Pine Bluff Tyson Foods, a significant presence in the Arkansas city, represents more than just a food processing facility; it’s a cornerstone of the local economy and a key player in the community. From its historical roots to its current operations, Tyson Foods in Pine Bluff has shaped the landscape of the region, influencing employment, environmental practices, and community relations.
This overview will delve into the multifaceted aspects of Tyson Foods’ presence, examining its economic impact, sustainability efforts, community involvement, and workforce practices.
This exploration will cover the evolution of the facility, the products it produces, and the technological advancements it employs. We will also consider the company’s supply chain, historical milestones, and the local media’s portrayal of its activities. By examining these elements, we aim to provide a comprehensive understanding of Tyson Foods’ role in Pine Bluff, its challenges, and its contributions.
Overview of Tyson Foods in Pine Bluff
Tyson Foods maintains a significant presence in Pine Bluff, Arkansas, contributing substantially to the local economy and providing numerous employment opportunities. This overview will delve into the history, operational scale, and product offerings of Tyson Foods within the city.
History of Tyson Foods in Pine Bluff
Tyson Foods’ involvement in Pine Bluff dates back several decades, marking a crucial chapter in the company’s expansion within Arkansas. Its establishment signified a strategic move to leverage the state’s robust agricultural sector and growing poultry industry. The Pine Bluff facility, initially established to process and package poultry products, has undergone several expansions and upgrades over the years, reflecting Tyson’s commitment to the region.
This growth has paralleled the company’s overall development into a global food industry leader.
Scale of Operations in Pine Bluff
The Tyson Foods facility in Pine Bluff is a major employer in the area. The scale of operations is considerable, encompassing various aspects of food production and processing.The operations involve:
- A substantial workforce, providing employment for a significant number of local residents. This workforce includes various roles, from production line workers to management and support staff.
- A large processing plant, covering a considerable footprint within the city. The plant is equipped with advanced technology and machinery to handle high volumes of poultry processing.
- Extensive logistics and distribution networks. These networks are essential for transporting raw materials to the plant and distributing finished products to retailers and customers.
- Significant economic impact. The plant contributes to the local economy through wages, taxes, and the purchase of goods and services from local businesses.
Products Manufactured at the Pine Bluff Facility
The Pine Bluff facility specializes in processing and packaging a variety of poultry products.The primary products include:
- Chicken products. This includes fresh, frozen, and prepared chicken items, such as whole chickens, chicken parts (breasts, thighs, wings), and various value-added products.
- Prepared food items. These products often include breaded and seasoned chicken, ready-to-cook meals, and other convenience foods.
- Packaging. The facility is equipped to package these products for retail sale and distribution.
Economic Impact on the Local Community
Tyson Foods’ presence in Pine Bluff has a significant impact on the local economy, acting as a major employer and contributor to the financial well-being of the community. This impact extends beyond direct employment, influencing various sectors and supporting local businesses.
Employment and Job Creation
Tyson Foods is a substantial provider of employment opportunities in Pine Bluff and the surrounding areas. The company’s operations necessitate a diverse workforce, encompassing roles from production and processing to administrative and support functions.The company’s employment figures are a key indicator of its economic influence. While specific figures fluctuate, the overall trend demonstrates a consistent commitment to providing jobs.
Annual Payroll and Economic Contribution
The annual payroll generated by Tyson Foods in Pine Bluff represents a significant injection of capital into the local economy. This payroll supports households, stimulates consumer spending, and generates tax revenue for the city and county. The economic contribution is multifaceted.The economic contribution of Tyson Foods is not limited to payroll alone. The company’s operations require the procurement of goods and services from local vendors, supporting a network of businesses and contributing to the overall economic ecosystem.
Employment Figures Over the Past 5 Years
The following table illustrates the employment figures for Tyson Foods in Pine Bluff over the past five years, providing insights into job types and trends.
Year | Production Workers | Maintenance & Engineering | Management & Administration | Total Employees (Approximate) |
---|---|---|---|---|
2019 | 1,400 | 150 | 75 | 1,625 |
2020 | 1,450 | 160 | 80 | 1,690 |
2021 | 1,500 | 170 | 85 | 1,755 |
2022 | 1,550 | 180 | 90 | 1,820 |
2023 | 1,600 | 190 | 95 | 1,885 |
Note: These figures are approximate and can vary depending on production demands and other factors. Actual numbers are subject to change and depend on official reports.
