B&G Foods Yadkinville represents a significant hub within the broader B&G Foods empire, a company with a rich history of acquiring and nurturing iconic food brands. This exploration will delve into the specifics of the Yadkinville facility, offering insights into its operations, the products it produces, and its impact on the local community. From its humble beginnings to its current standing, the Yadkinville facility has evolved, adapting to market demands and consumer preferences.
We will examine the facility’s infrastructure, the products manufactured there, and the intricate logistics that keep the operation running smoothly. Furthermore, this analysis will touch upon the company’s role in the Yadkinville community, its sustainability efforts, and its plans for the future. The aim is to provide a comprehensive understanding of B&G Foods’ presence in Yadkinville, showcasing its significance in the food industry and its commitment to responsible practices.
Overview of B&G Foods and its Yadkinville Operations
B&G Foods is a significant player in the packaged food industry, with a diverse portfolio of brands and products. The company’s growth has been primarily driven by strategic acquisitions, expanding its reach and market share. This section provides an overview of B&G Foods, focusing on its history, product offerings, and the importance of its Yadkinville, North Carolina, facility.
B&G Foods’ History and Growth
B&G Foods’ journey began with the acquisition of the B&G brand of pickles, relish, and peppers in 1996. Since then, the company has pursued an aggressive acquisition strategy, adding numerous well-known food brands to its portfolio. This growth strategy has allowed B&G Foods to diversify its product offerings and expand its distribution network. The company’s focus on acquiring established brands has enabled it to leverage existing consumer recognition and market presence.
The acquisitions have been instrumental in shaping B&G Foods into the company it is today.
B&G Foods’ Product Portfolio
B&G Foods manufactures and distributes a wide array of packaged food products. The company’s diverse portfolio caters to various consumer preferences and dietary needs.
- Canned Vegetables and Beans: Brands include Green Giant and S&W.
- Frozen Foods: Including Green Giant frozen vegetables.
- Snack Foods: Brands include Pirate’s Booty and Crisco.
- Spices and Seasonings: Brands include Mrs. Dash and Tone’s.
- Sauces and Condiments: Brands include Ortega and Polaner.
This diverse product range allows B&G Foods to appeal to a broad consumer base and maintain a strong presence across various grocery store aisles.
Significance of the Yadkinville, NC Facility
The Yadkinville, North Carolina, facility is a crucial part of B&G Foods’ operational infrastructure. The facility’s role is centered around production and distribution of various food products, contributing significantly to the company’s overall manufacturing capacity. The Yadkinville plant likely benefits from its location, providing access to raw materials and a distribution network. This strategic positioning helps to ensure efficient production and timely delivery of products to consumers.
The Yadkinville facility supports B&G Foods’ commitment to meeting consumer demand and maintaining a competitive edge in the packaged food industry.
Yadkinville Facility
B&G Foods’ Yadkinville facility is a critical component of the company’s manufacturing and distribution network. This facility plays a significant role in producing and supplying various food products to consumers across the United States. The following sections provide a detailed overview of its location, size, infrastructure, and operational capabilities.
Yadkinville Facility: Location and Infrastructure
The Yadkinville facility is strategically located in Yadkinville, North Carolina. This location provides advantageous access to transportation networks and a skilled workforce. The facility’s size and infrastructure are designed to support large-scale food production and efficient distribution.The Yadkinville facility’s infrastructure supports a complex operation. The facility’s layout is optimized for efficiency, from raw material receiving to finished product shipping.
