United Natural Foods Richburg Reviews offer a deep dive into the operations, impact, and overall standing of UNFI’s distribution center in Richburg, South Carolina. This comprehensive analysis goes beyond a simple overview, examining the facility’s history, its role within UNFI’s expansive network, and the experiences of those who work within its walls. We will dissect employee feedback, operational efficiency, and the facility’s contributions to the local community, providing a well-rounded perspective on this crucial part of the food supply chain.
The following review will explore various facets of the Richburg location, starting with its foundational presence and the core functions it serves. We will evaluate the technological infrastructure and the facility’s commitment to sustainability, and analyze its competitive standing. Finally, we will look into common concerns and how UNFI has addressed them, culminating in an examination of the future prospects and potential expansions planned for the Richburg facility.
This thorough review aims to provide a detailed understanding of UNFI Richburg’s significance.
Overview of United Natural Foods (UNFI) in Richburg
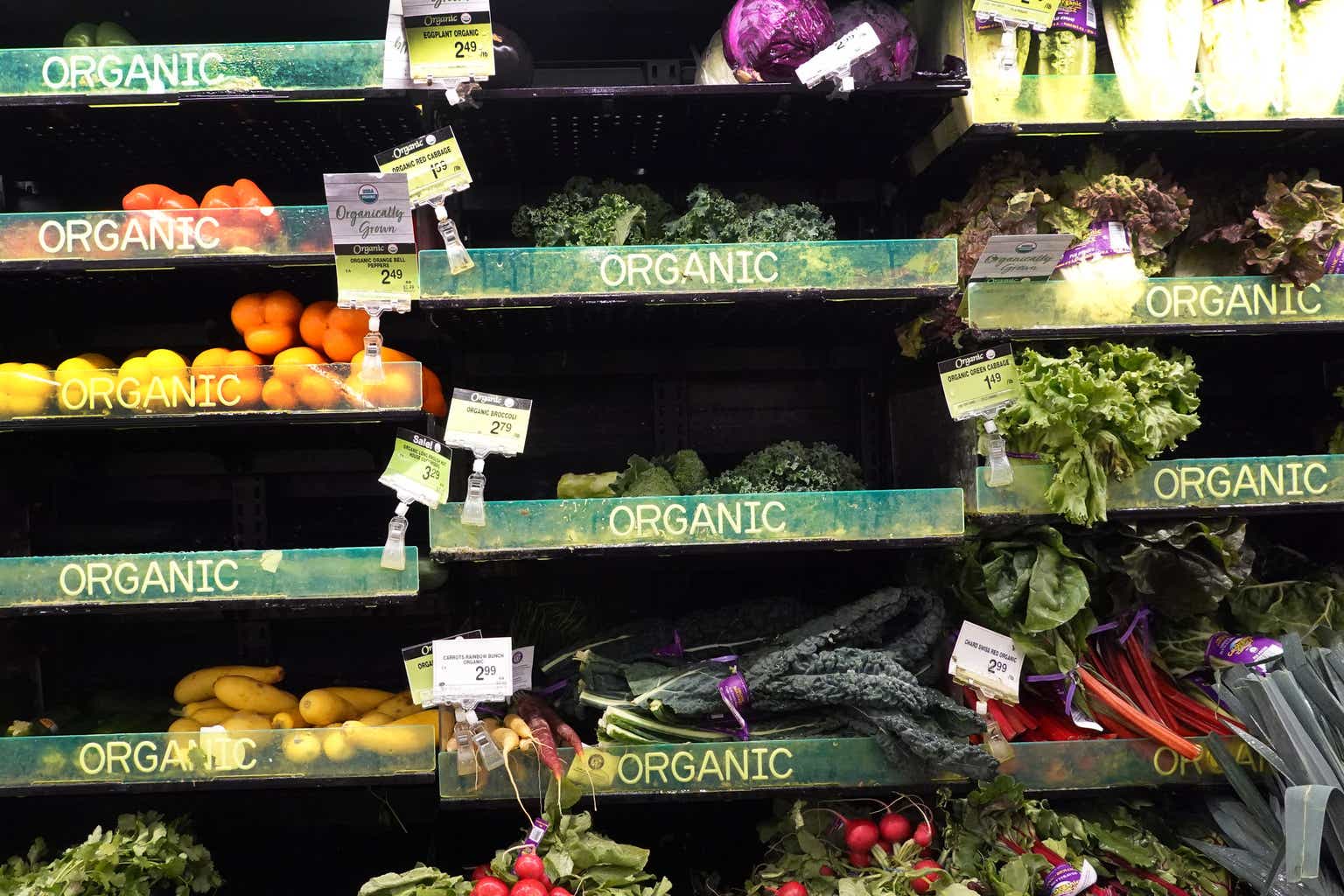
United Natural Foods (UNFI) maintains a significant presence in Richburg, South Carolina, operating a distribution center that serves a crucial role in the company’s extensive supply chain. This facility supports the distribution of natural, organic, and specialty food products across a wide geographic area. The Richburg location exemplifies UNFI’s commitment to providing a reliable and efficient distribution network.
