Food safe glass adhesive plays a critical, yet often unseen, role in ensuring the safety and integrity of the food and beverage products we consume daily. From the sturdy construction of food containers to the intricate sealing of processing equipment, this specialized adhesive is designed to meet stringent safety standards, preventing contamination and maintaining product quality. Its significance extends across various applications, safeguarding food from harmful substances and ensuring a secure bond between glass components.
This discussion will explore the intricacies of food safe glass adhesive, examining its composition, regulatory requirements, application techniques, and the various types available. We’ll delve into the crucial aspects of curing, testing, and quality control, alongside troubleshooting common issues and providing insights into industry applications. Furthermore, we’ll look into the future trends and innovations shaping this vital technology.
Introduction to Food Safe Glass Adhesive
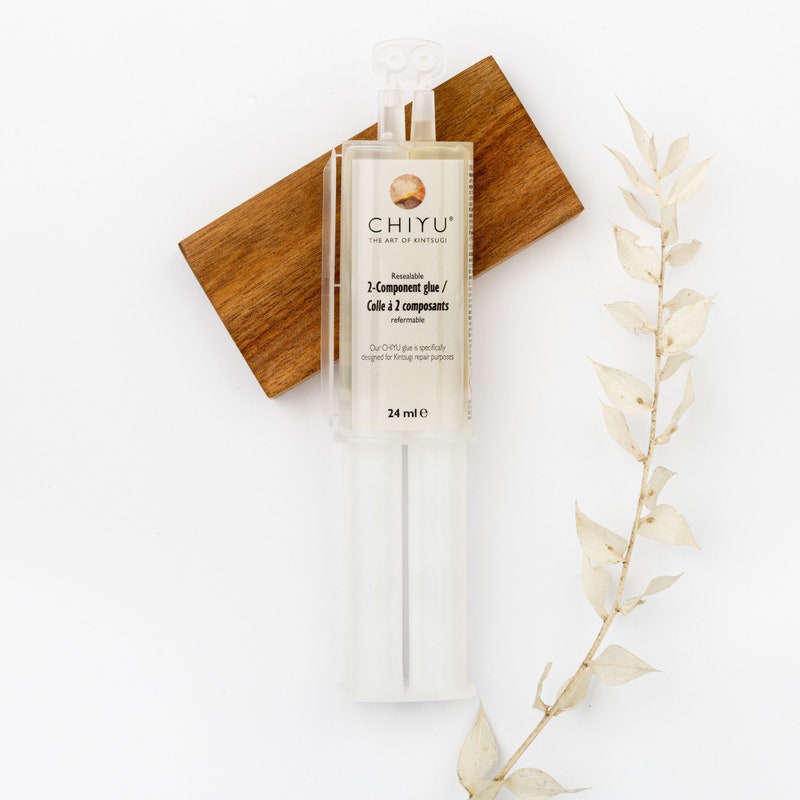
Food safe glass adhesive plays a crucial role in ensuring the integrity and safety of food packaging and preparation equipment. This specialized adhesive is designed to bond glass components together while maintaining a non-toxic environment, preventing any harmful substances from leaching into food products. Its significance lies in its ability to create a secure and sanitary seal, vital for preserving food quality and protecting consumer health.
Fundamental Purpose and Applications
The primary purpose of food safe glass adhesive is to create a durable and impermeable bond between glass surfaces that come into direct or indirect contact with food. This adhesive must withstand various conditions, including temperature fluctuations, moisture, and exposure to cleaning agents, without compromising its integrity or releasing any contaminants.Common applications of food safe glass adhesive include:
- Food Packaging: This adhesive is extensively used in the manufacturing of glass jars, bottles, and containers for food storage and preservation. The adhesive ensures a leak-proof seal, preventing spoilage and maintaining the freshness of the contents.
- Kitchen Appliances: It is utilized in assembling glass components of appliances like blenders, food processors, and ovens, where the adhesive must withstand heat and contact with food.
- Laboratory Equipment: In scientific settings, food safe glass adhesive is essential for constructing glassware used in food analysis and research, guaranteeing the accuracy and safety of experiments.
- Display Cases: It is employed in display cases used in restaurants, cafes, and grocery stores to showcase food items, maintaining their presentation and hygiene.
Differentiating Properties
Food safe glass adhesive is distinct from other adhesives due to its unique composition and properties. It is formulated to meet stringent regulatory standards, such as those set by the Food and Drug Administration (FDA) in the United States and similar agencies worldwide.Key differentiating properties include:
- Non-Toxicity: The adhesive is manufactured from materials that do not pose a health risk when in contact with food. It does not contain any substances that can migrate into the food and cause contamination.
- Chemical Resistance: It exhibits excellent resistance to various chemicals, including acids, bases, and solvents commonly used in food processing and cleaning.
- Temperature Stability: The adhesive maintains its bonding strength and integrity across a wide range of temperatures, from freezing to high-temperature sterilization processes.
- Water Resistance: It is resistant to water and moisture, preventing degradation and ensuring a durable seal even in humid environments.
- Durability: Food safe glass adhesives are formulated to provide a long-lasting bond, capable of withstanding the stresses of daily use and the rigors of food processing environments.