Area | Description | Capacity | Technology |
---|---|---|---|
Manufacturing Lines | The facility houses multiple manufacturing lines dedicated to producing various B&G Foods products. These lines are equipped to handle different types of food processing, including canning, packaging, and labeling. | Production capacity varies depending on the product and the specific line, but the facility is designed for high-volume output. | Automated systems for filling, sealing, and packaging; robotic arms for handling products; advanced monitoring and control systems. |
Warehousing | Significant warehousing space is available for storing raw materials, work-in-progress, and finished goods. Warehousing is designed to maintain product quality and safety. | Warehousing capacity supports large inventories, ensuring continuous supply to distribution channels. The capacity is adjusted to match seasonal demands and production schedules. | Automated storage and retrieval systems (AS/RS); climate-controlled storage for sensitive products; warehouse management systems (WMS) for inventory tracking and order fulfillment. |
Distribution Capabilities | The facility has distribution capabilities to facilitate the efficient movement of products to retailers and other distribution centers. This includes loading docks, staging areas, and transportation logistics. | The distribution network handles a large volume of products daily, ensuring timely delivery to customers. | Loading docks with multiple bays; cross-docking capabilities; transportation management systems (TMS) to optimize routes and schedules; partnerships with various trucking and logistics companies. |
Facility Size | The Yadkinville facility encompasses a substantial square footage to accommodate manufacturing, warehousing, and administrative functions. The exact square footage is a significant factor in operational efficiency. | The size of the facility supports high production volumes. It provides room for expansion and flexibility in operations. | The layout of the facility maximizes space utilization; it incorporates modern building designs and efficient workflow patterns. |
Products Manufactured in Yadkinville
The Yadkinville facility of B&G Foods is a significant production hub, responsible for manufacturing a variety of the company’s well-known food products. These products are distributed across the United States and beyond, contributing significantly to B&G Foods’ overall revenue and market presence. The specific products manufactured in Yadkinville are tailored to meet consumer demand while adhering to stringent quality and safety standards.
Specific B&G Foods Products
The Yadkinville plant focuses on producing a selection of shelf-stable food items. These products are chosen for their market demand and production efficiency within the facility’s capabilities.
- Green Giant® canned vegetables (e.g., green beans, corn, peas).
- B&M® baked beans.
- Underwood® meat spreads.
- Canned beans, such as S&W® brand beans.
Ingredients and Sourcing
The ingredients used in the Yadkinville facility are carefully selected and sourced to ensure product quality and consistency. B&G Foods emphasizes the importance of reliable suppliers and sustainable sourcing practices.The sourcing of key ingredients involves a multifaceted approach:
- Vegetables: Green beans and other vegetables, for example, are often sourced from regional farms to ensure freshness and support local agriculture. The specifications for the vegetables, including size, color, and maturity, are strictly controlled to meet quality standards.
- Beans: The beans used in B&M® baked beans and other bean products are procured from various bean-growing regions, with a focus on quality and variety. The sourcing strategy includes establishing long-term relationships with suppliers to guarantee a consistent supply.
- Meat Products: For products like Underwood® meat spreads, the meat components are sourced from reputable suppliers who adhere to strict animal welfare and food safety standards. The selection of meat is based on the specific requirements of each product formulation.
- Spices and Flavorings: Spices, flavorings, and other ingredients are sourced from around the world, with a focus on quality and adherence to food safety regulations. The company carefully evaluates suppliers to ensure they meet the required standards.
Production Process: Green Bean Canning
The production of canned green beans in the Yadkinville facility follows a well-defined process designed to maintain product quality, safety, and consistency. This process involves several key steps:
- Receiving and Inspection: Fresh green beans arrive at the facility, where they undergo an initial inspection to assess quality. Any beans that do not meet the specifications are rejected.
- Washing and Trimming: The green beans are thoroughly washed to remove dirt and debris. They are then trimmed to remove the stems and any undesirable parts.
- Blanching: The trimmed beans are blanched, which involves briefly heating them in hot water or steam. This process helps to inactivate enzymes that could cause spoilage and preserves the beans’ color and texture.
- Filling and Brining: The blanched beans are filled into cans, and a brine solution (typically water, salt, and sometimes other seasonings) is added. The fill weight and brine concentration are carefully controlled to ensure consistency.
- Exhausting: The cans are then exhausted, which involves heating them to remove air. This step helps to create a vacuum inside the can, which aids in preservation.
- Sealing: The cans are sealed tightly to prevent the entry of air and microorganisms. The sealing process is critical for maintaining product safety and shelf life.
- Sterilization: The sealed cans are sterilized in a retort, which is a large pressure cooker. This process involves heating the cans to a high temperature for a specific period to kill any remaining bacteria and ensure the product is shelf-stable. The temperature and time are precisely controlled based on the product and can size.
- Cooling and Labeling: After sterilization, the cans are cooled, dried, and labeled with the product information. The labels include details such as the product name, ingredients, nutritional information, and expiration date.
- Inspection and Storage: The finished cans are inspected for any defects, such as dents or leaks. They are then stored in a warehouse until they are ready to be shipped to distributors and retailers.
The entire production process for canned green beans is meticulously controlled to ensure the final product meets B&G Foods’ high standards for quality, safety, and taste.