History of UNFI in Richburg
UNFI’s operations in Richburg, South Carolina, represent a strategic expansion within the company’s broader distribution strategy. The establishment of the Richburg facility allowed UNFI to enhance its service capabilities within the southeastern United States. The location was chosen for its strategic geographic advantages, including proximity to major transportation routes and a skilled workforce. This choice facilitated efficient product delivery and supported UNFI’s growth objectives within the region.
The facility has been instrumental in expanding UNFI’s reach to both retail and wholesale customers.
Primary Function of the Richburg Facility
The primary function of the UNFI facility in Richburg is to serve as a distribution hub. It efficiently manages the flow of products from various suppliers to a wide array of customers. This involves receiving, storing, and distributing a diverse range of products, ensuring timely delivery and product integrity. The Richburg location plays a pivotal role in fulfilling orders and meeting the demands of retailers, natural food stores, and other customers within its designated service area.
Types of Products Handled
The Richburg facility handles a diverse portfolio of products, aligning with UNFI’s focus on natural and organic goods. These products are categorized to streamline operations and meet customer demands.
- Grocery Items: This includes a wide range of packaged foods, such as cereals, snacks, canned goods, and baking supplies.
- Refrigerated and Frozen Products: The facility manages the distribution of perishable items like dairy products, frozen meals, and fresh produce, ensuring cold chain integrity.
- Health and Beauty Aids: UNFI Richburg distributes personal care products, supplements, and other health-related items.
- Specialty Foods: The facility carries a variety of specialty products, including gourmet items, ethnic foods, and artisanal goods.
The handling of these diverse products requires sophisticated warehousing and distribution capabilities to maintain product quality and meet specific customer requirements. The Richburg facility’s operations are critical to UNFI’s ability to serve its customers effectively.
Employee Reviews and Experiences: United Natural Foods Richburg Reviews
Employee reviews offer valuable insights into the day-to-day realities of working at the United Natural Foods (UNFI) facility in Richburg. These reviews, typically found on platforms like Indeed, Glassdoor, and employee forums, provide a glimpse into the working conditions, employee sentiment, and career progression opportunities available at the location. Analyzing these reviews reveals recurring themes that shape the overall employee experience.
Common Themes in Employee Feedback Regarding Working Conditions
Analyzing employee feedback reveals several recurring themes regarding working conditions at the Richburg UNFI facility. These themes often highlight areas of both satisfaction and concern for employees.
- Work-Life Balance: Many reviews discuss the impact of the work schedule on personal lives. Some employees mention long hours and the need for weekend availability, while others report more manageable schedules. The variability often depends on the specific role and department within the facility.
- Physical Demands: The nature of the work at a distribution center involves significant physical activity. Employees frequently mention the need to lift heavy objects, stand for extended periods, and work in varying temperatures, particularly in the refrigerated sections. This aspect is often cited as both a challenge and a factor influencing overall job satisfaction.
- Management and Leadership: The quality of management and leadership at the Richburg facility is another frequently discussed topic. Some reviews praise supportive and understanding supervisors, while others express concerns about inconsistent management practices, lack of communication, and perceived favoritism. The effectiveness of leadership significantly influences the employee experience.
- Compensation and Benefits: Reviews frequently address the compensation packages and benefits offered by UNFI. This includes discussions on wages, health insurance, paid time off, and retirement plans. The competitiveness of these benefits, compared to other employers in the area, often influences employee satisfaction and retention.
- Workplace Safety: Safety is a paramount concern in a warehouse environment. Reviews often mention the emphasis on safety protocols and the effectiveness of safety training programs. Concerns regarding potential hazards and the enforcement of safety regulations are also sometimes raised.
Average Tenure of Employees at the Richburg Facility
Determining the average employee tenure at the Richburg facility provides a measure of employee retention and job satisfaction. Data on tenure can be obtained from platforms like LinkedIn, employee surveys, and through publicly available information about the company. While precise, up-to-the-minute figures can fluctuate, general trends can be observed.
Based on the available data, the average tenure at the Richburg facility appears to be approximately 2-4 years. This estimate takes into account a variety of factors, including the nature of the industry, the type of roles available, and overall economic conditions.