Food safe glass adhesive is often subject to rigorous testing to verify its compliance with food safety regulations. These tests include:
- Migration Testing: This involves exposing the adhesive to food simulants (such as water, acetic acid, and olive oil) under controlled conditions to determine if any substances migrate from the adhesive into the food simulant.
- Toxicity Testing: This assesses the potential for the adhesive to cause adverse health effects through oral, dermal, or inhalation exposure.
- Adhesion Testing: This measures the adhesive’s ability to bond glass surfaces together under various conditions, such as temperature and pressure.
The development and application of food safe glass adhesive are constantly evolving to meet the changing demands of the food industry, focusing on enhancing performance, expanding application possibilities, and improving the overall safety of food products.
Material Composition and Safety Standards
Food safe glass adhesive formulations prioritize the safety of consumers by ensuring that no harmful substances can leach into food products. This necessitates careful selection of raw materials and adherence to stringent regulatory standards. The composition typically involves a combination of polymers, additives, and solvents, each playing a specific role in achieving the desired adhesive properties while maintaining food safety.
Typical Materials and Their Safety Profiles
The materials used in food safe glass adhesives are chosen for their inertness and lack of toxicity. These materials undergo rigorous testing to ensure they meet the necessary safety requirements.
- Polymers: Common polymers include silicones, polyurethanes, and modified acrylics. Silicones are often preferred due to their excellent resistance to temperature fluctuations and chemical inertness. Polyurethanes can offer high strength and flexibility, while modified acrylics provide good adhesion properties. These polymers are typically manufactured to be free from extractable substances that could migrate into food.
- Additives: Additives enhance the adhesive’s performance. These can include plasticizers, stabilizers, and curing agents. Plasticizers improve flexibility, while stabilizers prevent degradation. Curing agents initiate the cross-linking process, which hardens the adhesive. The additives used must be food-grade and approved for use in food contact applications.
- Solvents: Solvents facilitate the application and curing of the adhesive. They evaporate during the curing process, leaving behind the solid adhesive matrix. Solvents are carefully selected to minimize any potential for residual presence after curing. Water-based or low-VOC (Volatile Organic Compounds) formulations are frequently favored to reduce health and environmental risks.
Regulatory Standards and Certifications
Food safe glass adhesives must comply with international regulations and certifications to ensure their suitability for use in food contact applications. These standards define the permissible levels of substances that can migrate from the adhesive into food and provide a framework for manufacturers to demonstrate compliance.
- United States – FDA (Food and Drug Administration): The FDA regulates food contact materials under 21 CFR (Code of Federal Regulations). Specifically, regulations like 21 CFR 175.105, “Adhesives,” Artikel the requirements for adhesives used in food packaging and processing equipment. Adhesives must be composed of substances that are generally recognized as safe (GRAS) or have been approved by the FDA. The FDA also conducts migration testing to assess the potential for the adhesive to transfer its components into food.
- European Union – EU Regulations: The EU’s primary regulation for food contact materials is Regulation (EC) No 1935/2004. This regulation sets out the general requirements for all food contact materials, including adhesives. Specific requirements for adhesives are often addressed under the framework of good manufacturing practice (GMP). The EU also regulates the use of specific substances in food contact materials, with lists of approved substances often detailed in specific directives and regulations.
The migration limits are defined according to the nature of the food and the contact conditions.
- Other International Standards: Many other countries and regions have their own regulations, often mirroring or aligning with the FDA and EU standards. These include regulations from countries like Canada (Health Canada), Australia (Food Standards Australia New Zealand), and Japan (Japan Food Research Laboratories). Compliance with these standards often requires testing by accredited laboratories and certification by recognized bodies.
Comparative Analysis of International Safety Requirements
The following table provides a comparison of the key safety requirements across different international standards for food safe glass adhesives.
Standard | Governing Body | Key Regulation/Standard | Key Requirements |
---|---|---|---|
FDA (United States) | Food and Drug Administration | 21 CFR 175.105 |
|
EU (European Union) | European Commission | Regulation (EC) No 1935/2004 |
|
Health Canada (Canada) | Health Canada | Food and Drugs Act and Regulations |
|
Food Standards Australia New Zealand (FSANZ) | Food Standards Australia New Zealand | Food Standards Code |
|
Types of Food Safe Glass Adhesives
Understanding the different types of food-safe glass adhesives available is crucial for selecting the appropriate adhesive for a specific application. The choice of adhesive significantly impacts the integrity, safety, and longevity of the bonded glass structure. This section details the common types, their characteristics, and the factors to consider when making a selection.
Silicone-Based Adhesives
Silicone-based adhesives are a popular choice for food-safe applications due to their flexibility, resistance to extreme temperatures, and generally good chemical resistance. They are typically single-component adhesives, meaning they cure upon exposure to moisture in the air.
Notice pure cravings cat food costco for recommendations and other broad suggestions.
- Advantages:
- Flexibility: Silicone adhesives remain flexible after curing, allowing for movement and stress absorption, which is beneficial in applications subject to thermal expansion and contraction.
- Temperature Resistance: They can withstand a wide range of temperatures, typically from -50°C to 200°C (-58°F to 392°F), making them suitable for applications in ovens, refrigerators, and freezers.