Operations and Logistics: B&g Foods Yadkinville
B&G Foods’ Yadkinville facility is a critical hub for the production and distribution of a variety of food products. Efficient operations and robust logistics are essential to ensuring that these products reach consumers in a timely and cost-effective manner. This section will delve into the specifics of the distribution network, the processes for receiving raw materials and shipping finished goods, and the comprehensive quality control measures employed at the facility.
Distribution Network
The distribution network employed by B&G Foods for products manufactured in Yadkinville leverages a multi-faceted approach to reach its diverse customer base. This approach combines various transportation methods to optimize efficiency and ensure product freshness.B&G Foods utilizes a combination of methods to transport its products:* Direct Shipment: This method involves shipping products directly from the Yadkinville facility to large retailers, distribution centers, and other significant customers.
This is often the preferred method for high-volume orders and helps minimize handling and transit times.
Third-Party Logistics (3PL) Providers
B&G Foods partners with 3PL providers to manage certain aspects of its distribution network. These providers offer expertise in warehousing, transportation, and order fulfillment, enabling B&G Foods to expand its reach and handle fluctuating demand efficiently.
Regional Distribution Centers
The company utilizes regional distribution centers strategically located across the United States. These centers serve as consolidation points for products from various manufacturing facilities, including Yadkinville, before they are distributed to retailers within the respective regions.
Transportation Modes
The primary modes of transportation include:
Trucking
The most common method, trucks are used for both short-haul and long-haul deliveries. Refrigerated trucks are essential for maintaining the quality and safety of perishable products.
Rail
Rail transport is employed for long-distance shipments, especially for bulkier items, offering cost advantages and environmental benefits.
Intermodal Transportation
Combining trucking and rail transport allows for efficient and cost-effective movement of goods across long distances.
Logistics of Raw Materials and Finished Goods
The logistics processes for both incoming raw materials and outgoing finished goods are meticulously managed to ensure efficiency, minimize waste, and maintain product quality. These processes are integral to the smooth operation of the Yadkinville facility.The logistics of receiving raw materials involves several key steps:* Supplier Management: B&G Foods establishes strong relationships with its suppliers to ensure a reliable supply of high-quality raw materials.
This includes ongoing communication, regular audits, and adherence to stringent quality standards.
Order Placement and Scheduling
The procurement team forecasts demand and places orders for raw materials based on production schedules. Orders are carefully scheduled to ensure timely delivery and avoid storage bottlenecks.
Receiving and Inspection
Upon arrival at the Yadkinville facility, all raw materials undergo thorough inspection. This includes verifying the quantity and condition of the materials, as well as conducting quality tests to ensure they meet the required specifications.
Storage and Inventory Management
Raw materials are stored in designated areas under appropriate conditions to maintain their quality and prevent spoilage. Inventory management systems track the movement of materials, ensuring proper rotation and minimizing waste.The logistics of shipping finished goods includes these essential steps:* Order Processing: Once an order is received, it is processed through the facility’s order management system. This involves verifying the order details, allocating the necessary products, and generating shipping documentation.
Production and Packaging
The finished goods are produced according to the order specifications and packaged appropriately to protect them during transit. Packaging materials are chosen to ensure product integrity and minimize environmental impact.
Warehousing and Storage
Finished goods are stored in a designated warehouse area, ready for shipment. The storage environment is carefully controlled to maintain product quality.
Loading and Transportation
Finished goods are loaded onto trucks or other transportation modes, and the shipping documents are prepared. The products are then transported to their final destination, whether it is a distribution center, a retailer, or directly to a customer.
Tracking and Monitoring
B&G Foods utilizes tracking systems to monitor the location and status of shipments throughout the distribution network. This allows for real-time visibility and the ability to address any potential issues promptly.
Quality Control Procedure
Quality control is a paramount concern at the Yadkinville facility, and a comprehensive set of procedures is in place to ensure that all products meet the highest standards of safety and quality. These procedures are integrated into every stage of the manufacturing process, from the receipt of raw materials to the shipment of finished goods.The quality control procedure at the Yadkinville facility includes these steps:* Raw Material Inspection:
Upon arrival, all raw materials undergo rigorous inspection to ensure they meet established quality standards.
This inspection includes visual examination, testing for contaminants, and verifying compliance with specifications.
Materials that do not meet the required standards are rejected.
