Food safe epoxy for ceramics is a fascinating topic, opening doors to a world where artistry meets practicality. This guide delves into the intricacies of using epoxy resins to enhance and protect ceramic pieces intended for food contact. We’ll explore what makes an epoxy food-safe, examining its compatibility with various ceramic types and the essential application techniques.
From understanding certifications and standards to mastering application methods and ensuring proper curing, we’ll equip you with the knowledge to confidently utilize food-safe epoxy. We will also consider common uses, maintenance, and troubleshooting, ensuring a complete understanding of this versatile material. Let’s dive in to discover how to transform your ceramic creations into safe and beautiful functional pieces.
Defining “Food Safe Epoxy for Ceramics”
Food safe epoxy for ceramics refers to a specific type of epoxy resin formulation designed to be used in direct contact with food items without leaching harmful chemicals or compromising food safety. These epoxies are typically used to repair, seal, or create ceramic items intended for food consumption, such as plates, bowls, and mugs. The selection of the right epoxy is crucial, as not all epoxy resins are suitable for this purpose.
Characteristics of Food Safe Epoxy Resins
Several characteristics distinguish food-safe epoxy resins from standard epoxy formulations. These properties are essential to ensure the safety of the food and the user.
- Non-Toxicity: Food-safe epoxies are formulated using ingredients that are inherently non-toxic and do not release harmful substances into food. This includes the resin, hardener, and any additives.
- Low Volatile Organic Compound (VOC) Content: These epoxies typically have a low or zero VOC content. This minimizes the release of fumes during application and curing, ensuring the final product is safe.
- Chemical Resistance: The cured epoxy must resist degradation from contact with various food items, including acids, bases, and solvents. This prevents the epoxy from breaking down and contaminating the food.
- Heat Resistance: Food-safe epoxies should withstand the temperatures encountered during normal food use, such as hot beverages or microwave heating, without degrading or releasing chemicals. The specific temperature resistance varies depending on the formulation.
- Cure Completeness: The epoxy must cure completely to eliminate the presence of uncured components, which could be harmful. The curing process and time must be strictly followed.
Comparison of Epoxy Resin Formulations for Ceramic Applications
Various epoxy resin formulations are available, each with its characteristics suitable for specific applications in ceramics. The selection depends on factors like desired finish, application method, and specific food contact requirements.
- Clear Epoxy Resins: These resins are popular for their transparency, allowing the ceramic’s original appearance to be preserved. They are often used for coating or sealing. They are usually available with varying viscosities.
- Colored Epoxy Resins: These resins include pigments to add color to the ceramic project. They are used for decorative purposes, repairs, or creating unique designs. Pigments must also be food-safe.
- High-Viscosity Epoxy Resins: These are suitable for applications where a thicker consistency is required, such as filling cracks or creating raised designs. They often require careful application to avoid air bubbles.
- Low-Viscosity Epoxy Resins: These resins are more fluid and suitable for coating or sealing applications where penetration into small cracks or pores is necessary. They may require multiple coats to achieve the desired thickness.
Critical Certifications and Standards for Food Safety
Food-safe epoxy resins must meet specific certifications and standards to ensure they are safe for food contact. These standards are set by regulatory bodies and organizations that govern food safety.
- FDA Compliance (U.S. Food and Drug Administration): This is a crucial standard. Epoxy resins must comply with FDA regulations, particularly 21 CFR 175.300, which Artikels the requirements for resinous and polymeric coatings used as a food-contact surface. Compliance ensures that the epoxy’s components and any additives are safe for food contact and do not migrate into food items in harmful amounts.
- EU Regulations (European Union): In the EU, food-contact materials are regulated under various directives and regulations, including Regulation (EC) No 1935/2004. Epoxy resins used in the EU must comply with these regulations, which specify the allowed substances and migration limits for food-contact materials.
- Migration Testing: Food-safe epoxies undergo migration testing to ensure that no harmful substances migrate from the cured epoxy into food. These tests simulate the conditions the epoxy will be exposed to, such as contact with different food types and temperatures. The results of these tests demonstrate the safety of the epoxy.
- Third-Party Certifications: Certifications from independent organizations, such as NSF International, provide additional assurance of food safety. NSF certification involves rigorous testing and audits to verify that the epoxy meets specific standards.
Ceramic Materials Compatibility
Understanding the interaction between food-safe epoxy and various ceramic materials is crucial for ensuring both the aesthetic appeal and the safety of the final product. The type of ceramic significantly impacts the epoxy’s performance and the overall suitability for food contact. This section delves into the compatibility of epoxy with different ceramic types, addressing potential challenges and offering insights for optimal application.
Common Ceramic Types and Compatibility
Different ceramic materials exhibit varying properties that affect their interaction with epoxy. These properties include porosity, density, and the presence of surface coatings or glazes.
- Earthenware: Earthenware is a relatively porous ceramic, typically fired at lower temperatures. This porosity can pose a challenge, as it allows the epoxy to penetrate the ceramic, potentially leading to uneven curing and increased epoxy consumption. However, food-safe epoxy can effectively seal earthenware, making it suitable for food contact when properly applied. For example, consider a handmade earthenware bowl; applying a food-safe epoxy coating on the interior can create a smooth, non-porous surface that is safe for serving food.
- Stoneware: Stoneware is fired at higher temperatures than earthenware, resulting in a denser and less porous material. This increased density makes stoneware generally more compatible with epoxy, leading to better adhesion and reduced epoxy absorption. A stoneware mug, for instance, is a good candidate for epoxy application, as the epoxy will adhere well to the surface and create a durable, food-safe finish.