- Chemical Resistance: Silicone adhesives demonstrate good resistance to many chemicals, including detergents and cleaning agents commonly used in food preparation and processing environments.
- Ease of Use: Single-component formulations are easy to apply, requiring no mixing.
- Disadvantages:
- Bonding Strength: Silicone adhesives generally have lower tensile strength compared to epoxy-based adhesives.
- Curing Time: They require time to cure, often dependent on humidity and temperature, which can range from several hours to a day.
- Surface Preparation: Proper surface preparation is crucial for optimal adhesion; surfaces must be clean and free of contaminants.
Examples of applications include sealing glass food containers, bonding glass components in kitchen appliances, and assembling glass display cases for food products.
Epoxy-Based Adhesives
Epoxy-based adhesives offer superior bonding strength and are known for their rigidity and resistance to a wide range of chemicals. They typically consist of two components: a resin and a hardener, which must be mixed before application.
- Advantages:
- High Bond Strength: Epoxy adhesives provide excellent bonding strength, making them suitable for structural applications.
- Chemical Resistance: They exhibit excellent resistance to solvents, acids, and bases, making them suitable for harsh environments.
- Durability: Epoxy adhesives are known for their durability and resistance to degradation over time.
- Disadvantages:
- Rigidity: The rigidity of cured epoxy adhesives can make them less suitable for applications where flexibility is required.
- Curing Time: Epoxy adhesives typically have a longer curing time compared to some other adhesive types, and the curing process is temperature-dependent.
- Mixing Required: The need to mix two components can be inconvenient and requires precise measurement.
- Temperature Limitations: While some epoxy adhesives can withstand moderate temperatures, they may degrade at high temperatures.
Epoxy adhesives are frequently used in applications that require strong, permanent bonds, such as assembling glass components in industrial food processing equipment.
UV-Cured Adhesives
UV-cured adhesives, also known as light-cured adhesives, cure rapidly upon exposure to ultraviolet (UV) light. They offer fast curing times and are ideal for high-volume production environments.
- Advantages:
- Fast Curing: UV adhesives cure within seconds, significantly reducing production time.
- Precise Control: The curing process is initiated only when exposed to UV light, allowing for precise control over the bonding process.
- Aesthetics: UV adhesives often result in clear, transparent bonds, which is aesthetically desirable in many applications.
- Disadvantages:
- UV Light Exposure: The adhesive requires direct exposure to UV light for curing, limiting its use to applications where light can reach the bond line.
- Special Equipment: UV curing requires specialized equipment, such as UV lamps or curing systems.
- Material Limitations: Certain materials can block UV light, preventing the adhesive from curing.
UV-cured adhesives are commonly used in the manufacturing of glass food containers, such as jars and bottles, where rapid curing and aesthetic appeal are important.
Decision-Making Flowchart for Adhesive Selection
Selecting the most appropriate food-safe glass adhesive involves considering several factors. The following flowchart guides the decision-making process:
- Application Requirements: Determine the specific requirements of the application.
- Is flexibility required? If yes, proceed to step 2. If no, proceed to step 3.
- Flexibility and Temperature Resistance: Consider silicone-based adhesives.
- Is temperature resistance critical? If yes, select a silicone adhesive with a suitable temperature range.
- Is the application exposed to chemicals? If yes, verify the silicone adhesive’s chemical resistance.
- Bond Strength and Durability: Consider epoxy-based adhesives.
- Is high bond strength essential? If yes, select an epoxy adhesive.
- Is chemical resistance important? If yes, select an epoxy adhesive with appropriate chemical resistance properties.
- Production Speed and Transparency: Consider UV-cured adhesives.
- Is rapid curing required? If yes, proceed to step 5.
- UV Light Access: Determine if the bond line can be exposed to UV light.
- Is UV light exposure possible? If yes, select a UV-cured adhesive.
- Is aesthetic appeal important? If yes, choose a UV-cured adhesive that provides a clear bond.
The flowchart helps streamline the selection process by systematically evaluating the application’s requirements and matching them with the characteristics of each adhesive type.
Application Techniques and Procedures
The successful application of food-safe glass adhesive hinges on meticulous preparation and adherence to a precise procedure. This section details the essential steps to ensure optimal adhesion, food safety compliance, and the long-term integrity of your glass bonding projects. Proper execution is critical to avoid potential contamination and maintain the safety of any food products that will come into contact with the bonded glass.
Surface Preparation for Optimal Adhesion
Effective surface preparation is the cornerstone of a strong and durable bond. Contaminants such as dust, grease, and oils can significantly impede adhesion, leading to bond failure. It is essential to thoroughly clean the glass surfaces before applying the adhesive.
- Cleaning Agents: Utilize appropriate cleaning agents specifically designed for glass surfaces. Avoid harsh chemicals or solvents that might leave residues. For instance, isopropyl alcohol (IPA) is often recommended for its effectiveness in removing contaminants without leaving a film. Always consult the adhesive manufacturer’s guidelines for recommended cleaning solutions.
- Cleaning Procedure: Clean the glass surfaces with the chosen agent, ensuring complete coverage. Use a clean, lint-free cloth or paper towel to wipe away any residue. Repeat the cleaning process if necessary, especially if the glass appears heavily soiled.