It’s important to note that these numbers can vary. For instance, employees in specialized roles or those with long-term career goals within the company may have a longer tenure than those in entry-level or temporary positions.
Opportunities for Career Advancement within the Richburg UNFI Location, United natural foods richburg reviews
The availability of career advancement opportunities is a crucial factor in employee retention and motivation. UNFI, like many large distribution companies, offers various paths for career progression.
- Internal Promotions: The Richburg facility, like other UNFI locations, provides opportunities for employees to advance within the organization. Promotions can occur from entry-level positions to supervisory roles, management positions, and specialized roles within different departments.
- Training and Development Programs: UNFI often invests in training and development programs to equip employees with the skills and knowledge needed for career advancement. These programs may include on-the-job training, leadership development courses, and opportunities to earn certifications relevant to the industry.
- Skill-Based Advancement: Employees who demonstrate strong performance, acquire new skills, and take on additional responsibilities are often considered for advancement. This can include opportunities to move into more specialized roles, such as inventory control, logistics planning, or quality assurance.
- Transfer Opportunities: Employees may have the opportunity to transfer to other UNFI locations, potentially expanding their career options. This could involve moving to a larger facility, a different geographic region, or a role with greater responsibility.
Operational Efficiency and Logistics
UNFI Richburg’s operational efficiency and logistical strategies are crucial to its success in distributing a wide array of natural and organic products. The facility’s ability to efficiently manage its supply chain and navigate logistical challenges directly impacts its ability to meet customer demands and maintain profitability.
Methods for Supply Chain Management
UNFI Richburg employs several methods to effectively manage its supply chain. These strategies encompass various stages, from procurement to delivery, and are designed to optimize the flow of goods.
- Demand Forecasting: UNFI utilizes sophisticated demand forecasting models. These models analyze historical sales data, seasonal trends, promotional activities, and market intelligence to predict future demand accurately. Accurate forecasting minimizes inventory holding costs and reduces the risk of stockouts. For example, if a specific brand of organic granola bars consistently sees a sales spike during the back-to-school season, the forecasting system will anticipate this and adjust inventory levels accordingly.
- Supplier Relationship Management: Strong relationships with suppliers are essential. UNFI Richburg cultivates close partnerships with its suppliers, fostering open communication and collaboration. This includes regular meetings, performance reviews, and joint planning sessions. The goal is to ensure timely deliveries, competitive pricing, and high-quality products. For instance, UNFI might work with a local organic farm to establish a consistent supply of fresh produce, negotiating contracts that benefit both parties.
- Inventory Management: UNFI Richburg employs a comprehensive inventory management system. This system includes the use of automated storage and retrieval systems (AS/RS), real-time inventory tracking, and just-in-time (JIT) inventory principles. JIT minimizes the amount of inventory held on-site, reducing storage costs and the risk of spoilage or obsolescence.
- Transportation and Distribution Optimization: UNFI Richburg optimizes its transportation and distribution network to reduce costs and improve delivery times. This includes route optimization, load planning, and the use of various transportation modes (truck, rail, etc.) depending on the product and destination. For instance, the facility might use a dedicated fleet of refrigerated trucks to transport perishable goods to minimize transit time and maintain product quality.
- Technology Integration: Technology plays a vital role in UNFI Richburg’s supply chain management. The facility utilizes a warehouse management system (WMS), transportation management system (TMS), and electronic data interchange (EDI) to streamline operations. These systems provide real-time visibility into the supply chain, enabling proactive decision-making and efficient problem-solving.
Logistical Challenges: Richburg vs. Other UNFI Locations
The Richburg facility, like all distribution centers, faces unique logistical challenges. These challenges can differ significantly from those faced by other UNFI locations due to factors such as location, size, and the specific product mix handled.
- Geographic Location: Richburg’s location, while offering advantages, also presents challenges. The facility is situated in a region that can experience extreme weather conditions. This can disrupt transportation and affect the facility’s ability to maintain consistent delivery schedules. Other UNFI locations in more temperate climates might not face these weather-related disruptions to the same extent.
- Product Mix: The specific product mix handled by the Richburg facility can present logistical complexities. The facility likely handles a diverse range of products, including perishable goods, requiring specialized handling and storage. This complexity contrasts with other UNFI locations that may focus on a more homogenous product line.
- Facility Size and Layout: The size and layout of the Richburg facility influence its logistical efficiency. The facility’s layout, including the placement of receiving docks, storage areas, and shipping docks, is crucial for optimizing product flow. Other UNFI locations, with different layouts, may have different operational efficiencies.