- Porcelain: Porcelain is fired at the highest temperatures, making it the densest and least porous of the common ceramic types. Its smooth, non-porous surface provides an excellent base for epoxy application. Porcelain’s high density typically leads to superior adhesion and a flawless finish. Think of porcelain dinner plates; a well-applied epoxy coating will create a virtually impermeable barrier, ensuring food safety and ease of cleaning.
Addressing Porosity in Ceramics
Porosity is a critical factor when considering epoxy application on ceramics. The degree of porosity varies between ceramic types, with earthenware being the most porous and porcelain the least. This characteristic directly influences how the epoxy interacts with the ceramic surface.
- Impact of Porosity: Porous ceramics can absorb epoxy, leading to increased epoxy usage, uneven curing, and potentially weaker bonds. The absorbed epoxy might also trap air, causing bubbles or imperfections in the final finish.
- Mitigating Porosity: Several strategies can address porosity. Pre-sealing the ceramic surface with a thin layer of epoxy can help to fill the pores before applying the main coat. Using a low-viscosity epoxy can also aid in penetration and sealing. Proper surface preparation, including cleaning and degreasing, is essential to ensure optimal adhesion.
- Examples: Consider a porous earthenware planter. Before applying a food-safe epoxy coating, applying a thin “sealer coat” helps fill the pores. This will result in a smoother, more durable, and waterproof finish compared to applying a single, thick coat directly to the porous surface. This is a common practice in ceramics restoration to ensure the epoxy is sealed properly.
Visual Guide: Epoxy and Ceramic Surface Interaction
The following table provides a visual representation of how epoxy interacts with different ceramic surfaces. It illustrates the impact of porosity and the resulting surface characteristics after epoxy application.
Ceramic Type | Porosity Level | Epoxy Interaction | Surface Characteristics after Epoxy Application |
---|---|---|---|
Earthenware | High | Epoxy penetrates the pores. Requires pre-sealing. | Smoother surface, reduced porosity, increased epoxy usage if not pre-sealed. Potential for some epoxy absorption. |
Stoneware | Medium | Epoxy adheres well, minimal penetration. | Smooth, durable surface, good adhesion, and minimal epoxy absorption. |
Porcelain | Low | Epoxy creates a strong bond, minimal penetration. | Smooth, glossy finish, excellent adhesion, and minimal epoxy absorption. |
Application Methods and Techniques
Applying food-safe epoxy to ceramic surfaces requires careful execution to ensure both safety and aesthetic appeal. The success of the application hinges on meticulous preparation, precise mixing, and the appropriate choice of application technique. This section provides a comprehensive guide to help you achieve optimal results.
Step-by-Step Guide for Applying Food-Safe Epoxy to Ceramic Surfaces
The following steps Artikel the process of applying food-safe epoxy, from initial preparation to the final curing stage. Each step is crucial for a successful and food-safe finish.
- Surface Preparation: This is the most critical step. Thoroughly clean the ceramic surface to remove any dust, grease, oils, or contaminants. Use a degreasing agent and ensure the surface is completely dry. Lightly sand the surface with fine-grit sandpaper (e.g., 220-grit) to create a slight texture for better epoxy adhesion. Clean again after sanding to remove sanding residue.
- Mixing the Epoxy: Precisely measure the epoxy resin and hardener according to the manufacturer’s instructions. Incorrect ratios can lead to improper curing and compromise the food-safe properties. Mix thoroughly for the specified time, typically 3-5 minutes, ensuring that you scrape the sides and bottom of the mixing container to incorporate all the components.
- Applying the Epoxy: Choose the appropriate application method based on the project. This could be brushing, pouring, or spreading. Apply the epoxy in thin, even coats to avoid air bubbles and ensure proper curing.
- Removing Air Bubbles: If bubbles appear, use a heat gun or a small torch, held a safe distance away from the surface, to gently heat the epoxy. This will help the bubbles rise to the surface and pop. Avoid overheating, which can cause the epoxy to yellow or cure improperly.
- Curing: Allow the epoxy to cure completely according to the manufacturer’s instructions. This typically takes several days. During the curing process, protect the surface from dust and debris.
- Inspection and Finishing: After curing, inspect the surface for any imperfections. If necessary, lightly sand and apply a second coat of epoxy. Once the final coat has cured, the surface can be considered food safe.
Detailed Procedure for Mixing Epoxy Resin and Hardener
Precise mixing is essential for the epoxy to cure correctly and achieve its intended properties. Following the manufacturer’s instructions meticulously is paramount. The following procedure ensures a consistent and reliable mix.
Further details about small food trucks for sale is accessible to provide you additional insights.
- Gather Materials: You will need epoxy resin, hardener, clean mixing containers (e.g., plastic cups), mixing sticks (e.g., wooden craft sticks), a measuring device (e.g., graduated cylinders or accurate scales), and protective gloves.
- Measure Accurately: Use the correct ratio of resin to hardener as specified by the manufacturer. This ratio is crucial for proper curing. Some epoxies are measured by volume, while others are by weight. Use the appropriate measuring method for your epoxy.
- Combine the Components: Pour the resin and hardener into the mixing container according to the measured amounts.
- Mix Thoroughly: Stir the mixture slowly and consistently for the recommended time, typically 3-5 minutes. Be sure to scrape the sides and bottom of the container to ensure all components are fully incorporated. Incomplete mixing can result in uncured or sticky spots.
- Check for Consistency: The mixture should appear clear and uniform after mixing. If you see streaks or cloudiness, continue mixing until the mixture is completely clear.