- Surface Inspection: After cleaning, carefully inspect the surfaces for any remaining imperfections or contaminants. Examine the surfaces under adequate lighting to ensure no residue or particles are visible.
- Drying: Allow the cleaned glass surfaces to dry completely before applying the adhesive. The drying time will vary depending on the cleaning agent and environmental conditions. Ensure the surfaces are completely dry to prevent trapping moisture, which can compromise the bond.
- Surface Roughening (if applicable): In some cases, especially with non-smooth glass surfaces, a light abrasion might be necessary to increase the surface area and improve adhesion. This should be done with extreme caution and only if recommended by the adhesive manufacturer, using appropriate abrasive materials.
Step-by-Step Adhesive Application
Following a systematic application process is vital to achieving a food-safe and durable bond. Deviations from the recommended procedures can compromise the integrity of the bond and potentially lead to food safety hazards.
- Preparation of the Adhesive: Carefully read and follow the manufacturer’s instructions for preparing the adhesive. This might involve mixing components or applying a primer. Ensure the adhesive is within its usable timeframe after preparation.
- Application of the Adhesive: Apply the adhesive to one of the prepared glass surfaces, following the manufacturer’s recommendations regarding bead size and pattern. Avoid excessive adhesive, which can result in squeeze-out and potential contamination.
- Joining the Surfaces: Carefully align the glass pieces and bring them together, ensuring proper positioning. Apply gentle pressure to distribute the adhesive evenly and remove air bubbles.
- Clamping or Securing: Secure the joined glass pieces using clamps, tape, or other appropriate methods to maintain alignment and pressure during the curing process. The type of securing method depends on the project design.
- Curing Time: Allow the adhesive to cure completely according to the manufacturer’s specifications. This time varies depending on the adhesive type, temperature, and humidity. Avoid disturbing the bonded pieces during the curing period.
- Inspection and Cleaning: After curing, inspect the bond for any gaps, voids, or imperfections. Remove any excess adhesive that has squeezed out, using a clean, appropriate tool. Clean the surrounding area as needed.
Visual Guide (Illustrations with Descriptions):
Step 1: Surface Cleaning (Illustration 1):
The illustration shows a person wearing gloves and safety glasses, using a spray bottle containing a cleaning solution and a clean, lint-free cloth to clean a glass surface. The glass surface is positioned horizontally, indicating easy access for cleaning. The spray bottle is labeled with a recognizable brand, and the cloth is shown in close-up to highlight its texture.
Step 2: Adhesive Application (Illustration 2):
The illustration displays a person holding a tube of adhesive with a nozzle, carefully applying the adhesive to the edge of a glass panel. The application is shown as a continuous bead, with attention to the evenness of the application. The person is wearing gloves, and the work area is clean and well-lit.
Step 3: Joining and Securing (Illustration 3):
The illustration depicts two glass panels being joined, with clamps in place to secure them. The illustration shows the panels are aligned correctly, with the adhesive bead between them. The clamps are clearly visible, demonstrating the pressure applied. The background is neutral to highlight the focus on the joining process.
Step 4: Curing and Inspection (Illustration 4):
The illustration shows the joined glass panels after the adhesive has cured. The clamps have been removed, and the bond line is clearly visible. A person is shown inspecting the bond for any imperfections, using a light source to check for voids or air bubbles. The surface appears clean, and the adhesive is evenly distributed.
Warnings:
- Always wear appropriate personal protective equipment (PPE), including gloves, eye protection, and, if necessary, a respirator, during the application process.
- Work in a well-ventilated area to avoid inhaling adhesive fumes.
- Follow the adhesive manufacturer’s instructions precisely.
- Do not use food-safe glass adhesive for applications outside of its intended purpose.
- Ensure the adhesive is fully cured before exposing it to food or beverages.
- If any adhesive comes into contact with food products, discard the affected items.
- Store the adhesive properly, as per the manufacturer’s instructions, to maintain its effectiveness and safety.
Curing and Drying Process
The curing and drying process is a critical stage in the application of food-safe glass adhesives. It directly impacts the adhesive’s final strength, durability, and its ability to meet food safety standards. Understanding the factors that influence this process and adhering to recommended curing times are essential for ensuring a successful and safe bond.
Factors Influencing Curing or Drying
Several factors can significantly influence the curing or drying process of food-safe glass adhesives. These factors must be carefully controlled to achieve optimal results.
- Temperature: Higher temperatures generally accelerate the curing process, while lower temperatures slow it down. Extreme temperatures, both high and low, can negatively impact the adhesive’s performance. Most adhesives have a recommended temperature range for optimal curing. For instance, silicone-based adhesives might cure faster at 25°C (77°F) than at 10°C (50°F).
- Humidity: Humidity plays a crucial role, especially for moisture-curing adhesives like some silicones. Higher humidity levels typically speed up the curing process by providing more moisture for the chemical reaction. Conversely, very low humidity can slow down or even halt the curing process.
- UV Exposure: Some adhesives, particularly those containing UV-curable components, require exposure to ultraviolet (UV) light to initiate and accelerate the curing process. The intensity and duration of UV exposure directly affect the curing rate. For example, a UV-cured adhesive used in a food-grade glass container might require a specific wavelength and exposure time to achieve full cure.
