Autojet systems for food applications represent a pivotal advancement in the food industry, offering precise and efficient solutions for marking, coding, and labeling food products. These systems utilize various technologies, from inkjet to laser marking, to apply critical information directly onto packaging, ensuring traceability, enhancing food safety, and streamlining production processes. This exploration delves into the diverse applications, benefits, and technological advancements associated with autojet systems, providing a comprehensive overview of their impact on the food industry.
From labeling ingredients and nutritional information to applying best-before dates and batch codes, autojet systems are integral to modern food production. They offer significant advantages over traditional methods, including increased speed, reduced waste, and enhanced regulatory compliance. This discussion will cover the types of systems available, their operational costs, and how they contribute to food safety and product authenticity. We will also examine real-world examples and future trends in this evolving field.
Introduction to Autojet Systems in Food Applications
Autojet systems, also known as automated spray systems, represent a significant advancement in food processing and packaging technologies. These systems utilize precisely controlled nozzles and automated processes to apply liquids, coatings, and other substances onto food products. Their implementation offers a high degree of precision and efficiency compared to manual methods, leading to improved product quality and reduced waste.
Core Function and Operation
Autojet systems function by precisely dispensing liquids or coatings onto food products. The process begins with the preparation of the substance to be applied, such as a sauce, glaze, or coating. This substance is then fed into a pump and delivered to a series of spray nozzles. These nozzles are carefully positioned and calibrated to ensure uniform and consistent application.
The automation aspect comes into play through the use of programmable logic controllers (PLCs) and other control systems that manage the flow rate, spray pattern, and nozzle movement. This allows for precise control over the application process, ensuring consistent coverage and minimizing waste.
Primary Benefits of Autojet Systems
The adoption of autojet systems in food processing offers several key advantages. These benefits contribute to enhanced operational efficiency and overall cost reductions.
- Increased Efficiency: Autojet systems significantly increase production speed compared to manual application methods. Automated processes operate continuously and consistently, reducing downtime and improving throughput.
- Reduced Waste: Precise application minimizes the use of coatings and ingredients, leading to less waste. This not only reduces material costs but also contributes to more sustainable practices.
- Improved Product Quality: Uniform application ensures consistent product appearance, taste, and texture. The controlled environment minimizes inconsistencies and enhances overall quality.
- Cost Savings: The combined effect of reduced waste, increased efficiency, and lower labor costs leads to significant cost savings over time.
- Enhanced Food Safety: Automated systems can be designed to minimize human contact, reducing the risk of contamination. They also allow for precise control over the application of sanitizing agents.
Examples of Food Products Processed
Autojet systems are versatile and can be adapted for a wide range of food products. The following are examples of applications.
- Bakery Products: Application of glazes on pastries, spraying of oil on bread and buns, and applying flavorings to cookies. For example, a large bakery chain could use an autojet system to apply a consistent glaze to thousands of donuts per hour, improving both appearance and taste.
- Meat and Poultry: Coating chicken nuggets with batter, applying marinades to poultry, and spraying seasonings onto processed meats. A poultry processing plant might use an autojets system to apply a precise amount of marinade to chicken breasts, resulting in a more flavorful and tender product.
- Snack Foods: Applying seasonings to potato chips, coating nuts with flavorings, and spraying oil on crackers. For example, a snack food manufacturer could use an autojet system to apply a consistent seasoning blend to potato chips, ensuring even distribution and a consistent flavor profile.
- Confectionery: Applying chocolate coatings to candies, spraying a glossy finish on chocolates, and applying flavored syrups to desserts.
- Frozen Foods: Applying sauces to frozen pizzas, coating vegetables with oil, and spraying ice cream cones with chocolate.
Types of Autojet Systems Used in Food Processing
Autojet systems play a crucial role in food processing, providing essential marking, coding, and labeling functionalities. These systems enhance traceability, ensure regulatory compliance, and provide vital information to consumers. The selection of an appropriate autojet system depends on various factors, including the type of food product, desired marking speed, and the specific requirements of the production process.
Inkjet Printing Systems
Inkjet printing is a widely adopted autojet technology in the food industry. This method involves propelling ink droplets onto a substrate to create text, graphics, or codes. The process allows for high-speed printing on various surfaces, including packaging materials and the food itself.
- Continuous Inkjet (CIJ): CIJ systems are characterized by a continuous stream of ink droplets, with a portion of the stream being deflected to form the printed image. The deflected ink is recycled. CIJ systems are suitable for high-speed applications and can print on uneven surfaces. For example, CIJ printers are often used to print best-before dates and batch codes on flexible packaging for snacks and confectionery products.
- Thermal Inkjet (TIJ): TIJ systems use heat to create pressure, which forces ink droplets onto the substrate. These systems offer high resolution and are known for their ease of use and low maintenance. TIJ printers are frequently employed for printing on porous materials, such as cardboard boxes used for packaging dry goods like cereals and pasta.
- Drop-on-Demand (DOD): DOD systems release ink droplets only when required, offering greater control over ink usage. DOD systems are particularly suitable for printing large characters or graphics. These are used for printing on secondary packaging such as cases of bottled water or cartons of frozen pizzas.
Inkjet printing systems offer several advantages:
- High Speed: Inkjet systems can operate at high speeds, making them suitable for fast-paced production lines.
- Versatility: They can print on a wide range of materials, including plastics, paper, and metal.
- Non-Contact Printing: The non-contact nature of inkjet printing prevents damage to delicate food products or packaging.