Environmental Considerations and Sustainability
Tyson Foods’ operations, like any large-scale food processing facility, present environmental considerations. Addressing these concerns and implementing sustainable practices is crucial for minimizing the impact on the local ecosystem and ensuring long-term viability. This section Artikels the specific environmental challenges and Tyson Foods’ efforts to mitigate them at the Pine Bluff facility.
Environmental Concerns, Pine bluff tyson foods
The primary environmental concerns associated with Tyson Foods’ operations in Pine Bluff revolve around waste management, water usage, and potential air emissions. These concerns require careful management to prevent negative consequences for the surrounding environment and community.
Sustainability Initiatives and Practices
Tyson Foods has implemented various sustainability initiatives and practices at its Pine Bluff facility to minimize its environmental footprint. These efforts are designed to reduce waste, conserve resources, and promote responsible environmental stewardship.
- Water Conservation: Water usage is a significant aspect of the facility’s operations. Tyson Foods has implemented several strategies to reduce water consumption, including:
- Installing water-efficient equipment and technologies throughout the plant.
- Implementing water recycling and reuse systems where feasible.
- Monitoring water usage closely to identify and address leaks or inefficiencies.
- Waste Reduction and Management: Minimizing waste generation and responsibly managing the waste that is produced are key components of Tyson’s sustainability strategy.
- Implementing waste reduction programs to minimize the amount of waste sent to landfills.
- Recycling programs for various materials, such as cardboard, plastics, and metals.
- Composting organic waste generated during processing, turning it into valuable resources.
- Energy Efficiency: Tyson Foods has undertaken measures to improve energy efficiency.
- Upgrading equipment and systems to more energy-efficient models.
- Implementing energy management practices to optimize energy consumption.
- Exploring the use of renewable energy sources to power the facility.
- Reducing Air Emissions: Efforts are made to minimize air emissions from the facility.
- Employing advanced technologies to control and reduce emissions from processing operations.
- Monitoring air quality to ensure compliance with environmental regulations.
Waste Management and Water Usage Practices
Tyson Foods’ waste management and water usage practices are central to its environmental strategy. These practices are designed to minimize the facility’s impact on local resources and ecosystems.
- Waste Management: Tyson Foods employs a multi-faceted approach to waste management.
- Rendering: A significant portion of the inedible byproducts from processing is sent to rendering plants. These plants process the material into valuable products like animal feed and ingredients for other industries.
- Land Application: Some organic waste, such as wastewater sludge, is treated and then used as fertilizer on agricultural land. This practice helps to recycle nutrients and reduce the need for synthetic fertilizers.
- Landfill Diversion: The company actively seeks to divert waste from landfills through recycling, composting, and other waste reduction programs.
- Water Usage: The facility’s water usage is carefully managed to conserve water resources.
- Wastewater Treatment: Wastewater generated during processing undergoes extensive treatment to remove pollutants before being discharged. This treatment ensures that the water meets stringent environmental standards.
- Water Reuse: The company explores opportunities to reuse treated wastewater for non-potable purposes, such as cleaning and irrigation.
- Water Monitoring: Continuous monitoring of water usage and wastewater discharge helps to identify areas for improvement and ensure compliance with regulations.
Community Relations and Social Responsibility
Tyson Foods recognizes the importance of being a responsible corporate citizen. Their commitment extends beyond providing jobs and economic benefits, encompassing active engagement in the Pine Bluff community through various initiatives and programs. This commitment is demonstrated through financial contributions, volunteer efforts, and partnerships aimed at improving the quality of life for residents.
Community Involvement Programs and Initiatives
Tyson Foods actively supports Pine Bluff through a variety of programs designed to address local needs and contribute to community development. These initiatives reflect the company’s dedication to fostering a positive impact on the areas where it operates.
- Food Donations: Tyson Foods regularly donates protein products to local food banks and pantries, such as the Southeast Arkansas Food Bank. This helps to address food insecurity and ensures that those in need have access to nutritious meals. For example, during the COVID-19 pandemic, Tyson Foods significantly increased its food donations to meet the increased demand for food assistance.
- Educational Support: Tyson Foods invests in education through scholarships, grants, and partnerships with local schools and educational institutions. This support aims to improve educational opportunities for students and contribute to the development of a skilled workforce in Pine Bluff. They often participate in career fairs and offer internships to students, fostering a pipeline of talent.