- Pot Life Awareness: Be aware of the epoxy’s pot life, which is the amount of time you have to work with the mixed epoxy before it starts to harden. Plan your application accordingly to avoid wasting material.
Demonstration of Different Application Techniques
Different application techniques are suitable for various projects. Each technique has its advantages and disadvantages. The choice of technique depends on the shape of the ceramic object, the desired finish, and the level of detail required.
- Brushing: This technique involves using a brush to apply the epoxy. It is suitable for smaller areas and intricate designs.
- Pros: Provides good control, allows for detailed work, and minimizes waste.
- Cons: Can leave brush strokes, may require multiple coats, and can be time-consuming for large surfaces.
- Example: Applying epoxy to a ceramic mug with a painted design. The brush allows the epoxy to be applied carefully to avoid smearing the design.
- Pouring: This technique involves pouring the epoxy directly onto the surface. It is suitable for creating a smooth, level finish.
- Pros: Creates a self-leveling surface, ideal for tabletops and large flat surfaces, and results in a smooth, glossy finish.
- Cons: Can be messy, requires careful leveling to avoid drips, and may trap air bubbles.
- Example: Coating a ceramic serving platter with a clear epoxy layer. The pouring technique ensures a perfectly flat and food-safe surface.
- Spreading: This technique involves using a spreader or squeegee to distribute the epoxy evenly across the surface.
- Pros: Efficient for large surfaces, minimizes air bubbles, and provides a consistent thickness.
- Cons: Requires practice to achieve an even finish, may not be suitable for complex shapes, and can be difficult to control.
- Example: Coating a ceramic tile backsplash. The spreading technique ensures a uniform and waterproof seal.
Curing and Safety Precautions
Ensuring the proper curing of food-safe epoxy and adhering to stringent safety protocols are paramount for the successful and safe application of this material on ceramic surfaces. The curing process dictates the final properties of the epoxy, including its food safety, while safety precautions protect the user from potential hazards. Both aspects require meticulous attention to detail for optimal results.
Curing Process Considerations
The curing process transforms liquid epoxy into a solid, durable material. This transformation is primarily driven by a chemical reaction between the resin and the hardener. Several environmental factors significantly influence this process, impacting the final properties and food safety compliance of the cured epoxy.Temperature plays a crucial role in the curing process. Generally, higher temperatures accelerate the reaction, leading to faster curing times.
Conversely, lower temperatures slow the reaction, potentially resulting in incomplete curing. It is essential to adhere to the manufacturer’s recommended temperature range for the specific epoxy product.Humidity also affects the curing process. High humidity can introduce moisture, which can interfere with the chemical reaction, leading to a weaker or less durable cured epoxy. This can compromise the food-safe properties of the epoxy.
Conversely, excessively dry environments can also affect the curing process, potentially leading to surface imperfections.Proper ventilation is crucial during curing. Epoxy emits fumes, and adequate airflow helps dissipate these fumes, improving air quality and safety. Ventilation also helps to regulate temperature and humidity, further optimizing the curing environment.Here are key considerations for the curing process:
- Temperature Range: Follow the manufacturer’s recommendations for the specific epoxy. A typical range is between 70°F (21°C) and 80°F (27°C). Temperatures outside this range can significantly affect curing time and final properties.
- Humidity Control: Aim for a relative humidity level between 40% and 60%. Use a dehumidifier or humidifier to maintain this range if necessary. High humidity can trap moisture, hindering the curing process.
- Curing Time: Curing times vary depending on the epoxy product and environmental conditions. Allow sufficient time for complete curing, typically several days, before exposing the coated ceramic to food. Refer to the manufacturer’s instructions for specific curing times.
- Ventilation: Ensure adequate ventilation during the curing process to remove fumes. This helps to maintain a consistent temperature and humidity environment.
Safety Precautions
Working with epoxy requires strict adherence to safety precautions to protect the user from potential hazards. Epoxy resins and hardeners can cause skin and eye irritation, and inhalation of fumes can be harmful. Proper personal protective equipment (PPE) and safe handling practices are essential.Personal Protective Equipment (PPE) is critical for safe epoxy application. This equipment creates a barrier between the user and the potentially hazardous materials.Here is a list of essential PPE:
- Gloves: Wear chemical-resistant gloves, such as nitrile or neoprene, to protect your skin from epoxy contact. Latex gloves are generally not recommended as they may not provide adequate protection.
- Eye Protection: Always wear safety glasses or goggles to protect your eyes from splashes and fumes.
- Respirator: In poorly ventilated areas, or when sanding or machining cured epoxy, use a respirator equipped with an organic vapor cartridge.
- Protective Clothing: Wear long sleeves and pants to protect your skin from contact with epoxy. Consider an apron or coveralls to protect clothing.
Safe handling practices are equally important:
- Ventilation: Work in a well-ventilated area to minimize exposure to fumes.
- Avoid Skin Contact: Prevent direct contact with epoxy. If contact occurs, immediately wash the affected area with soap and water. Do not use solvents to remove epoxy from the skin.
- Avoid Inhalation: Avoid breathing epoxy fumes. Use a respirator if necessary.
- Storage: Store epoxy products in a cool, dry place, away from direct sunlight and heat sources. Keep containers tightly closed.
- Disposal: Dispose of epoxy waste according to local regulations. Uncured epoxy should be treated as hazardous waste.
Avoiding Common Application Errors
Several common application errors can compromise the food safety of epoxy-coated ceramics. Avoiding these errors ensures the final product meets the necessary standards for safe food contact.Here are tips for avoiding common application errors:
- Improper Mixing: Thoroughly mix the resin and hardener according to the manufacturer’s instructions. Incomplete mixing can lead to uncured spots, compromising the epoxy’s integrity and food safety.
