Large food bags are indispensable in today’s food industry, serving as the primary packaging solution for a vast array of products. From the bulk transportation of grains to the individual packaging of pet food, these bags play a crucial role in preserving freshness, ensuring food safety, and streamlining distribution processes. Their versatility, durability, and cost-effectiveness make them a preferred choice for businesses of all sizes, significantly impacting how food reaches consumers worldwide.
This discussion delves into the multifaceted world of large food bags, exploring their diverse types, applications across various industries, and the innovative features that enhance their functionality. We will examine the materials used in their construction, the regulatory standards that govern their production, and the manufacturing processes involved. Furthermore, the emphasis will be placed on sustainability, cost considerations, and the emerging trends shaping the future of this essential packaging solution.
Types of Large Food Bags
Large food bags are essential for the storage, transportation, and distribution of bulk food products. These bags are designed to withstand significant weight and protect contents from environmental factors. Their construction varies significantly depending on the food item, desired shelf life, and handling requirements. Understanding the different types of large food bags is crucial for selecting the most appropriate packaging solution.
Materials Used in Manufacturing Large Food Bags
The materials used in manufacturing large food bags play a vital role in their performance characteristics. These materials determine the bag’s strength, durability, moisture barrier properties, and suitability for contact with food products. Several materials are commonly employed, each with distinct advantages and disadvantages.
- Polypropylene (PP): PP is a versatile thermoplastic polymer widely used in woven and non-woven forms for large food bags.
- Pros: High tensile strength, excellent resistance to chemicals and solvents, relatively low cost, and recyclable. Woven PP bags are particularly robust and resistant to tearing.
- Cons: Susceptible to UV degradation, and not as effective a moisture barrier as some other materials.
- Applications: Commonly used for pet food, animal feed, and agricultural products.
- Polyethylene (PE): PE, available in various densities (LDPE, HDPE), is another popular choice for large food bags, often used as liners within other bag types.
- Pros: Excellent moisture barrier properties, flexible, and relatively inexpensive. HDPE offers higher strength and stiffness than LDPE.
- Cons: Less resistant to punctures and tears compared to PP, and may not be suitable for all food products due to potential odor transfer.
- Applications: Used for flour, sugar, and other dry food products where moisture protection is critical.
- Multi-layer Paper: Multi-layer paper bags offer a natural and sustainable packaging solution, often combined with plastic films for enhanced performance.
- Pros: Renewable resource, good printability, and provides a barrier against light and oxygen.
- Cons: Less resistant to moisture compared to plastic, and can be more susceptible to tearing.
- Applications: Suitable for dry food products such as flour, grains, and pet food, especially when a biodegradable option is desired.
- Laminated Films: Laminated films combine multiple layers of different materials (e.g., PE, PP, aluminum foil) to create a bag with enhanced barrier properties.
- Pros: Excellent moisture, oxygen, and aroma barrier; can offer superior puncture resistance and durability.
- Cons: More expensive than single-layer materials, and recycling can be more complex due to the combination of materials.
- Applications: Ideal for food products that require extended shelf life, such as coffee, snacks, and pet food with high-fat content.
Examples of Large Food Bags for Specific Food Items
The design of large food bags is often tailored to the specific requirements of the food item they contain. This includes considerations for the food’s physical properties, storage conditions, and transportation needs. Here are some examples:
- Pet Food Bags: These bags typically feature robust woven PP or laminated film construction to withstand the weight of the product and protect against moisture and pests. They often incorporate a gusseted design for efficient stacking and filling, and may include features like handles for easy carrying. Some high-end pet food bags may also feature resealable closures to maintain freshness after opening.
- Flour Bags: Flour bags often utilize multi-layer paper or PE liners to protect the flour from moisture and contamination. The bags are designed to prevent sifting of the fine flour particles. They might also incorporate a valve for easy filling and dispensing.
- Grain Bags: Grain bags, designed for bulk storage of grains like wheat or corn, are usually made of woven PP for strength and durability. They are often designed to be breathable to prevent moisture buildup and spoilage. These bags may include a spout or bottom discharge for convenient unloading.
- Sugar Bags: Sugar bags frequently use PE liners within woven PP bags to prevent moisture absorption and sugar caking. They are designed to withstand the weight of the sugar and maintain its quality. The bags might have handles for easy transportation.
Comparison of Large Food Bag Types
Below is a table summarizing the different types of large food bags, comparing their materials, sizes, and intended uses.
