US Foods distribution centers are vital hubs in the food supply chain, ensuring that restaurants, healthcare facilities, and other foodservice providers receive the products they need. This comprehensive overview explores the intricate workings of these centers, from the initial receiving of food products to the final delivery to customers. It delves into the history, geographic spread, and the sheer scale of operations that make US Foods a leading distributor.
This discussion will also uncover the operational intricacies within these centers, including the technological advancements that optimize efficiency, the rigorous food safety protocols that safeguard consumer health, and the sustainability initiatives that contribute to environmental responsibility. Furthermore, we will examine the roles of employees, the importance of customer service, and the challenges and future trends shaping the landscape of food distribution.
Overview of US Foods Distribution Centers
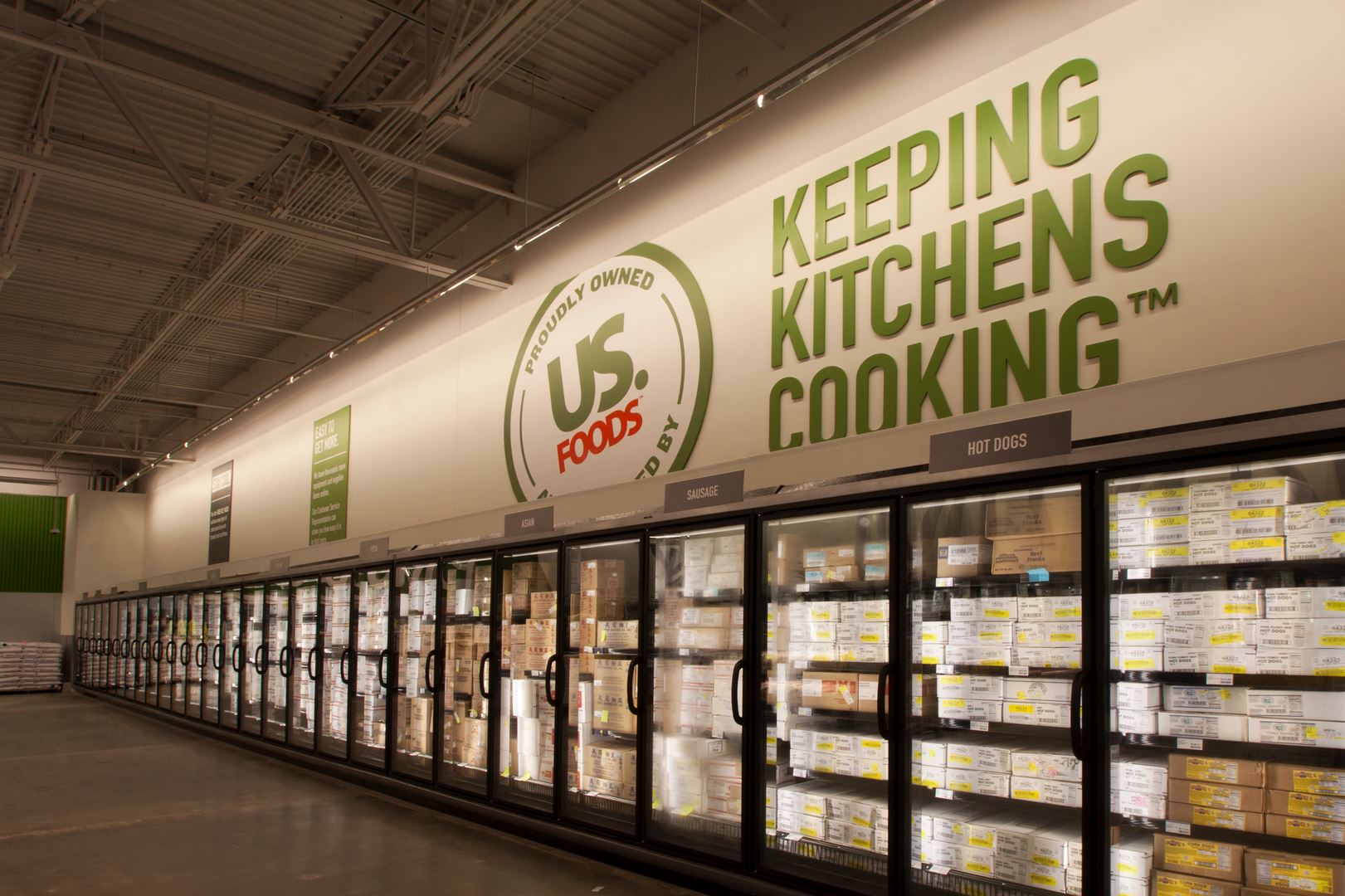
US Foods distribution centers are integral to the company’s operations, facilitating the efficient movement of food and related products to customers nationwide. These centers serve as critical hubs, ensuring the timely delivery of a vast array of goods to restaurants, healthcare facilities, educational institutions, and other foodservice establishments. The following sections will delve into the core functions, history, geographical presence, and operational scale of these vital facilities.
Primary Function of US Foods Distribution Centers
The primary function of US Foods distribution centers is to receive, store, and distribute food products and related supplies to a wide range of customers. This process involves several key activities, each playing a crucial role in maintaining the integrity and efficiency of the supply chain.
- Receiving: Goods are received from various suppliers, inspected for quality, and verified against purchase orders. This ensures accuracy and helps maintain product standards.
- Storage: Products are stored under appropriate conditions, including refrigerated, frozen, and dry storage areas, to maintain freshness and prevent spoilage. Inventory management systems are employed to track product location and ensure efficient retrieval.
- Order Fulfillment: Customer orders are processed, and items are picked, packed, and prepared for shipment. This often involves utilizing automated systems and technologies to optimize efficiency.
- Transportation: Orders are loaded onto delivery trucks and transported to customer locations. US Foods utilizes its own fleet of trucks and drivers, ensuring control over the delivery process.