- Incorrect Ratios: Accurately measure the resin and hardener according to the specified ratio. Deviating from the recommended ratio can affect the curing process and final properties.
- Surface Contamination: Ensure the ceramic surface is clean, dry, and free of contaminants before applying epoxy. Contaminants can interfere with adhesion and create weak points in the coating.
- Air Bubbles: Minimize air bubbles by using a heat gun or torch to remove them. Trapped air bubbles can create voids, potentially harboring bacteria.
- Insufficient Curing Time: Allow the epoxy to cure completely according to the manufacturer’s instructions. Premature use can result in incomplete curing and potential food safety issues.
- Using Non-Food-Safe Epoxy: Always use epoxy specifically labeled as “food safe.” Other types of epoxy may contain chemicals that are not safe for food contact.
Common Uses and Applications
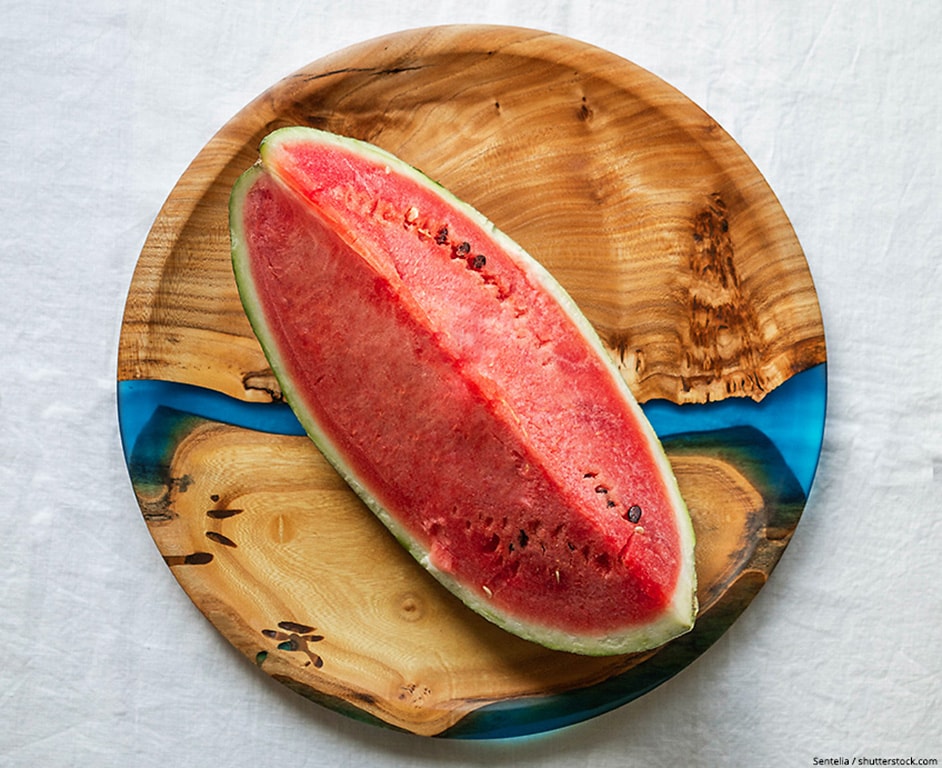
Food-safe epoxy for ceramics opens up a range of possibilities for creating and repairing ceramic items that come into contact with food. Its versatility makes it suitable for various applications, from functional tableware to decorative pieces. Understanding the common uses and limitations of this material is crucial for ensuring its safe and effective application.
Tableware and Utensils
Food-safe epoxy is frequently used in the repair and creation of tableware and utensils. This includes plates, bowls, mugs, and serving dishes.
- Repairing chipped or cracked ceramic plates: Epoxy can seamlessly fill in chips and cracks, restoring the plate’s functionality and aesthetic appeal. The repair is often nearly invisible once cured and polished.
- Sealing cracks in mugs and teacups: Small cracks in mugs can be a source of leaks and potential bacteria growth. Food-safe epoxy provides a watertight seal, extending the life of the mug.
- Creating decorative elements on serving dishes: Epoxy can be used to embed decorative items, such as small stones or pigments, onto the surface of serving dishes, adding a unique touch.
- Crafting custom ceramic utensils: Epoxy can be employed in the creation of unique ceramic utensils, such as spoons or ladles, by bonding ceramic pieces together or adding decorative handles.
Decorative Items
Beyond functional tableware, food-safe epoxy finds application in decorative ceramic items that may come into contact with food, such as serving platters or decorative bowls.
- Repairing decorative bowls and vases: Epoxy can mend broken decorative items, restoring their appearance and functionality, even if they hold food items like fruit.
- Creating mosaics and decorative surfaces: Epoxy can be used to create mosaic patterns or add decorative elements to the surface of ceramic platters, enhancing their visual appeal.
- Sealing porous ceramics: Epoxy can be applied to seal the surface of porous ceramics, making them more resistant to staining and easier to clean.
Limitations in Food-Related Scenarios
While food-safe epoxy is a valuable material, it has limitations that must be considered.
- High-heat applications: Epoxy generally has a lower heat resistance than the ceramic materials it bonds. Therefore, it is not suitable for use in ovens, microwaves, or on stovetops.
- Direct contact with acidic foods: Prolonged exposure to highly acidic foods, such as citrus fruits or vinegar, can potentially degrade the epoxy over time.
