a sophisticated distribution network to deliver its products from the Pottsville facility to various destinations, ensuring product freshness and timely delivery.
- Transportation Methods: The distribution network utilizes a multi-modal approach:
- Trucking: A significant portion of the products are transported via refrigerated trucks, which maintain the required temperature to preserve the quality of the food products.
- Rail: Depending on the destination and volume, rail transport may also be used for long-distance shipments.
- Distribution Centers: Products are often transported to regional distribution centers. From these centers, the products are further distributed to retailers, restaurants, and other foodservice establishments.
- Supply Chain Management: Tyson Foods utilizes advanced supply chain management systems to track products from the plant to the end consumer, optimizing routes and minimizing delivery times.
Packaging and Labeling Processes
The packaging and labeling processes at the Pottsville facility are designed to protect the product, provide essential information to consumers, and adhere to regulatory standards.
- Packaging Materials: The facility uses a variety of packaging materials. These include:
- Plastic films.
- Cardboard boxes.
- Insulated containers for maintaining product temperature.
- Labeling Information: Product labels provide essential information. This includes:
- Product name and description.
- Ingredients list.
- Nutritional information.
- Expiration dates.
- Handling instructions.
- Brand name and logo.
- Establishment number.
- Quality Control: Rigorous quality control measures are implemented throughout the packaging and labeling processes to ensure accuracy and compliance with all applicable regulations.
Recent Developments and News
The Tyson Foods plant in Pottsville, PA, like any large-scale operation, is subject to ongoing developments and news cycles that impact its operations and the surrounding community. Staying informed about these changes is crucial for understanding the plant’s evolution and its role in the local economy.
Facility Upgrades and Investments
Tyson Foods regularly invests in its facilities to improve efficiency, safety, and product quality. These investments can range from minor equipment upgrades to major expansions. Recent examples include:
- Automation Initiatives: The Pottsville plant has seen increased automation in recent years, particularly in areas like packaging and processing. This involves the implementation of robotic systems and automated guided vehicles (AGVs) to streamline operations and reduce manual labor. The shift toward automation is driven by the need to enhance productivity, minimize human error, and address labor shortages.
- Infrastructure Improvements: Upgrades to the plant’s infrastructure, such as the refrigeration systems and wastewater treatment facilities, are ongoing. These improvements are essential for maintaining food safety standards, reducing environmental impact, and ensuring the plant’s long-term operational viability.
- Employee Training Programs: Tyson Foods continues to invest in employee training programs to equip workers with the skills needed to operate and maintain the advanced equipment. These programs focus on areas such as safety protocols, food handling procedures, and technical expertise.
Impact of Recent Events
External events, such as changes in market demand, supply chain disruptions, and economic fluctuations, can significantly affect the Tyson Foods plant in Pottsville. The following points illustrate how these events can play out:
- Supply Chain Disruptions: Events like the COVID-19 pandemic and other unforeseen circumstances can disrupt the supply of raw materials, such as livestock. These disruptions can lead to production slowdowns, increased costs, and adjustments to product offerings. The plant must adapt to these challenges by diversifying its supply chain, building up inventory, and implementing contingency plans.
- Changes in Consumer Demand: Shifts in consumer preferences, such as a growing demand for plant-based protein alternatives, can influence the plant’s product mix and production volumes. Tyson Foods may respond by investing in the production of alternative protein products or adjusting its existing product lines to align with evolving consumer tastes.
- Economic Conditions: Economic downturns can affect consumer spending and demand for meat products. The Pottsville plant must navigate these challenges by managing costs, optimizing production efficiency, and exploring strategies to maintain market share during periods of economic uncertainty.
Environmental Considerations
The Tyson Foods plant in Pottsville, PA, like any large-scale food processing facility, operates with a significant environmental footprint. Understanding and mitigating this impact is crucial for sustainable operations and responsible corporate citizenship. This section will delve into the plant’s environmental effects, specifically focusing on emissions, water usage, and the company’s commitment to reducing its environmental impact at the Pottsville location.
Emissions and Air Quality
Air quality is a key environmental concern associated with food processing. The Pottsville plant’s operations generate emissions that need careful management.Emissions primarily stem from:
- Combustion of fuels for energy production, including natural gas used in boilers and other equipment.