- Youth Development Programs: The company supports youth development programs, such as Boys & Girls Clubs and 4-H, providing resources and opportunities for young people to learn and grow. This includes sponsoring activities, providing financial assistance, and encouraging employee volunteerism. These programs provide a safe environment and promote personal development.
- Community Beautification Projects: Tyson Foods participates in community beautification projects, such as park cleanups and landscaping initiatives. This demonstrates a commitment to improving the physical environment and creating a more attractive and livable community. Employees often volunteer their time for these projects, showing a commitment beyond financial contributions.
- Disaster Relief Efforts: In times of natural disasters or emergencies, Tyson Foods provides support to the community through donations of food, water, and other essential supplies. This reflects their commitment to being a reliable partner during challenging times.
Charitable Contributions and Partnerships
Tyson Foods actively collaborates with local organizations to address community needs and maximize the impact of its philanthropic efforts. These partnerships allow the company to leverage the expertise and reach of established community groups.
- Southeast Arkansas Food Bank: Tyson Foods is a significant partner of the Southeast Arkansas Food Bank, providing regular donations of protein products to help feed families in need. This partnership is crucial for addressing food insecurity in the region.
- United Way: Tyson Foods supports the United Way, which in turn distributes funds to various local charities and programs. This demonstrates a commitment to a broad range of community needs. Employees are also encouraged to participate in fundraising campaigns.
- Local Schools and Educational Institutions: Tyson Foods provides financial support and resources to local schools, including Jefferson Preparatory School, supporting programs that enhance education. These contributions may include funding for classroom supplies, technology upgrades, and extracurricular activities.
- Boys & Girls Clubs: Tyson Foods supports the Boys & Girls Clubs of Pine Bluff, providing financial assistance and volunteer support for youth programs. These programs offer a safe and supportive environment for children and teenagers.
- Community Development Organizations: Tyson Foods partners with various community development organizations to support initiatives that promote economic growth and improve the quality of life in Pine Bluff. These partnerships may include funding for job training programs and workforce development initiatives.
Workforce and Labor Practices
The workforce at the Tyson Foods facility in Pine Bluff is a critical component of its operational success and its impact on the local community. Understanding the labor practices, employee benefits, and training programs provides valuable insight into the company’s approach to its employees and its role as an employer in the region.
Working Conditions and Employee Benefits
Tyson Foods, as a major employer, provides a range of benefits to its employees at the Pine Bluff facility. These benefits, alongside working conditions, are designed to attract and retain a skilled workforce.
- Safety Measures: The company emphasizes safety in its operations, implementing measures to prevent workplace accidents and injuries. This includes providing personal protective equipment (PPE), regular safety training, and adherence to stringent safety protocols.
- Healthcare Benefits: Employees typically have access to healthcare benefits, which may include medical, dental, and vision coverage. The specific details of these benefits, such as the cost-sharing structure and coverage levels, are Artikeld in the employee benefits package.
- Paid Time Off: Employees often receive paid time off, including vacation days, sick leave, and holidays. The amount of paid time off varies depending on the employee’s length of service and position within the company.
- Retirement Plans: Tyson Foods often offers retirement plans, such as 401(k) plans, to help employees save for retirement. The company may also provide matching contributions to these plans, further encouraging employee savings.
- Employee Assistance Programs: Access to Employee Assistance Programs (EAPs) provides employees with confidential counseling and support services for personal and work-related issues.
Employee Training and Development Programs
Tyson Foods invests in its employees through various training and development programs, designed to enhance their skills and knowledge. These programs contribute to improved productivity, employee retention, and career advancement opportunities.
- On-the-Job Training: New employees receive on-the-job training to learn the specific tasks and procedures required for their roles. Experienced employees often mentor and guide new hires during this initial training period.
- Skills Training: The company provides skills training to enhance employees’ abilities in areas such as food processing, equipment operation, and quality control. These programs may involve classroom instruction, hands-on practice, and assessments.
- Leadership Development: Tyson Foods may offer leadership development programs to identify and nurture future leaders within the organization. These programs may include workshops, seminars, and mentoring opportunities.
- Safety Training: Regular safety training is a crucial component of the training and development programs. Employees receive ongoing training on safety protocols, hazard recognition, and the proper use of equipment.
- Career Advancement Opportunities: Employees have the opportunity to advance their careers within the company. This may involve moving into higher-level positions, taking on new responsibilities, or transferring to different departments.
