Food safe plastic glue is a crucial topic, and this guide will delve into its intricacies. It’s essential to understand the term “food safe” within the context of adhesives, which indicates that the glue will not leach harmful chemicals into food products. This exploration is vital across various applications, from food packaging to kitchen appliances, emphasizing the importance of choosing the right adhesive for safety and compliance.
This guide will cover the different types of food-safe plastic glues available, their properties, and the materials they bond. Furthermore, it will examine the regulations and standards that govern these adhesives, providing insights into selecting and applying the appropriate glue for your specific needs. Practical advice on application techniques, troubleshooting common issues, and alternative joining methods will also be included, ensuring a comprehensive understanding of food-safe plastic glue.
Introduction: Understanding Food Safe Plastic Glue
Food-safe plastic glue is a crucial component in various industries where contact with consumables is unavoidable. This adhesive type ensures that the materials used in the manufacturing, packaging, and repair of items do not pose a health risk to consumers. Understanding its properties, applications, and importance is vital for maintaining consumer safety and complying with regulatory standards.
Defining “Food Safe” Adhesives
The term “food safe” in the context of adhesives signifies that the glue’s composition and the materials it contacts are not expected to transfer harmful substances to food products. This includes the absence of toxic chemicals, migration of hazardous compounds, and the ability to withstand conditions like heat, moisture, and contact with food substances without degrading or leaching harmful components.
Adhesives must meet specific regulations and standards established by food safety agencies like the U.S. Food and Drug Administration (FDA) and the European Food Safety Authority (EFSA).
Common Uses of Food-Safe Plastic Glue
Food-safe plastic glue finds applications across a wide range of industries, playing a vital role in the integrity and safety of food-related products. Its uses include:
- Food Packaging: Gluing cardboard boxes, plastic containers, and labels that come into direct contact with food items.
- Food Processing Equipment: Assembly and repair of machinery used in food preparation and processing.
- Beverage Industry: Sealing of bottles, cans, and cartons containing beverages.
- Food Service: Repairing or assembling serving trays, utensils, and other items that come into contact with food.
- Household Applications: Repairing plastic containers and kitchenware used for food storage and preparation.
Importance of Food-Safe Glue in Applications
Using food-safe glue is paramount for several reasons, primarily centered around consumer health and regulatory compliance. Failure to use appropriate adhesives can lead to serious consequences.
- Preventing Contamination: Food-safe glue prevents the migration of harmful chemicals into food products, thus safeguarding consumer health.
- Compliance with Regulations: Adhering to food safety regulations is a legal requirement. Using food-safe glue ensures compliance with these standards.
- Maintaining Product Integrity: Food-safe glue contributes to the structural integrity of packaging and equipment, preventing leaks, spills, and spoilage.
- Protecting Brand Reputation: Using food-safe glue protects the manufacturer’s reputation and maintains consumer trust by demonstrating a commitment to safety.
Types of Food Safe Plastic Glue
The selection of food-safe plastic glue depends heavily on the specific application, the types of plastics involved, and the environmental conditions the bonded items will encounter. Several formulations are designed to meet the stringent requirements of food contact, each possessing unique characteristics.
Food-Safe Glue Categories
Understanding the available types of food-safe plastic glues is essential for making an informed choice. These glues are formulated to minimize the risk of chemical migration into food, ensuring consumer safety.
- Epoxy: Epoxy adhesives are known for their high strength and durability. They consist of two components: a resin and a hardener. When mixed, a chemical reaction occurs, resulting in a strong, rigid bond. Food-safe epoxies often utilize specific resins and hardeners that are approved for food contact.
- Cyanoacrylate (Super Glue): Cyanoacrylate glues, commonly known as super glues, offer rapid bonding capabilities. They work by reacting with moisture present on the surfaces being bonded. Food-safe versions are available, formulated with ingredients that comply with food safety regulations.
- Polyurethane: Polyurethane adhesives are flexible and resistant to impact. They are often used in applications where some movement or vibration is expected. Food-safe polyurethane glues are designed to maintain their integrity under various conditions.
- UV-Curing Adhesives: These adhesives cure when exposed to ultraviolet (UV) light. They are advantageous for their fast curing times and precise application. Food-safe UV-curing adhesives use photoinitiators and resins that are safe for food contact.
Glue Properties Comparison
The performance characteristics of each glue type vary significantly. The following table provides a comparative overview of key properties to aid in selection.
