Hormel Foods Beloit WI represents a significant presence in the food industry, offering a fascinating case study of production, community engagement, and economic influence. This exploration delves into the history of the facility, its manufacturing processes, and its impact on the local community. From its establishment to its current operations, the story of Hormel Foods in Beloit is one of growth, adaptation, and a commitment to quality.
We will examine the diverse product portfolio manufactured at the Beloit plant, its production methods, and its role in the broader Hormel Foods network. Furthermore, the discussion will encompass the company’s commitment to sustainability, community involvement, and the employment opportunities it provides. This analysis aims to provide a comprehensive overview of Hormel Foods’ operations in Beloit, WI.
Hormel Foods Presence in Beloit, WI
Hormel Foods’ operations in Beloit, Wisconsin, represent a significant chapter in the company’s history and a vital component of the local economy. The facility’s presence has evolved over decades, impacting the community through job creation, economic contributions, and various forms of civic engagement. This section will delve into the specifics of Hormel’s footprint in Beloit.
Finish your research with information from food midlothian tx.
History of Operations in Beloit, WI
Hormel Foods’ journey in Beloit began in 1959 with the establishment of a meat processing plant. Over the years, the facility has undergone significant expansions to accommodate increasing production demands and technological advancements.
- Initial Establishment: The Beloit plant was established in 1959, marking the beginning of Hormel’s presence in the city. This initial investment laid the groundwork for future growth.
- Expansion and Modernization: Throughout the following decades, the Beloit facility experienced several expansions. These included additions to production lines, upgrades to processing equipment, and enhancements to storage and distribution capabilities. The goal was to keep pace with the growing demand for Hormel products and to incorporate the latest industry standards.
- Current Operations: Today, the Beloit plant remains a key Hormel Foods location, continuing to produce a variety of meat products. The facility’s ongoing operations reflect Hormel’s commitment to the region.
Products Manufactured or Processed at the Beloit Facility
The Beloit plant is responsible for producing a range of meat products, contributing significantly to Hormel’s overall product portfolio.
- Key Product Lines: The Beloit facility primarily focuses on processing and packaging a variety of meat products. These typically include items like ham, bacon, and other pork-based products. The specific product mix can fluctuate based on market demand and consumer preferences.
- Processing and Packaging: The plant utilizes advanced processing and packaging technologies to ensure product quality, safety, and shelf life. The processes encompass everything from initial meat preparation to final packaging and labeling.
- Distribution: Products manufactured at the Beloit facility are distributed through Hormel’s extensive distribution network, reaching retail outlets and foodservice providers across the United States.
Economic Impact of Hormel Foods on Beloit, WI
Hormel Foods has a substantial economic impact on Beloit, contributing to job creation, tax revenue, and community involvement.
- Job Creation: The Beloit plant is a significant employer in the region, providing numerous jobs for local residents. These positions range from production and processing roles to administrative and management positions. This employment base contributes to the economic stability of the community.
- Tax Revenue: Hormel’s operations generate tax revenue for the city and county, supporting public services and infrastructure improvements. These tax contributions are a crucial element in the financial health of the local government.
- Community Involvement: Hormel Foods is known for its community involvement, which includes charitable donations, sponsorships, and employee volunteer programs. These activities enhance the quality of life in Beloit and demonstrate the company’s commitment to the community. For example, Hormel may support local food banks or sponsor youth sports teams.
Production Processes and Technologies
The Hormel Foods plant in Beloit, Wisconsin, employs a variety of sophisticated production methods to transform raw materials into a diverse range of food products. These processes are designed to maximize efficiency, maintain product quality, and ensure food safety. The facility integrates advanced technologies to streamline operations and meet the demands of a competitive market.
Specific Production Methods
The Beloit facility utilizes a combination of established and innovative production techniques. These methods are carefully chosen based on the specific product being manufactured. The plant is equipped with advanced machinery, including automated processing lines, sophisticated packaging equipment, and integrated control systems. This automation minimizes manual handling, reduces the risk of contamination, and ensures consistent product quality. Specific examples include high-speed slicing machines, automated cooking and chilling systems, and advanced blending technologies.