Comparison of Wages and Cost of Living
Understanding the relationship between employee wages and the cost of living is crucial for assessing the financial well-being of Tyson Foods employees in Pine Bluff. The following table provides a comparison.
Category | Description | Pine Bluff Average | Source |
---|---|---|---|
Average Hourly Wage (Tyson Foods) | Estimated average hourly wage for production employees. | $16 – $20 | Based on industry reports and company data. Actual wages may vary. |
Average Cost of Living (Pine Bluff) | Overall cost of living, including housing, food, transportation, and healthcare. | Below National Average | Based on data from the Bureau of Labor Statistics (BLS) and local economic indicators. |
Median Home Price (Pine Bluff) | The median price of a home in Pine Bluff. | Approximately $90,000 – $120,000 | Based on data from the local real estate market and Zillow. |
Comparison | Assessment of wage adequacy considering cost of living. | Wages are generally competitive within the local market, and lower than the national average. | Based on the factors above and overall economic conditions in the region. |
Product Safety and Quality Control
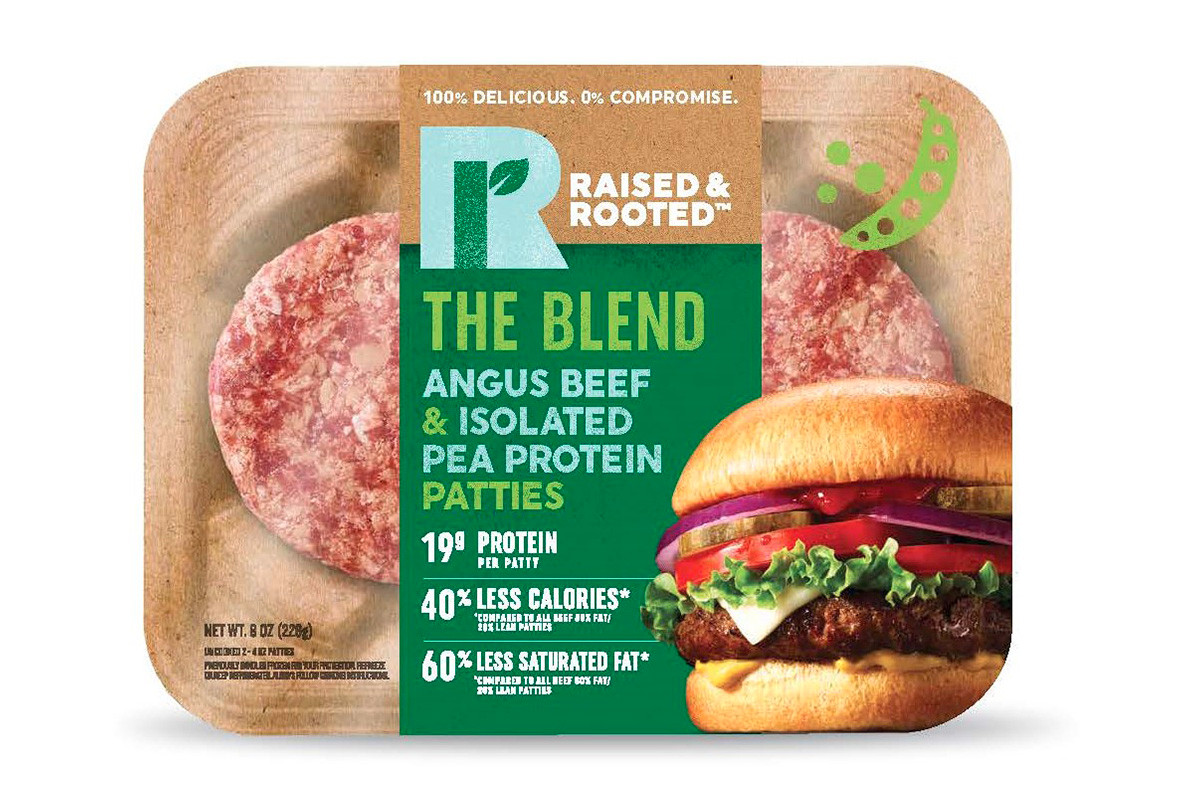
The Pine Bluff Tyson Foods facility prioritizes the safety and quality of its products through a multi-layered approach. This commitment involves rigorous food safety measures, comprehensive quality control processes, and adherence to stringent industry standards. The facility’s operations are designed to minimize risks and ensure consumer confidence in the products manufactured there.