- Air Circulation: Adequate air circulation can help remove solvents or byproducts released during the curing process, preventing them from interfering with the adhesive’s performance. Poor ventilation can trap these substances, potentially leading to incomplete curing or weakened bonds.
- Adhesive Type: Different adhesive formulations have different curing mechanisms and requirements. Some cure through evaporation of solvents, others through a chemical reaction triggered by moisture or UV light. The type of adhesive will dictate the specific factors that influence its curing process.
Importance of Curing Time
Allowing sufficient curing time is paramount for the adhesive to reach its full strength and to ensure its suitability for food contact. Premature use of the bonded glass can lead to several undesirable consequences.
- Reduced Bond Strength: Insufficient curing time means the adhesive hasn’t fully reacted or dried, resulting in a weaker bond that is more susceptible to failure under stress. This could lead to leakage or separation of the glass components.
- Compromised Food Safety: Incompletely cured adhesives might release harmful chemicals or leach into the food, posing a health risk. For instance, if a food-safe silicone adhesive used in a jar lid isn’t fully cured, it might release unreacted compounds into the food.
- Altered Physical Properties: Incomplete curing can affect the adhesive’s flexibility, resistance to temperature fluctuations, and overall durability. This can shorten the lifespan of the bonded product.
- Failure to Meet Standards: Products used before the complete curing time might not meet the stringent regulations set by food safety authorities, potentially leading to product recalls and legal repercussions.
Curing Times and Conditions for Different Adhesive Types
The following table illustrates the curing times and conditions for different types of food-safe glass adhesives. These are general guidelines, and the specific curing requirements may vary depending on the manufacturer and the specific adhesive formulation. Always consult the manufacturer’s instructions for the most accurate information.
Adhesive Type | Typical Curing Time (at 25°C/77°F) | Humidity Requirements | Other Conditions |
---|---|---|---|
Silicone Adhesive (Moisture-Curing) | 24-72 hours (full cure) | 40-80% relative humidity | Ensure good ventilation; avoid direct sunlight during curing. |
UV-Curable Adhesive | Seconds to minutes (depending on UV intensity) | Not a significant factor | Requires exposure to specific UV wavelength and intensity. Protect from UV exposure until ready to cure. |
Epoxy Adhesive (Two-Part) | 24-48 hours (full cure) | Not a significant factor, but higher temperatures can accelerate curing. | Ensure proper mixing of the two components; maintain a consistent temperature. |
Polyurethane Adhesive (Moisture-Curing) | 48-96 hours (full cure) | 40-70% relative humidity | Good ventilation is recommended. Protect from direct moisture exposure until cured. |
Testing and Quality Control
Ensuring the integrity and safety of food-safe glass adhesives is paramount. Rigorous testing and meticulous quality control measures are essential to verify that the adhesive meets the required performance standards and does not pose any risk to consumer health. This section details the common tests, quality control measures, and critical parameters involved in this process.
Common Tests for Performance Evaluation
Several tests are employed to assess the performance of food-safe glass adhesives, focusing on their bond strength, chemical resistance, and potential for migration of substances into food. These tests are crucial in determining the adhesive’s suitability for its intended application.
- Bond Strength Testing: This evaluates the adhesive’s ability to withstand forces that might cause the bonded glass components to separate.
- Tensile Shear Strength: This test measures the force required to pull the bonded glass surfaces apart in a shear direction. It is typically measured in pounds per square inch (psi) or megapascals (MPa). A higher value indicates a stronger bond.
- Peel Strength: This test assesses the adhesive’s resistance to peeling forces, often used for flexible or semi-rigid materials. The peel strength is measured in pounds per inch (ppi) or Newtons per millimeter (N/mm).
- Lap Shear Strength: This test is similar to tensile shear strength but involves overlapping the bonded surfaces. It is used to evaluate the adhesive’s performance under shear stress.
- Chemical Resistance Testing: This determines the adhesive’s ability to withstand exposure to various chemicals, including those commonly found in food and cleaning agents.
- Immersion Testing: Samples of the adhesive are immersed in specific food simulants (e.g., distilled water, 3% acetic acid, 10% ethanol, or olive oil) for a set period, usually at elevated temperatures, to accelerate the testing process.
- Exposure to Cleaning Agents: The adhesive is exposed to common cleaning agents, such as detergents and sanitizers, to assess its resistance to degradation or dissolution.
- Visual Inspection and Weight Change: After exposure, the adhesive is visually inspected for any signs of degradation, such as swelling, cracking, or discoloration. The weight change is also measured to determine if any substances have been absorbed or leached out.
- Migration Testing: This is critical for ensuring the adhesive does not contaminate food with harmful substances.
- Simulant Exposure: Bonded glass samples are exposed to food simulants under controlled conditions (temperature, time). The simulants are then analyzed to detect any migration of substances from the adhesive into the food simulant.
- Gas Chromatography-Mass Spectrometry (GC-MS): This technique is used to identify and quantify volatile organic compounds (VOCs) that may have migrated from the adhesive.
- Inductively Coupled Plasma Mass Spectrometry (ICP-MS): This method is used to detect and quantify the presence of metals that may have migrated from the adhesive.