Material | Size (Typical Capacity) | Intended Use | Key Features |
---|---|---|---|
Woven Polypropylene (PP) | 500kg – 2000kg | Pet Food, Animal Feed, Grains | High tensile strength, UV resistant, good for stacking, can be breathable |
Polyethylene (PE) Liner | 25kg – 100kg | Flour, Sugar, Dry Foods | Excellent moisture barrier, flexible, often used with paper or woven PP |
Multi-layer Paper | 10kg – 50kg | Flour, Grains, Dry Food | Good printability, barrier against light and oxygen, can be biodegradable |
Laminated Film | 5kg – 25kg | Coffee, Snacks, Pet Food (high fat) | Excellent moisture, oxygen, and aroma barrier, extended shelf life, resealable options |
Applications and Industries
Large food bags are indispensable across numerous industries, serving as a crucial component in packaging, storage, and distribution. Their versatility, durability, and cost-effectiveness make them a preferred choice for handling substantial volumes of food products. This section explores the key industries that heavily utilize these bags, their role in the supply chain, and the advantages they offer over alternative packaging solutions.
Industries Relying on Large Food Bags
Several industries depend on large food bags for efficient and effective operations. These bags provide a practical solution for handling bulk quantities of food products from manufacturing to retail.
- Agriculture: This sector utilizes large food bags extensively for storing and transporting grains (wheat, corn, rice), seeds, and animal feed. For instance, agricultural cooperatives often use these bags to store harvested crops before distribution.
- Food Processing: Food processing plants employ these bags for various ingredients such as flour, sugar, spices, and dried fruits. These bags are suitable for storing raw materials, as well as for holding intermediate products during the processing stages.
- Animal Feed Production: Manufacturers of animal feed rely on these bags for packaging and distributing feed products, including pellets, supplements, and ingredients like soy and corn meal. These bags protect the feed from contamination and maintain its quality during storage and transit.
- Dairy Industry: The dairy industry uses these bags for handling powdered milk, whey protein, and other dairy-based ingredients. These bags maintain product integrity and reduce the risk of spoilage.
- Pet Food Industry: Pet food manufacturers utilize large food bags for packaging dry pet food and treats. The bags are designed to maintain freshness and protect the product from moisture and pests.
- Bakeries and Confectioneries: These establishments utilize large food bags for ingredients like flour, sugar, and other bulk components. The bags facilitate efficient handling and storage of raw materials.
Role in the Supply Chain
Large food bags play a vital role in the food supply chain, supporting efficient handling, storage, and transportation of food products. Their impact is felt across all stages, from the point of manufacture to the final retail destination.
The process typically begins with the manufacturing of the bag itself, which is then transported to the food processing facility. The food product is then packaged into the large bags. These bags are then sealed and prepared for shipment. Transportation methods vary, often involving trucks, trains, or ships, depending on the distance and volume. Upon arrival at distribution centers or retail locations, the bags are either stored or directly sent to the point of sale.
Throughout this process, the bags protect the product from contamination and maintain its quality. For example, in the grain industry, large bags enable farmers to store their harvest efficiently, allowing them to sell their products over a longer period, thus stabilizing prices and ensuring a consistent supply. This also reduces waste by preventing spoilage.
Advantages Over Other Packaging Options
Large food bags offer several advantages over alternative packaging options, particularly for bulk quantities of food products. These advantages contribute to their widespread use across various industries.
- Cost-Effectiveness: Large food bags are often more cost-effective than rigid containers, such as drums or boxes, especially when handling large volumes. The material costs and manufacturing processes are generally lower.
- Durability and Protection: These bags are typically made from durable materials that protect food products from contamination, moisture, and pests. They can withstand rough handling during transportation and storage. For example, bags made from woven polypropylene are resistant to tearing and puncturing.
- Storage Efficiency: Large food bags can be easily stacked, optimizing storage space in warehouses and distribution centers. Their rectangular shape allows for efficient use of space.
- Flexibility and Versatility: These bags are available in various sizes, materials, and designs to accommodate different types of food products. They can be customized with features like liners, vents, and handles to meet specific requirements.
- Sustainability: Many large food bags are made from recyclable materials, and some are designed for reuse, contributing to reduced waste and environmental impact. Efforts are underway to develop bags from bio-based materials.
Regulations and Standards
The manufacturing and utilization of large food bags are subject to a complex framework of regulations and standards designed to ensure food safety, protect consumer health, and minimize environmental impact. These regulations govern various aspects, from the materials used in production to the disposal methods employed after use. Adherence to these standards is crucial for manufacturers and users alike, guaranteeing the integrity of the food supply chain and promoting sustainable practices.
Food Safety Regulations and Standards
Food safety regulations and standards dictate the permissible materials, manufacturing processes, and handling procedures for large food bags to prevent contamination and ensure product safety. These regulations vary by region and country, but the core principles remain consistent: safeguarding food from harmful substances and maintaining its quality.The United States, for example, relies heavily on regulations enforced by the Food and Drug Administration (FDA).