Brief History of US Foods and its Distribution Network
US Foods has a rich history rooted in the consolidation of various food distribution companies. This history has shaped the development and expansion of its distribution network, resulting in a significant presence across the United States.The company’s origins can be traced back to the late 19th century with the establishment of several independent food distribution businesses. The modern US Foods evolved through a series of mergers and acquisitions, beginning in the mid-20th century.
Key milestones include:
- 1906: The Sexton Company, one of the earliest companies that contributed to US Foods, was founded.
- Early 2000s: A major period of consolidation, with various regional distributors merging to form a larger national entity.
- Present: US Foods continues to refine its distribution network, incorporating advanced technologies and strategies to improve efficiency and customer service.
Geographic Distribution of US Foods Centers Across the United States
US Foods maintains a strategically positioned network of distribution centers throughout the United States, ensuring broad coverage and efficient delivery capabilities. This extensive network allows the company to serve a diverse customer base across various regions.The distribution centers are strategically located to optimize delivery times and minimize transportation costs. These locations are often chosen based on factors such as proximity to major transportation routes, customer concentration, and access to a skilled workforce.
While specific locations can vary, the network generally includes centers in:
- Northeast: Centers supporting major metropolitan areas and regional distribution.
- Southeast: Facilities serving the growing population and foodservice industry in the region.
- Midwest: Hubs for distribution throughout the central United States.
- Southwest: Centers supporting the rapidly expanding markets in the Southwest.
- West Coast: Facilities to serve the West Coast markets.
The exact number and specific locations of distribution centers may fluctuate over time based on market demands and strategic decisions.
Scale of Operations: Square Footage and Product Volume Handled
The scale of US Foods’ operations is substantial, reflecting the company’s position as a leading foodservice distributor. The size and capacity of its distribution centers are significant, enabling the handling of a vast quantity of products.The distribution centers vary in size, but many facilities encompass hundreds of thousands of square feet, some exceeding one million square feet. This extensive space allows for:
- Large-Scale Storage: Accommodating a wide range of food products, including fresh, frozen, and dry goods.
- Efficient Order Fulfillment: Space for processing a high volume of customer orders daily.
- Advanced Technology Integration: Enabling the implementation of automated systems, such as conveyor belts, picking robots, and inventory management systems.
The volume of products handled is also considerable. US Foods distributes a wide variety of items, including:
- Food Products: Fresh produce, meats, seafood, dairy, and frozen foods.
- Beverages: A wide selection of soft drinks, juices, and other beverages.
- Equipment and Supplies: Kitchen equipment, cleaning supplies, and disposable items.
The specific product volume handled at each center depends on its size, location, and customer base. The company’s large-scale operations and advanced logistics capabilities are crucial for maintaining its position in the foodservice distribution industry.
Operations and Logistics within Distribution Centers
US Foods distribution centers are meticulously designed hubs where vast quantities of food products are received, stored, processed, and dispatched to a diverse customer base. The efficiency of these operations is critical to maintaining food safety, minimizing waste, and ensuring timely delivery. This section delves into the core operational processes that underpin the success of these distribution centers.
Receiving Process for Incoming Food Products
The receiving process is the initial gateway for products entering a US Foods distribution center. It involves several critical steps to ensure product integrity and accuracy.The steps involved in the receiving process are:
- Unloading: Upon arrival, trucks are unloaded, and shipments are inspected for any visible damage. This often involves the use of forklifts and other material handling equipment.
- Verification: Each shipment is cross-referenced against the accompanying purchase order to verify the quantity and type of products received. Any discrepancies are immediately documented.
- Inspection: Products undergo a thorough inspection, which includes checking for temperature compliance (especially for refrigerated and frozen goods), expiration dates, and any signs of damage or spoilage.
- Quality Control: Samples may be taken for quality control testing, particularly for products with specific requirements or potential risks.
- Data Entry: Information about the received products, including the quantity, product codes, and date received, is entered into the inventory management system.
- Put-Away: Products are then transported to their designated storage locations within the distribution center. This process is optimized based on product type and storage requirements.
Storage Methods for Different Types of Food
Effective storage is crucial for preserving the quality, safety, and shelf life of food products. US Foods utilizes various storage methods tailored to the specific needs of different food categories.Here’s a breakdown of the storage methods used:
- Refrigerated Storage: Perishable items like fresh produce, dairy products, and some meats are stored in refrigerated areas maintained at specific temperatures (typically between 34°F and 40°F / 1°C and 4°C) to slow down spoilage and bacterial growth.
- Frozen Storage: Frozen foods, such as frozen vegetables, ice cream, and frozen meats, are stored in freezers at temperatures of 0°F (-18°C) or below to maintain their frozen state and extend their shelf life.
- Dry Storage: Non-perishable items like canned goods, dry pasta, and cereals are stored in dry, temperature-controlled environments. These areas are designed to protect products from moisture, pests, and extreme temperatures.
- Specialized Storage: Certain products may require specialized storage, such as controlled atmosphere storage for specific fruits and vegetables to extend their shelf life or areas with enhanced security for high-value items.
Order Fulfillment Process, from Order Placement to Shipment
The order fulfillment process is the core of a distribution center’s operations. It involves a series of coordinated activities to ensure that customer orders are accurately picked, packed, and shipped in a timely manner.The order fulfillment process generally includes the following steps:
- Order Receipt: Orders are received electronically, typically through an online portal or Electronic Data Interchange (EDI) system.
- Order Processing: Orders are processed and validated against inventory availability. This step may involve order consolidation, splitting, or substitution if needed.
- Picking: Warehouse staff, often using handheld scanners and automated systems, pick the ordered items from their designated storage locations.
- Packing: Picked items are packed securely into appropriate containers, often with temperature control measures for perishable goods.
- Verification: A final verification step ensures that the packed order matches the customer’s order accurately.