Glue Type | Advantages | Disadvantages | Drying Time | Strength | Temperature Resistance |
---|---|---|---|---|---|
Epoxy | High strength, excellent durability, good chemical resistance. | Longer curing time, can be brittle in some formulations. | 30 minutes – 24 hours (depending on formulation) | Very High | High (up to 200°C / 392°F, depending on formulation) |
Cyanoacrylate | Rapid bonding, easy to use. | Lower strength compared to epoxy, less resistant to moisture and solvents. | Seconds – minutes | Medium | Low (typically up to 80°C / 176°F) |
Polyurethane | Flexible bond, good impact resistance, good for dissimilar materials. | Slower curing time than cyanoacrylate, can be sensitive to moisture during application. | 30 minutes – 8 hours (depending on formulation) | Medium | Medium (typically up to 100°C / 212°F) |
UV-Curing | Fast curing, precise application, excellent for clear bonds. | Requires UV light source, may not bond opaque materials effectively. | Seconds | Medium – High (depending on formulation) | Medium (typically up to 120°C / 248°F) |
Chemical Composition and Food Safety
The chemical composition of food-safe glues is crucial for ensuring compliance with food safety regulations. Manufacturers carefully select ingredients to minimize the risk of harmful substances migrating into food.
- Epoxy: Food-safe epoxy formulations typically utilize bisphenol A diglycidyl ether (BADGE)-free resins or those with very low levels of BADGE. Hardeners are chosen for their inertness and lack of harmful byproducts.
- Cyanoacrylate: Food-safe cyanoacrylate glues are often formulated with stabilizers and additives that are approved for food contact. The primary ingredient, cyanoacrylate monomer, itself, must meet stringent purity standards.
- Polyurethane: Food-safe polyurethane adhesives use isocyanates and polyols that have been assessed for food contact. The final cured product is designed to be inert and not leach harmful chemicals.
- UV-Curing Adhesives: These adhesives rely on photoinitiators and resins that are approved for food contact. The curing process converts the liquid adhesive into a solid, inert polymer, minimizing the risk of migration.
The specific regulations governing food-safe materials vary by region. For example, in the United States, the Food and Drug Administration (FDA) regulates food contact materials. In Europe, the European Food Safety Authority (EFSA) provides guidance. Always check the manufacturer’s documentation to ensure compliance with relevant regulations.
Materials Commonly Bonded with Food Safe Plastic Glue
Understanding the materials that food-safe plastic glue can effectively bond is crucial for its proper application. The following information provides a detailed overview of the common plastics suitable for use with food-safe adhesives, the necessary surface preparation techniques, and methods for identifying the plastic type. This ensures the user can select the correct adhesive and achieve a durable and safe bond.
Commonly Bonded Plastics, Food safe plastic glue
Several types of plastics are frequently bonded using food-safe glue. It’s important to note that while a glue may be food-safe, the bond’s integrity and suitability for food contact depend on the specific plastic being used and the intended application.
- Polyethylene (PE): Commonly found in food packaging like plastic bags, bottles, and containers. It offers excellent chemical resistance and flexibility.
- Polypropylene (PP): Used for food containers, lids, and microwave-safe food packaging. PP is known for its high melting point and resistance to solvents.
- Polyethylene Terephthalate (PET or PETE): Often used for beverage bottles, food jars, and packaging trays. PET is clear, strong, and recyclable.
- Polystyrene (PS): Found in disposable cutlery, cups, and food containers. PS can be brittle and less resistant to certain chemicals.
- Polyvinyl Chloride (PVC): Used in food wrap and some food packaging applications. PVC’s suitability for food contact can depend on the specific formulation and additives.
Surface Preparation for Effective Bonding
Proper surface preparation is critical for achieving a strong and durable bond with food-safe plastic glue. The specific preparation steps will vary depending on the plastic type. However, the general principles remain the same.
- Cleaning: Remove any contaminants like grease, oil, dust, or food residue. Use a suitable cleaning agent, such as isopropyl alcohol, specifically formulated for plastics. Avoid harsh solvents that could damage the plastic.
- Abrasion (Optional): Lightly abrading the surface with fine-grit sandpaper or a Scotch-Brite pad can increase the surface area and improve adhesion, particularly for smooth plastics.
- Rinsing: After cleaning or abrasion, rinse the surface thoroughly with clean water and allow it to dry completely before applying the adhesive.
- Application: Apply the food-safe glue according to the manufacturer’s instructions. Ensure the glue is applied evenly and that the parts are properly aligned.
- Curing: Allow the adhesive to cure fully, as specified by the manufacturer, before exposing the bonded items to food or liquids.
Identifying Plastic Types
Identifying the type of plastic is crucial for selecting the correct food-safe glue and preparing the surface appropriately. There are several methods to determine the plastic type.
- Recycling Codes: Look for the recycling symbol (a triangle with chasing arrows) on the plastic item. Inside the triangle, a number from 1 to 7 indicates the plastic type. This is the most common and easiest way to identify the plastic. For example, “1” represents PETE, and “2” represents HDPE.
- Visual Inspection and Physical Properties: Observe the plastic’s appearance, flexibility, and texture. For example, PET is often clear, while PP is translucent.
- Burn Test (Use with extreme caution and only in a well-ventilated area): This test involves burning a small sample of the plastic and observing the flame, smoke, and odor. This test should be performed with great care, as some plastics can release toxic fumes. However, this method is not recommended for food contact items due to the potential for contamination.
