Tyson Foods Rome GA, a significant player in the food industry, provides a compelling focus for exploration. This overview delves into the multifaceted operations of Tyson Foods in Rome, Georgia, offering insights into its history, product offerings, and substantial impact on the local community. We will uncover the intricacies of its production processes, examine its commitment to food safety and environmental sustainability, and explore the challenges and opportunities that shape its future.
From its humble beginnings to its current standing, the Tyson Foods facility in Rome, GA, has evolved, adapting to changing market demands and technological advancements. This examination will encompass the facility’s size, the types of food products manufactured, and the significant role it plays in providing employment and contributing to the economic vitality of the region. Furthermore, we’ll explore the company’s values, its commitment to sustainability, and its vision for the future within the dynamic food industry.
Tyson Foods Rome, GA Overview
Tyson Foods’ presence in Rome, Georgia, represents a significant component of the company’s vast operations within the poultry industry. This overview aims to provide a comprehensive understanding of the facility’s activities, its historical development, and its current scale of operations. The information provided is based on publicly available data and aims to present an accurate picture of Tyson Foods’ involvement in the Rome, GA, community.
Primary Activities and Products
The Tyson Foods facility in Rome, Georgia, is primarily involved in the processing of poultry. This includes various stages of production, from receiving live chickens to producing finished products for distribution. The facility focuses on producing a range of poultry products that are supplied to retail and food service customers.
- Processing: The core function of the Rome facility involves the processing of chickens, which includes slaughtering, evisceration, and cutting.
- Product Line: The products manufactured at the Rome facility typically include fresh and frozen chicken parts, such as breasts, thighs, and wings.
- Distribution: Processed products are then prepared for distribution through various channels, including grocery stores and restaurants.
History and Evolution
The history of Tyson Foods in Rome, GA, reflects the broader trends in the poultry industry’s growth and consolidation. The facility’s development has been shaped by factors such as market demand, technological advancements, and the strategic decisions of the company.
- Initial Establishment: The exact date of the facility’s initial establishment is a key factor in understanding its origins. However, the precise date may be difficult to pinpoint without specific archival research.
- Expansion and Upgrades: Over the years, the Rome facility has likely undergone expansions and upgrades to increase production capacity and improve efficiency. This would have involved investments in new equipment and technologies.
- Impact of Acquisitions: Tyson Foods has grown significantly through acquisitions. Understanding how acquisitions influenced the Rome facility’s operations and product lines provides a more comprehensive view of its evolution.
Facility Size and Employment
The size of the Rome, GA, facility is a key indicator of its operational capacity and economic impact on the local community. Data regarding square footage and employee count provides a tangible measure of the facility’s scale. It’s important to remember that these numbers are dynamic and can fluctuate based on market conditions and operational needs.
- Square Footage: The facility’s square footage is a measure of its physical size. The exact figures may vary based on the specific data sources.
- Employee Count: The number of employees at the Rome facility represents its impact on local employment. The employee count is subject to changes due to factors such as automation and market demands.
- Economic Impact: The size of the facility, combined with its employment figures, directly influences the local economy. It provides jobs and contributes to tax revenues.
Products and Services
The Tyson Foods facility in Rome, GA, is a significant contributor to the company’s diverse product portfolio, specializing in the processing and manufacturing of various protein-based food items. The plant’s operations focus on meeting the demands of both retail and foodservice markets, ensuring a consistent supply of high-quality products. The facility’s commitment to efficiency and quality control allows it to deliver a wide range of food items to consumers and businesses.
Specific Food Product Manufacturing
The Rome, GA, facility primarily focuses on the production of fully cooked chicken products. This includes a variety of formats designed to cater to different consumer preferences and market needs. The plant’s processes are optimized to ensure food safety and maintain product quality throughout the production cycle.
- Fully Cooked Chicken: The facility manufactures a range of fully cooked chicken products, including chicken strips, nuggets, patties, and other formed chicken products. These products are designed for convenience and ease of preparation, targeting busy consumers and foodservice operations.
- Portion-Controlled Products: Tyson Foods in Rome, GA, also produces portion-controlled chicken items, which are often utilized in school lunch programs, healthcare facilities, and other settings where precise serving sizes are essential. These products help in managing costs and ensuring dietary compliance.
Unique or Specialized Products
While the Rome, GA, plant primarily focuses on core chicken product lines, it may also produce specialized items that cater to specific market demands. These specialized items often reflect current trends in the food industry, such as those focusing on health and convenience. The plant’s flexibility allows it to adapt to changing consumer preferences.