- Shipping: The packed orders are loaded onto trucks for delivery to the customer. Shipping labels and documentation are prepared.
Transportation Methods Used to Deliver Products to Customers
US Foods employs a variety of transportation methods to deliver products to its customers, ensuring efficient and timely delivery. The selection of transportation methods depends on factors such as the distance, the type of product, and the customer’s requirements.Transportation methods include:
- Trucking: The primary mode of transportation is trucking, utilizing a fleet of refrigerated and dry vans to transport goods to customers. US Foods operates a large private fleet, providing greater control over delivery schedules and product handling.
- Cross-Docking: Cross-docking is a technique where products are received at the distribution center and then immediately transferred to outbound trucks without being stored. This method is used for high-volume, fast-moving items to reduce storage costs and improve delivery speed.
- Dedicated Delivery Routes: US Foods often establishes dedicated delivery routes to serve specific customer segments, such as restaurants, hotels, and institutions. These routes are optimized for efficiency and to meet the unique needs of each customer.
- Third-Party Logistics (3PL) Providers: In some cases, US Foods may partner with 3PL providers to handle specific transportation needs, particularly for deliveries to remote locations or for specialized services.
Technology Used for Inventory Management and Tracking
Technology plays a critical role in the efficient management and tracking of inventory within US Foods distribution centers. These technologies help to optimize operations, reduce errors, and improve product visibility.The technology used for inventory management and tracking includes:
- Warehouse Management Systems (WMS): WMS software is used to manage all aspects of warehouse operations, including receiving, storage, picking, packing, and shipping.
- Radio Frequency Identification (RFID): RFID technology uses radio waves to track and identify items. RFID tags are attached to products or pallets, allowing for real-time inventory tracking and improved accuracy.
- Barcode Scanning: Barcode scanners are used throughout the distribution center to track products at various stages of the process, from receiving to shipping.
- Automated Guided Vehicles (AGVs): AGVs are used to transport products within the warehouse, reducing labor costs and improving efficiency.
- Temperature Monitoring Systems: Temperature sensors are used to monitor the temperature of refrigerated and frozen storage areas, ensuring that products are stored within the required temperature ranges.
- Inventory Optimization Software: This software uses algorithms to analyze inventory data and optimize inventory levels, reducing waste and ensuring product availability.
Technology and Automation in US Foods Centers
US Foods leverages cutting-edge technology and automation to streamline its distribution center operations, enhancing efficiency, food safety, and waste reduction. These advancements are critical for maintaining a competitive edge in the food distribution industry and meeting the evolving needs of its customers. The implementation of sophisticated systems allows US Foods to optimize every stage of the supply chain, from receiving and storage to order fulfillment and delivery.
Warehouse Management Systems (WMS) in Use
Warehouse Management Systems (WMS) are central to the efficient operation of US Foods distribution centers. These systems provide real-time visibility into inventory levels, order status, and warehouse activities.A WMS typically performs the following functions:
- Receiving: Manages the inbound process, including verifying deliveries, assigning storage locations, and updating inventory records.
- Inventory Management: Tracks the location and quantity of products, optimizes storage space utilization, and facilitates stock rotation (FIFO – First In, First Out).
- Order Fulfillment: Directs picking, packing, and shipping processes, ensuring accurate and timely order completion.
- Labor Management: Monitors and manages workforce productivity, optimizes staffing levels, and provides insights into operational efficiency.
- Reporting and Analytics: Generates reports on key performance indicators (KPIs), providing data-driven insights for continuous improvement.
Automated Systems for Picking, Packing, and Sorting
US Foods utilizes a range of automated systems to improve the speed and accuracy of order fulfillment. These technologies are particularly beneficial in handling the high volumes and diverse product offerings common in food distribution.Automated systems often include:
- Automated Storage and Retrieval Systems (AS/RS): These systems use computer-controlled cranes to automatically store and retrieve pallets or cases, optimizing space utilization and reducing labor costs.
- Automated Guided Vehicles (AGVs): AGVs transport materials throughout the warehouse, such as pallets or cases, reducing the need for manual handling and improving efficiency.
- Automated Picking Systems: These systems, such as pick-to-light or voice picking, guide warehouse workers to the correct locations and streamline the picking process, reducing errors and increasing speed.
- Automated Sorting Systems: High-speed conveyor systems with automated sorters direct packages to the appropriate shipping docks, optimizing the sorting process.
Data Analytics for Optimizing Distribution Center Efficiency
Data analytics plays a crucial role in optimizing distribution center efficiency at US Foods. By analyzing data from various sources, such as WMS, transportation management systems, and sales data, US Foods can gain valuable insights into its operations and make data-driven decisions.Data analytics applications include:
- Demand Forecasting: Analyzing historical sales data to predict future demand, enabling US Foods to optimize inventory levels and reduce waste.
- Route Optimization: Analyzing delivery routes to optimize transportation efficiency, reduce fuel costs, and improve delivery times.
- Performance Monitoring: Tracking key performance indicators (KPIs) such as order accuracy, on-time delivery, and warehouse productivity to identify areas for improvement.
- Inventory Optimization: Analyzing inventory levels to minimize storage costs, reduce waste, and ensure product availability.
Technology’s Impact on Food Safety and Waste Reduction
Technology significantly enhances food safety and reduces waste in US Foods distribution centers. The implementation of these technologies is essential for complying with food safety regulations and maintaining the quality of perishable products.Examples of how technology helps:
- Temperature Monitoring: Real-time temperature monitoring systems track the temperature of refrigerated and frozen products throughout the distribution process, ensuring that products remain within safe temperature ranges.
- Expiration Date Management: WMS and other systems track product expiration dates, enabling US Foods to rotate stock (FIFO) and minimize the risk of expired products.
- Traceability: Systems that track products from origin to delivery, enabling quick identification and removal of products in case of a recall.