- Chemical Resistance Tests: These tests involve exposing the plastic to various chemicals and observing its reaction. This method is best left to professionals with the appropriate equipment and expertise.
Applications of Food Safe Plastic Glue
Food-safe plastic glue plays a vital role in the food industry, providing a reliable and hygienic method for bonding various plastic components. Its versatility makes it indispensable in manufacturing, repair, and maintenance, ensuring the integrity and safety of food-related products. This section will explore specific applications, detailing practical procedures and highlighting essential safety considerations.
Applications in the Food Industry
Food-safe plastic glue finds numerous applications across the food industry. Its ability to create strong, durable bonds while adhering to strict safety standards makes it ideal for various uses.* Food Packaging: This is a primary application. The glue is used in assembling plastic containers, trays, and films that directly contact food. This includes sealing lids, joining container components, and creating airtight seals to preserve freshness and prevent contamination.
Kitchen Appliances
Manufacturers utilize food-safe glue in the construction of blenders, food processors, and other appliances. The glue secures plastic parts like housings, handles, and internal components, ensuring structural integrity and preventing leaks.
Food Processing Equipment
In food processing plants, the glue is used in assembling machinery components, such as conveyor belts, hoppers, and other equipment that comes into contact with food. The glue’s resistance to chemicals and high temperatures makes it suitable for harsh environments.
Beverage Containers
The glue is crucial in manufacturing plastic bottles, jugs, and other beverage containers. It seals the container components, creating a leak-proof and secure vessel for holding liquids.
Repair and Maintenance
The glue is essential for repairing damaged plastic items used in the food industry. This can range from broken containers to damaged appliance parts.
Gluing Procedures for Repairing a Plastic Food Container
Repairing a plastic food container with food-safe glue requires careful attention to detail to ensure a secure and hygienic bond. Following these steps will help achieve a successful repair.* Preparation: Begin by thoroughly cleaning the damaged area of the container. Remove any food residue, grease, or dirt using warm, soapy water and a clean cloth. Ensure the area is completely dry before proceeding.
Surface Preparation
Lightly roughen the surfaces to be glued with fine-grit sandpaper. This enhances the adhesion of the glue. Be sure to remove any sanding residue with a clean cloth.
Glue Application
Apply a thin, even layer of food-safe plastic glue to both surfaces to be joined. Avoid excessive glue, as this can weaken the bond and create unsightly residue.
Joining the Surfaces
Carefully align the broken pieces and press them firmly together. Hold them in place for the recommended curing time specified by the glue manufacturer. This may involve using clamps or tape to maintain pressure.
Curing
Allow the glue to cure completely according to the manufacturer’s instructions. The curing time is crucial for achieving a strong and durable bond. Avoid moving or stressing the container during this period.
Inspection
Once the glue has fully cured, inspect the repair. Ensure there are no gaps or weak points. If necessary, apply a second coat of glue to reinforce the bond.
Cleaning
After the glue has completely cured, clean the repaired area with warm, soapy water. Rinse thoroughly to remove any glue residue. The container is now ready for use.
Potential Risks and Safety Measures
While food-safe plastic glue is designed to be safe for use with food, it’s essential to follow safety precautions to minimize risks.* Chemical Composition Awareness: Always review the glue’s material safety data sheet (MSDS) to understand its chemical composition and potential hazards. This document provides critical information about the glue’s ingredients, potential health risks, and safe handling procedures.
Ventilation
Work in a well-ventilated area when applying the glue. Some glues may release fumes that can cause irritation or other health issues. Ensure adequate airflow to prevent the build-up of harmful vapors.
Personal Protective Equipment (PPE)
Wear appropriate PPE, such as gloves and eye protection, to protect yourself from skin and eye contact with the glue. This will help prevent irritation and allergic reactions.
Skin Contact
Avoid direct skin contact with the glue. If the glue comes into contact with your skin, wash the affected area immediately with soap and water.
Eye Contact
If the glue gets into your eyes, flush them with plenty of water for at least 15 minutes and seek medical attention.
Ingestion
Never ingest food-safe plastic glue. If ingested, seek immediate medical attention.
Storage
Store the glue in a cool, dry place, away from direct sunlight and heat sources. Keep the container tightly sealed when not in use.
Food Contact Guidelines
Always follow the manufacturer’s guidelines regarding the glue’s suitability for direct food contact. Ensure the glue is specifically labeled as food-safe and complies with relevant regulations.
Enhance your insight with the methods and methods of breakfast food truck ideas.
Curing Time Compliance
Adhere strictly to the recommended curing time specified by the manufacturer. Premature use of the glued item can compromise the bond and potentially introduce harmful chemicals into the food.
Surface Compatibility
Ensure the glue is compatible with the plastic material being bonded. Using the wrong type of glue can result in a weak bond or chemical reactions that compromise the integrity of the container.