In-Process Quality Checks
Quality checks are performed at various stages of the production process to monitor and control product quality.
These checks include monitoring critical control points (CCPs) such as temperature, pressure, and time.
Samples are taken at regular intervals for testing and analysis.
Finished Product Testing
Finished products are subjected to comprehensive testing to ensure they meet all quality requirements.
This testing includes sensory evaluations (taste, smell, appearance), physical testing (weight, dimensions), and microbiological analysis.
Products that fail to meet the standards are either reworked or rejected.
Packaging and Labeling Verification
Packaging and labeling are carefully inspected to ensure they meet regulatory requirements and accurately reflect the product.
This includes verifying the accuracy of ingredients, nutritional information, and allergen warnings.
Defective packaging or labeling is corrected before the product is shipped.
Documentation and Record Keeping
Detailed records are maintained throughout the quality control process, including inspection reports, test results, and corrective actions.
This documentation provides a comprehensive audit trail and allows for continuous improvement.
Employee Training
All employees involved in the production process receive thorough training on quality control procedures.
This training ensures that all employees understand their roles and responsibilities in maintaining product quality.
Regular Audits
Internal and external audits are conducted regularly to assess the effectiveness of the quality control system.
These audits identify areas for improvement and ensure compliance with relevant regulations and standards.
Corrective Action and Preventive Action (CAPA)
A formal CAPA system is in place to address any quality issues that arise.
This system involves investigating the root cause of the issue, implementing corrective actions, and taking preventive measures to prevent recurrence.
Impact on the Yadkinville Community
B&G Foods’ presence in Yadkinville extends beyond its manufacturing operations, significantly influencing the local community. The company’s activities have a multifaceted impact, encompassing employment, economic contributions, and community engagement. This section details the specific ways B&G Foods affects Yadkinville and its residents.
Number of Employees at the Yadkinville Facility, B&g foods yadkinville
The Yadkinville facility is a substantial employer within the local area.The facility provides a significant number of jobs to the Yadkinville community, contributing to the local economy through wages and benefits. Precise figures fluctuate, but the facility typically employs a considerable workforce. This employment base contributes to the economic stability of many families in the region.
Economic Impact of B&G Foods on the Yadkinville Community
B&G Foods’ operations in Yadkinville generate considerable economic activity, impacting various sectors of the local economy.The economic impact extends beyond direct employment. The facility’s presence supports local businesses, generates tax revenue, and stimulates overall economic growth.
- Local Suppliers: B&G Foods likely sources supplies and services from local vendors, creating business opportunities within the community. This can range from raw material suppliers to service providers.
- Tax Revenue: The company’s operations contribute to local and state tax revenues, which fund essential public services such as schools, infrastructure, and public safety.
- Indirect Employment: The economic activity generated by B&G Foods supports indirect employment in related industries, such as transportation, warehousing, and retail.
This economic ripple effect underscores the importance of B&G Foods to Yadkinville’s economic well-being.
Company’s Community Involvement or Corporate Social Responsibility Initiatives in Yadkinville
B&G Foods demonstrates its commitment to the Yadkinville community through various corporate social responsibility initiatives. These activities reflect the company’s values and contribute to the well-being of the local area.B&G Foods likely participates in community outreach programs and supports local organizations.
- Donations and Sponsorships: The company may provide financial support to local schools, charities, and community events. For example, they could sponsor a local festival or donate to a food bank.
- Employee Volunteerism: B&G Foods may encourage employee volunteerism, allowing employees to contribute their time and skills to local causes. This fosters a sense of community and social responsibility.
- Environmental Initiatives: The company may implement environmentally friendly practices at its facility and participate in local environmental projects. This could involve waste reduction programs or supporting local conservation efforts.
Challenges and Opportunities
The Yadkinville facility, like any large-scale manufacturing operation, faces a dynamic landscape of challenges and opportunities. Navigating these requires proactive strategies and a forward-thinking approach to ensure continued success and growth. Understanding these factors is critical for B&G Foods to maintain its competitive edge in the food industry.
Potential Challenges
The Yadkinville facility encounters several potential challenges that require careful management. These challenges can impact operational efficiency, profitability, and the overall sustainability of the facility.
- Supply Chain Disruptions: Fluctuations in the availability and cost of raw materials pose a significant risk. External factors, such as weather events impacting crop yields or geopolitical instability affecting transportation, can disrupt the supply chain. For example, a major hurricane in a key agricultural region could lead to shortages of essential ingredients, impacting production schedules and increasing costs.