- Value-Added Chicken Products: The facility may produce value-added chicken products that incorporate different flavor profiles or coatings. These products may include breaded or marinated chicken items, designed to offer consumers a wider range of culinary options.
- Customized Products: Depending on customer contracts, the Rome, GA, plant might also offer customized product development, producing items that are tailored to specific foodservice or retail requirements. This includes products designed for private label brands or specific menu applications.
Product Line Comparison
The following table provides a comparison of some of the product lines manufactured at the Tyson Foods facility in Rome, GA, including their primary ingredients and target markets. This comparison highlights the plant’s diverse production capabilities.
Product Line | Primary Ingredients | Target Market | Key Features |
---|---|---|---|
Chicken Strips | Chicken breast meat, seasonings, breading (flour, spices) | Retail consumers, foodservice (restaurants, cafeterias) | Convenient, pre-cooked, versatile for various dishes |
Chicken Nuggets | Ground chicken, seasonings, breading (flour, spices) | Families, quick-service restaurants (QSRs) | Kid-friendly, easy to prepare, often served with dipping sauces |
Chicken Patties | Ground chicken, seasonings, binders, breading | Retail consumers, foodservice (restaurants, schools) | Used in sandwiches and entrees, standardized portion sizes |
Portion-Controlled Chicken | Chicken breast or thigh meat, seasonings | Schools, healthcare facilities, institutional food service | Precise serving sizes, often low-sodium and tailored to dietary needs |
Employment and Community Impact
Tyson Foods’ presence in Rome, GA, extends far beyond its operational footprint, significantly shaping the economic and social fabric of the community. The company’s investment translates into tangible benefits, fostering job creation, supporting local businesses, and contributing to various community initiatives. This section explores the multifaceted impact of Tyson Foods on Rome, GA.
Economic Impact of Tyson Foods, Tyson foods rome ga
The economic influence of Tyson Foods in Rome, GA, is substantial, primarily stemming from its role as a major employer and its contribution to local spending. This impact is multifaceted, touching various sectors within the local economy.Tyson Foods’ presence has created a significant number of jobs in the Rome area. These jobs range from entry-level positions in processing and production to skilled roles in maintenance, management, and administration.
The payroll associated with these positions represents a substantial influx of income into the local economy, boosting consumer spending and supporting local businesses. The increased demand for goods and services from employees, coupled with Tyson Foods’ own procurement needs, benefits a wide array of local vendors, including suppliers of raw materials, transportation services, and maintenance providers. This creates a multiplier effect, where the initial investment and employment generate further economic activity throughout the community.
For instance, the establishment of a large manufacturing facility often leads to the development of supporting businesses, such as logistics companies and food service providers, which in turn create additional employment opportunities and contribute to local tax revenues.
Types of Jobs and Skills Required
The Rome, GA, facility offers a diverse range of employment opportunities, each requiring specific skill sets. Understanding these roles provides insight into the employment landscape at Tyson Foods.The available job types at the Tyson Foods Rome, GA, facility encompass several categories:
- Production and Processing: These roles involve the direct handling and processing of poultry products. Positions include line workers, packaging specialists, and quality control personnel. Skills required include the ability to work in a fast-paced environment, attention to detail, and the ability to follow safety protocols. Physical stamina is often a requirement.
- Maintenance and Engineering: Maintaining the operational efficiency of the facility necessitates skilled maintenance personnel. This category includes electricians, mechanics, refrigeration technicians, and engineers. Required skills involve technical expertise, problem-solving abilities, and the ability to diagnose and repair equipment.
- Management and Administration: These positions oversee various aspects of the facility’s operations, from human resources and finance to logistics and production management. Skills needed encompass leadership, communication, organizational abilities, and proficiency in relevant software and administrative processes.
- Transportation and Logistics: Managing the movement of raw materials and finished products is crucial. Roles include truck drivers, warehouse staff, and logistics coordinators. Skills required include safe driving practices, knowledge of transportation regulations, and the ability to manage inventory and distribution schedules.
Community Outreach Programs and Initiatives
Tyson Foods actively engages in community outreach programs and initiatives, demonstrating a commitment to social responsibility and contributing to the well-being of Rome, GA. These programs reflect a dedication to supporting local causes and fostering positive relationships with the community.Tyson Foods supports a variety of community initiatives, including:
- Food Donations: Tyson Foods regularly donates food products to local food banks and charitable organizations, addressing food insecurity in the community. These donations provide essential resources to families and individuals in need.
- Educational Programs: The company often supports educational initiatives, such as scholarships, STEM programs, and partnerships with local schools. These programs aim to enhance educational opportunities for students and contribute to workforce development.