Proper Disposal
Dispose of glue and empty containers according to local regulations. Do not pour glue down the drain or into the environment.
Selection Criteria for Food Safe Plastic Glue
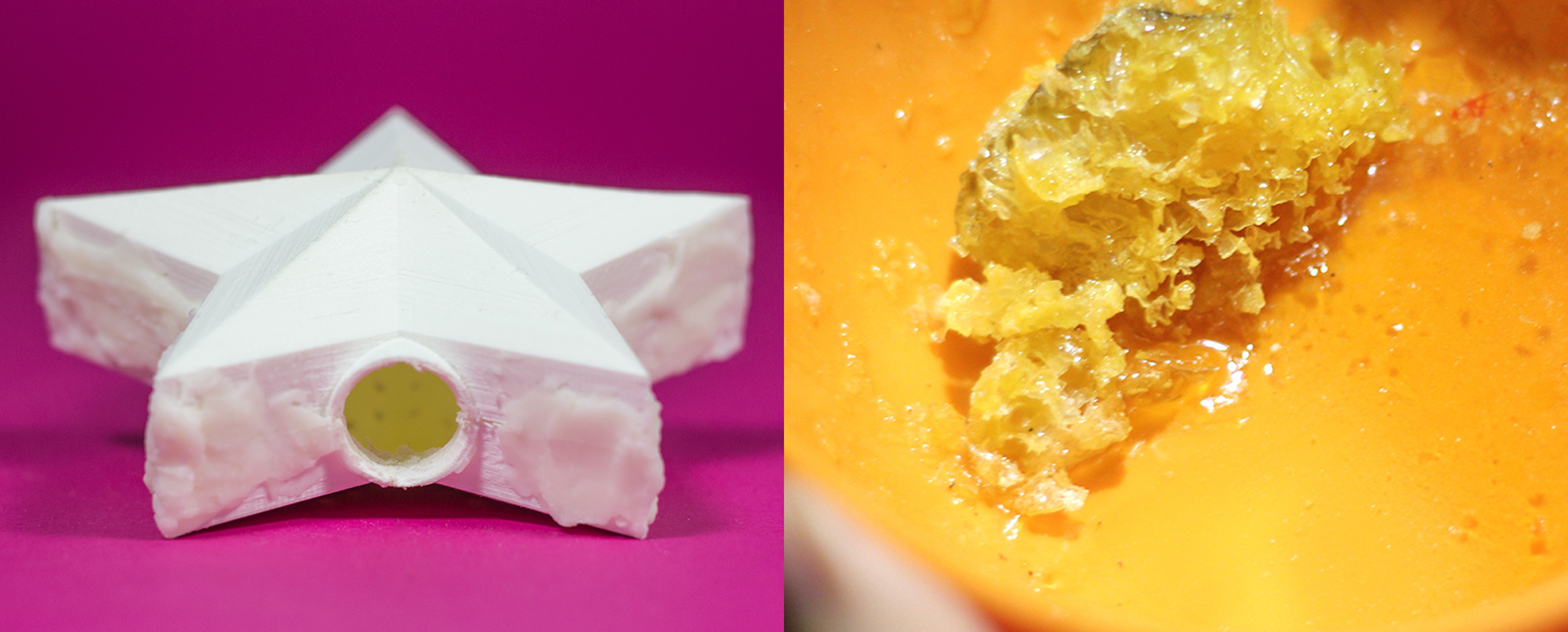
Choosing the correct food-safe plastic glue is crucial for ensuring the safety and integrity of food-related items. Several factors must be carefully considered to select the most appropriate adhesive for a given application. Failure to do so can lead to compromised seals, potential contamination, and ultimately, health risks.
Factors Influencing Glue Selection
Several key factors should guide the selection process when choosing a food-safe plastic glue. These considerations ensure the glue meets the specific requirements of the application and maintains food safety standards.
- Type of Plastic: Different plastics have varying surface energies and react differently to adhesives. The glue must be compatible with the specific plastic being bonded, such as polyethylene (PE), polypropylene (PP), polycarbonate (PC), or others. Compatibility ensures proper adhesion and bond strength.
- Application Environment: The environment in which the bonded item will be used significantly impacts glue selection. Consider factors such as temperature fluctuations, exposure to moisture, and the presence of cleaning agents. The glue must maintain its integrity under these conditions.
- Temperature Resistance: The glue’s ability to withstand a range of temperatures is critical. This includes both the temperatures during application and the temperatures the bonded item will experience during use, storage, or processing. Inadequate temperature resistance can lead to bond failure.
- Food Contact: The glue must be certified as food-safe and comply with relevant regulations, such as those set by the FDA (Food and Drug Administration) in the United States or the European Union’s regulations. This ensures the glue does not leach harmful chemicals into the food.
- Bond Strength Requirements: The required strength of the bond is a critical factor. Consider the stresses the bond will experience, such as tensile, shear, and peel forces. The glue must provide sufficient strength to withstand these forces.