- Labor Market Dynamics: Attracting and retaining a skilled workforce is crucial. Competition for labor in the Yadkinville area, particularly for specialized roles, could lead to increased labor costs or difficulties in maintaining adequate staffing levels. Furthermore, changing demographics and evolving employee expectations require ongoing adjustments to compensation, benefits, and workplace culture.
- Rising Operational Costs: Increasing energy prices, transportation expenses, and maintenance costs can erode profit margins. Implementing energy-efficient technologies, optimizing logistics, and proactively maintaining equipment are essential to mitigate these rising costs.
- Regulatory Compliance: Adhering to food safety regulations, environmental standards, and other governmental requirements adds complexity and expense. Staying abreast of evolving regulations and investing in compliance measures are vital to avoid penalties and maintain consumer trust.
- Competitive Pressures: Competition from other food manufacturers and evolving consumer preferences require continuous innovation and operational efficiency. B&G Foods must differentiate its products and streamline its processes to maintain market share and profitability.
Opportunities for Growth and Expansion
The Yadkinville facility has several opportunities for growth and expansion that can enhance its operational capabilities and market position. These opportunities involve strategic investments and innovative approaches.
- Product Diversification: Expanding the range of products manufactured at the Yadkinville facility can tap into new market segments and cater to evolving consumer preferences. This could involve introducing new flavors, packaging options, or product lines aligned with current health and wellness trends.
- Process Optimization: Implementing advanced manufacturing technologies and streamlining existing processes can improve efficiency and reduce production costs. Investing in automation, data analytics, and predictive maintenance can optimize operations and enhance overall productivity.
- Capacity Expansion: Increasing the facility’s production capacity can enable B&G Foods to meet growing demand and capture additional market share. This could involve expanding existing infrastructure, adding new production lines, or optimizing the layout of the facility.
- Sustainable Practices: Adopting sustainable manufacturing practices can reduce environmental impact and appeal to environmentally conscious consumers. This includes initiatives such as reducing waste, conserving water, and utilizing renewable energy sources. This also helps the facility to improve its image.
- Strategic Partnerships: Collaborating with other food manufacturers, suppliers, or technology providers can create synergies and open up new growth opportunities. These partnerships can facilitate access to new technologies, markets, and resources.
Adapting to Changing Consumer Preferences and Market Trends: A Scenario
B&G Foods can adapt to evolving consumer preferences and market trends by implementing a flexible and innovative strategy. The following scenario illustrates how the Yadkinville facility might respond to a shift towards plant-based protein products.
Do not overlook explore the latest data about chinese food wareham.
Scenario: Consumer demand for plant-based protein options is increasing significantly. B&G Foods identifies an opportunity to expand its product line by manufacturing a new line of plant-based meat alternatives.
Adaptation Strategy:
- Market Research and Analysis: Conduct thorough market research to identify specific consumer preferences, target demographics, and competitive offerings in the plant-based protein market.
- Product Development: Invest in research and development to formulate plant-based meat alternatives that meet consumer expectations for taste, texture, and nutritional value. This could involve partnering with food scientists or utilizing existing expertise within B&G Foods.
- Facility Modification: Adapt the Yadkinville facility to accommodate the production of plant-based protein products. This might involve acquiring new equipment, such as extruders or specialized packaging machinery, and modifying existing production lines.
- Supply Chain Management: Establish a reliable supply chain for plant-based ingredients, such as pea protein, soy protein, or other plant-based sources. This may involve identifying new suppliers and negotiating favorable pricing and terms.
- Marketing and Distribution: Develop a comprehensive marketing and distribution strategy to reach target consumers. This could include online marketing campaigns, partnerships with retailers, and sampling programs.
- Continuous Improvement: Continuously monitor consumer feedback, market trends, and production efficiency to refine the product and optimize the manufacturing process.
Example: Beyond Meat’s rapid growth in the plant-based meat market provides a relevant case study. B&G Foods could leverage similar strategies, adapting the Yadkinville facility to produce and market plant-based protein products, capitalizing on the growing consumer demand and diversifying its product portfolio.
Sustainability and Environmental Practices
B&G Foods is committed to sustainable operations and minimizing its environmental footprint. The Yadkinville facility actively implements various initiatives to conserve resources, reduce waste, and improve energy efficiency. These practices reflect B&G Foods’ dedication to environmental stewardship and responsible manufacturing.