- Environmental Sustainability: Tyson Foods may implement environmental sustainability programs, such as waste reduction initiatives and partnerships with local organizations to promote environmental conservation. This could include efforts to reduce water consumption, manage waste effectively, and minimize the facility’s environmental footprint.
- Employee Volunteerism: Tyson Foods encourages employee volunteerism, providing opportunities for employees to participate in community service projects. This fosters a culture of giving back and strengthens the company’s connection with the community.
- Support for Local Events: The company may sponsor or participate in local events, such as festivals, fairs, and charity drives. This involvement helps raise awareness for local causes and demonstrates Tyson Foods’ commitment to supporting the community’s social and cultural life.
Production Processes and Technology
The Tyson Foods facility in Rome, GA, employs sophisticated production processes and cutting-edge technology to efficiently transform raw materials into a variety of high-quality food products. These processes are carefully managed to ensure food safety, product consistency, and operational efficiency. The following sections detail the key steps, technologies, and the overall production flow.
Key Steps in Food Production
The food production process at Tyson Foods Rome, GA, is a complex, multi-stage operation. It involves several critical steps, each meticulously controlled to meet stringent quality and safety standards. These steps include the following:
- Receiving and Inspection of Raw Materials: Upon arrival, raw materials, such as poultry, are thoroughly inspected for quality, freshness, and compliance with established specifications. This involves visual inspections and potentially, laboratory testing.
- Processing and Preparation: This stage involves various processes depending on the final product. For poultry, this might include deboning, trimming, and cutting the meat into specific portions. Marinades, seasonings, and other ingredients are often added at this stage.
- Cooking and/or Forming: Products may undergo cooking, which could involve methods like grilling, baking, frying, or steaming. Alternatively, products might be formed into specific shapes, such as nuggets or patties, using specialized equipment.
- Packaging: Prepared products are then packaged in various formats, such as trays, bags, or boxes. Packaging protects the product and extends its shelf life. Packaging may also include modified atmosphere packaging (MAP) to further preserve freshness.
- Quality Control and Inspection: Throughout the production process, rigorous quality control measures are in place. This includes regular inspections, weight checks, and sensory evaluations to ensure products meet established standards.
- Freezing and Storage: Many products are frozen to maintain quality and extend shelf life. Frozen products are then stored in temperature-controlled warehouses.
- Shipping and Distribution: Finally, finished products are shipped to distribution centers and retail outlets for sale to consumers.
Technologies and Equipment
Tyson Foods Rome, GA, utilizes advanced technologies and equipment to streamline production and maintain high standards. These include:
- Automated Processing Equipment: Automated systems are used for various tasks, including cutting, deboning, and portioning. This enhances efficiency and reduces the need for manual labor.
- Advanced Cooking Systems: State-of-the-art cooking equipment, such as industrial ovens, fryers, and grills, are used to cook products quickly and consistently.
- Packaging Machinery: High-speed packaging lines are used to efficiently package products in various formats. This includes automated sealing, labeling, and coding systems.
- Refrigeration and Freezing Systems: Advanced refrigeration and freezing systems are essential for preserving product quality and extending shelf life. This includes blast freezers and temperature-controlled storage facilities.
- Quality Control Systems: Integrated quality control systems, including metal detectors, X-ray inspection systems, and automated weight scales, are used to ensure product safety and quality.
- Food Safety Technologies: Technologies such as Hazard Analysis and Critical Control Points (HACCP) systems are employed to proactively identify and mitigate potential food safety hazards.
Production Flow Illustration
The production flow at the Tyson Foods Rome, GA, facility is designed for efficiency and product safety. The process begins with the arrival of raw materials, which are thoroughly inspected. The raw materials then proceed to processing areas, where they are prepared and transformed. For example, incoming poultry may be unloaded from refrigerated trucks, inspected for any visible defects, and then conveyed to a processing line.
Here, automated machinery may debone, trim, and cut the poultry into specific portions, such as breasts, thighs, and wings. These portions may then be marinated or seasoned, depending on the final product.The prepared products move to the cooking or forming stage. If cooking is required, products may pass through industrial ovens or fryers, where they are cooked to the appropriate internal temperature.
Check what professionals state about food for people eureka ca and its benefits for the industry.
Products requiring forming, like chicken nuggets, are shaped using specialized equipment.Following cooking or forming, the products are packaged. This includes automated packaging lines that seal, label, and code the products. Packaging may also include modified atmosphere packaging (MAP) to extend shelf life. Throughout the production process, products undergo rigorous quality control checks, including metal detection and weight verification, to ensure safety and consistency.Finally, the finished products are quickly frozen, if necessary, and stored in temperature-controlled warehouses.
