The world of a food packaging factory is a complex yet fascinating one, where innovation meets practicality to deliver safe and appealing products to consumers. This overview will delve into the intricacies of these factories, from the layout and operational flow to the diverse materials and cutting-edge technologies that define the industry.
We’ll explore the crucial stages of the packaging process, including the selection of materials like plastic, paper, and metal, each with its own set of advantages and disadvantages. Moreover, the role of machinery, from filling and sealing to labeling, and the importance of food safety regulations and sustainability will be discussed. Finally, the journey will conclude with a glimpse into the future, highlighting emerging trends and innovative packaging solutions that are reshaping the food industry.
Factory Overview and Operations
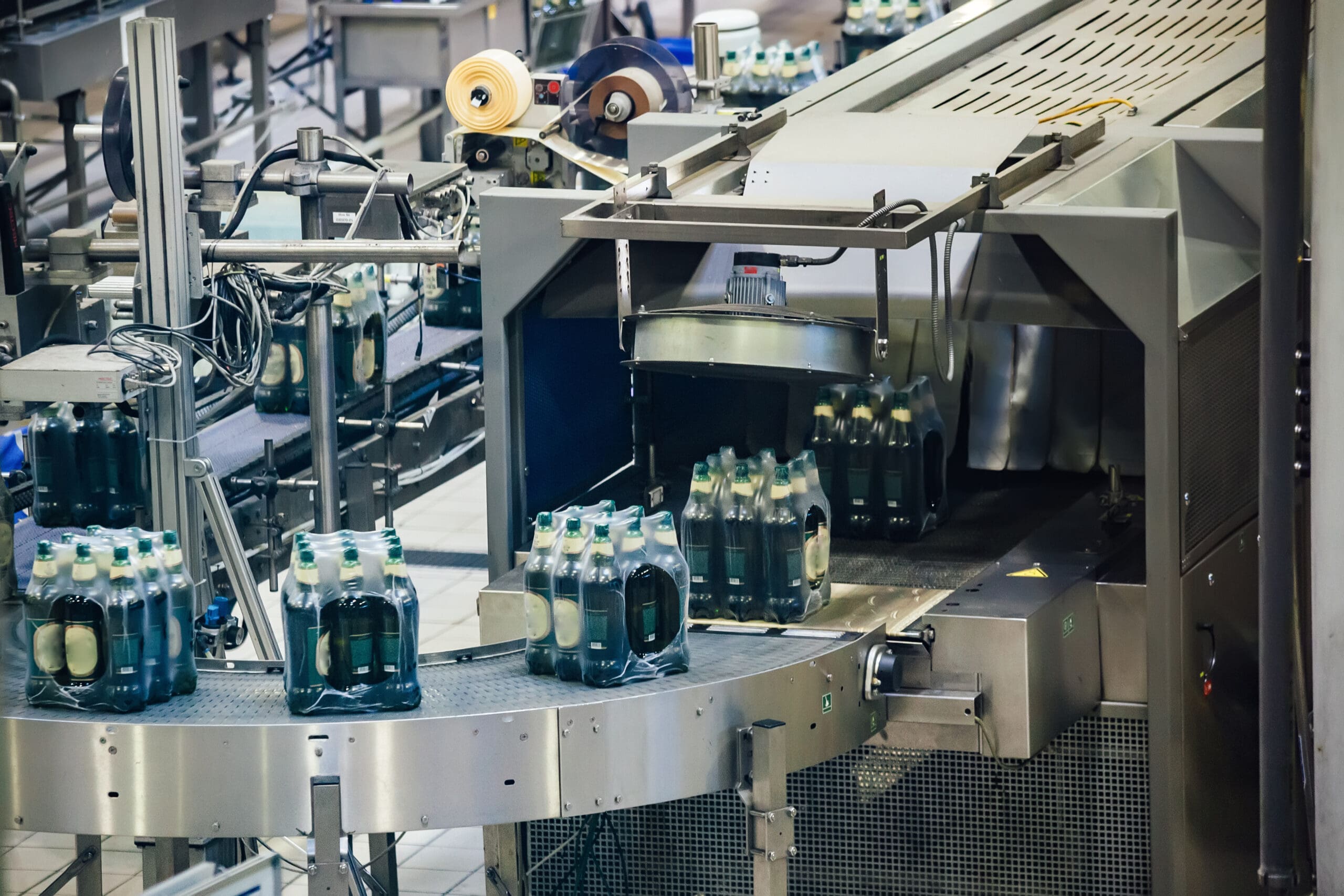
The efficient operation of a food packaging factory is crucial for ensuring product safety, minimizing waste, and meeting consumer demand. A well-designed factory layout and streamlined processes are fundamental to achieving these goals. This section provides an overview of the typical structure, operational stages, and technological advancements within a modern food packaging facility.