- Overall Migration Limits: Regulatory bodies, such as the FDA in the United States and the European Food Safety Authority (EFSA) in Europe, set limits on the overall migration of substances from food contact materials, including adhesives, into food.
Quality Control Measures for Food Safety Compliance
Implementing robust quality control measures is essential to ensure that the adhesive consistently meets food safety standards throughout the manufacturing process. This involves controlling the raw materials, manufacturing process, and final product.
- Raw Material Control:
- Supplier Qualification: Only suppliers who meet stringent quality standards and can provide certificates of analysis (COA) for their raw materials should be used.
- Incoming Inspection: Raw materials should be inspected upon arrival to verify they meet the specified requirements.
- Material Traceability: A system for tracking raw materials throughout the manufacturing process should be in place.
- Manufacturing Process Control:
- Process Parameters: Critical process parameters, such as mixing ratios, temperature, and curing time, should be strictly controlled and monitored.
- Equipment Calibration and Maintenance: All equipment used in the manufacturing process should be regularly calibrated and maintained to ensure accurate and consistent performance.
- Work Instructions: Clear and detailed work instructions should be provided to all personnel involved in the manufacturing process.
- Final Product Testing and Inspection:
- Batch Testing: Each batch of adhesive should be tested to verify that it meets the required performance and safety standards.
- Visual Inspection: The final product should be visually inspected for any defects, such as air bubbles, cracks, or incomplete curing.
- Documentation: All test results, inspection records, and process control data should be thoroughly documented and maintained.
Checklist of Critical Parameters for Testing and Quality Control
A comprehensive checklist helps ensure that all critical parameters are monitored and controlled during testing and quality control procedures.
Parameter | Description | Acceptance Criteria | Testing Frequency |
---|---|---|---|
Raw Material Verification | Confirmation of material specifications from suppliers. | Compliance with COA and technical data sheets. | Each batch. |
Mixing Ratio | Accurate measurement and mixing of adhesive components. | Within specified range. | Each batch. |
Temperature | Control of temperature during mixing and application. | Within specified range. | Continuous monitoring. |
Curing Time and Temperature | Monitoring of curing conditions. | Compliance with manufacturer’s specifications. | Each batch. |
Bond Strength (Tensile, Shear, Peel) | Measurement of bond strength. | Meets minimum strength requirements. | Each batch, or as specified by regulations. |
Chemical Resistance | Exposure to food simulants and cleaning agents. | No degradation, swelling, or leaching. | Periodically, as specified by regulations. |
Migration Testing | Analysis of food simulants for migrating substances. | Compliance with overall migration limits. | Periodically, as specified by regulations. |
Visual Inspection | Inspection for defects. | No visible defects (cracks, bubbles, etc.). | Each batch. |
Batch Testing | Testing to ensure compliance with all requirements. | Passes all required tests. | Each batch. |
Potential Issues and Troubleshooting
Even with careful adherence to best practices, issues can arise when working with food-safe glass adhesives. Understanding these potential problems and having effective troubleshooting strategies is crucial for ensuring the integrity and safety of the final product. This section Artikels common issues, their causes, and practical solutions.
Poor Adhesion
Poor adhesion is one of the most frequently encountered problems. This can manifest as the adhesive failing to bond properly to the glass surfaces, leading to leaks, separation, or structural instability.The causes of poor adhesion can be varied, including:
- Surface Contamination: The presence of grease, oil, dust, or other contaminants on the glass surfaces prevents the adhesive from making proper contact. This can include fingerprints or residue from previous cleaning agents.
- Improper Surface Preparation: Insufficient cleaning or etching of the glass surface, as recommended by the adhesive manufacturer, can hinder adhesion.
- Incorrect Adhesive Application: Applying too little or too much adhesive, or applying it unevenly, can compromise the bond.
- Expired Adhesive: Using adhesive that has exceeded its shelf life can lead to a reduced ability to bond.
- Environmental Factors: Extremely high or low temperatures, or high humidity during application and curing, can affect the adhesive’s performance.
To resolve poor adhesion, consider the following:
- Thorough Cleaning: Carefully clean the glass surfaces with a recommended cleaner, such as isopropyl alcohol or a specialized glass cleaner, ensuring all contaminants are removed. Allow the surfaces to dry completely.
- Surface Preparation: Follow the adhesive manufacturer’s instructions for surface preparation, which may include etching or priming. This enhances the surface for optimal bonding.
- Proper Application: Apply the adhesive evenly, using the recommended amount and technique. Ensure full contact between the adhesive and both glass surfaces.
- Check Expiration Date: Verify the adhesive’s expiration date before use. Discard expired adhesive.
- Control Environmental Conditions: Apply and cure the adhesive within the recommended temperature and humidity ranges specified by the manufacturer. This might involve using a climate-controlled environment.
Bubbling, Food safe glass adhesive
Bubbles trapped within the adhesive can weaken the bond and create aesthetic imperfections. This can occur during application or curing.The primary causes of bubbling include:
- Air Entrapment: Air can become trapped within the adhesive during mixing or application, particularly if the adhesive is applied too quickly.
- Outgassing: Certain adhesives may release gases during the curing process, especially in confined spaces.
- Improper Mixing: Inadequate mixing of multi-component adhesives can lead to uneven curing and bubble formation.