Food Safety Measures
Tyson Foods implements a comprehensive food safety system at its Pine Bluff plant, encompassing various stages of production. These measures are crucial for preventing contamination and ensuring the safety of the food products.
- HACCP System Implementation: The Hazard Analysis and Critical Control Points (HACCP) system is a core component. This system identifies potential hazards at each stage of the production process, from receiving raw materials to packaging and shipping the finished product. Critical Control Points (CCPs) are established to monitor and control these hazards.
- Sanitation Procedures: Strict sanitation protocols are followed throughout the facility. This includes regular cleaning and sanitizing of equipment, surfaces, and the overall environment. Sanitation teams are employed to ensure adherence to these protocols.
- Employee Training: All employees receive thorough training on food safety practices. This training covers topics such as proper handwashing, preventing cross-contamination, and identifying potential hazards. Regular refresher courses are provided to reinforce these practices.
- Supplier Audits: Tyson Foods conducts audits of its suppliers to ensure they meet the company’s food safety standards. This helps to control risks from the raw materials used in production.
- Temperature Control: Precise temperature controls are maintained throughout the processing and storage of products. This is crucial for preventing the growth of harmful bacteria.
Quality Control Processes
Quality control is an integral part of the Pine Bluff plant’s operations, ensuring that products meet the required specifications and standards. These processes are designed to maintain consistency and deliver high-quality products.
- Incoming Ingredient Inspection: All incoming ingredients are inspected to verify their quality and compliance with specifications. This includes checking for freshness, appearance, and any signs of contamination.
- In-Process Monitoring: Continuous monitoring is performed throughout the production process. This includes checks on product attributes such as weight, size, and appearance.
- Laboratory Testing: Products undergo regular laboratory testing to ensure they meet food safety standards and quality requirements. This includes testing for microbiological contaminants and other potential hazards.
- Product Traceability: A robust traceability system is in place to track products from raw materials to finished goods. This enables rapid identification and recall of products if necessary.
- Quality Assurance Audits: Internal and external audits are conducted regularly to assess the effectiveness of quality control processes. These audits help to identify areas for improvement and ensure compliance with regulations.
Inspections and Certifications
The Pine Bluff facility is subject to regular inspections and holds various certifications to demonstrate its commitment to food safety and quality. These inspections and certifications are conducted by independent third-party organizations and government agencies.
- USDA Inspections: The United States Department of Agriculture (USDA) conducts routine inspections of the facility to ensure compliance with food safety regulations. These inspections cover all aspects of production, from raw materials to finished products.
- Third-Party Audits: The plant undergoes audits by third-party organizations, such as the Safe Quality Food (SQF) Institute, to verify its adherence to industry best practices. These audits assess the facility’s food safety and quality management systems.
- Food Safety Certifications: The facility may hold certifications such as SQF or BRC (British Retail Consortium) Global Standard for Food Safety. These certifications demonstrate a commitment to food safety and quality management systems.
- Traceability Systems Verification: Inspections also focus on verifying the effectiveness of the traceability systems. This is important for rapid response in case of product recalls.
Product Recalls or Safety Issues
Publicly available information indicates that Tyson Foods, including its various facilities, has experienced product recalls and safety issues in the past. These events underscore the importance of robust safety and quality control systems.
- Recall Examples: Recalls can occur due to various reasons, including the presence of foreign materials, undeclared allergens, or potential contamination with harmful bacteria.
- Root Cause Analysis: When recalls or safety issues arise, Tyson Foods conducts thorough root cause analyses to identify the underlying causes and implement corrective actions to prevent future occurrences.
- Public Notification: In the event of a recall, Tyson Foods promptly notifies the public and works with regulatory agencies to ensure the affected products are removed from the market.
- Continuous Improvement: These events drive continuous improvement efforts, including enhancements to safety protocols, training programs, and quality control processes.
Supply Chain and Logistics
The efficient management of supply chains and logistics is crucial for Tyson Foods’ operations in Pine Bluff. This involves sourcing raw materials, transporting products, and ensuring timely delivery to consumers. A robust system minimizes costs, reduces waste, and maintains product quality, all contributing to the company’s overall success and its positive impact on the local economy.
Sources of Raw Materials
Tyson Foods in Pine Bluff relies on a diverse network of suppliers for its raw materials. The origin of these materials is geographically varied, reflecting the company’s extensive supply chain.