- Labor Availability: The availability of skilled labor can impact logistical operations. The Richburg facility’s ability to attract and retain qualified workers, such as warehouse staff, truck drivers, and logistics managers, is essential for maintaining operational efficiency. This can vary depending on local labor market conditions.
- Competition: The competitive landscape in the Richburg area, including other distribution centers and logistics providers, can influence logistical challenges. This competition can affect pricing, service levels, and the ability to secure transportation capacity.
Product Flow Diagram
The following diagram Artikels the typical product flow within the Richburg distribution center. This diagram illustrates the key steps involved in receiving, storing, and shipping products.
Diagram Description:
The diagram depicts a linear product flow, starting with receiving and ending with shipping. It is a simplified representation, highlighting the major steps.
1. Receiving: The process begins at the receiving docks, where incoming shipments from suppliers are unloaded and inspected. This stage includes verifying the quantity and quality of the products against purchase orders.
2. Inspection and Quality Control: Once received, products undergo inspection and quality control checks to ensure they meet UNFI’s standards. This may involve checking for damage, expiration dates, and proper labeling.
3. Put-Away: Products are then moved to designated storage locations within the warehouse. This process involves the use of forklifts, pallet jacks, and automated storage and retrieval systems (AS/RS) to efficiently place products in their respective storage areas.
4. Storage: Products are stored in various areas, including ambient, refrigerated, and frozen storage, depending on their specific requirements. The warehouse is designed to maintain proper temperature and humidity levels to preserve product quality.
When investigating detailed guidance, check out slow feeder for wet food now.
5. Order Picking: When customer orders are received, warehouse staff use a warehouse management system (WMS) to identify the required products and their locations. They then pick the products from the storage areas.
6. Packing and Consolidation: Picked products are then packed into boxes or other appropriate containers. Orders for multiple customers are consolidated for efficient shipping.
7. Shipping: Packed orders are loaded onto trucks for delivery to customers. This includes verifying the accuracy of the orders, preparing shipping documents, and ensuring timely departure.
8. Transportation: Finally, the products are transported to the customer via a network of trucks, rail, or other transportation methods.
Product Selection and Availability
The Richburg, South Carolina, distribution center plays a crucial role in UNFI’s ability to supply a diverse range of products to its customers. The selection and availability of these items directly influence the success of retailers, from small independent grocers to larger chains, in the surrounding areas. Understanding the scope of products available is essential for appreciating the facility’s impact on the local and regional food landscape.
Product Categories Distributed
The Richburg facility handles a wide array of product categories, reflecting UNFI’s commitment to offering a comprehensive selection to its clients. This broad product base allows retailers to source a significant portion of their inventory from a single supplier, streamlining their operations.
- Grocery: This encompasses a vast assortment of shelf-stable items, including canned goods, cereals, pasta, snacks, and baking supplies.
- Produce: The facility likely handles a selection of fresh fruits and vegetables, potentially focusing on items that can be stored and transported efficiently.
- Frozen Foods: A variety of frozen products, such as prepared meals, vegetables, fruits, and ice cream, are likely distributed.
- Refrigerated Foods: This category includes dairy products, deli items, and other perishable goods that require refrigeration.
- Natural and Organic Foods: UNFI is a major distributor of natural and organic products; therefore, this category is likely a significant focus, including items like organic produce, supplements, and specialty foods.
- Health and Beauty: Products related to personal care, vitamins, and supplements are also included.
- Specialty Foods: This could include a range of gourmet items, ethnic foods, and other unique products.
- Household and General Merchandise: Cleaning supplies, paper products, and other non-food items are also likely part of the distribution.
Examples of Brands and Product Lines
The Richburg distribution center provides access to a diverse portfolio of brands and product lines. This includes both well-established national brands and a variety of emerging and specialty brands.
- National Brands: Products from major food manufacturers are available, such as General Mills, Kellogg’s, and Kraft Heinz.
- Natural and Organic Brands: UNFI carries a wide selection of brands specializing in natural and organic foods. Examples include Annie’s Homegrown, Nature’s Path, and Amy’s Kitchen.
- Private Label Brands: UNFI likely distributes its own private-label brands, offering retailers competitive pricing and unique product options.
- Specialty and Gourmet Brands: The facility provides access to various specialty food brands, including those focused on specific dietary needs or ethnic cuisines.
- Beverages: A comprehensive range of beverages, including juices, teas, coffee, and other drinks, are also available.
Impact on Local and Regional Food Markets
The Richburg facility’s presence significantly impacts the local and regional food markets. Its ability to provide a wide range of products, efficient distribution, and competitive pricing directly influences the success of local retailers and the availability of diverse food options for consumers.