To address bubbling:
- Slow Application: Apply the adhesive slowly and carefully to minimize air entrapment.
- De-gassing: If applicable, consider de-gassing the adhesive before application, as suggested by the manufacturer. This can be achieved through vacuum techniques.
- Proper Mixing: Thoroughly mix multi-component adhesives according to the manufacturer’s instructions. Use a mixing tool and ensure all components are fully combined.
- Controlled Curing: Avoid rapid temperature changes during curing, which can exacerbate outgassing.
Discoloration
Discoloration, or changes in the adhesive’s color, can affect the appearance and, in some cases, the functionality of the bonded glass. This is more prevalent in clear adhesives.Common causes of discoloration are:
- UV Exposure: Prolonged exposure to ultraviolet (UV) light can cause some adhesives to yellow or discolor over time.
- Chemical Reactions: Contact with certain chemicals, food products, or cleaning agents can trigger discoloration.
- Improper Curing: Incomplete curing or exposure to incorrect temperatures can lead to color changes.
Solutions for discoloration include:
- UV Protection: Use adhesives specifically formulated with UV stabilizers if the bonded glass will be exposed to sunlight.
- Chemical Compatibility: Ensure the adhesive is compatible with the substances it will come into contact with. Check the manufacturer’s guidelines for chemical resistance.
- Proper Curing: Follow the manufacturer’s instructions for curing, including temperature and time requirements.
- Avoid Harsh Cleaning Agents: Use only recommended cleaning agents and avoid those known to react with the adhesive.
Storage and Handling
Proper storage and careful handling are crucial for maintaining the integrity, performance, and safety of food-safe glass adhesive. Adhering to recommended practices ensures the adhesive remains effective, prevents premature degradation, and protects individuals from potential hazards. This section Artikels essential guidelines for storing and handling these specialized adhesives.
Storage Conditions
Maintaining the appropriate storage environment is paramount to preserving the quality and extending the shelf life of food-safe glass adhesives. Inappropriate storage can lead to changes in viscosity, reduced adhesion strength, and even complete solidification of the product.
- Temperature: Food-safe glass adhesives should be stored in a cool, dry place, ideally between 5°C (41°F) and 25°C (77°F). Avoid storing the adhesive in areas subject to extreme temperature fluctuations, as this can compromise its chemical stability. High temperatures can accelerate degradation, while freezing can alter the adhesive’s composition.
- Humidity: Keep the adhesive away from high humidity. Moisture can react with the adhesive components, leading to premature curing or the formation of undesirable byproducts. A controlled environment with low humidity is preferable.
- Direct Sunlight: Protect the adhesive from direct sunlight. Ultraviolet (UV) radiation can degrade the adhesive’s polymers, reducing its effectiveness. Store the adhesive in its original, opaque container, or in a dark location.
- Container Integrity: Ensure the adhesive container is tightly sealed when not in use. This prevents the ingress of air and moisture, which can affect the adhesive’s properties. Regularly inspect the container for any signs of damage or leakage.
- Shelf Life: Adhere to the manufacturer’s specified shelf life. Most food-safe glass adhesives have a defined shelf life, typically indicated on the product label. Using expired adhesive may result in poor adhesion and compromised safety. It is advisable to rotate stock, using older products first.
Safe Handling Practices
Working with food-safe glass adhesive requires adherence to specific safety protocols to minimize potential hazards. These practices protect the user from exposure to chemicals and ensure the adhesive is applied safely and effectively.
- Personal Protective Equipment (PPE): Always wear appropriate PPE when handling food-safe glass adhesive. This typically includes:
- Gloves: Chemical-resistant gloves, such as nitrile or butyl rubber gloves, are essential to protect the skin from contact with the adhesive.
- Eye Protection: Safety glasses or goggles are necessary to shield the eyes from splashes or fumes.
- Respiratory Protection: In poorly ventilated areas, or when working with adhesives that release significant fumes, use a respirator with an appropriate filter. Consult the Safety Data Sheet (SDS) for specific respiratory protection recommendations.
- Protective Clothing: Wear a lab coat or other protective clothing to prevent the adhesive from contacting skin and clothing.
- Ventilation: Work in a well-ventilated area to minimize exposure to adhesive fumes. If adequate ventilation is not available, use a local exhaust system.
- Skin Contact: Avoid direct skin contact with the adhesive. If contact occurs, immediately wash the affected area with soap and water. Do not use solvents to remove the adhesive from the skin, as this can worsen irritation.
- Eye Contact: If the adhesive gets into the eyes, flush them immediately with plenty of water for at least 15 minutes and seek medical attention.
- Ingestion: Do not ingest the adhesive. If ingested, seek immediate medical attention and provide the SDS to the medical professional.
- Spills: Clean up spills promptly and thoroughly. Use absorbent materials to contain the spill, and dispose of the waste properly according to local regulations. Consult the SDS for specific spill cleanup procedures.
- Flammability: Some food-safe glass adhesives may be flammable. Keep the adhesive away from open flames, sparks, and other sources of ignition. Store the adhesive in a cool, well-ventilated area, away from flammable materials.
- SDS: Always consult the Safety Data Sheet (SDS) for detailed safety information, including hazards, first-aid measures, handling procedures, and disposal guidelines. The SDS provides crucial information for safe handling and use of the adhesive.