Factory Layout and Zones
A typical food packaging factory is meticulously organized into distinct zones to maintain hygiene, prevent cross-contamination, and optimize workflow. These zones are carefully planned to accommodate the specific needs of food processing and packaging.The factory layout typically includes the following zones:* Raw Material Receiving and Storage: This area receives incoming raw materials, such as packaging films, cartons, and other components. It includes inspection areas, temperature-controlled storage for perishables, and warehousing for non-perishable items.
Production Area
This is the heart of the factory, where the packaging process takes place. It is further subdivided into:
Processing Zone
Where food products are prepared or pre-processed (e.g., cleaning, cutting, mixing).
Filling Zone
Where the food product is filled into its packaging.
Sealing Zone
Where the packaging is sealed to ensure product integrity.
Labeling and Coding Zone
Where labels, date codes, and other information are applied to the packaged product.
Quality Control (QC) and Inspection Area
Dedicated to ensuring product quality and safety. It includes laboratories for testing samples, inspection stations for visual checks, and equipment for measuring parameters such as weight and seal integrity.
Finished Goods Storage
This area stores the packaged products before they are shipped to distributors or retailers. It often includes temperature-controlled storage and efficient inventory management systems.
Waste Management Area
This zone handles waste generated during the packaging process, including recycling and disposal.
Maintenance and Engineering Area
This area houses equipment for maintaining machinery, performing repairs, and ensuring the smooth operation of the factory.
Offices and Administrative Area
This zone accommodates administrative staff, management, and support functions.
Staff Amenities
Includes areas like changing rooms, restrooms, and break rooms.
Key Stages of the Food Packaging Process
The food packaging process involves a series of interconnected stages, each critical to the final product’s quality, safety, and presentation. These stages are designed to protect the food product from contamination, spoilage, and physical damage.The key stages are:* Raw Material Procurement: Sourcing and receiving packaging materials like films, cartons, and closures. Ensuring materials meet quality standards and regulatory requirements.
Packaging Material Preparation
This step involves preparing the packaging materials for the filling process. It may include printing, cutting, forming, or sterilizing packaging components.
Food Product Preparation
Preparing the food product for packaging, which can involve cleaning, processing, cooking, or portioning.
Filling
Dispensing the food product into the packaging material. This stage is critical to ensure accurate fill weights and volumes.
Sealing
Closing and sealing the packaging to protect the food product from external contaminants and maintain its freshness. Various sealing methods are used, including heat sealing, induction sealing, and vacuum sealing.
Labeling and Coding
Applying labels with product information, including ingredients, nutritional facts, date codes, and bar codes. This stage is essential for traceability and regulatory compliance.
Inspection and Quality Control
Inspecting the packaged product for defects, ensuring proper sealing, and verifying that all labeling requirements are met. This stage includes weight checks, seal integrity tests, and visual inspections.
Secondary Packaging
Grouping individual packaged products into larger units, such as cartons or cases, for easier handling and transportation.
Storage and Distribution
Storing the packaged products in a controlled environment and preparing them for distribution to retailers or consumers.
Diagram: Material and Product Flow, Food packaging factory
The diagram illustrates the typical flow of materials and products within a food packaging factory. The diagram demonstrates the movement of materials from the receiving area through the production process to the finished goods storage and distribution. Diagram Description:The diagram is a simplified flow chart illustrating the process. It starts with the “Raw Material Receiving” area, where packaging materials and raw food ingredients enter the factory.
Arrows indicate the flow to “Storage” areas for both packaging and ingredients. Packaging materials then move to “Packaging Material Preparation,” while food ingredients go to “Food Product Preparation.” Both streams converge at “Filling,” followed by “Sealing,” “Labeling & Coding,” and “Inspection & Quality Control.” Approved products proceed to “Secondary Packaging” and then to “Finished Goods Storage.” Finally, the packaged products are dispatched to “Distribution.” Waste from each stage is directed to a “Waste Management” area.
The diagram highlights the importance of quality control checks at various stages to ensure product safety and integrity.
Automation in Modern Food Packaging
Automation plays a pivotal role in modern food packaging factories, driving efficiency, improving product quality, and reducing labor costs. Automation encompasses the use of advanced technologies to streamline and optimize various aspects of the packaging process.The key areas of automation include:* Automated Material Handling: Robotic systems and conveyor belts transport raw materials, packaging components, and finished products throughout the factory.
Automated Filling and Sealing
High-speed filling machines and automated sealing equipment ensure accurate portioning, efficient sealing, and consistent product quality.
Automated Inspection Systems
Vision systems and sensors perform automated inspections to detect defects, ensure proper labeling, and verify seal integrity.
Robotics
Robots are used for various tasks, including picking and placing products, packing, and palletizing.
Data Analytics and Monitoring
Advanced software systems collect data from various stages of the packaging process, providing real-time insights into production performance, quality control, and equipment maintenance. This data allows for proactive decision-making and continuous improvement.