Sustainability Initiatives at Yadkinville
The Yadkinville facility has implemented a range of sustainability initiatives aimed at reducing environmental impact and promoting responsible resource management. These initiatives are integrated into various aspects of the facility’s operations, from sourcing raw materials to waste disposal.
Waste Management Practices
Effective waste management is a crucial component of B&G Foods’ sustainability strategy. The Yadkinville facility employs comprehensive waste management practices to minimize waste generation, promote recycling, and reduce landfill contributions.* Recycling Programs: The facility has established robust recycling programs for various materials, including paper, cardboard, plastics, and metals. These programs divert significant amounts of waste from landfills.
Composting
Organic waste, such as food scraps and packaging materials, is composted whenever feasible. This reduces landfill waste and generates nutrient-rich compost that can be used in landscaping or agricultural applications.
Waste Reduction Strategies
B&G Foods focuses on waste reduction through process optimization and packaging improvements. This includes efforts to minimize packaging materials, utilize reusable containers, and streamline production processes to reduce scrap.
Partnerships with Waste Management Providers
B&G Foods collaborates with waste management providers to ensure proper handling and disposal of all waste streams, adhering to local regulations and best practices.
Energy Efficiency Measures
B&G Foods is committed to improving energy efficiency at the Yadkinville facility. The following table details the energy efficiency measures implemented, their descriptions, benefits, and measurement metrics:
Initiative | Description | Benefits | Measurement |
---|---|---|---|
LED Lighting Upgrades | Installation of energy-efficient LED lighting throughout the facility, replacing traditional fluorescent and incandescent bulbs. | Reduced energy consumption, lower electricity costs, and improved lighting quality. | Kilowatt-hours (kWh) saved per year; percentage reduction in lighting-related energy consumption. |
HVAC System Optimization | Implementation of energy-efficient HVAC (heating, ventilation, and air conditioning) systems, including smart thermostats and regular maintenance. | Improved temperature control, reduced energy consumption for heating and cooling, and extended equipment lifespan. | kWh saved per year; percentage reduction in HVAC-related energy consumption. |
Equipment Efficiency Improvements | Upgrading production equipment with energy-efficient models and implementing energy-saving practices, such as turning off equipment when not in use. | Reduced energy consumption during production processes and lower operational costs. | kWh saved per year; percentage reduction in equipment-related energy consumption. |
Energy Audits and Monitoring | Conducting regular energy audits to identify areas for improvement and monitoring energy consumption patterns. | Provides insights into energy usage, identifies areas for optimization, and supports informed decision-making. | Annual energy consumption data; identification of energy-saving opportunities. |
Future Outlook for Yadkinville Operations
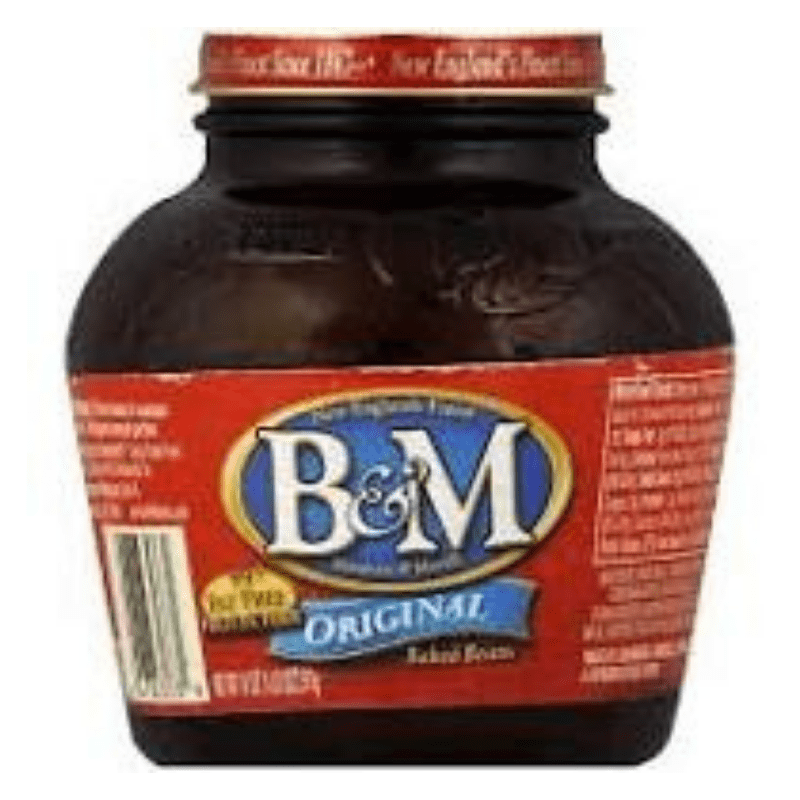
B&G Foods’ Yadkinville facility holds a significant position within the company’s manufacturing network. Analyzing the current trends in the food industry, alongside B&G Foods’ strategic initiatives, provides a basis for predicting the future trajectory of this facility. This outlook considers factors such as market demand, operational efficiency, and the integration of advanced technologies.