From there, they are shipped to distribution centers and retail outlets, ready for consumers. This entire process, from raw materials to finished product, is managed with strict adherence to food safety regulations and quality standards, ensuring that consumers receive safe and high-quality products.
Quality Control and Food Safety
Tyson Foods Rome, GA, places paramount importance on ensuring the quality and safety of its products. Rigorous measures are implemented throughout the entire production process, from sourcing raw materials to delivering finished goods. This commitment is driven by a dedication to consumer health and compliance with stringent regulatory standards.
Quality Control Measures
Tyson Foods Rome, GA, employs a comprehensive quality control system to maintain product integrity. This system encompasses several key aspects, each designed to minimize risks and ensure consistent product quality.
- Supplier Audits and Qualification: Before raw materials enter the facility, Tyson Foods conducts thorough audits of its suppliers. These audits assess the suppliers’ adherence to quality standards, food safety protocols, and ethical sourcing practices. Only approved suppliers are authorized to provide ingredients and packaging materials.
- Incoming Material Inspection: Upon arrival, all incoming raw materials and ingredients undergo rigorous inspection. This includes visual inspections, sensory evaluations (e.g., assessing color, odor, and texture), and laboratory testing to verify that they meet established specifications.
- In-Process Monitoring: Quality control is not limited to the beginning and end of the production process. Throughout each stage of processing, from initial preparation to packaging, continuous monitoring and testing are performed. This includes monitoring critical control points (CCPs) to ensure that hazards are controlled and product safety is maintained.
- Laboratory Testing: A dedicated on-site laboratory performs various tests, including microbiological analyses, chemical analyses, and physical property testing. These tests verify the absence of harmful pathogens, ensure compliance with ingredient specifications, and assess product characteristics such as moisture content and fat percentage.
- Process Validation and Verification: Production processes are validated to ensure they consistently produce safe and high-quality products. Verification procedures, such as regular audits and product testing, are in place to confirm that the processes are functioning as intended and meeting established standards.
- Employee Training and Certification: All employees receive comprehensive training on quality control procedures, food safety protocols, and good manufacturing practices (GMPs). Training programs are regularly updated to reflect the latest industry standards and regulatory requirements.
- Traceability Systems: Tyson Foods utilizes robust traceability systems to track products from origin to distribution. This allows for rapid identification and isolation of any product that may pose a safety risk, enabling efficient recall procedures if necessary.
Food Safety Protocols and Certifications
Food safety is a cornerstone of Tyson Foods Rome, GA, operations. The facility adheres to stringent food safety protocols and maintains certifications from recognized organizations.
- Hazard Analysis and Critical Control Points (HACCP): Tyson Foods Rome, GA, implements a HACCP system. This systematic approach identifies potential hazards in the food production process and establishes critical control points to prevent or eliminate those hazards.
- Good Manufacturing Practices (GMPs): The facility adheres to GMPs, which provide guidelines for maintaining a sanitary and safe food processing environment. This includes requirements for personnel hygiene, facility sanitation, equipment maintenance, and pest control.
- Third-Party Audits: The Rome, GA, plant undergoes regular audits by third-party organizations, such as the Safe Quality Food (SQF) Institute and the United States Department of Agriculture (USDA). These audits assess the facility’s compliance with food safety standards and help identify areas for improvement.
- Certifications: Tyson Foods Rome, GA, likely holds certifications from reputable organizations such as SQF, and possibly others relevant to the specific products manufactured at the plant. These certifications demonstrate the facility’s commitment to food safety and quality.
- Pathogen Control Programs: Comprehensive pathogen control programs are in place to minimize the risk of foodborne illnesses. These programs include sanitation procedures, testing for pathogens, and process controls to eliminate or reduce the presence of harmful microorganisms.
“Food safety is not just a responsibility; it is a fundamental commitment at Tyson Foods Rome, GA. We operate under the strict guidelines of the Food Safety Modernization Act (FSMA), which shifts the focus from responding to contamination to preventing it. This includes implementing preventive controls, enhancing inspection programs, and strengthening traceability systems. Furthermore, our commitment extends to adhering to all relevant regulations from agencies such as the USDA, which oversees the safety and labeling of meat, poultry, and egg products, and the FDA, which regulates other food products. We understand that the health and well-being of our consumers depend on the diligence and dedication of every team member, and we are unwavering in our pursuit of excellence in food safety.”