- Processes like rendering, which can release volatile organic compounds (VOCs) and other airborne pollutants if not properly controlled.
- Potential for odors associated with certain processes.
To address these challenges, Tyson Foods implements various strategies:
- Installing and maintaining air pollution control equipment, such as scrubbers and filters, to reduce emissions of particulate matter, VOCs, and other pollutants.
- Monitoring air quality through regular testing and compliance with environmental regulations set by the Pennsylvania Department of Environmental Protection (DEP) and the U.S. Environmental Protection Agency (EPA).
- Employing best practices in operations and maintenance to minimize emissions from various processes.
Water Usage and Wastewater Treatment
Water is essential for food processing, and the Pottsville plant requires a significant amount of water for various operations, including cleaning, sanitation, and ingredient processing.Water usage impacts include:
- High water consumption, potentially placing a strain on local water resources.
- Generation of wastewater containing organic matter, fats, oils, and grease (FOG), and other contaminants.
Tyson Foods addresses water-related concerns through:
- Implementing water conservation measures, such as reusing water in certain processes and optimizing cleaning procedures.
- Treating wastewater on-site to remove contaminants before discharge. The treatment process typically involves physical, chemical, and biological treatments.
- Complying with stringent discharge permits issued by the DEP to ensure the quality of treated wastewater discharged into the local waterways.
Sustainability Initiatives: Visual Representation
The following is a descriptive representation of Tyson Foods Pottsville plant’s sustainability initiatives.
The illustration is a circular diagram, symbolizing the continuous improvement cycle of sustainability. At the center is a stylized depiction of the Tyson Foods Pottsville plant, represented by a factory silhouette. Surrounding the plant are interconnected segments illustrating key sustainability initiatives.
- Water Conservation: Depicted as a water droplet with arrows, showing the reduction in water usage through reuse and optimization.
- Waste Reduction: Represented by a recycling symbol, highlighting efforts to minimize waste generation, promote recycling, and divert waste from landfills.
- Energy Efficiency: Shown as a lightbulb with a green leaf, indicating the use of energy-efficient technologies, such as high-efficiency lighting and equipment.
- Renewable Energy: Depicted as a solar panel and a wind turbine, representing the exploration of renewable energy sources like solar and wind power.
- Emission Reduction: Shown as a chimney with a reduced amount of smoke, emphasizing the use of emission control technologies and practices to reduce air pollution.
- Community Engagement: Represented by a handshake, highlighting the company’s involvement in local environmental projects and community initiatives.
Each segment is connected to the central plant image, indicating the integrated approach to sustainability. The diagram’s overall design emphasizes the company’s commitment to environmental stewardship and its continuous efforts to reduce its environmental footprint.
Labor Relations and Unionization
The labor relations landscape at Tyson Foods’ Pottsville, PA, plant is a critical aspect of its operational environment. Understanding the dynamics between the company, its employees, and any representing unions provides insight into the working conditions, employee benefits, and overall operational efficiency. The following sections will explore the specifics of labor relations at the Pottsville facility.
Union Representation
The presence of a union at the Tyson Foods Pottsville plant is a key factor in shaping labor relations. Unions typically act as a collective bargaining agent, negotiating with the company on behalf of its members regarding wages, benefits, and working conditions. This representation aims to ensure fair treatment and protect employee rights. The specific union representing employees at the Pottsville plant, along with its history and scope of representation, should be identified.
Comparative Analysis of Benefits and Working Conditions
A comparison of benefits and working conditions at the Pottsville plant with those at similar Tyson Foods facilities, or other comparable food processing plants, offers valuable insights. Such a comparison helps in assessing the competitive advantages and disadvantages of working at the Pottsville location. This analysis often includes aspects such as compensation, healthcare coverage, retirement plans, and workplace safety measures.
- Wages: Compare the average hourly wages for similar roles at the Pottsville plant versus other facilities. This comparison may highlight differences in pay scales due to factors such as union contracts, local cost of living, and plant location. For example, a plant located in a region with a higher cost of living might offer higher wages to compensate.