- Waste Management: Data analytics identifies patterns in waste generation, helping US Foods to optimize inventory management and reduce spoilage.
Comparison of Automation Types
US Foods employs various types of automation to enhance its distribution center operations. Each type of automation offers unique benefits in terms of efficiency, cost savings, and improved accuracy.
Automation Type | Description | Benefits |
---|---|---|
Automated Storage and Retrieval Systems (AS/RS) | Computer-controlled systems that automatically store and retrieve pallets or cases using cranes. | Optimized space utilization, reduced labor costs, improved inventory control. |
Automated Guided Vehicles (AGVs) | Vehicles that transport materials throughout the warehouse without the need for a human operator. | Increased efficiency, reduced labor costs, improved safety. |
Automated Picking Systems | Systems that guide warehouse workers to the correct locations and streamline the picking process, such as pick-to-light or voice picking. | Reduced picking errors, increased picking speed, improved order accuracy. |
Automated Sorting Systems | High-speed conveyor systems with automated sorters that direct packages to the appropriate shipping docks. | Increased sorting speed, reduced labor costs, improved order accuracy. |
Product Handling and Food Safety Protocols
US Foods prioritizes the safety and quality of its food products throughout the entire distribution process. This commitment is reflected in comprehensive protocols and rigorous training programs designed to minimize risks and ensure that customers receive safe and high-quality food items. These protocols are not just guidelines; they are integral to the company’s operational framework and are constantly updated to reflect the latest industry best practices and regulatory requirements.
Maintaining Food Safety Standards
Maintaining food safety standards at US Foods involves a multi-faceted approach that encompasses every stage of the distribution process, from receiving to delivery. These standards are in place to comply with all relevant regulations and guidelines, including those set by the Food and Drug Administration (FDA) and the Food Safety Modernization Act (FSMA).
- Receiving: Incoming shipments are inspected for temperature, packaging integrity, and expiration dates. Products failing to meet these standards are rejected. Detailed records of inspections are maintained.
- Storage: Products are stored in designated areas based on their temperature requirements (e.g., refrigerated, frozen, dry). Regular temperature monitoring is conducted, and any deviations trigger immediate corrective action.
- Order Fulfillment: During order picking and packing, employees follow strict hygiene protocols to prevent cross-contamination. Products are handled with care to maintain their integrity.
- Transportation: Temperature-controlled vehicles are used for transporting perishable goods. Drivers are trained in proper handling procedures and are equipped to monitor and maintain the required temperatures throughout the journey.
Temperature Control for Perishable Goods
Effective temperature control is crucial for preserving the quality and safety of perishable goods. US Foods employs a variety of strategies and technologies to ensure that products are maintained at the appropriate temperatures from the moment they arrive at a distribution center until they reach the customer. This commitment helps to prevent spoilage and minimize the risk of foodborne illnesses.
- Refrigerated and Frozen Storage: Distribution centers are equipped with advanced refrigeration and freezer systems that maintain precise temperature ranges. These systems include backup power to prevent temperature fluctuations during outages.
- Temperature Monitoring Systems: Continuous temperature monitoring systems are installed throughout the storage and transportation processes. These systems use sensors to track temperatures in real-time and alert personnel to any deviations from the established standards.
- Temperature-Controlled Vehicles: US Foods utilizes a fleet of refrigerated and frozen trucks equipped with advanced cooling systems. These vehicles are regularly inspected and maintained to ensure optimal performance.
- Cold Chain Management: A comprehensive cold chain management system ensures that the temperature of perishable goods is maintained throughout the entire distribution process. This system includes detailed protocols for handling, storage, and transportation.
- Example: A distribution center handling fresh produce might maintain a temperature range of 34-38°F (1-3°C) for refrigerated storage and transportation, while frozen products would be kept at 0°F (-18°C) or below.
Protocols for Handling Food Recalls and Product Returns
US Foods has established detailed protocols for handling food recalls and product returns to ensure that any potentially unsafe or defective products are quickly removed from the supply chain and that customers are protected. These protocols are designed to be efficient and effective, minimizing the impact of recalls and returns on both customers and the company. The protocols are regularly reviewed and updated to reflect the latest regulatory requirements and industry best practices.
- Recall Procedures: In the event of a food recall, US Foods immediately notifies its customers and initiates a product retrieval process. This process involves identifying the affected products, quarantining them, and arranging for their return or destruction.
- Product Traceability: US Foods uses a sophisticated product traceability system that allows it to track products from the point of origin to the customer. This system enables the company to quickly identify and isolate affected products during a recall.
- Customer Notification: Customers are promptly notified of any recalls and provided with detailed instructions on how to handle the affected products. This notification includes information on the product, the reason for the recall, and the actions that customers should take.
- Product Returns: US Foods has a process for handling product returns, which ensures that returned products are handled safely and efficiently. This process includes inspecting returned products to determine their condition and disposition.
- Example: If a product recall is issued for a specific brand of frozen vegetables due to potential contamination, US Foods would immediately notify its customers, identify and quarantine all affected product in its distribution centers, and arrange for the return or destruction of the recalled product.
Preventing Contamination and Ensuring Product Quality
Preventing contamination and ensuring product quality are paramount at US Foods. The company implements a range of measures to minimize the risk of contamination and maintain the integrity of its products. These measures include strict hygiene protocols, regular inspections, and employee training programs.
- Hygiene Protocols: Employees are required to follow strict hygiene protocols, including frequent handwashing, the use of gloves and hairnets, and the proper handling of food products.
- Facility Sanitation: Distribution centers are regularly cleaned and sanitized to prevent the growth of bacteria and other contaminants. This includes cleaning and sanitizing all equipment, storage areas, and transportation vehicles.
- Pest Control: US Foods has a comprehensive pest control program to prevent pests from entering and contaminating food products. This program includes regular inspections, pest monitoring, and the use of appropriate pest control measures.