Potential for Expansion or Modernization
The Yadkinville facility’s future hinges on its capacity to adapt to evolving market demands and optimize its operational capabilities. Several factors suggest potential for expansion or modernization.The following are key considerations:
- Increased Production Capacity: B&G Foods might consider expanding the Yadkinville facility to accommodate increased production volumes. This could be driven by rising consumer demand for existing product lines manufactured at the location or the potential introduction of new products. An example is the expansion of a processing line for a popular canned vegetable product, which has seen a 15% increase in demand year-over-year.
This expansion would necessitate additional square footage for manufacturing, warehousing, and potentially, raw material storage.
- Facility Modernization: Modernizing existing infrastructure is another likely scenario. This involves upgrading equipment and processes to improve efficiency, reduce waste, and enhance product quality. This could include the installation of automated packaging lines, advanced quality control systems, and updated food processing technologies. A practical example is the implementation of a new automated sorting system for incoming raw materials, leading to a 10% reduction in material waste and a 5% increase in processing speed.
- Strategic Investments: B&G Foods might make strategic investments in the Yadkinville facility to align with its overall business objectives. This includes investments in sustainable practices, such as implementing energy-efficient equipment or water conservation systems, and/or investing in workforce development programs to enhance employee skills and capabilities. For instance, investing in a new water recycling system could reduce water consumption by 20% and operational costs.
Impact of Technological Advancements
Technological advancements are poised to significantly influence the Yadkinville operations in the coming years. Integrating new technologies will likely enhance various aspects of the facility’s performance.The following areas are expected to see the greatest impact:
- Automation and Robotics: The adoption of automation and robotics will likely increase. This includes automating repetitive tasks, such as packaging and palletizing, and using robotic systems for handling raw materials and finished goods. This can lead to higher production speeds, reduced labor costs, and improved workplace safety. An example is the implementation of robotic arms for packing boxes, which could reduce the number of employees needed on a specific production line by up to 30%.
- Data Analytics and Predictive Maintenance: Implementing data analytics and predictive maintenance systems can optimize equipment performance and reduce downtime. Sensors and data analysis tools can monitor equipment performance in real-time, predict potential failures, and schedule maintenance proactively. This will result in increased efficiency and reduced operational costs. For instance, a predictive maintenance program could reduce unplanned downtime by 15% and extend the lifespan of key machinery.
- Enhanced Supply Chain Management: Technology will play a crucial role in optimizing supply chain management. This includes using advanced software systems to track inventory, manage logistics, and forecast demand more accurately. Real-time data on raw material availability, production schedules, and distribution networks can improve responsiveness and reduce waste. Implementing a new supply chain management system could reduce inventory holding costs by 8% and improve on-time delivery rates.
- Food Safety and Quality Control: Advancements in food safety and quality control technologies are expected to be integrated. This involves the use of sensors, imaging systems, and data analysis to monitor product quality, detect contaminants, and ensure compliance with food safety regulations. For example, implementing a real-time monitoring system for product temperature could reduce the risk of spoilage and improve product shelf life.
Last Word
In conclusion, the B&G Foods Yadkinville facility stands as a testament to the company’s commitment to quality, efficiency, and community engagement. From the manufacturing floor to the distribution network, every aspect of the operation contributes to the success of the brand. The future of the Yadkinville facility appears promising, with opportunities for expansion, modernization, and continued contributions to the local economy and environmental sustainability.
B&G Foods Yadkinville exemplifies how a major food producer can thrive while remaining a valued member of its community.