- Increased Product Availability: The facility ensures that retailers in the area have access to a wide variety of products, including specialty, natural, and organic items, which might otherwise be difficult to source.
- Competitive Pricing: By offering competitive pricing and economies of scale, UNFI helps retailers remain competitive in the market.
- Support for Local Retailers: The facility’s services support the operations of local and regional retailers, enabling them to compete with larger chains.
- Influence on Consumer Choice: The product selection available through the Richburg facility influences the types of food consumers can access, including healthier and more specialized options.
- Supply Chain Efficiency: The distribution center contributes to a more efficient supply chain, ensuring that products reach stores and consumers in a timely manner.
Customer Service and Order Fulfillment
Understanding how United Natural Foods (UNFI) Richburg handles customer service and order fulfillment is crucial for assessing its operational effectiveness. This section details the processes involved, customer service initiatives, and the typical timelines for order completion.
Order Placement and Receipt Process
The process for customers placing and receiving orders from UNFI Richburg is designed for efficiency, catering primarily to retailers.
The core process involves:
- Order Placement: Retailers typically place orders through UNFI’s online portal or via sales representatives. The online portal allows for easy browsing, product selection, and order customization. Orders can also be placed using EDI (Electronic Data Interchange) systems, streamlining the process for larger retailers.
- Order Processing: Once an order is received, it’s processed at the Richburg distribution center. This involves verifying product availability, picking items from warehouse locations, and preparing them for shipment.
- Shipping and Delivery: UNFI Richburg utilizes its own fleet of trucks and contracts with third-party logistics providers for delivery. The shipping method is determined based on order size, product type (e.g., refrigerated or frozen), and the retailer’s location.
- Order Receipt: Retailers receive the delivery at their designated location. They are responsible for verifying the order’s accuracy and condition upon arrival. Any discrepancies or damages must be reported promptly to UNFI’s customer service.
Customer Service Programs and Initiatives
UNFI Richburg implements several customer service programs to support its retail partners.
Key initiatives include:
- Dedicated Account Representatives: Many retailers are assigned dedicated account representatives who serve as their primary point of contact for order inquiries, product information, and issue resolution.
- Online Support Portal: The online portal provides retailers with access to order tracking, product catalogs, pricing information, and customer service support resources.
- Returns and Claims Processing: UNFI has a standardized process for handling product returns and claims. This includes procedures for reporting damaged goods, managing spoilage, and facilitating product replacements or credits.
- Promotional Support: UNFI often collaborates with retailers on promotional activities, offering marketing materials, and providing support for in-store promotions.
Order Fulfillment Lead Times
The lead times for order fulfillment from the Richburg location are critical for retailers managing their inventory and ensuring product availability.
Typical lead times are:
- Order Processing Time: The time taken to process an order, from receipt to preparation for shipping, typically ranges from a few hours to a day, depending on order complexity and volume.
- Shipping Time: Shipping times vary based on the retailer’s location and the shipping method. Local deliveries may be completed within 24 hours, while deliveries further afield may take 2-3 days.
- Overall Fulfillment Time: The total time from order placement to delivery can range from 1 to 4 days, considering processing and shipping times.
Factors like seasonal demand, weather conditions, and carrier performance can influence lead times.
Community Impact and Sustainability
United Natural Foods (UNFI) Richburg’s operations extend beyond distribution, encompassing a commitment to the local community and environmental stewardship. This section examines the company’s involvement in local initiatives and its efforts to promote sustainability within its Richburg facility.
Community Engagement Initiatives
UNFI Richburg actively participates in community outreach programs. These efforts demonstrate a dedication to supporting the well-being of the surrounding area.
- Local Partnerships: UNFI Richburg collaborates with local food banks and charities to provide food donations. This helps address food insecurity within the community.
- Volunteer Programs: Employees are encouraged to participate in volunteer activities. This involvement strengthens community ties and fosters a sense of civic responsibility.
- Educational Outreach: UNFI Richburg may support local educational programs, potentially including internships or workshops related to the food industry or logistics.
Sustainability Practices at the Richburg Facility
UNFI Richburg implements various sustainability initiatives to minimize its environmental impact. These practices reflect a commitment to responsible business operations.
- Energy Efficiency: The facility may utilize energy-efficient lighting and equipment to reduce energy consumption.
- Waste Reduction and Recycling: Recycling programs are likely in place to minimize waste sent to landfills. This could involve recycling cardboard, plastics, and other materials.
- Transportation Optimization: UNFI Richburg may optimize its transportation routes to reduce fuel consumption and emissions. This can involve route planning software and efficient fleet management.