- Cure Time: The time it takes for the glue to cure and reach its full bond strength is important. This impacts production efficiency and the time required before the bonded item can be used.
- Chemical Resistance: The glue’s resistance to chemicals, including cleaning agents, solvents, and food ingredients, is important. Exposure to these chemicals can weaken the bond over time.
Comparative Performance of Different Glues
The performance of food-safe plastic glues varies significantly depending on the type of glue and the conditions it is exposed to. The following table provides a comparative overview of different glue types under various conditions.
Glue Type | Condition | Performance | Notes |
---|---|---|---|
Epoxy (Food-Safe) | Exposure to Moisture | Excellent | Provides a strong, water-resistant bond. Ideal for applications involving frequent washing or exposure to liquids. |
Cyanoacrylate (Food-Safe) | Exposure to Heat (up to 80°C/176°F) | Good | Offers rapid bonding but may degrade at higher temperatures. Suitable for applications with moderate heat exposure. |
Polyurethane (Food-Safe) | Exposure to Cleaning Agents | Good | Resists many common cleaning agents, making it suitable for applications where regular cleaning is required. However, resistance varies by the specific cleaning agent. |
Silicone (Food-Safe) | Exposure to UV Light | Excellent | Provides excellent resistance to UV degradation, making it suitable for outdoor or sunlight-exposed applications. |
Modified Acrylic (Food-Safe) | Bonding to Polypropylene (PP) | Good | Some modified acrylics are specifically formulated for difficult-to-bond plastics like PP, offering improved adhesion compared to general-purpose adhesives. |
Importance of Selecting the Right Glue
Selecting the appropriate glue is not merely a matter of convenience but a critical aspect of ensuring food safety and the longevity of the bonded item.
- Preventing Contamination: Using the wrong glue can lead to the leaching of harmful chemicals into food, posing serious health risks. A food-safe glue certified by regulatory bodies is essential.
- Maintaining Bond Integrity: The glue must withstand the application environment, including temperature, moisture, and chemical exposure. Selecting the right glue ensures the bond remains intact and prevents leaks or separation.
- Ensuring Product Durability: A properly selected glue provides the necessary bond strength to withstand the stresses the item will experience during its lifecycle. This extends the product’s lifespan and reduces the risk of failure.
- Compliance with Regulations: Adhering to food safety regulations, such as those set by the FDA, is crucial. Selecting a compliant glue is a necessary step in meeting these requirements and avoiding legal issues.
Application Techniques and Best Practices
Applying food-safe plastic glue correctly is crucial for ensuring the bond’s integrity and, consequently, the safety of the food it may come into contact with. Proper application techniques not only maximize the adhesive’s effectiveness but also minimize the risk of contamination. Following these best practices will help achieve strong, durable, and food-safe bonds.
Surface Preparation for Optimal Adhesion
Effective surface preparation is the cornerstone of a successful bond. The surfaces to be joined must be meticulously prepared to remove any contaminants that could interfere with the glue’s adhesion. This process significantly influences the bond’s strength and longevity.
- Cleaning: Thoroughly clean the surfaces with a suitable solvent, such as isopropyl alcohol, specifically designed for the plastic type being bonded. This removes grease, oil, dust, and other debris. Avoid using solvents that could damage the plastic. Ensure the surfaces are completely dry before proceeding.
- Abrasion (if applicable): For certain plastics, particularly those with smooth surfaces, lightly abrading the surfaces with fine-grit sandpaper can improve adhesion. This creates a slightly rough surface that provides more surface area for the glue to grip. However, this step isn’t always necessary and depends on the plastic type and the glue’s formulation. Always test on a small, inconspicuous area first.
- Surface Activation (for challenging plastics): Some plastics, like polyethylene or polypropylene, are notoriously difficult to bond. In these cases, surface activation may be necessary. This can involve using specialized primers or treatments to modify the plastic’s surface and enhance its receptivity to the glue.
Application Techniques
The method of applying the glue depends on the type of glue and the specific application. However, several general principles apply to most food-safe plastic glues.
- Glue Application: Apply the glue sparingly, following the manufacturer’s instructions. Too much glue can weaken the bond and lead to unsightly residue. A thin, even layer is usually sufficient. Use the applicator tip provided by the manufacturer to ensure precise application.
- Bonding: Immediately after applying the glue, bring the surfaces together and hold them firmly in place. The required clamping time will vary depending on the glue type and the manufacturer’s specifications. Ensure the parts are aligned correctly during this stage.
- Clamping: Use clamps, tape, or weights to maintain consistent pressure during the curing process. Proper clamping ensures intimate contact between the surfaces, maximizing the bond’s strength. The clamping pressure should be sufficient to hold the parts together without distorting them.