Disadvantages of inkjet printing include:
- Ink Costs: Ink can be a significant operational expense, especially with high-volume printing.
- Maintenance: Regular maintenance is required to prevent nozzle clogging and ensure optimal print quality.
- Solvent Use: Some inkjet inks contain solvents, which may require special handling and disposal procedures.
Laser Marking Systems, Autojet systems for food applications
Laser marking systems utilize focused beams of light to create permanent marks on food packaging and products. The laser interacts with the material’s surface, causing changes in color or creating a physical alteration, resulting in a readable code or graphic.
- CO2 Lasers: CO2 lasers are commonly used for marking organic materials, such as paper, cardboard, and some plastics. They are effective at creating high-contrast marks. A typical application is the marking of expiration dates on cardboard packaging for baked goods.
- Fiber Lasers: Fiber lasers are more versatile and can mark a wider range of materials, including metals and certain plastics. They are known for their speed and precision. Fiber lasers are frequently used to mark codes on metal cans of food products, ensuring long-lasting and easily readable markings.
Laser marking offers several benefits:
- Permanent Marks: Laser marks are highly durable and resistant to abrasion, moisture, and chemicals.
- High Precision: Laser systems can create intricate designs and small characters with high accuracy.
- Low Maintenance: Laser systems generally require less maintenance compared to inkjet systems.
Disadvantages of laser marking include:
- Initial Cost: Laser systems often have a higher initial investment compared to inkjet systems.
- Material Limitations: Not all materials are suitable for laser marking, and the process can be affected by the material’s color and composition.
- Safety Considerations: Laser systems require safety precautions to protect operators from the laser beam.
Thermal Transfer Printing Systems
Thermal transfer printing uses heat to transfer ink from a ribbon onto the substrate. This method is suitable for printing on flexible packaging and labels.
- Direct Thermal Transfer: Direct thermal transfer involves applying heat to a special thermal paper, which changes color to create the image.
- Thermal Transfer Overprinting (TTO): TTO uses a heated printhead to melt ink from a ribbon onto the packaging material. This is a common method for printing variable data, such as expiration dates and batch codes, on flexible films.
Thermal transfer printing offers the following advantages:
- High Print Quality: Thermal transfer provides sharp, clear print quality, suitable for barcodes and small text.
- Cost-Effectiveness: TTO systems can be cost-effective for short print runs and variable data printing.
- Versatility: Can be used on a wide variety of packaging materials, including films, foils, and labels.
Disadvantages of thermal transfer printing include:
- Speed limitations: Generally slower than inkjet or laser systems.
- Ribbon Costs: The cost of ribbons can add up, especially with high-volume printing.
- Ribbon Waste: Produces waste ribbon, which needs to be managed.
Comparison of Autojet Technologies
The following table summarizes the operational costs, maintenance requirements, and lifespan of the different autojet technologies:
Feature | Inkjet Printing | Laser Marking | Thermal Transfer |
---|---|---|---|
Operational Costs | Moderate (ink costs, solvent disposal) | Moderate to High (electricity, consumables) | Moderate (ribbon costs) |
Maintenance Requirements | Moderate to High (nozzle cleaning, parts replacement) | Low (lens cleaning, occasional component replacement) | Moderate (printhead cleaning, ribbon changes) |
Lifespan | 3-7 years (depending on model and usage) | 5-10+ years (depending on model and usage) | 3-5 years (depending on model and usage) |
Food Applications of Autojet Technology
Autojet systems are integral to modern food processing, offering precise and efficient solutions across various stages of production. Their versatility in applying information directly onto products and packaging streamlines operations, enhances traceability, and ensures compliance with stringent food safety regulations. This technology is crucial for maintaining product integrity and providing consumers with reliable information.
Specific Food Processing Stages Utilizing Autojet Systems
Autojet technology finds extensive application throughout the food processing workflow. Its ability to apply variable data, such as date codes, batch numbers, and ingredient lists, makes it ideal for various tasks.
- Labeling and Coding: Autojet systems are widely used for printing product labels and applying codes directly onto packaging materials. This includes printing variable information like product names, nutritional facts, and barcodes. This ensures that products are properly identified and traceable.
- Date Marking: Date marking is critical for food safety and inventory management. Autojet systems accurately print “best before” or “use by” dates on packaging, ensuring that products are consumed within their optimal timeframe.
- Ingredient Printing: Autojet systems can print ingredient lists and allergen information directly onto packaging. This is especially crucial for consumers with dietary restrictions or allergies, as it provides clear and accurate information about the product’s composition.
- Ingredient Printing: Autojet systems can print ingredient lists and allergen information directly onto packaging. This is especially crucial for consumers with dietary restrictions or allergies, as it provides clear and accurate information about the product’s composition.
- Ingredient Printing: Autojet systems can print ingredient lists and allergen information directly onto packaging. This is especially crucial for consumers with dietary restrictions or allergies, as it provides clear and accurate information about the product’s composition.
Enhancing Product Traceability and Food Safety with Autojet Systems
Autojet systems significantly improve product traceability and food safety through precise data application and integration with tracking systems. This capability is essential for quickly identifying and isolating contaminated products during recalls.
- Real-time Data Application: Autojet systems can apply information in real-time, ensuring that each product is accurately marked with the necessary data. This includes batch numbers, production dates, and even unique identifiers for tracking individual units.
- Integration with Tracking Systems: Autojet systems can be integrated with broader tracking systems, such as Enterprise Resource Planning (ERP) and Warehouse Management Systems (WMS). This allows for seamless data flow throughout the supply chain, from raw material sourcing to final product distribution.