The FDA’s guidelines, specifically those related to food contact materials, are paramount. These regulations, detailed in the Code of Federal Regulations (CFR), Artikel acceptable substances and usage conditions for materials that come into direct contact with food.
- FDA 21 CFR Part 177: This section specifically addresses indirect food additives, including polymers and other materials used in the manufacture of food packaging. It provides a comprehensive list of substances that are approved for use and specifies limitations on their use. For instance, it might dictate the maximum allowable levels of certain additives or the types of foods with which a particular material can be used.
- Good Manufacturing Practices (GMP): GMP guidelines are critical in ensuring the quality and safety of food packaging production. These practices cover all aspects of the manufacturing process, from the cleanliness of the facility and equipment to the training of personnel. GMPs are designed to minimize the risk of contamination and ensure consistency in product quality.
- Migration Testing: This process assesses whether substances from the packaging materials migrate into the food product. The FDA and other regulatory bodies set limits on the amount of migration allowed, ensuring that the food remains safe for consumption. Various tests are performed to simulate real-world conditions, such as different food types, temperatures, and storage times.
In the European Union, similar regulations exist under the framework of the European Food Safety Authority (EFSA). The EU’s approach often focuses on a ‘positive list’ system, where only substances specifically authorized for food contact are permitted. Regulation (EC) No 1935/2004 is the cornerstone of this legislation, setting out general requirements for all food contact materials. Furthermore, specific regulations exist for different types of materials, such as plastics, with Regulation (EU) No 10/2011 establishing detailed rules for plastic materials and articles intended to come into contact with food.
This regulation provides specific migration limits for substances and includes lists of authorized substances.
- Overall Migration Limits (OML): These limits specify the maximum amount of any substance that can migrate from the packaging material into the food.
- Specific Migration Limits (SML): These limits apply to individual substances used in the packaging material.
These regulations necessitate that manufacturers conduct thorough testing and maintain detailed records to demonstrate compliance. Food businesses utilizing large food bags must also adhere to these regulations, ensuring that the bags are suitable for their intended use and that proper handling procedures are followed to maintain food safety.
Certifications and Accreditations
Certifications and accreditations play a pivotal role in verifying that manufacturers of large food bags meet specific quality and safety standards. These credentials provide assurance to consumers, retailers, and food processors that the bags are produced under controlled conditions and are suitable for their intended use. Obtaining these certifications often involves rigorous audits and inspections by independent third-party organizations.
- ISO 9001: This certification, awarded by the International Organization for Standardization (ISO), demonstrates a manufacturer’s commitment to quality management systems. It covers all aspects of the production process, from design and development to manufacturing and customer service. ISO 9001 certification signifies that a company has established and maintains a quality management system that meets international standards.
- ISO 22000: This certification focuses specifically on food safety management systems. It integrates the principles of HACCP (Hazard Analysis and Critical Control Points) and provides a framework for identifying and controlling food safety hazards. ISO 22000 certification demonstrates a company’s commitment to preventing foodborne illnesses.
- BRCGS Packaging Materials Certification: The BRCGS (Brand Reputation Compliance Global Standards) is a global standard for packaging and packaging materials. This certification covers a wide range of aspects, including food safety, quality, and operational criteria. It is widely recognized by retailers and food manufacturers worldwide.
- FSSC 22000: The Food Safety System Certification 22000 is a globally recognized certification scheme for food safety management systems. It is based on ISO 22000 and incorporates specific requirements for food packaging manufacturing. FSSC 22000 provides a comprehensive approach to managing food safety risks throughout the supply chain.
These certifications are often required by food processors and retailers as a prerequisite for doing business. They provide a level of assurance that the packaging meets the necessary standards for food safety and quality. The auditing process involves a detailed review of the manufacturer’s processes, documentation, and facilities, conducted by accredited certification bodies. Regular audits are conducted to ensure ongoing compliance.
Environmental Regulations and Compliance
Environmental regulations are increasingly influencing the production and disposal of large food bags. These regulations aim to reduce waste, promote sustainability, and minimize the environmental impact of packaging materials. Compliance with these regulations is essential for manufacturers and users to demonstrate their commitment to environmental responsibility.The specific regulations vary by region and country, but they generally address several key areas:
- Material Composition: Regulations may restrict the use of certain materials, such as non-recyclable plastics or those containing harmful substances. There is a growing emphasis on using recycled materials and designing packaging for recyclability. For example, some jurisdictions are implementing bans on single-use plastics or mandating minimum recycled content in packaging.
- Recycling and Waste Management: Regulations often establish requirements for recycling programs and waste management practices. This may include extended producer responsibility (EPR) schemes, where manufacturers are responsible for the collection and recycling of their packaging. These programs encourage manufacturers to design packaging that is easily recyclable and to support the infrastructure needed for recycling.