- Product Inspection: Products are regularly inspected for quality and safety. This includes checking for signs of spoilage, damage, and contamination.
- Supplier Audits: US Foods conducts regular audits of its suppliers to ensure that they meet its food safety and quality standards.
- Example: US Foods might conduct regular swab tests of food contact surfaces in its distribution centers to monitor for the presence of bacteria, ensuring that cleaning and sanitization protocols are effective.
Training Programs for Employees on Food Safety and Handling
US Foods invests significantly in training programs to educate its employees on food safety and handling procedures. These programs are designed to provide employees with the knowledge and skills they need to handle food products safely and effectively. Training is ongoing and is updated to reflect the latest industry standards and regulatory requirements. This is critical to ensuring that all employees understand their roles in maintaining food safety.
- New Hire Training: All new employees receive comprehensive training on food safety and handling procedures. This training covers topics such as hygiene protocols, temperature control, and product handling.
- Ongoing Training: Employees receive ongoing training to keep them updated on the latest food safety standards and procedures. This training may include refresher courses, webinars, and on-the-job training.
- Specialized Training: Employees in specific roles, such as those involved in handling perishable goods or operating temperature-controlled equipment, receive specialized training tailored to their responsibilities.
- Certification Programs: US Foods may offer certification programs, such as the ServSafe program, to provide employees with a recognized credential in food safety.
- Training Materials: Training materials include manuals, videos, and online modules. These materials are designed to be informative and engaging.
- Example: Employees might be required to complete a training module on proper handwashing techniques and receive a practical demonstration to ensure they understand and can implement the procedure correctly.
Sustainability Initiatives in Distribution Centers
US Foods recognizes the importance of environmental stewardship and has implemented various initiatives to minimize its environmental impact across its distribution network. These efforts focus on energy efficiency, waste reduction, sustainable transportation, and the use of eco-friendly packaging, reflecting a commitment to long-term sustainability.
Energy-Efficient Practices in US Foods Distribution Centers
US Foods employs several energy-efficient practices to reduce its carbon footprint. These include the implementation of advanced technologies and operational strategies designed to minimize energy consumption.
- LED Lighting: The company has transitioned to energy-efficient LED lighting systems in its distribution centers. This reduces energy consumption and lowers operational costs while providing better lighting quality for employees.
- Energy Management Systems: US Foods utilizes sophisticated energy management systems to monitor and optimize energy usage throughout its facilities. These systems allow for real-time tracking and analysis, enabling proactive adjustments to reduce energy waste.
- Smart Refrigeration Systems: Refrigeration systems are a significant energy consumer in food distribution. US Foods has invested in smart refrigeration technologies that optimize temperature control, minimize energy use, and ensure product integrity.
- Building Automation Systems: Implementing building automation systems that regulate HVAC, lighting, and other building systems helps to reduce energy consumption. These systems often use sensors and automated controls to adjust energy use based on occupancy and environmental conditions.
Waste Reduction and Recycling Programs
Waste reduction and recycling programs are integral to US Foods’ sustainability efforts. The company strives to minimize waste generation and maximize the recovery of recyclable materials.
- Comprehensive Recycling Programs: US Foods operates comprehensive recycling programs across its distribution centers, focusing on materials such as cardboard, plastics, paper, and metals. These programs divert significant amounts of waste from landfills.
- Food Waste Reduction: Strategies to reduce food waste are essential. US Foods implements inventory management systems and collaborates with food banks and charitable organizations to donate surplus food.
- Waste Audits and Optimization: Regular waste audits are conducted to identify opportunities for waste reduction and recycling improvements. These audits help to optimize waste management processes and identify areas where waste can be minimized.
- Composting Initiatives: Some distribution centers have implemented composting programs for organic waste, such as food scraps and yard waste, further reducing landfill waste.
Initiatives to Reduce the Carbon Footprint of Transportation and Logistics
Reducing the carbon footprint of transportation and logistics is a key component of US Foods’ sustainability strategy. The company employs various methods to optimize transportation efficiency and minimize emissions.
- Route Optimization: US Foods utilizes route optimization software to plan the most efficient delivery routes, minimizing mileage and fuel consumption.
- Fleet Efficiency: The company invests in fuel-efficient trucks and trailers, including those that run on alternative fuels.
- Driver Training: US Foods provides driver training programs that focus on fuel-efficient driving techniques, further reducing fuel consumption and emissions.
- Backhaul Programs: Implementing backhaul programs where trucks return with cargo after deliveries can reduce empty miles and improve overall transportation efficiency.
Use of Sustainable Packaging Materials
US Foods is committed to using sustainable packaging materials to reduce its environmental impact. This involves sourcing eco-friendly materials and designing packaging for recyclability.
- Recycled Content Packaging: The company uses packaging materials with a high percentage of recycled content.
- Reduced Packaging: US Foods strives to minimize the amount of packaging used, reducing material waste and transportation costs.
- Recyclable Packaging: The company is working towards using packaging materials that are easily recyclable.
- Collaboration with Suppliers: US Foods collaborates with its suppliers to encourage the use of sustainable packaging materials throughout the supply chain.
US Foods’ Sustainable Practices
US Foods integrates a wide range of sustainable practices into its operations. These practices are interconnected, contributing to a holistic approach to environmental responsibility.
- Energy Efficiency Improvements
- Waste Reduction and Recycling Programs
- Transportation and Logistics Optimization
- Sustainable Packaging Materials
- Employee Training and Awareness Programs
- Collaboration with Suppliers and Customers
- Compliance with Environmental Regulations
Employee Roles and Responsibilities: Us Foods Distribution Centers
US Foods distribution centers are complex ecosystems requiring a diverse workforce to ensure efficient operations. Each role plays a critical part in the journey of food products, from the receiving dock to the customer’s doorstep. Understanding the specific responsibilities, training requirements, and safety protocols associated with each position is crucial for the smooth functioning of the entire supply chain.