- Enhanced Recall Capabilities: In the event of a food safety issue, autojet systems facilitate rapid and effective recalls. By tracking each product’s origin, production date, and batch number, manufacturers can quickly identify and remove affected products from the market.
- Improved Allergen Management: Autojet systems enable precise labeling of allergen information, reducing the risk of cross-contamination and allergic reactions. They can also be programmed to alert operators to potential errors in allergen labeling.
Integrating an Autojet System into a Typical Food Production Line
The integration of an autojet system into a food production line involves several steps, from initial setup to ongoing maintenance. This integration enhances efficiency and ensures data accuracy.
- Initial Assessment: The first step is to assess the production line’s requirements, including the types of products, packaging materials, and data that need to be applied. This assessment helps determine the appropriate autojet system and its placement within the line.
- System Selection and Installation: Based on the assessment, an autojet system is selected and installed. This involves mounting the printer, connecting it to the power supply and data network, and configuring the printing parameters.
- Integration with Existing Systems: The autojet system is integrated with existing ERP or WMS systems to enable data exchange. This integration ensures that the printing data is synchronized with the production data.
- Testing and Calibration: After installation, the autojet system is tested and calibrated to ensure that it prints accurately and consistently. This includes adjusting the print head, ink flow, and other parameters.
- Training and Operation: Operators are trained on how to use the autojet system, including how to load the packaging materials, select the printing data, and monitor the system’s performance.
- Ongoing Maintenance and Monitoring: Regular maintenance and monitoring are essential to ensure the autojet system’s continued performance. This includes cleaning the print head, replacing ink cartridges, and monitoring the system’s logs for any errors or issues.
Materials Compatibility and Considerations
Selecting the appropriate autojet system for food applications necessitates a thorough understanding of material compatibility. The inks, solvents, and system components must be carefully chosen to ensure they do not interact negatively with the food product or its packaging, maintaining food safety and product integrity. This careful selection process is crucial for preventing contamination, preserving shelf life, and adhering to regulatory standards.
Suitable Food Packaging Materials for Autojet Printing and Marking
The range of food packaging materials compatible with autojet technology is extensive, allowing for versatile marking and coding across various formats. This adaptability supports a wide array of product types and packaging designs.
- Paper-based packaging: This includes cardboard boxes, paper labels, and paperboard cartons. Autojet systems can effectively print on these surfaces, providing information such as product names, expiration dates, and batch codes. The ink’s absorption rate and spread characteristics are key considerations.
- Plastic films and containers: Polyethylene (PE), polypropylene (PP), polyethylene terephthalate (PET), and other plastic materials commonly used for food packaging are compatible with autojet printing. The specific ink formulation is crucial to ensure adhesion and resistance to environmental factors like moisture and temperature fluctuations. Examples include flexible packaging for snacks, rigid containers for dairy products, and shrink-wrap labels.
- Metal cans and containers: Autojet systems are used to mark metal cans and containers, which are commonly employed for canned goods. The inks must be designed to adhere to the metal surface and withstand the canning process, including sterilization temperatures and potential exposure to moisture.
- Glass bottles and jars: Glass packaging can be marked with autojet systems, providing permanent coding solutions for products such as beverages, sauces, and preserves. The ink’s durability and resistance to abrasion are important factors.
- Laminated packaging: This type of packaging combines multiple layers of different materials to provide barrier protection and enhance product presentation. Autojet systems can be used on these surfaces, but the ink must be compatible with all layers and ensure proper adhesion.
Potential Issues and Resolutions with Specific Food Packaging Materials
Certain packaging materials present unique challenges when used with autojet systems. Understanding these potential issues and implementing appropriate solutions is critical for successful marking and coding operations.
Browse the implementation of cub foods in brooklyn park in real-world situations to understand its applications.
- Plastic Packaging: Poor Ink Adhesion
- Issue: The ink may not adhere properly to certain plastic surfaces, leading to smudging, fading, or complete removal of the printed code. This can be due to the plastic’s surface energy or the ink’s formulation.
- Resolution:
- Use inks specifically formulated for the plastic type (e.g., PP, PE, PET).
- Consider pre-treating the packaging surface with a corona treatment or plasma treatment to increase its surface energy and improve ink adhesion.
- Adjust the printing parameters, such as the jetting voltage or the distance between the printhead and the packaging.
- Glass Packaging: Ink Smearing or Poor Durability
- Issue: The ink may smear or rub off easily on glass surfaces, particularly if the glass is exposed to moisture or abrasion. This can lead to illegible codes and potential product recalls.
- Resolution:
- Select inks designed for use on glass, with good adhesion and abrasion resistance.
- Ensure the glass surface is clean and dry before printing.
- Optimize the ink drying process, potentially using heat or UV curing to improve durability.
- Metal Packaging: Corrosion or Ink Degradation
- Issue: The ink may corrode the metal surface or degrade over time, especially in harsh environments or when exposed to certain chemicals. This can affect the code’s legibility and the product’s shelf life.
- Resolution:
- Use inks specifically designed for metal surfaces, with corrosion resistance and chemical stability.
- Apply a protective coating over the printed code to further protect it from environmental factors.
- Conduct thorough testing to assess the ink’s durability under expected storage and handling conditions.
- Paper Packaging: Ink Bleed or Smudging
- Issue: The ink may bleed or smudge on paper-based packaging, especially if the paper is porous or absorbent. This can result in unclear or illegible codes.