Automated Labeling and Coding
Automated systems apply labels, date codes, and bar codes to packaging materials, ensuring accuracy and compliance with regulations.For example, in the snack food industry, automated packaging lines can package up to 600 bags of chips per minute. This high-speed packaging reduces labor costs and minimizes the chance of human error, leading to more consistent product quality and higher production volumes.
Furthermore, the use of robotic palletizers has significantly increased the efficiency of loading finished products onto pallets for shipping, reducing the time and labor required.
Materials and Packaging Types
Selecting the right packaging materials is crucial for preserving food quality, extending shelf life, and ensuring consumer safety. The food industry utilizes a wide range of materials and packaging types, each with its own set of advantages and disadvantages. Understanding these options is vital for optimizing packaging solutions and meeting the specific needs of various food products.
Common Packaging Materials
The food industry relies on several primary packaging materials to protect and preserve food. These materials offer different properties that influence their suitability for specific applications.
- Plastics: Polyethylene (PE), polypropylene (PP), polyethylene terephthalate (PET), and others. Plastics are widely used due to their versatility, cost-effectiveness, and barrier properties.
- Paper and Paperboard: Corrugated cardboard, paperboard cartons, and paper bags. These materials are favored for their biodegradability and recyclability.
- Metals: Aluminum and steel, primarily used in cans. Metals offer excellent barrier properties and are often used for long-term food preservation.
- Glass: Glass jars and bottles. Glass provides excellent barrier properties and is often perceived as a premium packaging choice.
- Flexible Films: Used in pouches and wrappers, often made from a combination of plastic and other materials. These films offer good barrier properties and are lightweight.
Comparing Packaging Materials
Each packaging material presents a unique set of benefits and drawbacks, impacting its suitability for different food products. The choice of material depends on factors like the food product’s characteristics, desired shelf life, and sustainability goals.
- Plastic: Advantages include its low cost, lightweight nature, and excellent barrier properties against moisture and gases. Disadvantages include environmental concerns related to disposal and the potential for leaching chemicals into food. An example of plastic packaging is PET bottles for soft drinks.
- Paper: Advantages include biodegradability, recyclability, and its renewable resource base. Disadvantages include lower barrier properties compared to plastic and metal, making it less suitable for products requiring extended shelf life or protection from moisture. Paper packaging is frequently used for dry goods like cereals and snacks.
- Metal: Advantages include exceptional barrier properties, making it ideal for preserving food for extended periods. Disadvantages include higher cost, weight, and the potential for corrosion if not properly coated. Canned goods, such as soups and vegetables, commonly utilize metal packaging.
Selecting Packaging Materials for Food Products
The selection of packaging materials is a complex process that considers various factors to ensure product safety, quality, and consumer satisfaction.
- Food Product Characteristics: The type of food product dictates the necessary protection level. For example, highly perishable foods require packaging with excellent barrier properties to prevent spoilage.
- Shelf Life Requirements: The desired shelf life influences the choice of material. Products requiring a long shelf life often utilize packaging with superior barrier properties, such as metal cans or multi-layer films.
- Cost Considerations: Packaging costs significantly impact overall product costs. Manufacturers must balance performance requirements with budgetary constraints.
- Sustainability Goals: Consumers and businesses are increasingly focused on sustainable packaging options. Recyclable and biodegradable materials are gaining popularity.
- Regulatory Compliance: Food packaging must comply with regulations regarding food safety and labeling.
Comparison of Packaging Types
The following table provides a comparative overview of different packaging types based on key factors.
Packaging Type | Cost | Sustainability | Protection | Examples |
---|---|---|---|---|
Pouches (Flexible Films) | Low to Moderate | Moderate (Recyclability varies; multi-layer films can be challenging) | Good (Barrier properties can be tailored) | Snack foods, coffee, frozen vegetables |
Cartons (Paperboard) | Moderate | Good (Recyclable and biodegradable) | Moderate (Protects against crushing, limited barrier properties) | Cereals, dry goods, frozen foods |
Cans (Metal) | High | Moderate (Recyclable, but manufacturing can be energy-intensive) | Excellent (Provides a strong barrier against light, air, and moisture) | Canned vegetables, soups, fruits |
Bottles (Glass/Plastic) | Moderate to High (depending on material) | Moderate (Glass is recyclable; plastic recyclability varies) | Good (Protects against contamination, provides visibility) | Beverages, sauces, dressings |
Equipment and Machinery
Food packaging factories rely heavily on specialized equipment and machinery to efficiently process, package, and prepare food products for distribution. The selection and maintenance of this equipment are critical for ensuring product quality, safety, and operational efficiency. This section will delve into the different types of machinery, their specific functions, the importance of preventative maintenance, and a typical packaging line process.
Types of Machinery Used
A wide array of machinery is employed in food packaging, each designed to perform specific tasks within the overall packaging process. These machines are typically categorized based on their function.