Job Roles within a US Foods Distribution Center
A variety of roles are present within a US Foods distribution center, each contributing to a specific area of operations. These roles are essential for receiving, storing, picking, packing, and shipping food products to customers.
- Receiving Clerk: Responsible for checking incoming shipments against purchase orders, verifying product quality, and documenting any discrepancies. They ensure the accurate and timely intake of goods.
- Warehouse Worker/Order Selector: These individuals are responsible for picking and packing customer orders. They use various tools and technologies, such as forklifts, pallet jacks, and handheld scanners, to locate and retrieve products from storage areas.
- Forklift Operator: Operates forklifts to move products throughout the warehouse, including loading and unloading trucks, storing inventory, and retrieving items for order fulfillment. This role requires specialized training and certification.
- Inventory Control Specialist: Monitors and manages inventory levels, conducts cycle counts, investigates discrepancies, and ensures accurate stock records. They play a crucial role in minimizing waste and optimizing inventory management.
- Shipping Clerk: Prepares outgoing shipments, including verifying orders, packing goods, creating shipping labels, and coordinating with transportation providers.
- Quality Assurance Specialist: Ensures food safety and quality standards are met throughout the distribution process. They conduct inspections, monitor temperatures, and implement corrective actions as needed.
- Maintenance Technician: Maintains and repairs warehouse equipment, including forklifts, conveyor systems, and refrigeration units. They ensure the operational efficiency of the facility.
- Warehouse Supervisor/Manager: Oversees daily operations, manages teams of employees, and ensures that productivity and safety goals are met. They are responsible for coordinating activities and resolving issues.
Training and Skills Required for Each Role
Specific training and skill sets are required for each position to ensure efficient and safe operations. US Foods provides comprehensive training programs to equip employees with the necessary knowledge and abilities.
- Receiving Clerk: Requires basic computer skills, attention to detail, and the ability to work with inventory management systems. Training includes product knowledge, receiving procedures, and safety protocols.
- Warehouse Worker/Order Selector: Demands physical stamina, the ability to operate handheld scanners, and the ability to follow order picking procedures accurately. Training includes order selection techniques, warehouse layout familiarization, and safety training.
- Forklift Operator: Requires specialized training and certification, including safe operation practices, load handling techniques, and pre-operational inspection procedures. This training is usually provided by certified instructors.
- Inventory Control Specialist: Requires strong analytical skills, proficiency in inventory management software, and the ability to investigate and resolve inventory discrepancies. Training includes inventory control principles, data analysis, and auditing procedures.
- Shipping Clerk: Requires proficiency in shipping software, attention to detail, and the ability to prepare shipping documentation accurately. Training includes shipping procedures, packaging techniques, and carrier requirements.
- Quality Assurance Specialist: Requires knowledge of food safety regulations, quality control procedures, and the ability to conduct inspections and implement corrective actions. Training includes HACCP principles, food safety standards, and auditing techniques.
- Maintenance Technician: Requires technical skills in equipment repair and maintenance, including electrical, mechanical, and refrigeration systems. Training includes equipment-specific maintenance procedures, troubleshooting techniques, and safety protocols.
- Warehouse Supervisor/Manager: Requires leadership skills, the ability to manage teams, and knowledge of warehouse operations. Training includes leadership development, performance management, and warehouse management principles.
Safety Protocols for Employees
Safety is paramount in US Foods distribution centers. Strict safety protocols are implemented to protect employees from potential hazards. These protocols include the use of personal protective equipment (PPE), adherence to safety procedures, and regular safety training.
- Personal Protective Equipment (PPE): Employees are required to wear appropriate PPE, such as safety shoes, gloves, eye protection, and high-visibility vests, depending on the job role and the tasks being performed.
- Equipment Operation: Strict guidelines are in place for the safe operation of forklifts, pallet jacks, and other warehouse equipment. Employees must be properly trained and certified to operate such equipment.
- Load Handling: Proper lifting techniques and load handling procedures are emphasized to prevent injuries. Employees are trained on how to lift and carry heavy objects safely.
- Hazard Communication: Employees are informed about potential hazards in the workplace, including the handling of hazardous materials and the location of safety equipment.
- Emergency Procedures: Regular drills and training are conducted to ensure employees are prepared for emergency situations, such as fires or other incidents.
- Regular Safety Training: Ongoing safety training programs are conducted to reinforce safety protocols and update employees on new safety procedures and regulations.
Teamwork and Collaboration within the Operation
Effective teamwork and collaboration are essential for the efficient functioning of a US Foods distribution center. Success relies on employees working together to achieve common goals, share information, and support each other.
- Communication: Open and effective communication between employees, supervisors, and other departments is crucial for coordinating activities and resolving issues.
- Shared Goals: Employees are united by shared goals, such as meeting order deadlines, ensuring product quality, and maintaining a safe working environment.
- Cross-Functional Collaboration: Different departments and teams collaborate to ensure seamless operations, from receiving to shipping.
- Problem-Solving: Employees work together to identify and resolve problems, contributing to continuous improvement.
- Recognition and Appreciation: Recognizing and appreciating teamwork and collaborative efforts fosters a positive and supportive work environment.
Typical Career Progression within a Distribution Center
US Foods offers opportunities for career advancement within its distribution centers. Employees can progress through various roles based on their skills, experience, and performance.
- Entry-Level Positions: These include roles such as receiving clerk or warehouse worker, providing a foundation for understanding warehouse operations.
- Experienced Roles: Employees with experience may advance to roles like inventory control specialist or shipping clerk, taking on more responsibility.
- Supervisory Positions: High-performing employees may be promoted to supervisory positions, such as warehouse supervisor, leading teams and overseeing daily operations.