- Dishwasher use: While some food-safe epoxies are dishwasher-safe, others may degrade with repeated exposure to high temperatures and harsh detergents.
- Food storage: It is crucial to consider the intended use of the ceramic item. For instance, food-safe epoxy is not recommended for long-term food storage due to the potential for leaching.
Suitability of Epoxy for Ceramic Items and Food Types
The following table summarizes the suitability of food-safe epoxy for various ceramic items and food types.
Ceramic Item | Suitable Food Types | Unsuitable Food Types | Considerations |
---|---|---|---|
Plates and Bowls | Dry foods, cold foods, room temperature foods. | High-heat foods, acidic foods, prolonged food storage. | Ensure epoxy is fully cured and food-safe certified. Avoid direct contact with food if unsure. |
Mugs and Cups | Beverages (coffee, tea, etc.), cold drinks. | High-heat beverages (boiled liquids), prolonged storage of acidic liquids. | Check epoxy’s heat resistance. Avoid microwaving or using on stovetops. |
Serving Dishes | Dry snacks, fruits, vegetables, pre-prepared foods. | Hot foods, highly acidic foods (e.g., lemon slices), oily foods. | Avoid direct contact with food if decorative elements are embedded. |
Utensils (Spoons, Ladles) | Food contact for stirring and serving. | Direct contact with hot foods at high temperatures, or acidic ingredients. | Ensure the epoxy used is specifically formulated for utensil contact and is heat resistant. |
Choosing the Right Epoxy Product
Selecting the appropriate food-safe epoxy for ceramic applications is critical for ensuring both the aesthetic appeal and the safety of your finished pieces. Careful consideration of several factors will help you choose the best product for your specific project, guaranteeing durability, functionality, and adherence to safety standards.
Key Factors in Epoxy Selection
Several critical factors must be considered when selecting a food-safe epoxy product. These factors ensure the epoxy is suitable for its intended purpose, considering both performance and safety.
- Food Contact Certification: Verify that the epoxy is explicitly certified as food-safe by a recognized organization such as the FDA (in the United States) or similar bodies in your region. This certification confirms that the epoxy has undergone testing and meets specific standards for contact with food.
- Viscosity: The viscosity of the epoxy affects its application. Thinner epoxies are easier to apply and self-level, making them suitable for coatings. Thicker epoxies are better for filling gaps or creating thicker layers.
- Working Time and Cure Time: Working time is the period during which the epoxy remains workable after mixing. Cure time is the duration required for the epoxy to fully harden. Consider these times based on the complexity of your project and the desired pace of your work.
- UV Resistance: If the ceramic item will be exposed to sunlight, choose an epoxy with UV resistance to prevent yellowing or degradation over time.
- Heat Resistance: Determine the maximum temperature the ceramic item will experience. Select an epoxy that can withstand those temperatures without softening or releasing harmful chemicals.
- Clarity and Color: Consider the desired aesthetic. Some epoxies are crystal clear, while others may have a slight tint. Some products offer color pigments or additives to achieve specific effects.
- Chemical Resistance: Evaluate the potential exposure to chemicals, such as cleaning agents. Choose an epoxy with the necessary resistance to maintain its integrity.
Epoxy Brand Comparison
The following table compares several popular food-safe epoxy brands, highlighting their features, benefits, and drawbacks. This information is intended to assist in making an informed decision based on your project’s requirements.
Brand | Key Features | Benefits | Drawbacks |
---|---|---|---|
ProMarine Supplies Crystal Clear Epoxy Resin | Crystal clear, UV resistant, low odor, self-leveling. | Excellent clarity, easy to use, ideal for coating and casting, good for beginners. | May require multiple coats for deep pours, cure time can be longer in cooler temperatures. |
ArtResin Epoxy Resin | Non-toxic, UV resistant, food-safe certified, easy 1:1 mix ratio. | User-friendly, scratch-resistant, great for art projects, food contact safe. | Slightly higher cost, limited working time compared to some other brands. |
Stone Coat Countertops Epoxy | High-build, UV resistant, chemical resistant, available in various colors and pigments. | Durable, suitable for countertops and high-use surfaces, customizable color options. | Requires more experience due to the high-build nature, may have a stronger odor during application. |
TotalBoat TableTop Epoxy | High-gloss finish, UV resistant, durable, easy to apply. | Provides a professional-grade finish, resistant to scratches and stains, ideal for tabletops and surfaces. | Slower cure time compared to some alternatives, can be more expensive. |
Recommendations for Specific Ceramic Applications
Choosing the right epoxy often depends on the intended use of the ceramic item. Here are some recommendations based on common applications.
- For Coating Ceramic Mugs and Plates: Use a crystal-clear, food-safe epoxy with good UV resistance and a relatively fast cure time. This ensures a durable, glossy finish that protects the ceramic and is safe for food contact. Products like ProMarine Supplies Crystal Clear Epoxy Resin are well-suited for this.
- For Filling Cracks or Chips in Ceramic: A thicker, food-safe epoxy with good adhesion properties is recommended. This type of epoxy can fill imperfections and provide a strong, lasting repair. Consider brands like ArtResin, known for its ease of use and reliable performance.
- For Creating Decorative Ceramic Art Pieces: Select an epoxy with excellent clarity and the ability to incorporate pigments or additives. UV resistance is crucial if the piece will be exposed to sunlight. ArtResin and Stone Coat Countertops Epoxy are good choices because they offer color customization and aesthetic appeal.