Environmental Sustainability
Tyson Foods is committed to environmental stewardship, and the Rome, GA, facility actively participates in the company’s sustainability initiatives. These efforts are designed to minimize the plant’s environmental impact and contribute to a more sustainable food production system. The focus includes reducing waste, conserving water, and optimizing energy usage.
Waste Reduction and Management
Tyson Foods Rome, GA, prioritizes waste reduction through various strategies, including the implementation of recycling programs and the utilization of byproducts. The goal is to minimize landfill waste and maximize the value derived from all materials used in the production process.
- Recycling Programs: The facility has established comprehensive recycling programs for materials such as cardboard, plastics, and metals. This helps divert waste from landfills and conserves resources. For example, the plant recycles an estimated 100 tons of cardboard monthly, which is then repurposed into new packaging materials.
- Byproduct Utilization: Tyson Foods Rome, GA, finds beneficial uses for byproducts generated during the processing of poultry. These byproducts are often converted into animal feed or other valuable products. The rendering process is a key example, where inedible parts are processed into useful ingredients.
- Waste Minimization: The plant constantly seeks ways to reduce waste at the source. This includes optimizing production processes to minimize scrap and implementing strategies to improve the efficiency of packaging materials.
Water Conservation Practices
Water conservation is a critical aspect of Tyson Foods’ sustainability efforts. The Rome, GA, facility employs several water-saving practices to reduce water consumption and protect local water resources.
- Water Recycling: The facility implements water recycling systems where feasible. This involves treating and reusing water for non-potable purposes, such as cleaning and sanitation. A significant portion of the water used for cooling and washing equipment is recycled, reducing the demand on the local water supply.
- Efficient Equipment: The plant utilizes water-efficient equipment and technologies, such as low-flow nozzles and automated cleaning systems. These systems help minimize water usage during cleaning and sanitation processes.
- Water Monitoring and Management: Continuous monitoring of water usage and leaks is performed. The plant employs a dedicated team to monitor water consumption and promptly address any leaks or inefficiencies. Regular audits are conducted to identify opportunities for further water conservation.
Steps to Reduce Environmental Footprint
The Rome, GA, facility implements a multifaceted approach to reduce its environmental footprint. This involves a combination of practices aimed at conserving resources, reducing emissions, and minimizing waste.
- Energy Efficiency Measures: The facility has implemented energy-efficient lighting, HVAC systems, and equipment upgrades to reduce energy consumption. The plant’s transition to LED lighting has resulted in a significant reduction in energy usage.
- Renewable Energy Integration: Tyson Foods explores the feasibility of incorporating renewable energy sources at the Rome, GA, facility. This might involve the use of solar panels or the purchase of renewable energy credits to offset the plant’s carbon footprint.
- Supplier Engagement: Tyson Foods works with its suppliers to promote sustainable practices throughout the supply chain. This includes encouraging suppliers to implement their own environmental initiatives.
- Community Involvement: The plant actively engages with the local community to promote environmental awareness and support conservation efforts. This includes participating in local clean-up events and supporting environmental education programs.
Challenges and Opportunities
Tyson Foods’ Rome, GA, facility, like any large-scale operation, navigates a complex landscape of challenges and opportunities. These factors significantly influence the plant’s operational efficiency, profitability, and long-term sustainability. Understanding these dynamics is crucial for assessing the facility’s overall performance and future prospects.
Supply Chain and Labor Challenges
The Rome, GA, plant faces several operational hurdles. Supply chain disruptions and labor shortages are particularly impactful.
“The meat and poultry industry has been affected by supply chain disruptions in the past few years, including those caused by the COVID-19 pandemic and other unforeseen events, leading to increased costs and operational challenges.”
- Supply Chain Issues: The facility relies on a consistent flow of raw materials, packaging, and transportation. Disruptions, such as those caused by extreme weather events, transportation bottlenecks, or supplier issues, can lead to production delays, increased costs, and potential shortages. For example, a shortage of specific types of packaging materials could force a temporary halt in production of certain products, impacting delivery schedules and potentially leading to lost sales.
- Labor Shortages: Attracting and retaining a skilled workforce is critical. Labor shortages can lead to understaffing, increased overtime costs, and reduced production capacity. The poultry industry, in particular, often faces challenges in recruiting and retaining workers due to the demanding nature of the work. The Rome plant competes with other local employers for a limited pool of available workers, requiring ongoing efforts to offer competitive wages, benefits, and working conditions.
Growth and Expansion Opportunities
The Rome, GA, facility possesses several avenues for growth and expansion. These opportunities could lead to increased production capacity, diversification of product offerings, and enhanced market share.