- Management Roles: With further experience and training, employees can advance to management roles, such as warehouse manager, overseeing larger areas of the operation.
- Specialized Roles: Opportunities exist for specialized roles, such as quality assurance specialist or maintenance technician, requiring specific skills and expertise.
Customer Service and Distribution Center Interactions
US Foods distribution centers play a crucial role in fostering strong customer relationships, going beyond mere order fulfillment to provide comprehensive support and address individual needs. This section delves into the various ways these centers interact with customers, from processing orders to handling feedback, highlighting the commitment to service excellence.
Supporting Customer Orders and Requests
Distribution centers are the operational backbone for fulfilling customer orders. They provide support to the customers in different ways.
- Order Processing: Orders are received through various channels, including online platforms, sales representatives, and direct communication. The distribution center’s Warehouse Management System (WMS) processes these orders, allocating inventory, and generating picking instructions.
- Order Fulfillment: Trained warehouse staff meticulously pick, pack, and prepare orders for shipment, ensuring accuracy and adherence to customer specifications. This includes selecting the correct products, verifying quantities, and maintaining product integrity.
- Delivery Coordination: The distribution center coordinates deliveries with its own fleet or third-party logistics providers. This involves scheduling delivery times, optimizing routes, and communicating with customers regarding delivery status.
- Real-time Information: Customers can access real-time information about their orders, including tracking updates and estimated delivery times, through online portals or customer service representatives.
- Proactive Communication: Distribution centers proactively communicate with customers regarding potential delays, product substitutions, or any other issues that may impact their orders.
Handling Customer Complaints and Inquiries
Addressing customer complaints and inquiries effectively is paramount to maintaining customer satisfaction. Distribution centers have established procedures to manage these interactions.
- Dedicated Customer Service Teams: Each distribution center typically has a dedicated customer service team equipped to handle complaints, inquiries, and resolve issues promptly.
- Complaint Channels: Customers can submit complaints and inquiries through various channels, including phone, email, online portals, and direct communication with sales representatives.
- Issue Resolution: Customer service representatives investigate complaints, identify the root cause of issues, and take appropriate actions to resolve them. This may involve product replacements, refunds, or adjustments to future orders.
- Documentation: All complaints and inquiries are documented in a centralized system to track trends, identify recurring issues, and improve service quality.
- Feedback Loop: Customer feedback is used to continuously improve operational processes, product offerings, and overall customer experience.
Building Customer Relationships
Distribution centers are instrumental in cultivating strong customer relationships through consistent and reliable service. The centers offer a lot to the customers, some of them are:
- Personalized Service: Distribution centers strive to provide personalized service to meet the specific needs of each customer.
- Proactive Problem Solving: Customer service teams proactively identify and resolve potential issues before they impact customers.
- Relationship Building: Sales representatives and customer service teams build strong relationships with customers through regular communication and personalized support.
- Loyalty Programs: US Foods may offer loyalty programs or other incentives to reward and retain valued customers.
- Feedback Solicitation: Distribution centers actively solicit customer feedback to understand their needs and improve service.
Order Customization and Special Requests
US Foods distribution centers accommodate order customization and special requests to meet diverse customer needs. These include:
- Product Selection: Customers can select from a wide range of products, including standard and specialty items, to create customized orders.
- Portioning and Packaging: Distribution centers offer portioning and packaging services to meet specific customer requirements, such as repackaging products into smaller or larger quantities.
- Labeling and Branding: Customers can request custom labeling or branding on their products.
- Special Deliveries: Distribution centers can accommodate special delivery requests, such as specific delivery times or locations.
- Ingredient Sourcing: In some cases, distribution centers can assist customers with sourcing specific ingredients or products to meet their needs.
Process for Handling Customer Feedback
A structured process for handling customer feedback is crucial for continuous improvement. Here’s a process that distribution centers can adopt:
1. Feedback Collection
Gather feedback through multiple channels: surveys, online reviews, direct customer communication, and sales team reports.
2. Feedback Categorization
Categorize feedback based on topic (e.g., delivery, product quality, customer service) and sentiment (positive, negative, neutral).
3. Issue Investigation
Investigate negative feedback to identify root causes. This involves reviewing order details, delivery logs, and internal processes.
4. Corrective Action
Implement corrective actions to address the issues. This might involve process improvements, employee training, or product adjustments.
5. Communication and Resolution
Communicate the findings and resolutions to the customer. Offer apologies and compensation if appropriate.
6. Process Monitoring
For descriptions on additional topics like food alexandria la, please visit the available food alexandria la.
Continuously monitor feedback trends to identify recurring issues and track the effectiveness of corrective actions.
7. Continuous Improvement
Use feedback to continuously improve processes, products, and services. Implement changes to prevent similar issues from arising in the future.
Challenges and Future Trends
US Foods distribution centers, like any large-scale operation, are constantly navigating a dynamic landscape of challenges and opportunities. Adapting to these shifts is crucial for maintaining efficiency, profitability, and customer satisfaction. Understanding the current hurdles and anticipating future trends allows US Foods to remain competitive and meet the evolving demands of the food service industry.
Current Challenges in Distribution Centers
Distribution centers face several persistent challenges that require ongoing attention and strategic solutions. These challenges impact various aspects of operations, from labor management to supply chain resilience.
- Labor Shortages and Retention: Attracting and retaining qualified workers, particularly in roles requiring physical labor, is a significant challenge. The demanding nature of the work, coupled with competition from other industries, contributes to high turnover rates. US Foods addresses this by investing in employee training, offering competitive wages and benefits, and implementing automation to reduce the physical strain on workers. For instance, they may provide opportunities for advancement and create a positive work environment.
- Supply Chain Disruptions: Global events, weather patterns, and transportation issues can lead to disruptions in the supply chain, affecting the availability of products. Managing these disruptions requires proactive planning, diversification of suppliers, and robust inventory management systems. US Foods utilizes data analytics to predict potential disruptions and adjust inventory levels accordingly. They may also establish contingency plans, such as alternative sourcing options and optimized transportation routes.