- For Sealing Ceramic Kitchenware (e.g., Bowls, Serving Dishes): Prioritize an epoxy with high chemical resistance and proven food-safe certification. This ensures that the epoxy can withstand repeated washing and contact with various foods. TotalBoat TableTop Epoxy offers excellent durability and is often chosen for such applications.
Maintenance and Care
Maintaining the integrity of your food-safe epoxy coating on ceramic items is crucial for its longevity and safety. Proper care ensures that the epoxy remains non-toxic and continues to protect the underlying ceramic. This section details the best practices for cleaning, avoiding damage, and addressing minor imperfections.
Cleaning Ceramic Items with Food-Safe Epoxy
Regular cleaning is essential to keep your epoxy-coated ceramics in optimal condition. It prevents the buildup of food particles, which can harbor bacteria, and maintains the aesthetic appeal of the item.To clean your epoxy-coated ceramic items, follow these guidelines:
- Gentle Cleaning Agents: Use mild dish soap and warm water. Avoid abrasive cleaners.
- Soft Cloths or Sponges: Opt for non-abrasive cloths or sponges to prevent scratching the epoxy surface.
- Rinse Thoroughly: Ensure all soap residue is rinsed away.
- Air Dry or Soft Towel: Allow items to air dry or pat them dry with a clean, soft towel.
Cleaning Products and Methods to Avoid
Certain cleaning products and methods can damage or degrade food-safe epoxy. Understanding these limitations is vital to preserving the coating.The following should be avoided:
- Abrasive Cleaners: Avoid abrasive powders, scouring pads, and steel wool, as they can scratch the epoxy surface, leading to clouding or damage.
- Harsh Chemicals: Do not use strong solvents, bleach, or ammonia-based cleaners, as they can break down the epoxy over time, causing it to become porous or lose its protective properties.
- High Heat: Avoid placing epoxy-coated items in the dishwasher or subjecting them to extremely high temperatures, as this can soften or deform the epoxy.
- Prolonged Soaking: Avoid soaking the items for extended periods, as this can potentially lead to water absorption and compromise the epoxy’s bond with the ceramic.
Repairing Minor Damage to the Epoxy Coating
Despite careful handling, minor damage such as scratches or small chips can occur. Addressing these issues promptly can prevent further degradation and maintain the safety of the item.Here are methods for repairing minor damage:
- Minor Scratches: Fine scratches can often be buffed out using a polishing compound specifically designed for epoxy. Follow the manufacturer’s instructions for application and buffing.
- Small Chips: For small chips, you can apply a thin layer of food-safe epoxy to the damaged area. Ensure the area is clean and dry before applying the epoxy. Allow the epoxy to cure completely according to the manufacturer’s instructions. After curing, the surface can be sanded and polished to blend the repair with the existing coating.
- Larger Damage: For more significant damage, it may be necessary to remove the damaged epoxy and reapply a new coating. This process requires careful preparation of the surface and application of the epoxy, following the manufacturer’s guidelines for best results.
Troubleshooting Common Issues
Applying food-safe epoxy to ceramics, while generally straightforward, can sometimes present challenges. Recognizing and addressing these issues promptly is crucial for achieving a flawless, durable, and food-safe finish. This section will detail common problems encountered during application and offer practical solutions to ensure a successful outcome.
Bubble Formation
Bubble formation is perhaps the most frequent issue encountered when working with epoxy. These air pockets, if not addressed, can mar the surface, compromising both the aesthetic appeal and potentially the integrity of the coating.
- Causes of Bubble Formation: Bubbles can originate from several sources. Improper mixing techniques, particularly vigorous stirring, can introduce air into the epoxy mixture. The release of air trapped within the ceramic substrate during the curing process is another common cause, especially with porous ceramics. Furthermore, temperature fluctuations and the viscosity of the epoxy can influence bubble formation.
- Solutions for Bubble Removal: Several methods can be employed to mitigate bubble formation. Slow, deliberate mixing is essential. Allow the mixed epoxy to sit for a few minutes to allow some bubbles to naturally rise to the surface. Using a heat gun or a small propane torch, held a safe distance from the surface, can effectively pop bubbles. The heat reduces the surface tension of the epoxy, causing the bubbles to burst.
Applying thin coats and allowing each layer to partially cure before applying the next can also minimize bubble entrapment. Vacuum degassing equipment, although more specialized, offers a highly effective solution for removing bubbles before application.
Cloudiness and Yellowing
Cloudiness and yellowing can significantly detract from the clarity and appearance of the epoxy coating. These issues often arise due to improper mixing ratios, exposure to UV light, or the use of low-quality epoxy products.
- Causes of Cloudiness and Yellowing: Incomplete mixing of the resin and hardener is a primary cause of cloudiness. Incorrect mixing ratios, even slight deviations from the manufacturer’s recommendations, can lead to an improper cure, resulting in a cloudy finish. Prolonged exposure to ultraviolet (UV) light can cause epoxy to yellow over time. Using epoxy not specifically formulated for UV resistance exacerbates this problem.
Furthermore, certain environmental factors, such as high humidity or extreme temperatures during the curing process, can contribute to cloudiness.
- Solutions for Cloudiness and Yellowing: Ensure thorough and precise mixing of the resin and hardener, following the manufacturer’s instructions meticulously. Consider using a digital scale for accurate measurement of the components. Choose epoxy products specifically formulated with UV resistance to minimize yellowing. Store the finished ceramic pieces away from direct sunlight. Applying a UV-resistant topcoat can provide an additional layer of protection.
Maintaining a controlled environment during curing, with consistent temperature and humidity levels, can also help prevent cloudiness.