- Resolution:
- Choose inks with low viscosity and fast drying times.
- Use paper with a smooth surface to minimize ink absorption.
- Adjust the printing parameters, such as the dot size and jetting speed, to reduce ink spread.
- Laminated Packaging: Ink Migration or Delamination
- Issue: The ink may migrate through the packaging layers or cause delamination, compromising the integrity of the packaging and potentially contaminating the food product.
- Resolution:
- Select inks that are specifically designed for use on laminated packaging and have good barrier properties.
- Test the ink’s compatibility with all packaging layers to ensure that it does not cause delamination or migration.
- Ensure the printing process is optimized to minimize ink penetration and potential issues.
Operational Efficiency and Productivity Gains
Autojet systems are transformative in food processing, offering significant advantages in terms of speed, efficiency, and overall productivity. Their ability to automate critical processes leads to reduced operational costs and improved product quality, making them an increasingly valuable asset in the food industry. This section will delve into specific areas where autojet systems excel, highlighting their impact on operational efficiency and productivity.
Speed and Efficiency Improvements
Autojet systems are designed to streamline food processing operations, significantly enhancing both speed and efficiency. By automating tasks such as spraying, coating, labeling, and packaging, these systems minimize human intervention, leading to faster processing times and reduced labor costs. The precision and consistency of autojet systems also contribute to a more reliable and predictable production cycle.
Reduction of Waste and Errors
The implementation of autojet systems directly correlates with a decrease in waste and errors within food production. The automated nature of these systems ensures precise application of ingredients, coatings, and labeling, minimizing over-application, spills, and mislabeling. This precision leads to a reduction in product spoilage and waste, ultimately contributing to higher profitability and sustainability. For instance, in the packaging of ready-to-eat meals, autojet systems can accurately dispense sauces and dressings, minimizing the risk of incorrect portioning and preventing food waste.
Comparison of Manual Labeling Methods Versus Autojet Systems
The transition from manual labeling to autojet systems represents a significant shift in food production efficiency. Manual methods are often labor-intensive, time-consuming, and prone to human error. Autojet systems, on the other hand, offer speed, accuracy, and cost savings. The following table illustrates a comparative analysis of manual labeling and autojet systems, focusing on throughput and labor costs:
Feature | Manual Labeling | Autojet Labeling | Percentage Improvement | Notes |
---|---|---|---|---|
Throughput (Labels per Minute) | 20-30 | 80-150 | 266% – 400% | Throughput varies depending on label size and complexity, and operator skill. |
Labor Cost (per Hour) | $15-$25 | $5-$10 (Maintenance & Oversight) | 50% – 80% reduction | Includes wages, benefits, and training costs. Autojet systems require fewer personnel. |
Error Rate (Labels Applied Incorrectly) | 5-10% | <1% | 90% – 95% reduction | Based on industry averages. Errors include incorrect label placement, illegible printing, or wrong label applied. |
Material Waste (Labels/Product) | 2-5% | <0.5% | 75% – 90% reduction | Due to misapplication, damaged labels, or over-labeling with manual methods. |
The data presented in the table highlights the substantial advantages of autojet systems in terms of throughput, labor cost reduction, error minimization, and waste reduction. The implementation of autojet systems can therefore yield a significant return on investment through enhanced operational efficiency and productivity gains.
Food Safety and Regulatory Compliance
Autojet systems play a crucial role in ensuring food safety and adherence to stringent regulatory standards within the food processing industry. Their precision and control capabilities directly contribute to minimizing contamination risks and facilitating accurate product information, essential for consumer protection and compliance.
Contribution to Food Safety and Regulatory Standards
Autojet systems enhance food safety by providing precise control over various processing parameters, reducing the potential for contamination and ensuring consistent product quality. This directly supports compliance with food safety regulations, such as those established by the Food and Drug Administration (FDA) in the United States and the European Union (EU) food safety regulations.
- Reduced Cross-Contamination: Autojet systems, particularly in cleaning and sanitization applications, can be programmed to deliver precise amounts of cleaning agents and sanitizers, ensuring effective removal of contaminants and preventing cross-contamination between different food products. This is critical for adhering to regulations concerning allergen control and hygiene standards.
- Precise Ingredient Control: Accurate dispensing of ingredients, including additives and preservatives, is another key area. By precisely controlling the amounts of these substances, autojet systems help manufacturers stay within the limits set by regulatory bodies, thus ensuring consumer safety.
- Traceability and Documentation: Many autojet systems are integrated with data logging capabilities, allowing for the detailed tracking of processing parameters, such as temperature, pressure, and dispensing rates. This information is vital for demonstrating compliance and facilitating rapid product recall in case of any issues. This level of traceability aligns with regulatory requirements for food safety.
Facilitating Accurate Labeling of Food Products
Autojet systems significantly contribute to the accurate and clear labeling of food products, including the provision of nutritional information and allergen warnings. This is crucial for consumer transparency and compliance with labeling regulations.
- Nutritional Information Accuracy: Autojet systems can precisely measure and dispense ingredients, leading to more accurate nutritional information on product labels. This includes controlling the quantities of fats, sugars, and other nutrients, thus allowing for reliable nutritional data.
- Allergen Management: These systems can be programmed to manage ingredient segregation and cleaning protocols to prevent cross-contamination, a crucial factor in preventing allergic reactions. Accurate ingredient control is paramount for including allergen warnings on labels, which helps protect consumers with food sensitivities.