- Product Diversification: Expanding the range of products offered could attract new customers and cater to evolving consumer preferences. This could involve introducing new cuts of meat, value-added products like pre-seasoned or marinated items, or exploring opportunities in the plant-based protein market. For instance, if consumer demand for organic chicken increases, the plant could explore the possibility of sourcing organic poultry and establishing a separate production line for organic products.
- Process Optimization: Implementing new technologies and streamlining existing processes can improve efficiency and reduce operating costs. This could include automating certain tasks, upgrading equipment to increase throughput, and optimizing the layout of the production facility. An example would be adopting advanced robotics for tasks such as packaging or palletizing, which could increase speed and reduce the risk of human error.
- Market Expansion: Identifying and penetrating new markets can drive revenue growth. This could involve expanding distribution networks to reach new geographic areas or targeting specific customer segments, such as restaurants, food service providers, or international markets. For example, the plant could explore opportunities to supply products to emerging markets in Asia or Latin America.
Adapting to Changing Market Demands
Tyson Foods’ Rome, GA, plant is constantly adapting to shifts in consumer preferences and market demands. This responsiveness is essential for maintaining competitiveness and ensuring long-term success.The facility can adapt by:
- Responding to Health Trends: There’s a growing consumer demand for healthier food options. The plant can adapt by offering leaner cuts of meat, reduced-sodium products, or items with added nutritional benefits. For instance, if consumer demand for grass-fed beef increases, the plant could adjust its sourcing strategies to include grass-fed cattle.
- Meeting Demand for Convenience: Consumers increasingly seek convenience in their food choices. The Rome, GA, plant can adapt by expanding its offerings of ready-to-eat meals, pre-cooked products, and easy-to-prepare meal kits. An example is the production of pre-cooked chicken strips or rotisserie chickens to cater to busy consumers.
- Adjusting to Sustainable Practices: Growing consumer awareness of environmental issues and the demand for sustainable practices require the Rome plant to adopt eco-friendly initiatives. This could include reducing water and energy consumption, minimizing waste, and sourcing ingredients from sustainable suppliers. For example, implementing a water recycling system can reduce the plant’s environmental footprint and decrease operating costs.
Location and Logistics
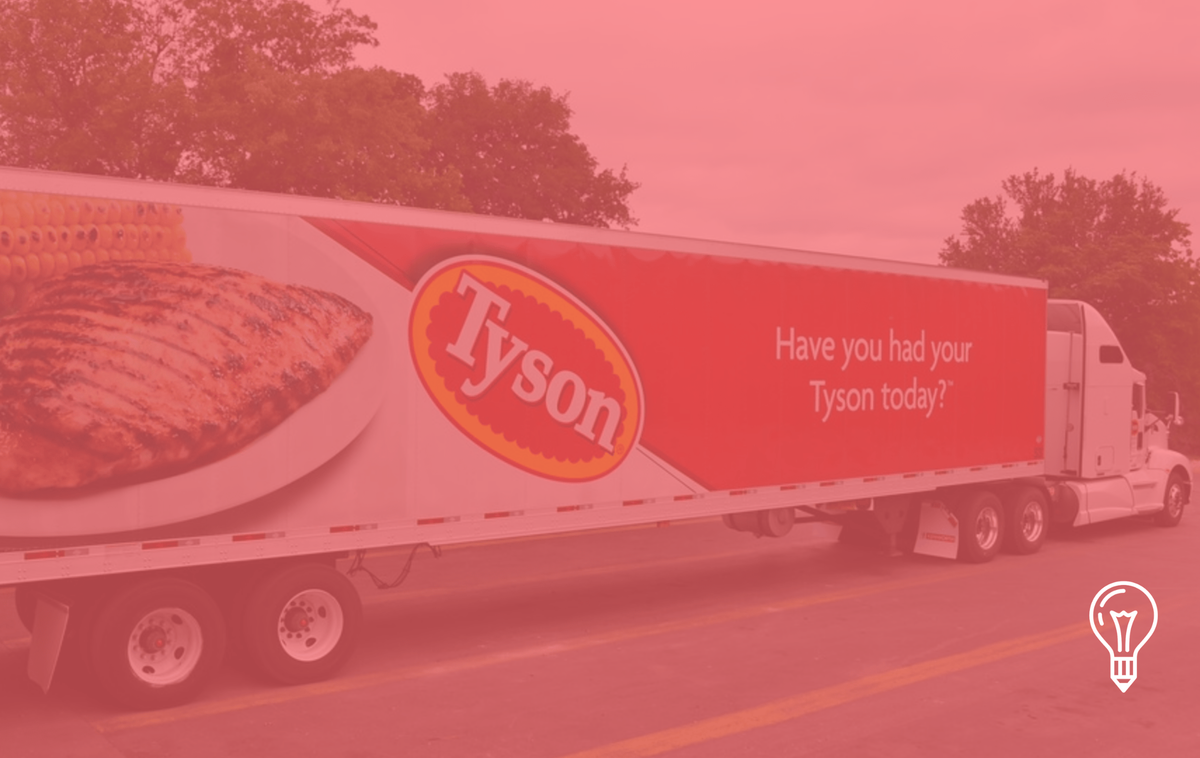
The strategic placement and efficient logistical operations of Tyson Foods’ Rome, GA, facility are crucial for its operational success. These factors directly impact the company’s ability to receive raw materials, process them effectively, and distribute finished products to customers. This section details the facility’s location, transportation links, and the various methods employed for material and product movement.