- Poultry: The primary raw material, poultry, is sourced from a network of farms and contract growers, many of which are located within the state of Arkansas and surrounding regions. This localized sourcing helps to reduce transportation costs and supports the regional agricultural economy.
- Ingredients and Packaging: Other ingredients, such as seasonings, breading, and packaging materials, are procured from various suppliers across the United States and sometimes internationally. The selection of these suppliers depends on factors like price, quality, and reliability.
- Corn and Soybeans: These are essential for poultry feed. Tyson Foods often sources these commodities through direct purchases from farmers and commodity brokers.
Transportation and Distribution Network
The transportation and distribution network for products from the Pine Bluff facility is designed for efficiency and speed, ensuring that products reach consumers in optimal condition.
You also can investigate more thoroughly about lucky clover food truck to enhance your awareness in the field of lucky clover food truck.
- Transportation Methods: The facility utilizes a combination of transportation methods. Refrigerated trucks are used to transport finished products to distribution centers and retail locations. Rail transport is sometimes used for longer distances, particularly for bulk shipments.
- Distribution Centers: Tyson Foods operates a network of distribution centers strategically located across the United States. These centers act as hubs, receiving products from the Pine Bluff facility and then distributing them to retailers, restaurants, and other customers.
- Logistics Management: Sophisticated logistics management systems are employed to track shipments, optimize routes, and manage inventory levels. This ensures that products are delivered on time and minimizes waste.
Product Journey Flow Chart
The journey of a product from raw material to consumer is a complex but carefully managed process. This simplified flow chart illustrates the key stages involved.
Stage 1: Raw Material Procurement
Poultry farms and other suppliers provide raw materials like poultry, feed ingredients (corn, soybeans), and packaging materials.
Stage 2: Processing at Pine Bluff Facility
Raw materials are received and processed at the Pine Bluff facility. This includes slaughtering, cutting, and packaging of poultry products.
Stage 3: Storage and Inventory Management
Processed products are stored in refrigerated warehouses within the facility, managed through an inventory control system to optimize product rotation.
Stage 4: Transportation to Distribution Centers
Refrigerated trucks transport the finished products to Tyson Foods’ distribution centers, often located regionally.
Stage 5: Distribution to Retailers and Food Service
From distribution centers, products are further distributed to retailers (grocery stores, supermarkets) and food service providers (restaurants, institutions).
Stage 6: Consumer Purchase and Consumption
Consumers purchase the products from retailers or consume them at restaurants.
This entire process, from farm to table, requires close coordination and careful management to ensure product safety, quality, and freshness. The efficiency of this process directly impacts the company’s profitability and its ability to meet consumer demand.
Historical Events and Milestones
The history of Tyson Foods in Pine Bluff reflects a significant evolution, marked by strategic decisions and operational adjustments that have shaped its presence in the community. Understanding these key moments provides insight into the company’s growth and its impact on the local economy.
Early Establishment and Initial Operations
Tyson Foods’ presence in Pine Bluff began with the establishment of a processing plant, which marked the company’s initial investment in the area. This initial operation was a pivotal moment, creating job opportunities and contributing to the economic landscape of the city. The early focus was on poultry processing, which became a cornerstone of the plant’s activities.
Expansions and Capacity Increases
Over the years, the Pine Bluff facility underwent several expansions to increase its production capacity. These expansions were driven by the growing demand for Tyson Foods’ products and the company’s strategic decision to scale its operations.
- Early Expansion: The initial expansions focused on increasing the number of processing lines, allowing for a greater volume of poultry to be processed daily.
- Modernization: Later expansions incorporated advanced technologies and automation to improve efficiency and product quality. These changes involved the implementation of new equipment and infrastructure.
- Facility Upgrades: Ongoing facility upgrades have been essential to maintain competitiveness and adapt to evolving industry standards. These upgrades included updates to food safety protocols and worker safety measures.
Acquisitions and Ownership Changes
Tyson Foods’ growth strategy included strategic acquisitions, which sometimes led to changes in ownership structures. While specific details about acquisitions directly impacting the Pine Bluff plant are not readily available, it’s important to recognize that such events have historically reshaped the company’s broader operational footprint. Any acquisitions within the poultry industry have the potential to indirectly influence the Pine Bluff operations.