- Filling Machines: These machines accurately dispense the product into its packaging. They vary depending on the product’s consistency (liquid, powder, solid) and the packaging type.
- Sealing Machines: Sealing machines create a secure closure for the packaging, preventing contamination and preserving product freshness. Different sealing methods are used depending on the packaging material.
- Labeling Machines: Labeling machines apply labels to the packaging, providing essential product information such as ingredients, nutritional facts, and branding.
- Form-Fill-Seal (FFS) Machines: These machines form packaging from rolls of film or other materials, fill them with product, and seal them in a continuous process.
- Inspection Systems: Inspection systems use various technologies, such as cameras and sensors, to check for defects, fill levels, and foreign objects in the packaging.
- Coding and Marking Machines: These machines print date codes, lot numbers, and other identification marks on the packaging.
- Cartoning Machines: Cartoning machines automatically place packaged products into cartons or boxes.
- Palletizing Machines: Palletizing machines stack packaged products onto pallets for shipping and storage.
Functions of Filling, Sealing, and Labeling Machines
The core of any packaging line consists of filling, sealing, and labeling machines, each playing a crucial role in the final product. Understanding their specific functions is essential.
- Filling Machines: Filling machines are responsible for accurately dispensing the food product into its packaging. There are several types, including:
- Volumetric Fillers: These fillers measure a specific volume of product. They are suitable for free-flowing products like grains and powders.
- Gravimetric Fillers: Gravimetric fillers weigh the product to ensure accurate fill weights. They are often used for products where precise weight is critical.
- Piston Fillers: Piston fillers use a piston to draw product into a cylinder and then dispense it into the package. They are suitable for liquids and semi-viscous products.
- Sealing Machines: Sealing machines ensure that the packaging is securely closed, protecting the product from external contaminants and preserving its shelf life. Common sealing methods include:
- Heat Sealing: Heat sealing uses heat to melt and fuse the packaging material, creating a hermetic seal. This is common for plastic films and pouches.
- Impulse Sealing: Impulse sealing applies a short burst of heat to seal the packaging.
- Induction Sealing: Induction sealing uses electromagnetic induction to heat a foil seal inside the package cap.
- Labeling Machines: Labeling machines apply labels to the packaging, providing essential information and branding. Different labeling methods exist, including:
- Pressure-Sensitive Labeling: This method applies labels that have an adhesive backing.
- Wrap-Around Labeling: Wrap-around labeling applies a label that wraps around the entire container.
Importance of Preventative Maintenance
Preventative maintenance is critical for ensuring the reliability, efficiency, and longevity of packaging equipment. Regular maintenance reduces downtime, minimizes repair costs, and maintains product quality.
- Reduced Downtime: Regular maintenance, such as lubrication, cleaning, and part replacement, helps prevent unexpected breakdowns, minimizing downtime and production delays.
- Extended Equipment Life: Preventative maintenance extends the lifespan of machinery by addressing potential issues before they escalate into major problems.
- Improved Product Quality: Properly maintained equipment ensures accurate filling, sealing, and labeling, contributing to consistent product quality and minimizing product waste.
- Enhanced Safety: Regular inspections and maintenance can identify and address safety hazards, protecting workers and preventing accidents.
- Cost Savings: Although preventative maintenance requires an initial investment, it can lead to significant cost savings in the long run by reducing the need for expensive emergency repairs and minimizing production losses.
Process Flow Chart of a Typical Packaging Line
A typical packaging line involves a series of steps, from receiving raw materials to preparing the packaged product for shipment. The specific steps and machinery involved will vary depending on the product and packaging type. The following illustrates a general process flow.
+---------------------+ +---------------------+ +---------------------+ +---------------------+ +---------------------+ +---------------------+ | Raw Material | --> | Filling Machine | --> | Sealing Machine | --> | Labeling Machine | --> | Inspection System | --> | Cartoning/Palletizing| | Receiving | | (e.g., Volumetric) | | (e.g., Heat Seal) | | (e.g., Pressure- | | (e.g., Camera-based) | | (e.g., Cartoner) | +---------------------+ +---------------------+ +---------------------+ | Sensitive) | +---------------------+ +---------------------+ | | | | +---------------------+ | Coding and Marking | | Machine | +---------------------+
Note: The diagram provides a simplified overview, and the specific machinery and steps can vary significantly based on the product and packaging requirements. For example, a packaging line for a ready-to-eat meal might involve a different sequence and equipment compared to a line packaging cereal.
Sustainability and Eco-Friendly Practices
Food packaging, while essential for protecting products and extending shelf life, significantly impacts the environment. The industry faces increasing pressure to adopt sustainable practices to minimize its ecological footprint. This involves a shift towards eco-friendly materials, waste reduction strategies, and energy-efficient operations.