Facility Location and Transportation Networks
The Tyson Foods plant in Rome, GA, is strategically located to leverage efficient transportation networks. This positioning allows for streamlined access to both raw materials and distribution channels.The Rome, GA, facility is situated in close proximity to:
- Major highways, including Interstate 75, providing efficient truck transportation routes for both inbound and outbound goods.
- Rail lines, offering an alternative mode of transport for large volumes of materials and products, reducing transportation costs and environmental impact.
- Regional distribution centers, enabling faster and more cost-effective delivery to customers across a wide geographic area.
Raw Material Receiving and Finished Product Distribution
The logistics of managing raw materials and distributing finished products are critical for the Rome, GA, facility. This involves a complex network of suppliers, transportation providers, and warehousing operations.Raw materials, such as poultry, are sourced from various locations, including regional farms and processing facilities. Upon arrival at the Rome plant, materials undergo inspection and are stored in temperature-controlled environments. The facility uses advanced inventory management systems to track and manage these materials efficiently.Finished products, including various types of processed poultry, are distributed to a wide range of customers, including grocery stores, restaurants, and food service providers.
The distribution process involves:
- Order fulfillment: Receiving and processing customer orders.
- Warehousing: Storing finished products in refrigerated and frozen storage.
- Transportation: Utilizing a combination of trucking and potentially rail to deliver products to customers.
Shipping Methods Comparison
The Rome, GA, facility utilizes a variety of shipping methods to ensure the efficient and timely delivery of its products. The choice of shipping method depends on factors such as product type, volume, distance, and customer requirements.
Here’s a comparison of the primary shipping methods:
Shipping Method | Description | Advantages | Disadvantages |
---|---|---|---|
Trucking | Primary method for short-to-medium distances, using refrigerated trucks for temperature-sensitive products. | Flexibility, speed, direct delivery, wide geographic reach. | Higher cost compared to rail, potential for delays due to traffic, environmental impact. |
Rail | Used for long-distance transportation of large volumes of products. | Cost-effective for bulk shipments, lower environmental impact compared to trucking. | Less flexibility, longer transit times, requires rail infrastructure. |
Intermodal Transport | Combining trucking and rail transport for a comprehensive solution. | Combines the benefits of both trucking and rail, offers cost efficiency and flexibility. | Requires coordination between different transport modes, potential for delays during transfer. |
Less-Than-Truckload (LTL) | Shipping method for smaller shipments that do not fill an entire truck. | Cost-effective for small businesses, flexibility in shipping volumes. | Longer transit times compared to full truckload, more handling of goods, increased risk of damage. |
Company Culture and Values: Tyson Foods Rome Ga
Tyson Foods, including its facility in Rome, GA, cultivates a work environment emphasizing teamwork, integrity, and a commitment to excellence. The company’s culture is shaped by its core values, which guide its daily operations and interactions with employees, customers, and the community. This section provides insight into the company culture at the Rome, GA facility and illustrates how Tyson Foods’ core values are put into practice.
Company Culture Description
The company culture at Tyson Foods in Rome, GA, promotes a collaborative and inclusive environment. Emphasis is placed on open communication, respect for all employees, and opportunities for professional development. The facility encourages employee feedback and involvement in decision-making processes. Regular training programs are provided to enhance employee skills and ensure adherence to safety protocols. The company fosters a culture of continuous improvement, seeking ways to enhance efficiency, product quality, and workplace safety.
Teamwork is a cornerstone of the operation, with employees from various departments working together to achieve common goals.