- Curing Time: Allow the glue to cure completely before subjecting the bonded item to stress or use. The curing time can range from minutes to hours, depending on the glue and the environmental conditions. Refer to the manufacturer’s instructions for specific curing times.
Removing Excess Glue and Cleaning Spills
Managing excess glue and spills is crucial for maintaining a clean and safe work environment and ensuring the aesthetic appearance of the bonded item.
- Removing Excess Glue: Wipe away any excess glue immediately with a clean cloth or paper towel, following the manufacturer’s recommendations. Use a solvent appropriate for the glue type and the plastic being bonded.
- Cleaning Spills: If a spill occurs, contain it immediately. Use absorbent materials, such as paper towels or cloths, to soak up the spill. Dispose of the absorbent materials properly, following local regulations. Wear appropriate personal protective equipment (PPE), such as gloves and eye protection, during the cleanup process.
- Solvent Selection: Always use the correct solvent recommended by the glue manufacturer to avoid damaging the plastic. Test the solvent on an inconspicuous area first to ensure it doesn’t affect the plastic’s surface.
Troubleshooting Common Issues
Using food-safe plastic glue, while generally straightforward, can sometimes present challenges. Understanding these potential problems and how to address them is crucial for achieving strong, durable, and safe bonds. This section focuses on identifying and resolving common issues that users may encounter during the application process.
Weak Bonds
Weak bonds are perhaps the most frequent issue encountered when using food-safe plastic glue. This can manifest as the joined pieces separating easily or failing under minimal stress. Several factors can contribute to this problem.
- Surface Contamination: Contaminants like grease, oil, dust, or residue from previous adhesives can prevent the glue from properly adhering to the plastic surfaces. This is a very common cause of weak bonds.
- Incorrect Surface Preparation: Inadequate preparation, such as failing to roughen smooth surfaces or clean them thoroughly, can compromise the bond’s strength.
- Improper Glue Application: Applying too little glue, applying glue unevenly, or applying glue to the wrong surfaces can result in a weak bond.
- Incorrect Glue Selection: Using a glue that is not specifically designed for the type of plastic being bonded or that is not food-safe can lead to bond failure.
- Curing Time: Allowing insufficient curing time, or working in conditions outside the recommended temperature and humidity range, can prevent the glue from fully setting and achieving its maximum strength.
To troubleshoot weak bonds, the following steps are recommended:
- Surface Cleaning: Thoroughly clean the plastic surfaces with a suitable cleaner (e.g., isopropyl alcohol) to remove any contaminants. Let the surfaces dry completely.
- Surface Preparation: Lightly roughen smooth plastic surfaces using fine-grit sandpaper or a specialized plastic surface preparation tool. This creates a better surface for the glue to grip.
- Glue Application: Apply an adequate amount of glue evenly across the surfaces to be bonded. Ensure the glue covers the entire bonding area.
- Glue Selection Review: Double-check that the chosen glue is appropriate for the specific type of plastic being used and is food-safe. Refer to the glue manufacturer’s recommendations.
- Curing Time and Conditions: Allow the glue to cure for the full recommended time under the appropriate temperature and humidity conditions. Avoid disturbing the bond during the curing process.
Slow Drying Times
Slow drying times can be a frustrating issue, especially when quick results are desired. While some food-safe plastic glues are designed for rapid bonding, others require a longer curing period. Several factors can influence the drying time.
- Temperature: Lower temperatures can significantly slow down the curing process. Most glues cure best at room temperature.
- Humidity: High humidity can also impact drying times, potentially slowing the process.
- Glue Type: Different types of food-safe plastic glues have varying drying times. Some require hours, while others may cure within minutes.
- Amount of Glue Applied: Applying an excessive amount of glue can extend the drying time, as the excess glue takes longer to cure.
- Ventilation: Poor ventilation can trap solvents released by the glue, potentially slowing down the curing process.
To troubleshoot slow drying times, consider the following:
- Temperature Adjustment: If possible, increase the ambient temperature to the recommended range for the glue.
- Humidity Control: Try to reduce the humidity in the working environment. A dehumidifier can be helpful.
- Glue Type Consideration: If speed is critical, consider using a faster-curing food-safe plastic glue.
- Glue Application Adjustment: Apply the recommended amount of glue. Avoid applying too much.
- Ventilation Improvement: Ensure adequate ventilation in the working area to allow solvents to evaporate.
Glue Not Adhering Properly
When the glue fails to adhere to the plastic surface, the bond will be weak or non-existent. This problem often stems from issues related to surface preparation or the glue itself.
- Surface Contamination: As with weak bonds, contaminants on the plastic surface can prevent proper adhesion.
- Incompatible Plastics: Some glues are not suitable for all types of plastic. Using an incompatible glue can result in poor adhesion.
- Expired Glue: Using expired glue can lead to adhesion problems, as the glue’s chemical composition may have degraded.
- Improper Application Technique: Incorrect application techniques, such as applying glue to only one surface or not clamping the pieces together, can prevent proper adhesion.