Environmental Impact of Food Packaging
The environmental impact of food packaging is multifaceted, encompassing resource depletion, pollution, and greenhouse gas emissions. Traditional packaging materials, such as plastics, often rely on fossil fuels for production. Their disposal contributes to landfill waste and plastic pollution in oceans and ecosystems. The manufacturing processes for packaging materials, including paper and cardboard, can also consume significant amounts of energy and water.
Furthermore, the transportation of packaging materials and packaged goods contributes to carbon emissions.
Sustainable Packaging Materials and Practices
Several sustainable packaging materials and practices are available to mitigate the environmental impact of food packaging. These alternatives focus on reducing waste, using renewable resources, and minimizing pollution.
- Compostable Packaging: Materials like bioplastics (made from cornstarch or sugarcane) and paper-based packaging that can break down naturally in composting facilities or home composts.
- Recycled Content Packaging: Utilizing recycled materials, such as recycled paperboard or recycled plastic, to create new packaging, reducing the demand for virgin resources.
- Reusable Packaging: Implementing systems that encourage the reuse of packaging, such as refillable containers or returnable shipping systems.
- Plant-Based Plastics: Employing plastics derived from renewable resources like corn, sugarcane, or algae, which have a lower carbon footprint than traditional plastics.
Methods for Reducing Waste and Improving Environmental Footprint
Food packaging factories can implement various methods to reduce waste and improve their environmental footprint. These practices aim to optimize resource use, minimize pollution, and promote a circular economy.
- Optimizing Packaging Design: Designing packaging to minimize material usage, reduce void space, and enhance recyclability. This includes lightweighting packaging, using less material overall.
- Implementing Recycling Programs: Establishing effective recycling programs within the factory to collect and process packaging waste.
- Reducing Energy Consumption: Investing in energy-efficient equipment, such as LED lighting and optimized machinery, and using renewable energy sources.
- Reducing Water Usage: Implementing water-saving technologies and practices throughout the manufacturing process.
- Source Reduction: Minimizing the amount of packaging material used in the first place. This can be achieved through lightweighting, consolidation, and eliminating unnecessary packaging layers.
- Waste Diversion: Implementing strategies to divert waste from landfills, such as composting organic waste and sending non-recyclable materials to waste-to-energy facilities.
Sustainable Packaging Solutions Table
The following table presents different sustainable packaging solutions and their benefits.
Packaging Solution | Material | Benefits | Considerations |
---|---|---|---|
Compostable Packaging | Bioplastics (PLA, PHA), paper-based materials | Reduces landfill waste, breaks down naturally, made from renewable resources. | Requires access to composting facilities, may not be suitable for all food types. |
Recycled Content Packaging | Recycled paperboard, recycled PET | Reduces demand for virgin materials, lowers energy consumption compared to virgin production. | May have limitations in terms of food safety and performance, sourcing of high-quality recycled materials. |
Reusable Packaging | Durable plastics, glass, stainless steel | Reduces waste generation, minimizes the need for single-use packaging, can be cost-effective over time. | Requires a robust collection and cleaning infrastructure, potential for increased transportation emissions if not optimized. |
Plant-Based Plastics | PLA (from corn), PHA (from various sources) | Lower carbon footprint than traditional plastics, derived from renewable resources. | May require specialized composting facilities, potential for land use competition with food crops. |
Quality Control and Inspection
Maintaining the integrity and safety of food packaging is paramount in ensuring consumer health and brand reputation. Rigorous quality control and inspection procedures are essential within a food packaging factory to identify and rectify potential issues throughout the production process. This proactive approach minimizes the risk of defective packaging, product contamination, and potential recalls.
Role of Quality Control in Food Packaging Factories
Quality control (QC) serves as a critical function in food packaging factories, acting as a gatekeeper to ensure that all materials, processes, and finished products meet the required standards and specifications. It involves a comprehensive system of checks, inspections, and tests designed to prevent defects and ensure consistent product quality. The QC department is responsible for setting quality standards, monitoring production processes, and taking corrective actions when deviations are identified.
The ultimate goal is to provide consumers with safe, reliable, and high-quality food packaging that protects the product and preserves its freshness. Effective QC also helps to minimize waste, reduce costs, and enhance the overall efficiency of the manufacturing operation.
Methods Used to Inspect Packaging Materials and Finished Products
Inspection methods are diverse, ranging from visual assessments to advanced instrumental analyses, to guarantee that packaging materials and finished products meet the required quality standards. These methods are applied at various stages of the production process, from raw material intake to the final packaging of the food product.
- Visual Inspection: This is a fundamental step, involving a close examination of the packaging for any visible defects such as tears, punctures, misprints, or inconsistencies in the material. Inspectors use their eyes to assess the overall appearance, clarity, and color of the packaging. This process is often augmented by the use of specialized lighting to highlight any imperfections.