Product Journey: Raw Materials to Packaging
A typical product’s journey through the Beloit plant involves several key stages, each meticulously controlled to guarantee quality and safety. The following bullet points detail this process:
- Raw Material Receiving and Inspection: Upon arrival, raw materials, such as meat, spices, and packaging materials, undergo rigorous inspection. This includes visual examination, temperature checks, and laboratory testing to ensure they meet Hormel’s stringent quality standards. Any materials failing to meet these standards are rejected.
- Preparation and Processing: The raw materials are then prepared for processing. This may involve trimming, grinding, blending, or other preparation steps. The specific processing method depends on the final product. For example, meat may be seasoned, cooked, and then formed into specific shapes.
- Cooking and Formulation: Products requiring cooking, such as sausages or hams, are cooked using precisely controlled temperature and time parameters. Advanced cooking systems ensure uniform cooking and enhance product safety. Formulations, including the addition of spices, seasonings, and other ingredients, are precisely measured and mixed to maintain the desired taste and texture.
- Packaging: Once processed, the product is packaged using advanced packaging equipment. This includes automated filling, sealing, and labeling systems. Packaging materials are selected to preserve the product’s freshness, protect it from damage, and provide important consumer information.
- Quality Control Checks: Throughout the production process, products undergo multiple quality control checks. These checks verify product dimensions, weights, appearance, and internal temperatures.
- Storage and Distribution: Packaged products are stored in climate-controlled warehouses to maintain their quality and safety. From there, they are distributed to retailers and foodservice customers.
Quality Control Measures
Quality control is paramount at the Beloit facility, with comprehensive measures implemented throughout the production process. These measures ensure product safety, consistency, and compliance with all relevant regulations.
- HACCP System: The plant operates under a Hazard Analysis and Critical Control Points (HACCP) system. This science-based approach identifies potential hazards in the food production process and establishes critical control points (CCPs) to prevent or minimize those hazards. CCPs are monitored and controlled to ensure food safety.
- Regular Inspections and Audits: The facility undergoes regular inspections and audits by both internal and external regulatory bodies. These audits assess compliance with food safety regulations and quality standards.
- Laboratory Testing: Products and raw materials are routinely tested in on-site laboratories. These tests include microbiological analysis to detect potential pathogens, chemical analysis to verify ingredient composition, and sensory evaluations to assess taste, texture, and appearance.
- Employee Training: All employees receive comprehensive training in food safety and quality control procedures. This training ensures that everyone understands their role in maintaining product safety and quality.
- Traceability Systems: The plant utilizes robust traceability systems to track products throughout the supply chain. This allows for rapid identification and removal of any potentially unsafe products from the market if necessary.
- Continuous Improvement: Hormel Foods is committed to continuous improvement in its quality control processes. This includes regular reviews of procedures, implementation of new technologies, and ongoing employee training.
Product Portfolio and Brands
Hormel Foods’ Beloit, Wisconsin, facility plays a crucial role in the company’s overall manufacturing network. This section will delve into the specific brands and products manufactured at this plant, providing insights into the scale of operations and the variety of offerings produced. The information presented is based on publicly available data and industry reports.
Specific Products and Production Volume, Hormel foods beloit wi
The Beloit plant primarily focuses on producing a variety of meat products, contributing significantly to Hormel’s diverse portfolio. While specific production volumes are often proprietary, it’s possible to infer the scale of operations through industry reports and company statements. The Beloit facility is considered a significant production hub within the Hormel network.
The plant likely handles substantial quantities, given the size and scope of Hormel Foods’ operations.
Based on publicly available information, the Beloit plant is expected to be a large-scale operation.
Hormel Foods’ annual reports often provide insights into overall production and sales figures, which can indirectly reflect the significance of plants like the one in Beloit.
Product Lines, Ingredients, and Packaging
The Beloit facility manufactures a range of products. The table below details some of the product lines, typical ingredients, and packaging types associated with production at the plant.