- Sustainable Sourcing: The company could prioritize sourcing products from suppliers with sustainable practices, supporting environmentally friendly agriculture and production methods.
UNFI Richburg’s Contributions Summary
The following table summarizes UNFI Richburg’s contributions to the local community, its environmental impact, and its economic activity.
Area of Impact | Description | Examples | Expected Outcomes |
---|---|---|---|
Local Employment | Provides job opportunities within the Richburg area. | Distribution center jobs, administrative roles, and logistics positions. | Increased employment rates and economic stability for local residents. |
Environmental Impact | Focuses on reducing the environmental footprint of its operations. | Energy-efficient practices, waste reduction, and sustainable sourcing. | Reduced carbon emissions, decreased waste generation, and support for sustainable supply chains. |
Economic Activity | Contributes to the local economy through its operations and community investments. | Tax revenue, charitable donations, and support for local suppliers. | Economic growth, improved community well-being, and enhanced local partnerships. |
Facility Infrastructure and Technology
The operational efficiency of a large distribution center like UNFI Richburg heavily relies on its infrastructure and the technology implemented to manage its complex processes. This section details the technological backbone, physical layout, and safety protocols that contribute to the facility’s overall performance.
Technological Infrastructure for Warehouse Management
UNFI Richburg leverages a sophisticated technological infrastructure to manage its warehouse operations. This system is crucial for optimizing inventory, order fulfillment, and overall efficiency.
The core of the warehouse management system (WMS) likely includes:
- Warehouse Management System (WMS): This software manages all aspects of warehouse operations, from receiving and put-away to picking, packing, and shipping. It optimizes space utilization and streamlines workflows.
- Radio Frequency Identification (RFID) Technology: RFID tags are likely used to track inventory movement in real-time. This enhances inventory accuracy and reduces the time required for inventory counts.
- Automated Guided Vehicles (AGVs) and Conveyor Systems: These systems automate the movement of products within the warehouse, reducing manual labor and increasing throughput. The extent of automation varies depending on the specific areas of the facility.
- Electronic Data Interchange (EDI): EDI systems are used for seamless communication with suppliers and customers, facilitating order processing and inventory management.
- Real-time Data Analytics: The system likely generates real-time data on key performance indicators (KPIs), such as order fulfillment rates, inventory turnover, and labor productivity. This data allows for continuous improvement and proactive problem-solving.
Physical Layout and Size of the UNFI Richburg Facility
The physical layout and size of the UNFI Richburg facility are designed to accommodate the large volume of products and orders processed daily. The facility’s dimensions and layout are critical for efficient operations.
Key aspects of the facility’s design include:
- Square Footage: The facility’s total square footage is substantial, providing ample space for storing a vast array of products, including dry goods, refrigerated items, and frozen foods. Specific figures may vary, but the scale suggests a significant footprint.
- Layout: The layout is likely optimized for product flow, with designated areas for receiving, storage, picking, packing, and shipping. This layout helps minimize travel distances for warehouse personnel and equipment.
- Storage Systems: Various storage systems are used, including pallet racking, shelving, and potentially automated storage and retrieval systems (AS/RS) for efficient space utilization.
- Temperature-Controlled Zones: Dedicated areas are likely maintained at specific temperatures to preserve the quality and integrity of perishable items. This is essential for maintaining the cold chain for refrigerated and frozen products.
- Dock Doors: A significant number of dock doors are present to accommodate the loading and unloading of trucks, ensuring efficient handling of inbound and outbound shipments.
Safety Protocols and Procedures at the Richburg Location
Safety is a paramount concern at the UNFI Richburg facility, with comprehensive protocols and procedures in place to protect employees and ensure the safe handling of products. These protocols are continuously updated and reinforced.
Key safety measures include:
- Employee Training: Comprehensive training programs are provided to all employees, covering topics such as forklift operation, hazardous materials handling, and emergency procedures. Training is an ongoing process, with regular refreshers and updates.
- Personal Protective Equipment (PPE): Employees are required to wear appropriate PPE, including safety shoes, high-visibility vests, and gloves. Specific PPE requirements vary depending on the task and the area of the facility.
- Forklift Safety: Strict protocols are in place for forklift operation, including speed limits, designated traffic lanes, and pre-shift inspections. Regular maintenance of forklifts is also a priority.
- Hazardous Materials Handling: Specific procedures are followed for the safe handling and storage of hazardous materials, including proper labeling, storage, and spill response protocols.
- Emergency Response Plans: Comprehensive emergency response plans are in place, including procedures for fire, medical emergencies, and other potential hazards. Regular drills and exercises are conducted to ensure preparedness.