- Dimensional Measurement: Accurate dimensions are critical for ensuring that packaging fits correctly and functions as intended. Measurements are taken using calibrated instruments like calipers, micrometers, and rulers to verify that the packaging meets the specified size and shape requirements. Deviations from the established standards can lead to issues in filling, sealing, and overall product presentation.
- Leak Testing: This is a crucial test to confirm that the packaging provides an effective barrier against external contaminants. Methods include air pressure testing, water immersion tests, and dye penetration tests. The goal is to identify any leaks or weaknesses in the packaging that could compromise the product’s safety and shelf life. For example, air pressure testing involves sealing the package and applying air pressure to detect any pressure drop, which indicates a leak.
- Seal Integrity Testing: The seals of the packaging are carefully inspected to ensure they are strong and airtight. This is often achieved through methods such as peel tests, tensile strength tests, and burst tests. Seal integrity is essential for preventing product spoilage, maintaining freshness, and preventing contamination. The results are measured to ensure that the sealing process is consistently achieving the required level of performance.
Discover more by delving into indian food catering jersey city further.
- Material Testing: The physical and chemical properties of packaging materials are rigorously tested to ensure they meet the required specifications. This can include tests for tensile strength, impact resistance, barrier properties (such as oxygen and moisture permeability), and chemical resistance. These tests help to determine the durability and protective capabilities of the packaging.
- Functional Testing: This involves simulating real-world conditions to evaluate the packaging’s performance. Examples include drop tests, vibration tests, and stacking tests. These tests assess the packaging’s ability to withstand handling, transportation, and storage without compromising the product’s integrity. For example, drop tests involve dropping the packaged product from a specified height to assess its resistance to impact.
- Printing Quality Inspection: If the packaging involves printing, the quality of the printing is assessed. This includes checking for correct color registration, print clarity, and the accuracy of text and graphics. Inspectors use specialized equipment, such as spectrophotometers, to measure color accuracy and ensure that the printed information meets the required standards.
Key Quality Control Parameters Typically Monitored
Several key parameters are consistently monitored during the food packaging manufacturing process to ensure consistent quality and compliance with regulations. These parameters are crucial for guaranteeing the safety, integrity, and shelf life of the packaged food products.
- Material Specifications: Verifying that all incoming raw materials, such as films, paperboard, and adhesives, meet the required specifications for composition, thickness, and other relevant properties. This includes confirming that the materials are sourced from approved suppliers and that they comply with food safety regulations.
- Dimensional Accuracy: Ensuring that the dimensions of the packaging, including height, width, and depth, are within the specified tolerances. This is critical for proper filling, sealing, and overall product fit.
- Seal Integrity: Monitoring the strength and airtightness of the seals to prevent leakage and maintain product freshness. This involves regular testing of seal strength and leak resistance.
- Barrier Properties: Assessing the packaging’s ability to protect the food product from external factors such as oxygen, moisture, and light. This is essential for maintaining the product’s shelf life and preventing spoilage.
- Print Quality: Verifying the accuracy, clarity, and color consistency of any printed information on the packaging. This includes checking for correct text, graphics, and bar codes.
- Cleanliness and Sanitation: Ensuring that the packaging materials and production environment are clean and free from contaminants. This involves implementing strict sanitation protocols and regularly monitoring for potential hazards.
- Weight and Fill Accuracy: Confirming that the correct amount of product is filled into each package. This involves regular weight checks and adjustments to the filling equipment as needed.
- Visual Appearance: Inspecting the packaging for any visible defects, such as tears, punctures, or misprints. This ensures that the packaging is visually appealing and meets the required standards.
Quality Control Procedures Checklist for a Food Packaging Factory
A well-defined checklist ensures that all quality control procedures are consistently followed. This structured approach helps to maintain high standards and minimize the risk of errors. The following is a comprehensive checklist:
- Incoming Material Inspection:
- Verify material specifications against purchase orders.
- Inspect materials for visible defects (e.g., tears, contamination).
- Perform dimensional checks (e.g., thickness, width).
- Conduct material testing (e.g., tensile strength, barrier properties).
- Document inspection results and maintain records.
- Production Process Monitoring:
- Monitor machine settings and operating parameters.
- Conduct regular visual inspections of packaging during production.
- Perform dimensional checks on finished packaging.
- Conduct seal integrity tests (e.g., leak tests, peel tests).
- Monitor print quality (e.g., color registration, text accuracy).
- Check fill weights and volumes.
- Implement and enforce sanitation protocols.
- Maintain detailed production records and track any deviations.
- Finished Product Inspection:
- Conduct a final visual inspection of finished packaging.
- Perform comprehensive functional tests (e.g., drop tests, stacking tests).
- Conduct final seal integrity tests.
- Verify labeling and coding accuracy.
- Conduct a final review of all inspection results.
- Calibration and Maintenance:
- Calibrate all measuring and testing equipment regularly.