Product Line | Typical Ingredients | Packaging Types | Notes |
---|---|---|---|
Processed Meats (e.g., hams, sausages) | Pork, seasonings, curing agents (nitrates/nitrites), water, binders, flavorings | Vacuum-sealed packaging, plastic casings, modified atmosphere packaging (MAP), bulk packaging | Product formulations can vary based on the specific product and brand. |
Ready-to-Eat Meals (e.g., microwaveable entrees) | Meat, vegetables, sauces, grains (rice, pasta), preservatives, flavorings | Microwaveable trays (plastic), film sealing, cardboard sleeves, multi-compartment packaging | Ingredient lists are extensive and vary depending on the specific meal. |
Meat Snacks (e.g., pepperoni, dried meat sticks) | Meat (beef, pork, or a combination), spices, salt, curing agents, sugar, flavorings | Flexible film packaging (e.g., pouches), individual serving sizes, multi-packs | Shelf-stable products designed for convenience. |
Bacon | Pork belly, salt, sugar, curing agents, flavorings, preservatives | Vacuum-sealed packaging, stackable trays, pre-cooked options in various packaging formats | Packaging designed to maintain freshness and extend shelf life. |
Community and Corporate Social Responsibility
Hormel Foods demonstrates a strong commitment to corporate social responsibility, particularly within the Beloit, WI, community. This commitment is evident through various philanthropic endeavors, partnerships, and sustainability initiatives. The company’s actions reflect a dedication to not only producing high-quality food products but also contributing positively to the well-being of the local area and the environment.
Community Involvement and Philanthropic Activities
Hormel Foods actively engages with the Beloit community through various philanthropic programs and partnerships. These efforts aim to address local needs and support initiatives that enhance the quality of life for residents.
- Food Bank Donations: Hormel Foods regularly donates food products to local food banks and pantries in Beloit. This provides essential resources to individuals and families facing food insecurity. This is a practical application of the company’s core product, helping to feed those in need.
- Educational Support: The company supports educational programs and initiatives in Beloit, often through financial contributions or volunteer efforts. This may include sponsoring school events, providing scholarships, or partnering with educational institutions to promote learning and development.
- Community Events: Hormel Foods participates in and sponsors various community events in Beloit, such as festivals, fundraisers, and charity drives. This helps foster a sense of community and demonstrates the company’s commitment to being an active and engaged member of the local area.
- Employee Volunteerism: Hormel Foods encourages and supports employee volunteerism. Employees are often given opportunities to volunteer their time and skills to support local charities and community projects, further strengthening the company’s community ties.
Sustainability Initiatives at the Beloit Facility
Hormel Foods has implemented several sustainability initiatives at its Beloit facility to reduce its environmental impact and promote responsible operations. These initiatives focus on waste reduction, energy efficiency, and resource conservation.
- Waste Reduction Programs: The Beloit facility has implemented comprehensive waste reduction programs. This includes recycling initiatives, composting programs, and efforts to minimize packaging waste. The goal is to divert waste from landfills and reduce the environmental footprint of the facility.
- Energy Efficiency Measures: Hormel Foods has invested in energy-efficient technologies and practices at the Beloit facility. This includes upgrading equipment to be more energy-efficient, implementing energy management systems, and optimizing operational processes to reduce energy consumption.
- Water Conservation: Water conservation is another key area of focus. The facility employs water-efficient technologies and practices to minimize water usage in its operations. This may include water recycling systems, efficient cleaning processes, and leak detection programs.
- Sustainable Sourcing: Hormel Foods is committed to sustainable sourcing practices. This involves working with suppliers who adhere to environmentally responsible practices and sourcing ingredients from sustainable sources whenever possible. This helps ensure the long-term viability of the food supply chain.
Awards and Recognition
Hormel Foods has received recognition for its operations and community contributions in Beloit, WI. These accolades highlight the company’s commitment to excellence and its positive impact on the local community.
- Safety Awards: The Beloit facility has been recognized for its commitment to workplace safety. This includes awards for maintaining a safe working environment and implementing effective safety programs.
- Community Service Awards: Hormel Foods has received awards and recognition for its community involvement and philanthropic efforts in Beloit. These awards acknowledge the company’s contributions to local charities, educational institutions, and community events.
- Sustainability Awards: The company may have received awards for its sustainability initiatives, such as waste reduction, energy efficiency, and water conservation. These awards recognize Hormel Foods’ commitment to environmental stewardship and responsible business practices.