Uneven Coating and Runs
Achieving a smooth, even coating is critical for both aesthetics and functionality. Unevenness and runs can compromise the appearance and potentially create areas where food particles or moisture can accumulate.
- Causes of Uneven Coating and Runs: Applying the epoxy too thickly can cause it to sag and run, particularly on vertical surfaces or curved areas. Uneven application techniques, such as using an unsuitable applicator or applying the epoxy inconsistently, contribute to this problem. The viscosity of the epoxy also plays a role; thinner epoxies are more prone to running. Environmental factors, like high temperatures, can accelerate the curing process, leading to unevenness.
- Solutions for Uneven Coating and Runs: Apply the epoxy in thin, even layers, allowing each layer to partially cure before applying the next. Use an appropriate applicator, such as a foam brush or a squeegee, to ensure uniform distribution. If runs occur, carefully remove the excess epoxy with a clean tool while the epoxy is still partially cured. Adjust the application technique to compensate for the ceramic’s shape, applying slightly more epoxy to concave areas and less to convex ones.
Consider using a self-leveling epoxy or a product with a higher viscosity to minimize running.
Impact of UV Exposure and Environmental Factors
The long-term durability and appearance of the epoxy coating are significantly affected by environmental factors, particularly UV exposure. Understanding these impacts and taking preventative measures is crucial.
- UV Exposure: As previously mentioned, UV light can cause epoxy to yellow and degrade over time. This degradation can weaken the coating, making it more susceptible to scratches and other damage. Direct sunlight exposure, even through a window, can accelerate this process.
- Temperature Fluctuations: Extreme temperature changes can cause the epoxy to expand and contract, potentially leading to cracking or delamination from the ceramic substrate.
- Humidity: High humidity during the curing process can interfere with the chemical reaction, leading to cloudiness or an incomplete cure.
- Chemical Exposure: Exposure to harsh chemicals, such as strong cleaning agents, can damage the epoxy coating, leading to discoloration or erosion.
Preventative Measures: To mitigate these environmental impacts, choose epoxy products with UV resistance. Store ceramic pieces away from direct sunlight. Consider applying a UV-resistant topcoat. Avoid exposing the coated ceramics to extreme temperatures or rapid temperature fluctuations. Use mild cleaning agents and avoid abrasive cleaners.
Alternatives to Epoxy for Ceramic Food Contact
When considering food-safe applications on ceramics, several alternatives to epoxy offer distinct advantages and disadvantages. The choice of material depends on the specific application, the desired aesthetic, and the required level of durability and food safety. Understanding these alternatives is crucial for making informed decisions.
Food-Safe Glazes
Food-safe glazes are a common and often preferred method for creating a food-safe surface on ceramic items. These glazes are formulated to be non-toxic and resistant to leaching, ensuring that food and beverages do not come into contact with potentially harmful substances from the ceramic body.
- Advantages:
- High aesthetic flexibility: Glazes come in a vast array of colors, textures, and finishes, allowing for extensive design possibilities.
- Durability: Properly fired glazes are generally durable and resistant to scratching and chipping, making them suitable for everyday use.
- Food safety: Food-safe glazes are specifically designed to be inert and prevent the leaching of heavy metals or other harmful substances into food.
- Disadvantages:
- Complexity: Applying and firing glazes require specialized equipment (kiln) and expertise, making it less accessible for DIY projects.
- Potential for defects: Imperfect firing or application can lead to glaze defects that compromise food safety or aesthetics.
- Limited repair options: Repairing a damaged glazed surface is often difficult and may require re-firing the entire piece.
Silicone Sealants
Food-grade silicone sealants offer a flexible and waterproof alternative for sealing or repairing ceramic items intended for food contact. These sealants are often used for applications where flexibility and resistance to temperature changes are important.
- Advantages:
- Flexibility: Silicone is flexible and can withstand some movement and temperature fluctuations without cracking.
- Waterproof: Provides an effective barrier against water and other liquids, preventing leaks.
- Ease of use: Silicone sealants are relatively easy to apply, requiring no special equipment.
- Disadvantages:
- Limited durability: Silicone is not as durable as epoxy or glaze and may degrade over time, especially with repeated washing or exposure to high temperatures.
- Aesthetic limitations: Silicone sealants typically come in a limited range of colors and may not be suitable for all aesthetic preferences.
- Potential for microbial growth: Silicone can be prone to microbial growth if not properly cleaned and maintained.
Polyurethane Coatings
Food-grade polyurethane coatings provide a hard, durable, and chemically resistant surface that can be applied to ceramic items. These coatings are often used in situations where a high level of protection and resistance to abrasion is required.
- Advantages:
- High durability: Polyurethane coatings are known for their excellent abrasion resistance and durability.
- Chemical resistance: They can resist a wide range of chemicals, making them suitable for various food contact applications.
- Ease of application: Polyurethane coatings can be applied using various methods, including brushing, spraying, and dipping.
- Disadvantages:
- Potential for toxicity: Some polyurethane coatings may contain volatile organic compounds (VOCs) that can pose health risks.
- Limited flexibility: Polyurethane coatings are generally less flexible than epoxy or silicone, which may lead to cracking over time.
- Adhesion issues: Achieving good adhesion to ceramic surfaces can be challenging and may require surface preparation.
Other Food-Safe Materials
Beyond the materials mentioned above, other alternatives exist for food contact applications on ceramics. These may include specialized waxes or coatings, although their suitability depends heavily on the specific application and the materials’ chemical properties.
- Considerations:
- Thorough research: Always thoroughly research any material before using it in food contact applications.