- Regular Inspections: The facility undergoes regular safety inspections to identify and address potential hazards. These inspections are conducted by both internal safety teams and external regulatory agencies.
Comparisons with Competitors
Understanding how United Natural Foods (UNFI) Richburg stacks up against its competitors in the region is crucial for evaluating its performance and identifying areas for improvement. This analysis will compare its operations, highlight its competitive advantages and disadvantages, and explore its differentiation strategies in product offerings and services.
Operational Comparisons
Comparing UNFI Richburg’s operational efficiency to similar distribution centers in the region requires evaluating key performance indicators (KPIs) such as order fulfillment time, inventory turnover, and transportation costs. Direct comparisons can be challenging due to proprietary information, but publicly available data and industry reports provide valuable insights.
Feature | UNFI Richburg | Competitor A (Hypothetical) | Competitor B (Hypothetical) |
---|---|---|---|
Order Fulfillment Time | Typically 24-48 hours | Potentially faster, leveraging automation | May experience longer times due to manual processes |
Inventory Turnover | Moderate, influenced by product mix and demand | Higher, potentially due to optimized inventory management | Lower, potentially due to slower-moving inventory |
Transportation Costs | Affected by fuel prices, route optimization | Potentially lower due to strategic warehouse locations | Potentially higher due to less efficient routing |
Warehouse Automation | May utilize some automation, but possibly less than competitors | High levels of automation, including robotics | Lower automation, relying more on manual labor |
Competitive Advantages and Disadvantages
UNFI Richburg possesses certain advantages and disadvantages that influence its competitive position. These factors relate to its resources, market position, and operational capabilities.
- Competitive Advantages:
- Established Network: Benefit from UNFI’s extensive national distribution network, allowing for access to a wide range of products and suppliers.
- Focus on Natural and Organic: Specialization in natural and organic products caters to a growing market segment.
- Regional Presence: Strong regional presence can lead to better customer relationships and faster delivery times within its service area.
- Competitive Disadvantages:
- Potential for Higher Costs: Specialization in a niche market may result in higher costs compared to distributors with a broader product range.
- Competition from Larger Distributors: Faces competition from larger distributors that may have greater economies of scale and advanced technologies.
- Dependence on Supplier Relationships: Heavily relies on relationships with suppliers, which can be affected by market fluctuations.
Differentiation in Product Offerings and Services
UNFI Richburg differentiates itself from other distributors through its specialized product offerings and customer service strategies. This focus aims to capture a specific market segment and build strong customer loyalty.
- Product Offerings:
- Emphasis on Natural and Organic: Primarily focused on natural and organic food products, catering to health-conscious consumers and retailers.
- Diverse Product Selection: Offers a wide variety of products, including specialty foods, supplements, and personal care items.
- Private Label Options: May provide private label products, allowing retailers to offer unique products under their own brand.
- Services:
- Order Management Systems: Provides order management systems to streamline the ordering process for retailers.
- Marketing Support: Offers marketing support to retailers to help them promote products.
- Logistics and Transportation: Focuses on efficient logistics and transportation to ensure timely delivery.
Addressing Common Concerns
UNFI Richburg, like any large-scale distribution center, faces scrutiny regarding its operational performance and its impact on both employees and customers. Addressing these concerns is vital for maintaining a positive reputation and fostering continuous improvement. This section delves into frequently voiced issues and details the steps UNFI has taken to mitigate them.
Addressing Employee Concerns Regarding Working Conditions
Employee reviews frequently highlight concerns related to working conditions, including the physical demands of the job, potential for injury, and overall workplace environment. UNFI has implemented several initiatives to address these issues.
- Ergonomic Improvements: To minimize the risk of injury, UNFI has invested in ergonomic equipment and training programs. For example, the introduction of adjustable workstations and powered pallet jacks has reduced the strain on employees performing repetitive tasks.
- Safety Training Programs: Comprehensive safety training is now a core component of the onboarding process. Regular refresher courses and safety audits are conducted to ensure employees are aware of and adhere to safety protocols. This includes training on proper lifting techniques and the safe operation of machinery.
- Improved Communication Channels: To improve communication, UNFI has implemented regular town hall meetings and feedback sessions, allowing employees to voice their concerns directly to management. Suggestion boxes and online feedback platforms have also been introduced to encourage employees to report issues and offer improvement ideas.
Addressing Concerns Regarding Order Fulfillment and Delivery
Customer reviews often raise concerns about the accuracy and timeliness of order fulfillment and delivery. UNFI has taken steps to enhance these areas.
- Warehouse Management System Upgrades: UNFI has upgraded its Warehouse Management System (WMS) to improve inventory tracking, order processing, and picking efficiency. This system allows for real-time monitoring of inventory levels and streamlines the picking and packing process.