- Maintain a schedule for equipment maintenance.
- Keep detailed records of calibration and maintenance activities.
- Documentation and Record Keeping:
- Maintain detailed records of all inspections, tests, and corrective actions.
- Ensure all records are accurate, complete, and readily accessible.
- Establish a system for tracking and resolving any quality issues.
- Employee Training and Competency:
- Provide comprehensive training to all employees involved in quality control.
- Ensure employees are competent in performing their assigned tasks.
- Regularly assess employee performance and provide feedback.
- Corrective and Preventive Actions:
- Implement a system for identifying and addressing quality issues.
- Conduct root cause analysis to determine the underlying causes of defects.
- Implement corrective actions to prevent recurrence.
- Establish preventive measures to avoid potential issues.
Supply Chain and Logistics
An efficient supply chain is crucial for the success of a food packaging factory. It directly impacts production costs, product quality, and delivery times. A well-managed supply chain ensures the timely availability of raw materials, efficient production processes, and prompt delivery of finished products to customers, ultimately contributing to profitability and customer satisfaction.
Importance of an Efficient Supply Chain
The efficiency of a food packaging factory’s supply chain significantly affects its operational effectiveness. Delays in receiving raw materials, for example, can halt production, leading to lost revenue and potential penalties for late deliveries. Conversely, inefficient logistics can result in higher transportation costs and damage to finished products. A streamlined supply chain allows for better inventory management, waste reduction, and improved responsiveness to market demands.
This, in turn, enables the factory to maintain competitive pricing, meet customer expectations, and adapt quickly to changes in the market.
Logistics of Receiving Raw Materials and Shipping Finished Products
The logistics involved in a food packaging factory encompass a series of interconnected steps, from sourcing raw materials to delivering finished products. These steps must be meticulously planned and executed to ensure efficiency and minimize disruptions.
- Receiving Raw Materials: This begins with sourcing materials like paperboard, plastics, inks, and adhesives from various suppliers. Upon arrival at the factory, materials are inspected for quality and quantity. They are then stored in designated areas, such as temperature-controlled warehouses for sensitive materials. Effective inventory management, including tracking and forecasting, is critical to avoid shortages and minimize waste.
- Production Process: Raw materials are then fed into the production line, where they undergo various processes such as printing, cutting, and forming.
- Quality Control: Throughout the production process, quality control checks are performed to ensure that the packaging meets the required standards for food safety and durability.
- Storage of Finished Products: Once the packaging is complete, it is stored in a warehouse, ready for shipment. The storage environment must protect the packaging from damage and maintain its integrity.
- Shipping Finished Products: Finished products are prepared for shipment, often involving palletizing and wrapping. Transportation is arranged using various modes, such as trucks, trains, or ships, depending on the destination and volume. Careful planning of shipping routes and modes of transport is essential to minimize costs and ensure timely delivery.
- Delivery to Customers: Finally, the packaged food products are delivered to the customer, such as food manufacturers or distributors. Proof of delivery is obtained to confirm the successful completion of the logistics process.
Strategies for Optimizing the Supply Chain and Reducing Costs
Several strategies can be employed to optimize the supply chain and reduce costs in a food packaging factory. These strategies often involve leveraging technology, building strong relationships with suppliers, and implementing lean manufacturing principles.
- Supplier Relationship Management: Establishing strong relationships with suppliers is essential. This includes negotiating favorable pricing, ensuring consistent quality, and collaborating on supply chain improvements. For example, long-term contracts can provide price stability and secure access to critical materials.
- Inventory Management Techniques: Implementing inventory management techniques such as Just-In-Time (JIT) inventory can minimize storage costs and reduce the risk of obsolescence. This involves receiving materials only when they are needed for production.
- Transportation Optimization: Optimizing transportation routes and modes can significantly reduce costs. This can involve using transportation management systems (TMS) to plan and manage shipments efficiently. Consolidating shipments and negotiating favorable rates with transportation providers are also effective strategies.
- Technology Integration: Using technology such as Enterprise Resource Planning (ERP) systems can improve supply chain visibility and enable better decision-making. Real-time data on inventory levels, production schedules, and transportation status can help identify and address potential problems.
- Lean Manufacturing Principles: Implementing lean manufacturing principles can help reduce waste, improve efficiency, and optimize the flow of materials. This includes eliminating unnecessary steps in the production process, reducing setup times, and implementing continuous improvement initiatives.
- Demand Forecasting: Accurate demand forecasting is critical for planning production and managing inventory. Using historical sales data, market trends, and customer feedback can help improve forecasting accuracy and minimize the risk of overstocking or stockouts.
- Automation: Automating various processes, such as material handling and packaging, can improve efficiency and reduce labor costs.
Implementing these strategies requires a holistic approach, involving all stakeholders in the supply chain. Continuous monitoring and evaluation are also crucial to identify areas for improvement and adapt to changing market conditions.