Supply Chain and Logistics
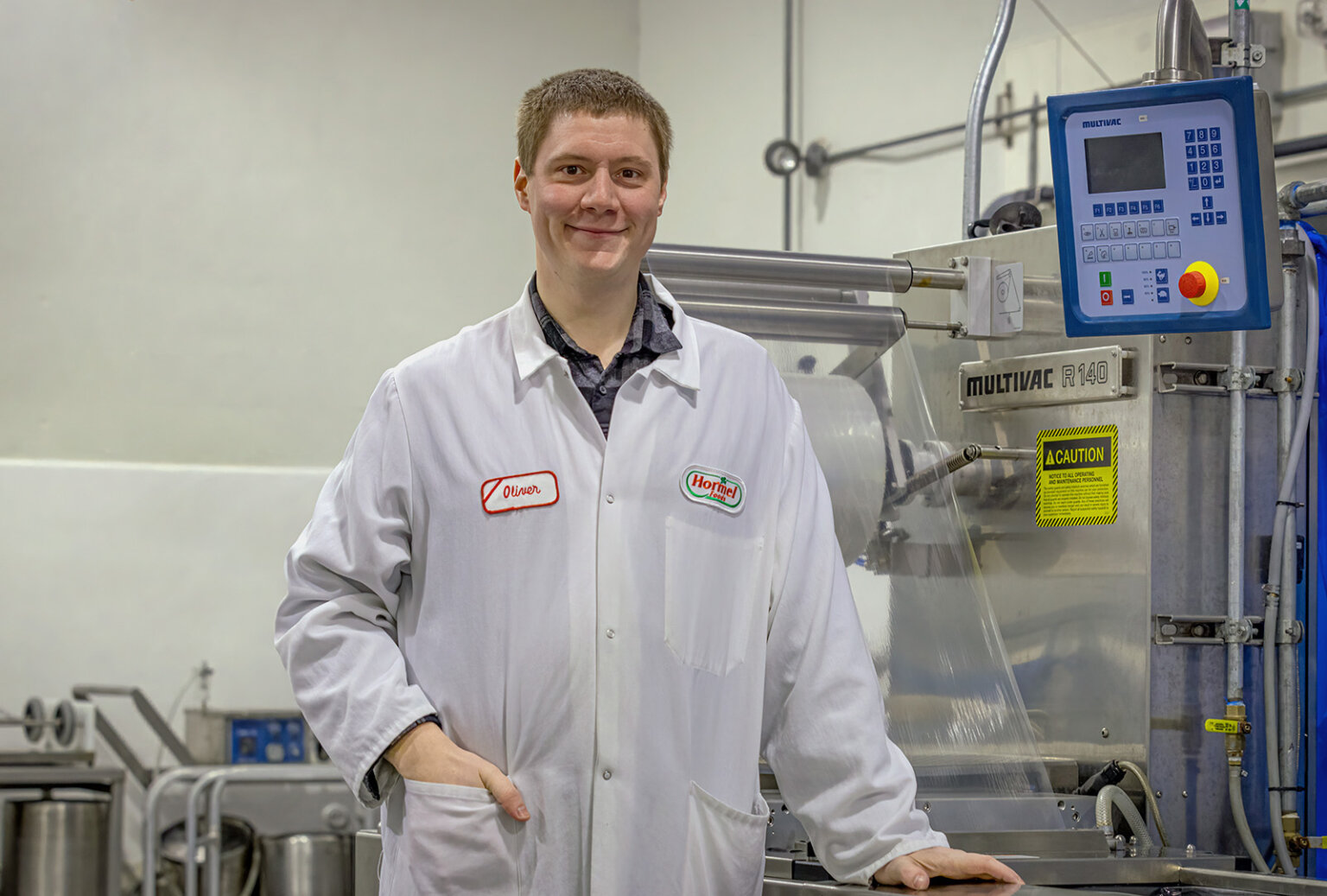
The efficient movement of raw materials into the Beloit facility and the distribution of finished products to consumers are critical for Hormel Foods’ success. This section Artikels the intricate supply chain network and logistics operations that support the Beloit, WI, plant.