- Batch Coding and Date Marking: Autojet systems are often used for precise printing of batch codes, production dates, and expiration dates on food packaging. This is essential for traceability and regulatory compliance.
Role in Preventing Counterfeiting and Ensuring Product Authenticity
Autojet systems can be integrated with technologies that help prevent food product counterfeiting and ensure authenticity.
- Unique Marking and Coding: The precise dispensing capabilities of autojet systems can be utilized to apply unique codes, identifiers, or even micro-markings on packaging. These features can make it more difficult for counterfeiters to replicate genuine products.
- Tamper-Evident Packaging: Autojet systems can be used to apply tamper-evident seals or coatings to packaging, providing a visual indicator if the product has been opened or tampered with.
- Ingredient Authentication: Autojet systems can be programmed to only accept ingredients that meet specific quality and authenticity criteria, ensuring the use of genuine ingredients.
Maintenance and Troubleshooting
Regular maintenance and effective troubleshooting are crucial for maximizing the lifespan, performance, and reliability of Autojet systems in food applications. A proactive approach to maintenance minimizes downtime, reduces the risk of product contamination, and ensures consistent and high-quality marking and coding. This section Artikels essential maintenance procedures and provides guidance on addressing common operational issues.
Regular Maintenance Procedures
Implementing a consistent maintenance schedule is paramount for the optimal functioning of Autojet systems. Regular upkeep helps prevent breakdowns and ensures the equipment operates efficiently.
- Daily Checks: Perform visual inspections of the system components. This includes checking ink levels, verifying print quality, and inspecting the printhead for any clogs or debris. Ensure that the system’s environment is clean and free from excessive dust or moisture.
- Weekly Cleaning: Clean the printhead nozzles with appropriate solvents, following the manufacturer’s instructions. Wipe down the system’s exterior to remove any accumulated food residue or ink spills. Inspect and clean any air filters to ensure proper airflow.
- Monthly Maintenance: Replace filters as recommended by the manufacturer. Check and tighten any loose connections or fittings. Lubricate moving parts, if applicable, using food-grade lubricants. Review and update the system’s software, if necessary.
- Annual Servicing: Schedule a comprehensive inspection and service by a qualified technician. This may involve calibration of the system, replacement of worn parts, and a thorough assessment of overall performance.
Troubleshooting Common Issues
Even with diligent maintenance, Autojet systems may encounter operational problems. A systematic approach to troubleshooting can quickly identify and resolve these issues.
- Poor Print Quality: This can manifest as faded, distorted, or incomplete prints. Common causes include clogged printheads, incorrect ink viscosity, or improper settings.
Clean the printhead nozzles, adjust ink viscosity settings, and verify print parameters such as jet speed and drop size.
If the issue persists, the printhead may need replacement.
- Ink System Problems: Issues such as low ink pressure or ink leaks can disrupt operation.
Check ink levels, ensure proper connections, and inspect the ink system for leaks. Replace any faulty components, such as filters or pumps.
Verify the ink type used is compatible with the equipment.
- System Errors: Error messages on the system display indicate a problem. Consult the system’s manual for error codes and their corresponding solutions. These may involve hardware failures, software glitches, or sensor malfunctions.
Restart the system, check connections, and contact technical support if the problem persists.
- Connectivity Issues: Problems with network connections or data transfer can hinder operation.
Verify network settings, check cable connections, and ensure that the system is communicating with the network. Update software and drivers if necessary.
Importance of Appropriate Inks and Consumables
The selection and use of appropriate inks and consumables significantly impact the reliability and performance of Autojet systems. Using the wrong ink can lead to system damage, poor print quality, and potential food safety concerns.
- Ink Compatibility: Always use inks specifically designed for Autojet systems and the intended application. Ensure the ink is compatible with the food product, packaging material, and environmental conditions. For instance, inks for direct food contact must meet stringent food safety regulations.
- Consumable Quality: Use high-quality consumables, such as cleaning solvents and make-up fluids, recommended by the system manufacturer. Inferior consumables can damage the system and affect print quality.
- Storage and Handling: Store inks and consumables according to the manufacturer’s instructions, typically in a cool, dry place away from direct sunlight. Handle inks with care to prevent spills and contamination.
- Regulatory Compliance: Ensure that the inks and consumables comply with all relevant food safety regulations, such as those set by the FDA or European Food Safety Authority (EFSA). Proper documentation, including Material Safety Data Sheets (MSDS), is essential.