Trends and Innovations: Food Packaging Factory
The food packaging industry is constantly evolving, driven by consumer demand, technological advancements, and environmental concerns. Staying abreast of these trends and embracing innovations is crucial for food packaging factories to remain competitive and meet the challenges of the future. This section will explore the most significant developments shaping the industry.
Emerging Trends in Food Packaging
Several key trends are reshaping the food packaging landscape. These trends reflect shifts in consumer preferences, regulatory pressures, and technological advancements.
- Sustainability: There is a growing emphasis on sustainable packaging materials and practices. Consumers are increasingly aware of the environmental impact of packaging and demand eco-friendly alternatives. This includes the use of recycled materials, biodegradable plastics, and reduced packaging.
- Convenience: Consumers prioritize convenience, leading to demand for packaging that is easy to use, resealable, microwaveable, and portion-controlled. Single-serve packaging and on-the-go formats are becoming increasingly popular.
- E-commerce Integration: The rise of e-commerce has significantly impacted food packaging. Packaging must be robust enough to withstand shipping and handling, while also maintaining product freshness and integrity.
- Food Safety and Traceability: Consumers and regulators place a high value on food safety and traceability. Packaging is evolving to provide enhanced protection against contamination and facilitate tracking of products throughout the supply chain.
- Personalization and Customization: Brands are seeking ways to personalize packaging to connect with consumers. This includes customized designs, messaging, and interactive elements.
Innovative Packaging Technologies
Innovation is at the forefront of food packaging, with several technologies emerging to enhance product preservation, consumer experience, and sustainability.
- Active Packaging: Active packaging interacts with the food to extend shelf life and maintain quality. This includes oxygen scavengers, moisture absorbers, and antimicrobial agents incorporated into the packaging materials. For example, oxygen-absorbing sachets are used in packaged meats to prevent spoilage.
- Smart Packaging: Smart packaging utilizes sensors and indicators to provide real-time information about the product’s condition. This can include temperature sensors, freshness indicators, and RFID tags for tracking and tracing.
- Edible Packaging: Edible packaging is made from materials that are safe to consume, such as seaweed or plant-based films. This reduces waste and provides a novel consumer experience.
- Modified Atmosphere Packaging (MAP): MAP technology modifies the gas composition within the package to extend shelf life and preserve food quality. This is commonly used for fresh produce, meats, and cheeses.
- Sustainable Materials: The development and utilization of sustainable materials like mushroom packaging, seaweed-based packaging, and recycled plastics is increasing. These materials aim to reduce environmental impact.
Impact of E-commerce on Food Packaging Factories
E-commerce has significantly altered the requirements for food packaging, presenting both challenges and opportunities for factories.
- Increased Durability: Packaging must withstand the rigors of shipping and handling, including drops, vibrations, and temperature fluctuations. This requires more robust materials and designs.
- Temperature Control: Maintaining the correct temperature is critical for perishable foods. E-commerce packaging often includes insulated materials, refrigerants, and temperature monitoring systems.
- Shipping Efficiency: Packaging needs to be lightweight and space-efficient to minimize shipping costs. This encourages innovative designs that reduce void space and optimize material usage.
- Brand Presentation: E-commerce packaging serves as the first point of contact with the consumer. It must be visually appealing and effectively communicate the brand’s values.
- Returns and Handling: Packaging needs to facilitate easy returns and handling of products if necessary, which requires considering resealable options or durable construction.
Futuristic Food Packaging Concept Illustration
The following describes a futuristic food packaging concept.
The illustration depicts a sleek, cylindrical food container constructed from a bio-degradable, plant-based polymer. The container’s surface is a matte, earthy green color, reflecting its sustainable nature. A circular, transparent window is located on the side, displaying the food contents, with an integrated smart label embedded in the packaging material. The smart label is connected to a user’s mobile device, providing information on the product’s freshness, origin, and nutritional information.
The label’s display shows real-time data such as temperature, and also provides a digital recipe recommendation. The container’s top is sealed with a heat-sealed film, also made from a bio-degradable material. The film has a built-in, embedded RFID chip that tracks the product throughout the supply chain, ensuring full traceability. The top portion of the container incorporates a re-sealable mechanism, allowing the consumer to easily open and close the packaging to preserve freshness.
The design emphasizes minimal material usage and a focus on ease of use, reducing waste and providing an enhanced consumer experience. The entire concept represents a blend of sustainability, technology, and convenience.
Conclusive Thoughts
In conclusion, the food packaging factory is a dynamic environment driven by innovation, sustainability, and unwavering attention to quality. From efficient operations and material selection to stringent food safety protocols and eco-friendly practices, these factories are at the forefront of ensuring that food products reach consumers safely and in optimal condition. As the industry continues to evolve, embracing cutting-edge technologies and sustainable practices will be key to its continued success and impact on the global food supply chain.