- Benefits: Analyze the health insurance plans, retirement contributions (such as 401(k) matching), and paid time off (vacation, sick leave) offered at the Pottsville plant compared to other locations. Differences in benefit packages can impact employee satisfaction and retention rates.
- Working Conditions: Evaluate the safety measures, equipment, and overall work environment at the Pottsville plant. This includes examining the frequency of workplace injuries, the availability of protective equipment, and the implementation of safety protocols. Compare these aspects with those at other facilities, considering factors like the age of the equipment, the design of the production lines, and the presence of automated systems.
- Union Contract Provisions: If a union is present, review the specific provisions of the union contract at the Pottsville plant. These provisions might include clauses related to seniority, grievance procedures, and dispute resolution mechanisms. Compare these with similar provisions in contracts at other unionized plants to assess the level of employee protections and benefits.
- Employee Turnover and Retention: Examine the employee turnover rates at the Pottsville plant compared to other Tyson Foods facilities. High turnover rates could indicate issues with wages, benefits, or working conditions. Conversely, lower turnover rates might suggest that the plant offers a more attractive employment environment.
Supply Chain and Raw Materials
The efficiency and sustainability of Tyson Foods Pottsville’s operations are heavily reliant on a robust and well-managed supply chain. This encompasses the sourcing, transportation, and management of raw materials, which directly impacts the quality of the products and the company’s overall environmental footprint. A well-structured supply chain also ensures that the plant can meet production demands consistently.
Raw Material Supply Chain Overview
The supply chain for raw materials at the Tyson Foods Pottsville plant is a complex network involving numerous suppliers, transportation methods, and processing stages. The primary raw materials include poultry (primarily chicken), various seasonings and ingredients, and packaging materials. The journey of these materials from their origin to the production line is carefully managed to ensure freshness, quality, and adherence to food safety standards.
This intricate process is critical for maintaining product integrity and consumer trust.
Sourcing Practices for Key Ingredients and Materials
Tyson Foods utilizes a multifaceted approach to sourcing its key ingredients and materials. This includes establishing long-term relationships with suppliers, implementing rigorous quality control measures, and promoting sustainable agricultural practices. The company places a strong emphasis on traceability, allowing them to track materials from the farm to the processing plant. This transparency is crucial for addressing potential food safety concerns and ensuring compliance with regulatory requirements.
The process of sourcing raw materials can be Artikeld as follows:
- Supplier Selection: Tyson Foods identifies and evaluates potential suppliers based on several criteria. These include quality standards, food safety certifications (e.g., Safe Quality Food – SQF), ethical sourcing practices, and the ability to meet volume requirements.
- Contract Negotiation: Once a supplier is selected, Tyson Foods negotiates contracts that specify pricing, delivery schedules, and quality specifications. These contracts often include clauses related to sustainability and animal welfare.
- Material Procurement: Upon agreement, Tyson Foods initiates the procurement process, which involves placing orders for the required raw materials. This is typically managed through a sophisticated inventory management system.
- Transportation: The raw materials are then transported from the supplier to the Pottsville plant. Tyson Foods utilizes a variety of transportation methods, including trucks, rail, and refrigerated containers, depending on the material and distance. The company strives to optimize transportation routes and minimize its carbon footprint.
- Receiving and Inspection: Upon arrival at the plant, all raw materials undergo rigorous inspection to verify their quality, freshness, and compliance with food safety standards. This includes visual inspections, laboratory testing, and adherence to established protocols.
- Storage and Handling: Once inspected, the raw materials are stored under appropriate conditions to maintain their quality and prevent spoilage. This may involve refrigeration, freezing, or other preservation methods. The plant adheres to strict protocols for handling and storage to minimize the risk of contamination.
- Production and Processing: The raw materials are then integrated into the production process, where they are processed and transformed into finished products. Tyson Foods follows stringent food safety guidelines throughout the entire process.
Summary
In conclusion, Tyson Foods Pottsville PA stands as a testament to the complex interplay between industry, community, and sustainability. The facility’s success is intertwined with the economic well-being of Pottsville, creating both opportunities and challenges. As we’ve seen, the company’s commitment to safety, environmental responsibility, and employee development are essential for its continued success and its positive influence on the region.