Raw Material and Ingredient Supply Chain
Hormel Foods relies on a complex supply chain to ensure a consistent flow of raw materials and ingredients to its Beloit facility. This network is designed to maintain product quality, manage costs, and mitigate risks.
- Sourcing of Raw Materials: The primary raw materials include pork, beef, and poultry, sourced from various suppliers across the United States. Hormel Foods has established relationships with farmers and processors, often employing long-term contracts to secure supply and maintain consistent quality. These relationships also incorporate sustainability practices, ensuring ethical and environmentally responsible sourcing.
- Ingredient Procurement: A wide array of ingredients, such as spices, seasonings, packaging materials, and other additives, are sourced from a global network of suppliers. Hormel Foods prioritizes suppliers who meet stringent quality standards, adhere to food safety regulations, and offer competitive pricing.
- Transportation and Logistics: Raw materials and ingredients are transported to the Beloit facility using a combination of transportation modes, including:
- Trucking: Primarily used for shorter distances and delivering goods directly to the plant.
- Rail: Employed for longer distances and bulk shipments, offering cost-effectiveness and efficiency.
The company utilizes advanced logistics systems to track shipments, manage inventory, and optimize delivery schedules, minimizing storage costs and potential disruptions.
- Inventory Management: The Beloit facility employs sophisticated inventory management techniques, such as just-in-time (JIT) inventory, to minimize storage costs and ensure the availability of necessary materials. These systems are integrated with supplier networks, providing real-time visibility into inventory levels and demand forecasts.
Logistics and Distribution of Finished Products
The distribution of finished products from the Beloit plant to various markets involves a comprehensive logistics network designed to preserve product quality and ensure timely delivery.
- Warehousing: Finished products are stored in temperature-controlled warehouses at the Beloit facility, designed to maintain the integrity and freshness of the food products.
- Distribution Channels: Hormel Foods utilizes a multi-channel distribution strategy, reaching consumers through various outlets:
- Retail: Products are distributed to grocery stores, supermarkets, and other retail outlets through direct distribution networks and third-party logistics providers.
- Foodservice: Hormel Foods supplies products to restaurants, cafeterias, and other foodservice establishments.
- E-commerce: Products are available for online purchase through the company’s website and other e-commerce platforms.
- Transportation Methods: Finished products are transported using refrigerated trucks, railcars, and intermodal shipping containers to maintain product quality and meet delivery requirements. The selection of transportation modes depends on factors such as distance, volume, and the specific product.
- Temperature Control: Maintaining the proper temperature is crucial for the safety and quality of Hormel Foods products. Refrigerated trucks and warehouses are used throughout the distribution process to ensure products remain within the required temperature range.
- Tracking and Traceability: Hormel Foods employs advanced tracking and traceability systems to monitor the movement of products from the Beloit facility to their final destinations. This enables the company to respond quickly to any issues and ensure product safety.
Comparison of Distribution Strategies
Hormel Foods employs a standardized approach to distribution across its various facilities, including the Beloit, WI, plant. However, there are some nuances based on the specific products manufactured at each location and the geographic markets served.
- Centralized Distribution Network: Hormel Foods utilizes a centralized distribution network, which leverages economies of scale and optimizes logistics operations. This approach ensures consistent service levels and reduces distribution costs.
- Regional Distribution Centers: Products from the Beloit facility are often routed through regional distribution centers to serve specific geographic markets. This allows for faster delivery times and reduces transportation costs.
- Product-Specific Strategies: The distribution strategy may vary based on the type of product. For example, refrigerated products require specialized transportation and handling, while shelf-stable products may have different distribution requirements.
- Market-Specific Strategies: Distribution strategies are tailored to meet the needs of specific markets. This may involve adapting packaging, labeling, and delivery methods to comply with local regulations and consumer preferences.
- Integration of Technology: Hormel Foods utilizes advanced technology, such as enterprise resource planning (ERP) systems and transportation management systems (TMS), to optimize its distribution network and improve efficiency. These systems provide real-time visibility into inventory levels, shipment tracking, and delivery schedules.