- Manufacturer’s instructions: Follow the manufacturer’s instructions for application, curing, and maintenance.
- Testing: Consider testing the material’s food safety properties to ensure it meets your specific needs.
Resources for Further Information
The following resources provide valuable information on food-safe materials for ceramics:
- Websites:
- The FDA (Food and Drug Administration): Offers information on food contact substances and regulations.
- NSF International: Provides certification and testing services for food-safe materials.
- Material safety data sheets (MSDS): Provide detailed information on the chemical composition and safety of various materials.
- Books and Publications:
- Ceramic textbooks: Offer in-depth information on glazes, firing processes, and material properties.
- Industry publications: Provide updates on new materials and technologies in the ceramics field.
Illustrative Examples and Case Studies: Food Safe Epoxy For Ceramics
Understanding the practical application of food-safe epoxy for ceramics is best achieved through illustrative examples and real-world case studies. These examples provide visual representations of successful repairs and highlight the epoxy’s versatility and effectiveness. By examining these scenarios, one can gain a clearer understanding of the techniques, results, and potential applications of food-safe epoxy in various ceramic projects.
Visual Representation: Before-and-After Ceramic Repair
A visual representation effectively demonstrates the transformative capabilities of food-safe epoxy in ceramic repair. This section Artikels the details of such a visual, providing a clear before-and-after comparison.Imagine a chipped ceramic mug, a common casualty of daily use. The “Before” image depicts the mug with a noticeable chip on its rim, revealing the porous ceramic beneath. The chip is clearly visible, disrupting the smooth contour of the mug and potentially posing a safety hazard.
The “After” image shows the same mug, meticulously repaired. The chip is filled with food-safe epoxy, carefully matched to the original color of the ceramic. The repaired area is smooth, seamless, and almost indistinguishable from the surrounding surface. The epoxy has restored the mug’s structural integrity and aesthetic appeal, making it safe and usable once again. The visual highlights the epoxy’s ability to fill voids, bond strongly, and create a food-safe, durable surface.
The before image conveys damage and potential hazard, while the after image conveys restoration and usability.
Case Study: Successful Application in a Ceramic Serving Platter, Food safe epoxy for ceramics
A case study provides in-depth information about a specific project, showcasing the practical use of food-safe epoxy. This particular case focuses on a successful application involving a ceramic serving platter.
A renowned artisan, known for their intricate ceramic serving platters, faced a challenge when a platter sustained a significant crack during transit. The crack extended across a substantial portion of the platter’s surface, rendering it unusable for food service. The artisan, committed to preserving their work and maintaining food safety standards, chose a food-safe epoxy specifically designed for ceramic repair. Following the manufacturer’s instructions meticulously, the artisan cleaned the crack thoroughly, ensuring the removal of any debris. The epoxy was then carefully mixed and applied to the crack, ensuring complete penetration. After the epoxy cured, the artisan meticulously sanded and polished the repaired area to create a smooth, seamless finish, matching the original glaze as closely as possible. The repaired platter was then tested for food safety, passing all relevant regulations. The successful repair not only restored the platter’s functionality and aesthetic value but also saved the artisan the cost of replacing the damaged piece. This case study demonstrates the epoxy’s efficacy in repairing significant damage, its ability to meet stringent food safety requirements, and its potential to salvage valuable ceramic items.
Illustration: Stages of Applying Food-Safe Epoxy
An illustration detailing the stages of applying food-safe epoxy offers a step-by-step guide to the repair process. This visual aid enhances understanding and promotes successful application.The illustration comprises a sequence of panels, each depicting a distinct stage of the epoxy application process:
1. Preparation
The first panel shows a close-up of a chipped ceramic item (e.g., a bowl). The surface around the chip is being cleaned with isopropyl alcohol and a soft cloth. The image conveys the importance of removing dirt, grease, and loose particles to ensure proper adhesion of the epoxy.
2. Mixing
The second panel depicts the mixing stage. Two containers are shown, one containing the epoxy resin and the other the hardener. A user is carefully mixing the two components using a disposable mixing stick, ensuring a homogeneous mixture. The illustration emphasizes the importance of adhering to the manufacturer’s recommended mixing ratio and thorough mixing to ensure proper curing.
3. Application
The third panel focuses on the application of the mixed epoxy. A small amount of the mixture is being carefully applied to the chipped area using a spatula or applicator. The image illustrates the importance of applying the epoxy in thin, even layers to avoid air bubbles and ensure a smooth finish.
4. Curing
The fourth panel shows the item in a controlled environment, such as a dust-free area. The image highlights the importance of allowing the epoxy to cure completely according to the manufacturer’s instructions, considering factors like temperature and humidity.
5. Sanding and Polishing
The fifth panel depicts the sanding and polishing stage. The repaired area is being carefully sanded with fine-grit sandpaper to remove any excess epoxy and create a smooth surface. This is followed by polishing with a polishing compound to restore the original gloss and finish.
6. Inspection
The final panel shows the repaired item, ready for use. The repair is almost invisible, seamlessly integrated with the original ceramic surface. This illustrates the successful outcome of the epoxy application process.
Epilogue
In conclusion, the application of food-safe epoxy for ceramics presents a compelling blend of art, science, and safety. This exploration has illuminated the critical aspects of choosing, applying, and maintaining epoxy coatings on ceramic items, allowing you to create durable, beautiful, and safe pieces. Whether you’re a seasoned artisan or a curious hobbyist, this information provides a solid foundation for your ceramic projects.
By understanding the nuances of food-safe epoxy, you can confidently craft ceramic items that are both aesthetically pleasing and safe for everyday use.