Advances and Innovations in Autojet Technology for Food: Autojet Systems For Food Applications
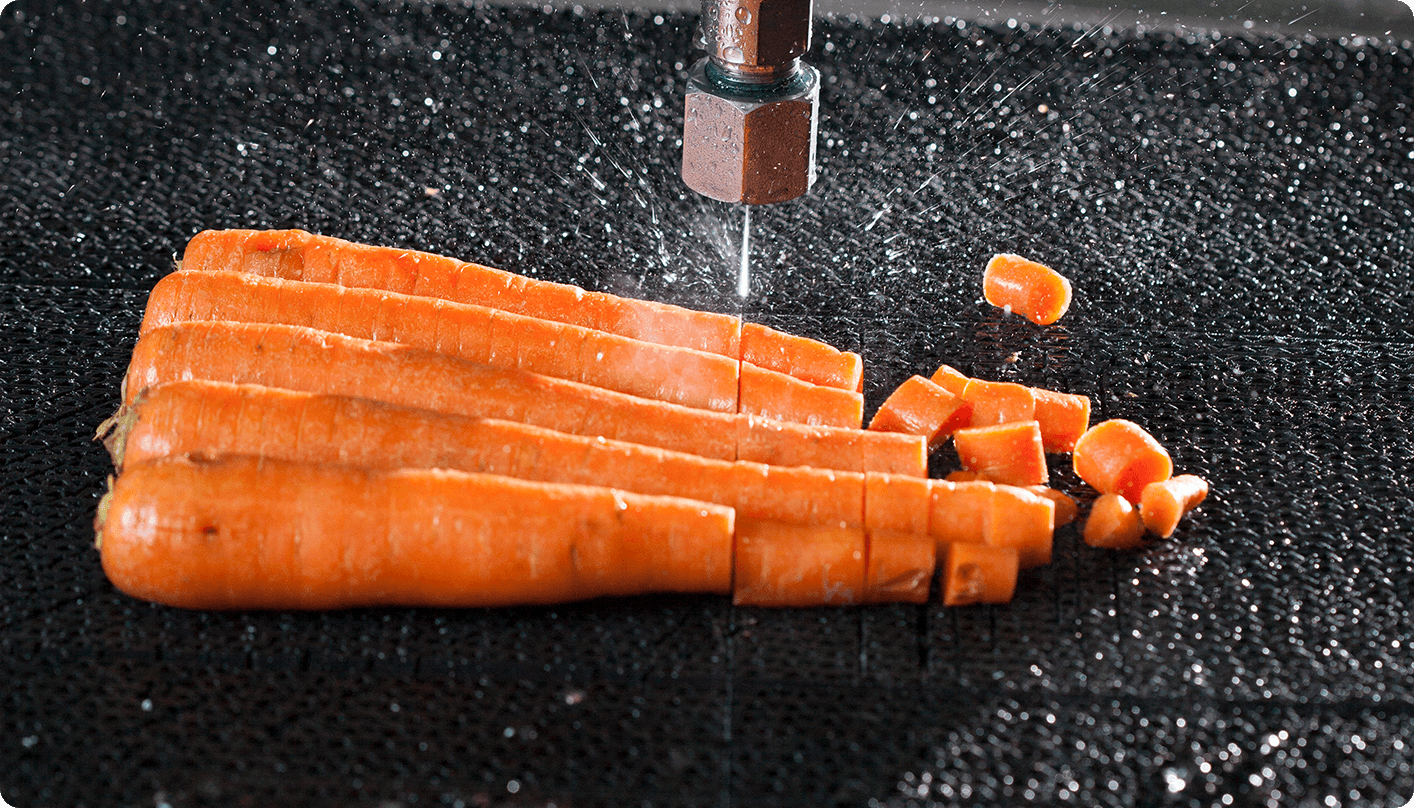
Autojet technology continues to evolve rapidly, driven by the demands of the food industry for increased efficiency, enhanced food safety, and greater customization. These advancements are transforming food processing and packaging, leading to more sustainable and consumer-friendly practices. The focus is on improving printing capabilities and integrating autojet systems with other technologies.
Emerging Trends in Printing Speed, Resolution, and Ink Formulations
The capabilities of autojet printing are constantly being refined, with significant improvements in printing speed, resolution, and the types of inks used. These advancements directly translate to increased production throughput and the ability to print more complex and detailed information.
- Increased Printing Speed: Modern autojet systems can achieve significantly higher printing speeds compared to earlier models. This allows food manufacturers to keep pace with high-volume production demands. For example, some advanced systems can now print at speeds exceeding 1,000 feet per minute, a considerable increase over previous generations. This is particularly crucial for fast-moving product lines, such as snack foods or beverages.
- Enhanced Resolution: Higher resolution printing allows for the inclusion of more detailed graphics, smaller text, and complex barcodes. This enhances product information and brand communication. High-resolution printing enables the printing of intricate designs and small text, essential for ingredient lists, nutritional information, and traceability codes. This also improves the readability of critical information on packaging.
- Advanced Ink Formulations: The development of new ink formulations is a key area of innovation. These inks are specifically designed to meet the stringent requirements of the food industry, including food safety, durability, and compatibility with various packaging materials. This includes:
- Food-Grade Inks: Inks must be compliant with food safety regulations, such as those set by the FDA and the European Food Safety Authority (EFSA).
These inks are specifically formulated to be safe for incidental food contact.
- Durable Inks: Inks need to withstand various environmental conditions, including moisture, temperature fluctuations, and abrasion. This ensures that the printed information remains legible throughout the product’s shelf life.
- Specialized Inks: The development of specialized inks is another area of advancement. This includes inks for printing on specific materials like films, foils, and plastics.
- Food-Grade Inks: Inks must be compliant with food safety regulations, such as those set by the FDA and the European Food Safety Authority (EFSA).
Integration of Autojet Systems with Automation and Data Analytics
The integration of autojet systems with automation and data analytics is creating smart factories, enabling more efficient, data-driven production processes. This integration offers significant benefits in terms of process optimization, quality control, and traceability.
- Automation Integration: Autojet systems are increasingly integrated into automated production lines. This includes integration with conveyor systems, robotic arms, and other automated equipment.
- Automated Labeling and Coding: Autojet systems are used to automate the labeling and coding of products. This can be integrated into automated packaging lines.
- Real-time Data Acquisition: Data from the autojet system, such as print speed, ink usage, and error rates, can be monitored in real time.