Regulatory Compliance and Safety
Hormel Foods maintains a steadfast commitment to regulatory compliance and the safety of its employees and products at its Beloit, WI facility. This commitment is paramount, ensuring the production of safe, high-quality food products and a secure working environment. The following sections detail the specific measures and protocols in place to uphold these standards.
Food Safety Standards Adherence
Hormel Foods’ Beloit facility strictly adheres to all applicable food safety regulations. This includes compliance with standards set forth by the Food and Drug Administration (FDA) and the United States Department of Agriculture (USDA), depending on the specific products manufactured at the plant. These regulations encompass various aspects of food production, from ingredient sourcing and handling to processing, packaging, and distribution.
- Hazard Analysis and Critical Control Points (HACCP) Implementation: Hormel Foods utilizes the HACCP system, a science-based approach to food safety, to identify and control potential hazards throughout the production process. This involves:
- Conducting a hazard analysis to identify potential biological, chemical, and physical hazards.
- Determining Critical Control Points (CCPs), points in the process where control is essential to prevent or eliminate a food safety hazard.
- Establishing critical limits for each CCP.
- Implementing monitoring procedures to ensure CCPs are under control.
- Establishing corrective actions to be taken when critical limits are not met.
- Verifying the effectiveness of the HACCP plan.
- Maintaining detailed records of all aspects of the HACCP plan.
- Good Manufacturing Practices (GMPs) Compliance: The facility adheres to GMPs, which are foundational to food safety. These practices cover a wide range of operational aspects, including:
- Personnel hygiene, such as handwashing and the use of appropriate protective clothing.
- Building and facility maintenance to prevent contamination.
- Equipment maintenance and sanitation.
- Control of ingredients and packaging materials.
- Proper labeling and traceability.
- Ingredient and Supplier Control: Hormel Foods maintains rigorous standards for its ingredients and suppliers. This includes:
- Approved Supplier Programs: Only suppliers that meet Hormel Foods’ stringent quality and safety standards are approved.
- Ingredient Verification: Ingredients are thoroughly inspected and tested to ensure they meet specifications and are free from contaminants.
- Traceability Systems: Comprehensive traceability systems are in place to track ingredients from their source to the finished product, enabling rapid identification and recall of products if necessary.
Safety Protocols and Procedures for Employees
The Beloit facility prioritizes employee safety through a comprehensive safety program. This program encompasses various measures to prevent workplace injuries and illnesses.
- Personal Protective Equipment (PPE): Employees are provided with and required to use appropriate PPE, including:
- Safety glasses or goggles.
- Hearing protection.
- Gloves.
- Protective footwear.
- Other specialized PPE as required by specific job tasks.
- Machine Guarding: All machinery is equipped with appropriate guards to prevent contact with moving parts. Regular inspections are conducted to ensure guards are in place and functioning correctly.
- Lockout/Tagout Procedures: Lockout/Tagout (LOTO) procedures are strictly followed during maintenance and repair activities to prevent accidental startup of machinery. This involves:
- Identifying the energy source.
- Isolating the energy source.
- Applying locks and tags to prevent activation.
- Verifying the isolation.
- Hazard Communication: Employees are trained on the hazards of chemicals used in the facility and provided with access to Safety Data Sheets (SDS).
- Ergonomics Program: An ergonomics program is in place to assess and mitigate ergonomic hazards, such as repetitive motions and awkward postures, to prevent musculoskeletal disorders.
- Emergency Response Plan: A comprehensive emergency response plan is in place to address potential emergencies, including:
- Fire.
- Medical emergencies.
- Chemical spills.
- Natural disasters.
Regular drills are conducted to ensure employees are familiar with emergency procedures.
- Safety Training: All employees receive comprehensive safety training, including:
- General safety awareness.
- Job-specific safety training.
- Regular refresher training.
Inspections and Audits at the Beloit Facility
The Beloit facility undergoes regular inspections and audits to ensure compliance with food safety and safety regulations. These assessments are conducted by both internal and external parties.
- Internal Audits: Hormel Foods conducts regular internal audits of its food safety and safety programs. These audits are performed by trained personnel and cover all aspects of the operation.