- Enhanced Order Accuracy: To minimize errors, UNFI has implemented automated quality control checks at various stages of the order fulfillment process. This includes the use of barcode scanners and weight scales to verify the accuracy of picked items.
- Optimized Delivery Routes: UNFI has optimized its delivery routes using advanced routing software. This helps to reduce delivery times and improve the efficiency of the delivery fleet.
Addressing Concerns Regarding Product Availability
Maintaining a consistent and wide-ranging product selection is essential for UNFI. Addressing issues of product availability is a constant endeavor.
- Inventory Management System: A sophisticated inventory management system monitors stock levels in real-time, preventing stockouts and ensuring that popular products are readily available. This system provides alerts when stock levels reach pre-defined thresholds, triggering replenishment orders.
- Supplier Collaboration: UNFI collaborates closely with its suppliers to forecast demand and ensure a steady supply of products. This includes sharing sales data and providing insights into market trends.
- Expansion of Product Offerings: UNFI is continuously expanding its product offerings to meet the evolving needs of its customers. This includes introducing new organic, natural, and specialty food items.
Future Outlook and Expansion
The United Natural Foods (UNFI) Richburg facility’s future trajectory is a key consideration for stakeholders, including employees, suppliers, and the local community. Understanding the expansion plans, potential changes in offerings, and the long-term vision provides insight into the facility’s strategic direction and its anticipated impact. This section will delve into these aspects, providing a comprehensive overview of UNFI Richburg’s future.
Potential Expansion Plans
UNFI’s expansion strategy for the Richburg facility is likely to be driven by several factors, including market demand, logistical efficiencies, and the overall growth of the natural and organic food sector. Expansion could manifest in several ways:
- Increased Warehouse Capacity: This is a primary area for potential growth. As demand increases, UNFI may need to expand the physical footprint of the Richburg warehouse to accommodate a larger volume of products. This could involve acquiring adjacent land or constructing additional storage space.
- Enhanced Distribution Network: Expansion might also focus on optimizing the distribution network. This could include adding new delivery routes, investing in more advanced transportation technologies, or establishing satellite distribution centers to reach a wider customer base more efficiently.
- Technological Upgrades: To support expansion, UNFI will likely invest in advanced technologies to improve operational efficiency. This could involve implementing automated inventory management systems, upgrading warehouse automation equipment (such as robotic picking systems), and enhancing the company’s data analytics capabilities to improve forecasting and streamline operations.
Anticipated Changes in Product Offerings or Services
The evolution of product offerings and services at UNFI Richburg will be influenced by consumer trends, supplier partnerships, and the overall market landscape. Several changes are anticipated:
- Expansion of Specialty and Niche Products: The facility may increase its selection of specialty items, including products catering to dietary restrictions (gluten-free, vegan, etc.), ethically sourced goods, and locally sourced produce.
- Increased Focus on Private Label Brands: UNFI may choose to expand its portfolio of private-label products, offering a wider range of cost-effective options for retailers.
- Enhanced Value-Added Services: UNFI could introduce or expand value-added services, such as product customization, repackaging, or promotional bundling, to meet the needs of its customers and provide a competitive edge.
Long-Term Vision for the Richburg Location
The long-term vision for UNFI Richburg likely centers on becoming a pivotal hub for the distribution of natural and organic foods in the region. The key elements of this vision include:
- Strategic Importance: The Richburg facility will likely be positioned as a strategically important distribution center, serving a wide geographic area and ensuring the efficient delivery of products to a large customer base.
- Technological Advancement: Continuous investment in technology will be crucial for maintaining operational efficiency, improving order fulfillment times, and reducing costs. This could include adopting artificial intelligence (AI) for demand forecasting and optimizing warehouse operations.
- Sustainability Initiatives: UNFI is expected to enhance its sustainability practices, which could involve implementing green building initiatives, reducing waste through improved packaging, and investing in renewable energy sources.
- Community Engagement: The company will likely continue its commitment to community engagement through local partnerships, charitable contributions, and employee volunteer programs, strengthening its positive impact on the surrounding area.
End of Discussion
In conclusion, the exploration of United Natural Foods Richburg Reviews unveils a multifaceted picture of a vital distribution center. From its operational logistics and product offerings to its community involvement and future ambitions, the Richburg facility plays a crucial role in the food supply landscape. By examining employee experiences, logistical challenges, and sustainability initiatives, we gain a clear understanding of UNFI Richburg’s impact.
The facility’s ongoing efforts to address concerns and its vision for expansion suggest a promising trajectory, solidifying its place within the regional and national food distribution network.