Best Practices for Storage and Handling
Implementing these best practices helps ensure the safe and effective use of food-safe glass adhesives, maintaining product quality and protecting user safety.
- Inventory Management: Maintain a well-organized inventory system. Clearly label all containers with the product name, lot number, and expiration date. Rotate stock, using older products first.
- Training: Provide comprehensive training to all personnel who handle food-safe glass adhesives. Training should cover safety procedures, proper application techniques, and spill cleanup protocols.
- SDS Accessibility: Ensure that the SDS for each adhesive used is readily accessible to all personnel. Keep the SDS in a designated location and update it regularly.
- Regular Inspections: Conduct regular inspections of storage areas and handling practices. This helps identify and correct any potential safety hazards or storage deficiencies.
- Waste Disposal: Dispose of adhesive waste and empty containers according to local, state, and federal regulations. Do not pour adhesive down drains or into the environment. Consult the SDS for specific disposal guidelines.
- Emergency Procedures: Establish and communicate emergency procedures for dealing with spills, fires, or other incidents involving food-safe glass adhesives. Ensure that all personnel are familiar with these procedures.
- Material Compatibility: Be aware of material compatibility issues. Some adhesives may react with certain materials, such as plastics or metals. Consult the manufacturer’s recommendations for material compatibility.
- Temperature Monitoring: Implement a system for monitoring the storage temperature, especially if temperature-sensitive adhesives are used. Record temperature fluctuations to ensure the adhesive is stored within the recommended range.
- Preventative Maintenance: Regularly inspect application equipment, such as dispensing guns and nozzles, to ensure they are in good working order. Clean and maintain equipment according to the manufacturer’s instructions.
- Documentation: Maintain records of adhesive usage, storage conditions, and any incidents that occur. This documentation is essential for tracking product performance, identifying potential issues, and ensuring compliance with safety regulations.
Future Trends and Innovations: Food Safe Glass Adhesive
The food-safe glass adhesive sector is poised for significant advancements, driven by consumer demand for sustainability, enhanced product safety, and improved manufacturing efficiency. These trends are leading to the development of novel adhesive technologies and application methods.
Eco-Friendly Formulations
The environmental impact of manufacturing processes is increasingly scrutinized. This scrutiny is driving the development of eco-friendly food-safe glass adhesives.* The emphasis is on reducing the use of volatile organic compounds (VOCs) and hazardous air pollutants (HAPs).
- Bio-based adhesives derived from renewable resources like plant oils, starches, and cellulose are gaining prominence.
- These adhesives offer a reduced carbon footprint and improved worker safety.
- Manufacturers are also exploring the use of recycled materials in adhesive formulations.
- The development of water-based adhesives is another key trend, as they offer a safer and more environmentally friendly alternative to solvent-based adhesives.
Advanced Curing Methods
Traditional curing methods often involve lengthy waiting periods and energy-intensive processes. New technologies are emerging to accelerate the curing process.* UV-curing adhesives, which cure rapidly upon exposure to ultraviolet light, are becoming more common.
- These adhesives enable faster production cycles and reduce the need for large curing ovens.
- Microwave curing is another emerging technology, offering rapid and uniform curing of adhesives.
- Induction curing, which uses electromagnetic fields to generate heat within the adhesive, is also being explored.
- These advanced curing methods offer improved process control and reduced energy consumption.
Cutting-Edge Adhesive Technology: Smart Adhesives
A significant innovation is the development of “smart” adhesives that incorporate advanced functionalities. This technology represents a leap forward in both performance and safety.* Description: Imagine an adhesive that not only bonds glass but also integrates sensors. These sensors can detect changes in temperature, pressure, or the presence of contaminants. The adhesive itself might change color to indicate degradation or contamination, providing a visual warning.
It could also release antimicrobial agents in response to bacterial growth, ensuring product safety.
Advantages
Enhanced Safety
Real-time monitoring of the bonded structure for potential hazards.
Improved Shelf Life
Detection of early spoilage indicators.
Reduced Waste
Proactive alerts to prevent product contamination and disposal.
Optimized Packaging
Intelligent packaging that provides feedback on the product’s condition.
Predictive Maintenance
Monitoring of adhesive integrity over time.
“Smart adhesives represent a convergence of materials science, sensor technology, and data analytics, offering unprecedented control and insights into the performance of food-safe glass bonding applications.”
* Real-World Examples: While still in the early stages, some research groups are exploring the use of nanoparticles in adhesives to enhance their properties. These nanoparticles could be designed to change color or release specific compounds in response to environmental changes. This would allow manufacturers to detect problems early and take corrective action, ensuring the safety and quality of the food product.
Another example includes the development of adhesives with built-in RFID tags to track the location and condition of the bonded components throughout the supply chain.
Last Point
In conclusion, food safe glass adhesive is more than just an adhesive; it’s a cornerstone of food safety and product integrity. From its carefully selected materials and adherence to strict regulations to its versatile applications and continuous advancements, this technology continues to evolve, ensuring a safer and more reliable food supply chain. Understanding its nuances and embracing its potential is essential for both manufacturers and consumers alike, promising a future where food safety remains paramount.