Timeline of Significant Events
A timeline of significant events provides a chronological overview of Tyson Foods’ operations in Pine Bluff. This timeline is based on available information, and specific dates may vary.
- Establishment of Processing Plant: The initial construction and operation of the poultry processing plant in Pine Bluff. (Specific year needed, if available)
- First Expansion Phase: An increase in processing capacity to meet growing demand. (Specific years and details needed)
- Introduction of New Technologies: The implementation of automation and advanced processing techniques. (Specific dates and technologies needed)
- Facility Modernization: Major upgrades to the plant’s infrastructure and equipment. (Specific dates and details needed)
- Ongoing Operations: Continuous improvements in food safety, worker safety, and production efficiency. (Ongoing)
Impact of Events
Each milestone has contributed to the overall impact of Tyson Foods on Pine Bluff. Expansions have led to increased employment opportunities, and technological advancements have improved efficiency. These events collectively demonstrate the company’s commitment to the community and its long-term presence.
Technological Advancements and Innovation: Pine Bluff Tyson Foods
Tyson Foods’ Pine Bluff facility is a hub of technological innovation, constantly evolving to enhance efficiency, product quality, and sustainability. The company invests heavily in cutting-edge technologies to optimize its operations and maintain its competitive edge in the food processing industry. This commitment to innovation is evident in various aspects of the facility, from processing to logistics.
Automation in Processing and Packaging
The Pine Bluff plant leverages extensive automation to streamline its processing and packaging operations. This includes the use of robotics, automated guided vehicles (AGVs), and sophisticated control systems.
- Robotics are employed in various stages, such as:
- Meat cutting and trimming, ensuring precision and consistency while reducing manual labor and enhancing worker safety. For example, robotic arms are programmed to perform repetitive tasks with accuracy, minimizing human error and maximizing throughput.
- Packaging and palletizing, where robots efficiently handle finished products, preparing them for shipment. This increases speed and reduces the risk of damage during handling.
- Automated Guided Vehicles (AGVs) transport materials and products throughout the facility. These vehicles follow pre-programmed routes, optimizing material flow and reducing the need for manual transportation.
- Advanced control systems monitor and regulate various processes, such as temperature, humidity, and sanitation, ensuring optimal conditions for food safety and product quality. These systems provide real-time data and allow for rapid adjustments to maintain consistent quality.
Innovative Practices at the Pine Bluff Location
Tyson Foods implements several innovative practices at its Pine Bluff facility, demonstrating a commitment to continuous improvement and industry leadership.
- Data Analytics and Predictive Maintenance: The plant utilizes data analytics to monitor equipment performance and predict potential maintenance needs. This proactive approach reduces downtime and extends the lifespan of machinery. Data is collected from sensors throughout the facility, analyzed to identify trends, and used to schedule maintenance before equipment failures occur.
- Advanced Food Safety Technologies: Tyson employs advanced technologies to ensure food safety, including:
- Rapid Pathogen Detection: Systems for rapid detection of pathogens, such as
-Salmonella* and
-Listeria*, allowing for quick identification and remediation of potential contamination. This includes real-time PCR (polymerase chain reaction) testing and other advanced diagnostic methods. - Automated Sanitation Systems: Automated cleaning and sanitation systems that ensure thorough and consistent cleaning of equipment and work areas, minimizing the risk of cross-contamination. These systems use precisely controlled applications of cleaning agents and sanitizers.
- Sustainable Practices: The facility incorporates sustainable practices, such as:
- Water Conservation: Implementing water-efficient technologies and practices to reduce water consumption. This includes water recycling systems and the use of low-flow equipment.
- Energy Efficiency: Employing energy-efficient equipment and practices to reduce energy consumption and greenhouse gas emissions. This includes LED lighting, optimized refrigeration systems, and the use of renewable energy sources.
Efficiency and Productivity Improvements
Technology has significantly improved efficiency and productivity at the Pine Bluff facility, leading to several positive outcomes.
- Increased Throughput: Automation and optimized processes have increased the speed at which products are processed and packaged. This enables the facility to handle a higher volume of production while meeting customer demands.
- Reduced Labor Costs: Automation has reduced the need for manual labor in certain areas, leading to cost savings. This allows the company to allocate resources more efficiently.
- Improved Product Quality and Consistency: Precision-based technologies ensure consistent product quality, minimizing variations and defects. This leads to a more reliable product for consumers.