- Data Analytics: Data analytics plays a crucial role in optimizing autojet operations. By analyzing data collected from the printing process, manufacturers can identify areas for improvement, predict maintenance needs, and enhance product quality.
- Predictive Maintenance: Data analysis can be used to predict when maintenance is needed, minimizing downtime and improving equipment lifespan.
- Quality Control: Data analytics can be used to identify and address printing defects.
- Track and Trace: Autojet systems can incorporate track-and-trace capabilities, allowing manufacturers to monitor the movement of products throughout the supply chain. This includes the ability to track the origin of ingredients, the production date, and the final destination of each product. This enhances food safety and enables rapid responses to product recalls.
Impact on the Food Industry and the Future of Processing and Packaging
These innovations are fundamentally changing the food industry, creating more efficient, safer, and consumer-focused processes. The future of food processing and packaging will be significantly shaped by these technological advancements.
- Enhanced Food Safety: Autojet technology contributes significantly to food safety through improved traceability, accurate labeling, and the use of food-grade inks. This helps prevent contamination and enables quicker responses to potential food safety issues.
- Increased Customization: Autojet technology enables greater customization of packaging, allowing for personalized products, promotional messages, and variable data printing. This allows for greater consumer engagement.
- Improved Sustainability: The ability to print on demand, reduce waste, and use eco-friendly inks contributes to more sustainable practices. This includes the ability to print variable data on packaging.
- Cost Reduction: Increased efficiency, reduced waste, and optimized processes contribute to cost savings.
- Examples:
- Personalized packaging for cereals: Imagine cereal boxes printed with individual names or custom messages.
- Variable data printing for expiration dates and batch codes: Ensures accurate information and enhances traceability.
- Printing nutritional information and ingredient lists directly on food packaging: Improves legibility and accuracy.
Cost Analysis and Return on Investment
Implementing an autojet system in a food processing facility involves a significant upfront investment. However, the long-term benefits, including increased efficiency, reduced waste, and labor savings, often result in a substantial return on investment (ROI). A thorough cost analysis is crucial to understand the financial implications and make informed decisions.
Initial Investment Costs
The initial investment in an autojet system encompasses several cost components. These costs can vary depending on the complexity of the system, the specific food processing application, and the chosen vendor.
- Equipment Costs: This is the most significant cost, including the autojet printing units, conveyor systems (if not already present), and any required ancillary equipment like vision systems for quality control. The price can range significantly, from a few thousand dollars for a basic system to hundreds of thousands for a highly automated, multi-head system.
- Installation Costs: Professional installation is often required to ensure proper integration with existing production lines. This includes labor costs for technicians and any necessary modifications to the facility infrastructure.
- Software and Integration Costs: Autojet systems require software for programming, data management, and integration with other systems, such as Enterprise Resource Planning (ERP) software. Integration costs can vary depending on the complexity of the existing infrastructure.
- Training Costs: Training for operators and maintenance personnel is essential to ensure efficient and safe operation of the system. Training costs can include vendor-provided training sessions and internal training programs.
- Initial Consumables: The initial purchase of inks, solvents, and other consumables required for the system’s operation.
Calculating Return on Investment (ROI)
Calculating the ROI for an autojet system involves quantifying the benefits and comparing them to the initial and ongoing costs. The primary drivers of ROI include:
- Increased Efficiency: Autojet systems typically operate at higher speeds than manual labeling methods, leading to increased production output. This can be quantified by measuring the increase in units produced per hour.
- Reduced Waste: Autojet systems can minimize waste by accurately applying labels, reducing label misapplication and product spoilage. The reduction in waste can be measured by tracking the decrease in rejected products.
- Labor Savings: Autojet systems automate the labeling process, reducing the need for manual labor. Labor savings can be calculated by comparing the cost of manual labor to the cost of operating the autojet system.
- Reduced Downtime: Advanced autojet systems often incorporate features like predictive maintenance and remote diagnostics, reducing downtime and increasing overall equipment effectiveness (OEE).
- Improved Labeling Accuracy: Autojet systems minimize labeling errors, which can prevent costly recalls and maintain brand reputation.
The ROI can be calculated using the following formula:
ROI = ((Net Profit from Investment) / (Cost of Investment)) – 100
For example, if an autojet system costs $50,000 and generates a net profit of $20,000 per year (after accounting for all operating costs), the ROI would be 40% per year. This ROI is often achieved within 2-3 years depending on the scale of the food processing operation.
Long-Term Operational Cost Comparison
Comparing the long-term operational costs of autojet systems versus traditional labeling methods reveals significant differences. The following table provides a comparative overview:
Cost Category | Autojet Systems | Traditional Labeling Methods | Notes |
---|---|---|---|
Consumables | Ink, solvents, cleaning solutions. Cost is variable depending on usage. | Labels, adhesives, potentially manual label applicators. Costs are directly related to production volume. | Autojet systems can often optimize ink usage, reducing overall consumable costs compared to the constant need for labels. |
Maintenance | Scheduled maintenance, potential for parts replacement. Regular maintenance is crucial for longevity. | Maintenance of manual applicators or other equipment. Less frequent but potentially more expensive repairs. | Proper maintenance is key to the long-term cost-effectiveness of autojet systems. Neglecting maintenance can lead to costly repairs. |
Labor | Reduced labor for labeling. Operators may be required to monitor the system. | Significant labor costs for manual labeling. High labor dependence. | Autojet systems significantly reduce labor requirements, leading to substantial cost savings. |
Downtime | Potential downtime due to system malfunctions. Predictive maintenance can minimize downtime. | Downtime due to equipment failure or label supply issues. | Autojet systems offer increased reliability and faster troubleshooting, minimizing downtime compared to manual methods. |
Case Studies and Real-World Examples
Autojet systems have revolutionized food processing, and understanding their practical application is crucial. This section presents several case studies, illustrating the tangible benefits and challenges encountered when implementing autojet technology. These examples demonstrate how autojet systems contribute to improved efficiency, enhanced product quality, and adherence to stringent industry standards.