Core Values and Operational Reflection
Tyson Foods’ core values are integral to its operations, shaping its business practices and interactions. These values are not merely statements but are actively demonstrated throughout the company, including the Rome, GA, facility. The company strives to integrate these values into every aspect of its operations, from product development to employee relations and community engagement. The commitment to these values helps build trust with stakeholders and contributes to the long-term success of the company.The following list details Tyson Foods’ core values and provides examples of how these values are demonstrated at the Rome, GA, facility:
- Integrity: Tyson Foods operates with honesty and ethical conduct.
- At the Rome, GA, facility, this is reflected in the strict adherence to food safety regulations and quality control procedures. Employees are trained to identify and report any potential issues, ensuring product safety and consumer trust.
- Teamwork: The company fosters a collaborative environment.
- The Rome, GA, facility organizes regular team meetings to discuss production goals, address challenges, and share best practices. Cross-functional teams collaborate on projects to improve efficiency and solve problems, promoting a sense of shared responsibility.
- Excellence: Tyson Foods is committed to achieving high standards in all aspects of its operations.
- The Rome, GA, facility implements rigorous quality control measures throughout the production process. This includes regular inspections, testing, and process optimization to ensure the consistent delivery of high-quality products.
- Growth: Tyson Foods encourages innovation and continuous improvement.
- The Rome, GA, facility invests in employee training and development programs, including leadership courses and technical skills training. Employees are encouraged to suggest process improvements, leading to increased efficiency and better products.
- Responsibility: The company takes its responsibilities to employees, customers, and the community seriously.
- The Rome, GA, facility actively participates in local community initiatives, such as food drives and educational programs. The company prioritizes employee safety and well-being, offering comprehensive health and safety training programs and promoting a safe work environment.
Future Outlook
Tyson Foods in Rome, GA, is strategically positioned to navigate the evolving landscape of the food industry. The company is committed to long-term sustainability and growth, focusing on innovation, operational efficiency, and community engagement. This outlook encompasses planned investments, adaptation strategies, and a clear vision for the future.
Planned Investments and Expansions
Tyson Foods consistently evaluates opportunities for investment and expansion to meet growing consumer demand and enhance operational capabilities. These investments are crucial for maintaining competitiveness and adapting to technological advancements.The company’s approach to expansion typically involves:
- Modernization of Existing Facilities: Upgrading current infrastructure with advanced technology to improve efficiency and product quality. For instance, the implementation of automated systems for packaging and processing.
- Capacity Expansion: Increasing production capacity to meet growing demand. This may involve adding new production lines or expanding existing facilities. An example of this is adding a new line for chicken processing.
- New Product Development: Investing in research and development to create innovative products that align with consumer preferences, such as plant-based protein options.
Adaptation to Future Challenges and Opportunities
The food industry faces constant challenges, including fluctuating commodity prices, evolving consumer preferences, and environmental concerns. Tyson Foods proactively addresses these challenges by implementing adaptable strategies.These strategies include:
- Supply Chain Resilience: Diversifying sourcing and strengthening relationships with suppliers to mitigate risks associated with disruptions. This could include establishing backup suppliers for key ingredients.
- Consumer-Driven Innovation: Focusing on product development that caters to changing consumer demands, such as healthier options and sustainable packaging. For example, developing lower-sodium products or using compostable packaging.
- Sustainability Initiatives: Reducing environmental impact through water conservation, waste reduction, and sustainable sourcing practices. This could involve implementing water recycling systems or reducing packaging waste.
- Technological Integration: Utilizing advanced technologies like artificial intelligence and data analytics to optimize production processes and improve decision-making. This may involve using AI to predict equipment failures or optimize production schedules.
Future Vision of Tyson Foods in Rome, GA
The future of Tyson Foods in Rome, GA, is envisioned as a hub of sustainable food production, operational excellence, and community partnership. The facility will continue to be a significant employer and contributor to the local economy, characterized by a commitment to innovation, quality, and environmental responsibility. The company aims to lead the industry in food safety, animal welfare, and sustainable practices, offering consumers a diverse range of high-quality products while minimizing its environmental footprint.
This vision includes fostering a culture of continuous improvement, empowering employees, and building strong relationships with stakeholders, ensuring a prosperous future for both the company and the community.
Final Conclusion
In conclusion, Tyson Foods Rome GA represents a vital component of the local economy and a key participant in the broader food industry. The facility’s dedication to quality, safety, and sustainability, coupled with its forward-thinking approach to adapting to future challenges, paints a promising picture. As Tyson Foods Rome, GA continues to evolve, it is poised to remain a significant contributor to both the community and the food landscape, highlighting its adaptability and resilience in a constantly changing environment.