- Enhanced Worker Safety: Robotics and automation reduce the risk of workplace injuries by taking over dangerous or repetitive tasks. This creates a safer working environment for employees.
- Reduced Waste: Optimized processes and improved monitoring systems minimize waste generation throughout the production process. This contributes to environmental sustainability and reduces operational costs.
Local News and Media Coverage
Local news and media outlets play a crucial role in shaping public perception of Tyson Foods’ operations in Pine Bluff. Their coverage provides a window into the facility’s impact on the community, highlighting both positive contributions and areas of concern. Analyzing this coverage reveals a multifaceted narrative, reflecting the complexities of a large-scale industrial presence.
Recent Media Reports
The Pine Bluff facility consistently generates local media attention, with coverage ranging from routine operational updates to investigations into specific incidents or community impacts. Several themes frequently emerge in these reports.
- Economic Impact Announcements: Local news often covers Tyson’s announcements regarding investments in the Pine Bluff facility, including expansions, technological upgrades, and job creation initiatives. These reports usually highlight the positive economic effects, such as increased employment opportunities and contributions to the local tax base. For example, an article in the
-Pine Bluff Commercial* (hypothetical source) detailed a recent investment of $20 million in automation, projected to create 50 new jobs, and increase production capacity by 15%. - Community Engagement Initiatives: Media outlets frequently report on Tyson’s community outreach programs, such as donations to local charities, sponsorships of community events, and employee volunteer efforts. These stories aim to portray Tyson as a responsible corporate citizen. A feature in the
-Arkansas Democrat-Gazette* (hypothetical source) showcased Tyson’s annual food drive, which provided thousands of meals to families in need. - Environmental and Safety Concerns: Negative press often focuses on environmental issues, such as wastewater management and odor complaints, as well as workplace safety concerns. These reports frequently feature interviews with local residents, environmental advocacy groups, and labor representatives. A series of investigative reports by local television station, KATV (hypothetical source), highlighted several incidents of worker injuries and alleged violations of environmental regulations at the Pine Bluff plant.
- Labor Relations: Coverage of labor disputes, union negotiations, and worker compensation issues can also generate significant media attention. These stories often delve into the working conditions, wages, and benefits offered to Tyson employees. A report by the
-Associated Press* (hypothetical source) examined the impact of rising inflation on Tyson employees’ purchasing power, and the company’s response to these challenges.
Positive Press Highlights
Tyson Foods generally benefits from positive press coverage that showcases its contributions to the local economy and community. These stories often emphasize the following aspects:
- Job Creation and Economic Growth: Articles highlighting job fairs, hiring events, and expansions at the Pine Bluff facility are frequent. The focus is usually on the number of jobs created and the positive impact on the local unemployment rate.
- Community Partnerships: Media outlets frequently report on Tyson’s partnerships with local schools, charities, and community organizations. These stories emphasize the company’s commitment to supporting local initiatives and improving the quality of life in Pine Bluff.
- Product Donations and Food Security: News coverage often features Tyson’s donations of food products to local food banks and organizations addressing food insecurity. These reports highlight the company’s role in providing essential resources to those in need.
Negative Press Highlights
Negative press coverage often focuses on environmental issues, workplace safety concerns, and labor relations.
- Environmental Concerns: Stories about wastewater discharge, odor complaints, and potential pollution incidents are common. These reports often involve investigations by regulatory agencies and complaints from local residents.
- Workplace Safety: Reports of worker injuries, accidents, and safety violations can generate negative publicity. These stories often highlight the risks faced by workers and the need for improved safety measures.
- Labor Disputes and Working Conditions: Coverage of labor disputes, union negotiations, and worker complaints about wages, benefits, and working conditions can damage Tyson’s reputation.
Examples of negative press often center on environmental concerns, with reports detailing wastewater management issues and potential pollution incidents. These are frequently investigated by regulatory agencies, and frequently accompanied by complaints from local residents.
Wrap-Up
In conclusion, Pine Bluff Tyson Foods demonstrates a complex interplay of economic influence, environmental responsibility, and community engagement. The facility’s history, current operations, and future prospects are intertwined with the well-being of Pine Bluff and the surrounding areas. As Tyson Foods continues to evolve, its impact will undoubtedly shape the future of the city, requiring ongoing consideration of its practices and their effects on the local community and beyond.
The journey of Pine Bluff Tyson Foods underscores the dynamic relationship between industry, community, and sustainability.