Solutions to this issue involve:
- Thorough Cleaning: Clean the plastic surfaces meticulously before applying the glue. Use a suitable cleaning agent, such as isopropyl alcohol.
- Plastic Compatibility Check: Verify that the glue is compatible with the specific type of plastic being used. Consult the glue manufacturer’s guidelines.
- Expiration Date Verification: Check the expiration date on the glue container. Discard and replace expired glue.
- Application Technique Review: Follow the manufacturer’s instructions for applying the glue. Ensure that the glue is applied to both surfaces (if required) and that the pieces are properly clamped together during the curing process.
Storage and Handling of Food Safe Plastic Glue
Proper storage and handling are critical to maintaining the effectiveness, safety, and longevity of food-safe plastic glue. This section Artikels essential guidelines to ensure the glue remains usable and prevents any potential contamination of food products.
Safe Storage Guidelines
Adhering to specific storage conditions is vital for preserving the glue’s integrity and preventing degradation. Incorrect storage can alter its properties, making it less effective or even unsafe for food-related applications.
- Temperature Control: Store the glue in a cool, dry place, ideally between 10°C and 25°C (50°F and 77°F). Avoid extreme temperatures, such as direct sunlight or freezing conditions, as these can negatively affect the glue’s chemical composition. For example, storing the glue in a hot car during summer can significantly reduce its shelf life and performance.
- Airtight Containers: Always store the glue in its original, tightly sealed container or a suitable airtight container. This prevents the glue from drying out, reacting with air, or absorbing moisture, which can lead to premature degradation.
- Proper Ventilation: Ensure the storage area is well-ventilated to prevent the buildup of fumes, especially if the glue contains volatile organic compounds (VOCs). Good ventilation also helps maintain consistent temperature and humidity levels.
- Away from Food Products: Store the glue separately from food products and food preparation areas to prevent accidental contamination. This includes keeping it away from ingredients, utensils, and surfaces used for food handling.
- Labeling and Identification: Clearly label the glue container with the product name, date of purchase, and any relevant safety information. This ensures proper identification and traceability.
Preventing Contamination During Handling
Handling food-safe plastic glue requires meticulous attention to hygiene to prevent contamination of both the glue and the food products it will come into contact with.
- Clean Hands: Always wash your hands thoroughly with soap and water before handling the glue. This minimizes the risk of transferring contaminants from your hands to the glue or the food product.
- Clean Tools and Surfaces: Use clean and dedicated tools, such as applicators, mixing containers, and dispensing equipment, when working with the glue. Avoid using tools that have been used with other substances, as cross-contamination can occur.
- Protective Gear: Wear appropriate personal protective equipment (PPE), such as gloves, when handling the glue to protect your skin and prevent contamination.
- Avoid Cross-Contamination: Do not use the same tools or surfaces for both the glue and food preparation. This prevents any transfer of the glue’s components to food products.
- Proper Disposal: Dispose of any excess glue, used applicators, and contaminated materials properly according to local regulations. Do not pour glue down the drain or dispose of it in a way that could contaminate the environment.
Shelf Life and Expiration Recognition
Understanding the shelf life of food-safe plastic glue and how to identify when it has expired is essential for ensuring its effectiveness and safety. Using expired glue can compromise the integrity of the bond and potentially introduce harmful substances into food products.
- Shelf Life Information: Check the manufacturer’s instructions for the specific shelf life of the glue. This information is usually printed on the product packaging. Common shelf lives range from 6 months to 2 years, depending on the type of glue and storage conditions.
- Expiration Date: Pay close attention to the expiration date printed on the container. Do not use the glue after this date, as its properties may have deteriorated.
- Visual Inspection: Regularly inspect the glue for any signs of degradation, such as:
- Changes in Consistency: The glue may become thicker, thinner, or develop lumps or clumps.
- Color Changes: The glue may change color from its original appearance.
- Separation: The glue may separate into different layers.
- Odor Changes: The glue may develop an unusual or unpleasant odor.
- Performance Tests: If you suspect the glue has expired or is nearing its expiration date, perform a small-scale test to assess its performance. Apply the glue to a sample material and check the bond strength and drying time.
- Disposal of Expired Glue: Dispose of expired glue according to local regulations. Do not use expired glue for any food-related applications.
Alternatives to Food Safe Plastic Glue
While food-safe plastic glue offers a convenient solution for bonding plastics in food-related applications, it’s not always the optimal choice. Several alternative methods exist, each with its own set of advantages and disadvantages. The best alternative often depends on factors such as the type of plastic, the desired strength of the bond, the specific application, and cost considerations. Understanding these alternatives empowers informed decision-making in choosing the most suitable joining method.
Plastic Welding
Plastic welding is a process that involves melting the surfaces of two plastic parts and fusing them together. This creates a strong, permanent bond without the use of adhesives. The process can be achieved using various methods, including hot gas welding, ultrasonic welding, and laser welding.