- Third-Party Audits: The facility is subject to audits by third-party organizations, such as:
- Food safety certification bodies (e.g., Safe Quality Food (SQF), British Retail Consortium (BRC)).
- Regulatory agencies (e.g., FDA, USDA).
- Regulatory Inspections: The FDA and USDA regularly inspect the facility to ensure compliance with food safety regulations. These inspections typically involve:
- Reviewing records.
- Observing production processes.
- Collecting samples for testing.
- Audit Outcomes and Corrective Actions:
- Any deficiencies identified during inspections or audits are documented and addressed through corrective actions.
- Corrective actions may include:
- Implementing new procedures.
- Providing additional training.
- Making modifications to equipment or facilities.
- Follow-up audits are conducted to verify that corrective actions have been implemented effectively.
Historical Events and Milestones
Hormel Foods’ presence in Beloit, Wisconsin, has a rich history marked by significant events and developments that have shaped its operations and contributions to the community. This section delves into the key historical moments, expansions, and changes that have defined Hormel’s footprint in Beloit.
Early Establishment and Initial Operations
The initial establishment of Hormel Foods in Beloit, Wisconsin, marked a pivotal moment in the company’s expansion and its commitment to the region.
- Early 20th Century: While specific dates of initial operations may vary depending on the source, Hormel Foods’ presence in Beloit began in the early 20th century. The exact year of establishment would require additional research from primary historical documents or company archives.
- Strategic Location: Beloit’s location, likely chosen for its proximity to transportation networks and agricultural resources, was crucial for the efficient sourcing of raw materials and distribution of finished products.
- Initial Focus: The early operations likely focused on producing and processing meat products, aligning with Hormel’s core business at the time.
Major Expansions and Investments
Over the years, Hormel Foods has made significant investments in its Beloit facility, expanding its capacity and capabilities to meet growing demand and incorporate new technologies. These expansions reflect the company’s long-term commitment to the area.
- Mid-20th Century Expansion: Expansion projects during the mid-20th century likely involved increasing production capacity and modernizing facilities to accommodate new product lines and processing techniques.
- Technological Upgrades: Investments in advanced technologies, such as automated processing systems and refrigeration, would have improved efficiency and product quality.
- Late 20th and Early 21st Century Investments: Continued investments in the late 20th and early 21st centuries focused on further automation, sustainability initiatives, and expanding the product portfolio to meet changing consumer preferences. This may have included the introduction of new product lines and packaging technologies.
Changes in Ownership and Management
Throughout its history in Beloit, the Hormel facility has experienced changes in management and ownership, reflecting broader corporate restructuring and market dynamics.
- Corporate Restructuring: Corporate restructuring initiatives, such as mergers, acquisitions, and reorganizations, have influenced the management and operational structure of the Beloit facility.
- Leadership Transitions: Leadership changes within the company have likely led to shifts in strategic direction and operational priorities at the Beloit plant.
- Impact on Local Operations: These changes have the potential to impact local employment, community involvement, and the overall operational focus of the Beloit facility.
Timeline of Key Dates and Events
The following timeline highlights key dates and events in the history of Hormel Foods in Beloit, WI. Please note that some specific dates may require further research and verification from primary sources.
- Early 20th Century: Establishment of Hormel Foods operations in Beloit, WI. Exact year needs to be verified.
- Mid-20th Century: Major expansion and modernization of the Beloit facility. Specific dates need to be verified.
- Late 20th Century: Further investments in technology and production capacity. Specific dates and details of these investments would need to be verified through company records or historical archives.
- Early 21st Century: Continued investment in automation, sustainability, and product diversification. Details of these initiatives should be found in company reports or public announcements.
- Present Day: Ongoing operations, with a focus on efficiency, sustainability, and community engagement.
Concluding Remarks: Hormel Foods Beloit Wi
In conclusion, Hormel Foods Beloit WI exemplifies the multifaceted nature of a modern food processing facility. Its contributions extend beyond product manufacturing, encompassing economic development, community support, and a dedication to sustainable practices. The facility’s continued success underscores the importance of adapting to evolving market demands while maintaining a strong commitment to quality, safety, and the well-being of its workforce and the surrounding community.