- Rising Operational Costs: Fuel costs, energy expenses, and the cost of raw materials all contribute to rising operational expenses. Efficiency improvements, such as optimized routing, energy-efficient equipment, and waste reduction programs, are essential to mitigate these costs. US Foods implements strategies like consolidating deliveries, utilizing renewable energy sources where feasible, and implementing lean principles to minimize waste.
- Meeting Regulatory Compliance: Adhering to stringent food safety regulations and other compliance requirements is paramount. This necessitates rigorous quality control measures, detailed record-keeping, and ongoing employee training. US Foods invests in advanced technologies, such as real-time temperature monitoring systems and automated tracking of products, to ensure compliance and maintain the integrity of the food supply.
Adapting to Changing Market Demands
US Foods continually adapts its operations to meet the evolving needs of its customers and the broader market. This adaptability is crucial for maintaining a competitive edge.
- Customization and Specialization: The food service industry is increasingly demanding customized products and specialized offerings. US Foods responds by expanding its product portfolio, offering tailored solutions, and providing value-added services. For example, they might offer pre-cut produce, customized portioning, or specialized packaging to meet specific customer needs.
- Focus on Fresh and Local: Growing consumer demand for fresh, locally sourced products influences distribution strategies. US Foods partners with local farmers and suppliers to offer fresh produce and other regional specialties. This not only meets customer preferences but also reduces transportation costs and supports local economies. They may also implement temperature-controlled transportation for optimal freshness.
- Sustainability Initiatives: Environmental concerns are driving changes in the food industry. US Foods embraces sustainability through various initiatives, including reducing food waste, minimizing packaging, and optimizing transportation routes to lower carbon emissions. They may also invest in energy-efficient equipment and explore renewable energy sources.
- Technology Integration: Leveraging technology to enhance efficiency and customer service is crucial. US Foods utilizes data analytics to optimize inventory management, predict demand, and improve delivery routes. They also implement technologies like warehouse management systems (WMS) and transportation management systems (TMS) to streamline operations.
Impact of E-commerce and Online Ordering
The rise of e-commerce and online ordering has significantly impacted distribution centers, necessitating changes in infrastructure, processes, and technology.
- Increased Order Volume and Complexity: Online ordering leads to a higher volume of smaller, more frequent orders, increasing the complexity of order fulfillment. Distribution centers must adapt their processes to handle these changes efficiently. US Foods invests in automated picking and packing systems to handle increased order volumes.
- Faster Delivery Times: Customers expect faster delivery times, requiring distribution centers to optimize their delivery routes and improve their logistics. US Foods leverages technology to streamline delivery processes, including real-time tracking and optimized routing software.
- Last-Mile Delivery Challenges: Last-mile delivery, the final leg of the delivery process, presents unique challenges, including navigating urban areas and meeting specific delivery requirements. US Foods collaborates with delivery partners and optimizes delivery routes to overcome these challenges.
- Inventory Management and Accuracy: Accurate inventory management is crucial to fulfill online orders efficiently. US Foods uses real-time inventory tracking systems and automated processes to ensure accuracy. They may also implement strategies such as “just-in-time” inventory management to reduce waste and improve efficiency.
Future Trends in Food Distribution, Us foods distribution centers
Several emerging trends are poised to transform the food distribution landscape. These trends involve advancements in automation, robotics, and other innovative technologies.
- Automation and Robotics: Automation and robotics are playing an increasingly significant role in distribution centers. Robots can perform tasks such as picking, packing, and palletizing, improving efficiency and reducing labor costs. US Foods is actively investing in automation technologies to streamline operations.
- Artificial Intelligence (AI) and Machine Learning (ML): AI and ML are used to optimize various aspects of distribution center operations, including demand forecasting, inventory management, and route optimization. These technologies help improve efficiency and reduce costs. US Foods uses AI to analyze data and improve forecasting accuracy.
- Blockchain Technology: Blockchain technology can enhance traceability and transparency in the food supply chain, improving food safety and reducing the risk of contamination. US Foods is exploring the use of blockchain to track products from origin to delivery.
- Data Analytics and Predictive Modeling: Data analytics and predictive modeling are used to optimize operations, predict demand, and improve decision-making. US Foods leverages data analytics to optimize inventory management, predict demand, and improve delivery routes.
Potential Innovations in Distribution Center Design and Operations
The design and operation of distribution centers are evolving to accommodate new technologies and changing market demands.
- Automated Guided Vehicles (AGVs) and Autonomous Mobile Robots (AMRs): AGVs and AMRs are used to transport goods within distribution centers, improving efficiency and reducing labor costs. These robots can navigate autonomously and perform tasks such as picking and packing. US Foods can implement these technologies to streamline operations.
- Vertical Warehousing: Vertical warehousing maximizes space utilization by stacking storage units vertically. This approach can reduce the footprint of distribution centers and increase storage capacity.
- Automated Storage and Retrieval Systems (AS/RS): AS/RS systems automate the storage and retrieval of goods, improving efficiency and reducing labor costs. These systems can handle a large volume of products and improve order fulfillment times.
- Micro-Fulfillment Centers: Micro-fulfillment centers are smaller, localized distribution centers that are located closer to customers. This approach can reduce delivery times and improve customer satisfaction. US Foods could establish micro-fulfillment centers in urban areas to improve delivery efficiency.
Ultimate Conclusion
In conclusion, US Foods distribution centers are complex ecosystems that play a crucial role in the food industry. From advanced technology to stringent safety protocols and sustainable practices, these centers are constantly evolving to meet the demands of a dynamic market. Understanding these centers is essential for anyone involved in the foodservice industry, and this overview provides a solid foundation for further exploration.