Dairy Processing: Automated CIP System for Yogurt Production
This case study focuses on a large-scale dairy processing plant specializing in yogurt production. The plant sought to improve its Clean-in-Place (CIP) system, aiming for better sanitation, reduced downtime, and decreased water and chemical consumption. The existing CIP system relied on manual monitoring and adjustment, leading to inconsistencies in cleaning effectiveness and increased operational costs.
- Challenge: The primary challenge was ensuring consistent and thorough cleaning of complex processing equipment, including tanks, pipelines, and filling machines. Manual monitoring often resulted in incomplete cleaning, potentially compromising product quality and increasing the risk of bacterial contamination. Additionally, the existing system consumed excessive amounts of water and cleaning chemicals.
- Solution: The dairy plant implemented an autojet CIP system equipped with advanced sensors and automated control valves. The system was programmed with specific cleaning cycles tailored to the equipment and product type. Sensors monitored parameters such as temperature, pressure, and conductivity to ensure optimal cleaning performance. The system automatically adjusted cleaning parameters based on real-time data, ensuring consistent and effective cleaning.
- Quantifiable Benefits: The implementation of the autojet CIP system yielded several significant benefits:
- Reduced Downtime: Automated cleaning cycles minimized downtime, allowing for faster changeovers between production runs. The system could complete cleaning cycles in a shorter time frame compared to the manual system.
- Improved Product Quality: Consistent and thorough cleaning reduced the risk of bacterial contamination, resulting in a higher quality product and fewer product recalls.
- Reduced Water and Chemical Consumption: The automated system optimized the use of water and cleaning chemicals, leading to significant cost savings and a reduced environmental footprint. The system’s efficiency meant less water and chemicals were wasted.
- Increased Efficiency: The automated system eliminated the need for manual monitoring and adjustment, freeing up plant personnel for other tasks.
Bakery: Automated Spray Coating for Bread Production
This case study examines a large bakery that produces a variety of bread products. The bakery aimed to improve the consistency and efficiency of its spray coating process, which was critical for achieving the desired texture, appearance, and shelf life of its products. The existing manual spray coating system resulted in inconsistencies in coating application and increased waste.
- Challenge: The manual spray coating process was prone to inconsistencies, leading to variations in product quality and increased waste of coating materials. Achieving uniform coating across all bread products was difficult, resulting in uneven browning, inconsistent texture, and shorter shelf life.
- Solution: The bakery implemented an autojet spray coating system equipped with precision nozzles and automated control mechanisms. The system was programmed to apply the coating with precise control over spray patterns, flow rates, and coating thickness. The system utilized sensors to monitor the speed and position of the bread products, ensuring accurate coating application.
- Quantifiable Benefits: The implementation of the autojet spray coating system resulted in several significant improvements:
- Improved Product Quality: The automated system ensured uniform coating application, resulting in improved product appearance, texture, and shelf life. Products achieved consistent browning and reduced waste.
- Reduced Waste: Precision coating application minimized waste of coating materials, leading to cost savings and a reduced environmental impact.
- Increased Production Throughput: The automated system streamlined the coating process, increasing production throughput and reducing cycle times.
- Reduced Labor Costs: The automated system reduced the need for manual labor, freeing up plant personnel for other tasks.
Meat Processing: Automated Injection System for Marinade Application
This case study highlights the implementation of an autojet injection system in a meat processing plant. The plant aimed to improve the consistency and efficiency of its marinade application process, enhancing product flavor and tenderness. The existing manual injection system led to inconsistencies in marinade distribution and increased waste.
- Challenge: The primary challenge was ensuring consistent and even distribution of marinade throughout the meat products. Manual injection methods were prone to variations in marinade penetration, leading to inconsistent flavor profiles and texture. This also led to increased waste of marinade.
- Solution: The meat processing plant implemented an autojet injection system with automated needle placement and injection control. The system was programmed to inject marinade with precise control over injection pressure, depth, and spacing. The system used sensors to monitor product dimensions and adjust injection parameters accordingly.
- Quantifiable Benefits: The autojet injection system provided several significant benefits:
- Improved Product Quality: Consistent marinade distribution resulted in improved flavor, tenderness, and overall product quality.
- Reduced Waste: Precision injection minimized marinade waste, leading to cost savings.
- Increased Production Efficiency: The automated system increased the speed of the injection process, resulting in higher production throughput.
- Enhanced Food Safety: The automated system improved hygiene by minimizing manual handling and reducing the risk of cross-contamination.
Last Point
In conclusion, autojet systems are indispensable in the food industry, offering a blend of efficiency, safety, and regulatory compliance. The adoption of these technologies leads to improvements in production speed, reduces errors, and facilitates clear and accurate product labeling. As the food industry continues to evolve, embracing the latest innovations in autojet technology will be crucial for businesses aiming to maintain a competitive edge, ensure consumer trust, and adapt to stringent food safety standards.
The ongoing developments in this area suggest a promising future for enhanced food processing and packaging practices.