- Hot Gas Welding: This method uses a stream of heated gas, typically air or nitrogen, to melt the plastic surfaces and a filler rod made of the same plastic to create the weld. It’s a versatile technique suitable for various plastics and thicknesses. The welder holds a hot gas welding torch in one hand and the filler rod in the other.
The filler rod is fed into the weld pool as the welder moves the torch along the joint. The melted plastic from the filler rod fuses with the plastic parts, creating a solid bond.
- Ultrasonic Welding: This process uses high-frequency sound waves to generate heat at the interface of the plastic parts. The parts are held together under pressure, and the ultrasonic energy melts the plastic, creating a weld. It’s a fast and efficient method, particularly well-suited for joining small parts and producing large quantities. The process involves an ultrasonic welder, which includes a transducer to convert electrical energy into mechanical vibrations, a booster to amplify the vibrations, and a horn (also known as a sonotrode) that transmits the vibrations to the plastic parts.
- Laser Welding: This method uses a laser beam to melt the plastic along the joint. It’s a precise and controlled technique that can create strong, aesthetically pleasing welds. The laser beam is focused on the joint area, melting the plastic and fusing the parts together. This method is especially useful for joining transparent and opaque plastics.
Plastic welding offers several advantages, including high bond strength, resistance to solvents, and the absence of adhesives that could potentially contaminate food. However, it requires specialized equipment and skilled operators. Additionally, the process may not be suitable for all types of plastics, and the weld can sometimes be visible.
Mechanical Fasteners
Mechanical fasteners, such as screws, bolts, rivets, and clips, provide a method of joining plastic parts by physical means. These fasteners create a bond by clamping the parts together or by passing through them.
- Screws and Bolts: These fasteners offer a strong and easily adjustable method for joining plastic parts. They are available in various sizes, materials, and head styles, allowing for flexibility in design. Screws and bolts are generally used with pre-drilled holes in the plastic parts. The choice of screw or bolt depends on the application’s requirements, including the desired clamping force, the plastic’s thickness, and the environmental conditions.
- Rivets: Rivets are permanent fasteners that create a strong bond by expanding within a hole in the plastic parts. They are suitable for applications requiring a flush or smooth surface. Rivets are inserted into pre-drilled holes and then deformed to create a head on the opposite side, securing the parts together.
- Clips: Clips are typically used for quick assembly and disassembly. They are designed to snap onto or into plastic parts, providing a secure connection. Clips are often used in applications where access to the components is required for maintenance or repair.
Mechanical fasteners provide several benefits, including ease of assembly and disassembly, the ability to join dissimilar materials, and good resistance to temperature changes. However, they may require pre-drilled holes, which can weaken the plastic, and the fasteners themselves can sometimes create stress points. Also, there’s a potential for the fastener to corrode or come loose over time.
Scenarios Favoring Alternatives
Alternatives to food-safe plastic glue are often preferred in specific situations. For example, in applications involving high-stress environments or exposure to harsh chemicals, plastic welding or mechanical fasteners may be selected for their superior bond strength and durability. In the manufacturing of large-scale food processing equipment, such as storage tanks or conveyor systems, welding offers a reliable and cost-effective joining solution.
Method | Advantages | Disadvantages | Preferred Scenario |
---|---|---|---|
Plastic Welding | High bond strength, no adhesives, solvent resistance | Requires specialized equipment and skills, may not be suitable for all plastics, visible welds | High-stress environments, large-scale equipment manufacturing, applications requiring chemical resistance |
Mechanical Fasteners | Ease of assembly and disassembly, ability to join dissimilar materials, good temperature resistance | May require pre-drilled holes, can weaken the plastic, potential for corrosion or loosening | Applications requiring frequent access for maintenance, joining of dissimilar materials, situations where bond strength is not the primary concern |
Food-Safe Plastic Glue | Ease of use, versatility, suitable for a wide range of plastics | Bond strength may be limited, potential for contamination if not properly applied, less resistant to harsh chemicals | Smaller components, applications where ease of use and flexibility are critical, repairs or modifications to existing equipment |
For example, consider the scenario of manufacturing a large polyethylene (PE) storage tank for food-grade liquids. Welding would likely be the preferred method due to the high bond strength required, the need for a leak-proof seal, and the chemical resistance of the weld. Conversely, in the assembly of a small plastic food container, food-safe glue might be sufficient due to its ease of use and the less demanding requirements of the application.
Conclusion
In conclusion, understanding and correctly utilizing food-safe plastic glue is paramount for maintaining food safety and product integrity. This guide has covered the essentials, from the different types of glue and their properties to the necessary regulations and best application practices. By carefully considering factors like the plastic type, application environment, and adherence to safety guidelines, you can confidently select and use food-safe plastic glue, ensuring both functionality and consumer safety.
Remember to always prioritize safety and follow the recommended guidelines for storage, handling, and disposal.