- Biodegradable and Compostable Materials: There is a growing interest in using biodegradable and compostable materials for food packaging. Regulations may specify the standards that these materials must meet to be certified as compostable. These materials are designed to break down naturally, reducing the amount of waste that ends up in landfills.
- Greenhouse Gas Emissions: Regulations may also address the environmental impact of manufacturing processes, including greenhouse gas emissions. This may involve implementing energy-efficient production methods and using renewable energy sources. Companies may be required to report their emissions and take steps to reduce their carbon footprint.
Compliance with environmental regulations often requires manufacturers to conduct life cycle assessments (LCAs) of their products. An LCA evaluates the environmental impact of a product throughout its entire life cycle, from raw material extraction to disposal. This information can be used to identify areas for improvement and to demonstrate the environmental benefits of the packaging.The European Union’s Packaging and Packaging Waste Directive (94/62/EC) is a key piece of legislation in this area.
It sets targets for recycling and recovery of packaging waste and encourages the use of recycled materials. Furthermore, the EU is implementing policies, such as the Single-Use Plastics Directive, to reduce the use of single-use plastics and promote the use of more sustainable alternatives.In the United States, the Environmental Protection Agency (EPA) plays a significant role in regulating waste management and promoting recycling.
While there is no single federal law that comprehensively addresses packaging waste, the EPA provides guidance and support for state and local recycling programs. Individual states and municipalities have also enacted their own regulations, such as extended producer responsibility laws and bans on single-use plastics.
Manufacturing Processes
The production of large food bags involves a series of intricate manufacturing processes, each contributing to the final product’s strength, durability, and suitability for food storage. These processes are carefully managed to ensure the bags meet stringent quality standards and regulatory requirements. From the initial selection of raw materials to the final sealing and inspection, every step is crucial in delivering a reliable and safe packaging solution.
Primary Manufacturing Processes
Several key processes are employed in the creation of large food bags. These processes are often integrated and customized based on the specific bag design, materials used, and desired performance characteristics.
- Extrusion: This process forms the foundation for many plastic-based bags. Raw plastic pellets are melted and forced through a die to create a film or sheet. This film can then be used directly to form the bag or be further processed. Extrusion is critical for producing the base material of many bag types, including those made from polyethylene or polypropylene.
- Printing: Printing allows for branding, product information, and other necessary details to be applied to the bag’s surface. Various printing methods, such as flexographic printing, are used, depending on the material and the desired print quality. Flexographic printing is a common method for large food bags due to its versatility and cost-effectiveness, particularly for printing on flexible films.
- Cutting: After printing and/or extrusion, the material is cut to the desired dimensions and shape. Precise cutting is essential for ensuring the bag’s structural integrity and accurate dimensions. This stage involves the use of specialized machinery that can handle the large format materials.
- Sealing: Sealing is the process of joining the bag’s edges to create a secure and airtight enclosure. Heat sealing, sewing, or a combination of methods are commonly used, depending on the bag’s design and the material. Heat sealing is a widely used method for creating strong and reliable seals in plastic bags.
- Weaving (for woven bags): For bags made from woven materials, such as woven polypropylene, the process involves weaving the plastic strands together to create a strong fabric. This fabric is then cut, printed, and sewn to form the bag. Weaving provides high tensile strength, making these bags suitable for heavy-duty applications.
Extrusion Process Steps
Extrusion is a fundamental process in manufacturing many types of large food bags, particularly those made from plastic materials. Here’s a detailed look at the steps involved:
- Material Preparation: Raw plastic pellets, typically polyethylene or polypropylene, are prepared. These pellets are often mixed with additives, such as UV stabilizers or colorants, to enhance the bag’s properties.
- Melting: The plastic pellets are fed into an extruder, where they are heated to their melting point. This process transforms the solid pellets into a molten state.
- Extrusion through a Die: The molten plastic is forced through a die, which shapes the plastic into a film or sheet. The die’s design determines the thickness and width of the film. For example, a flat die will produce a flat film, while a blown film die will create a tubular film.
- Cooling: The extruded film is cooled, typically using air or water, to solidify the plastic. This step is crucial for maintaining the film’s dimensions and properties. The cooling process must be carefully controlled to avoid defects.
- Slitting and Winding: The cooled film may be slit to the desired width and then wound onto rolls for further processing, such as printing or cutting. Slitting ensures that the film is the correct width for the bag’s design.
Quality Control Measures
Quality control is paramount in the production of large food bags. Stringent measures are implemented throughout the manufacturing process to ensure that the bags meet the required standards for safety, durability, and performance.
Quality control measures include:
- Raw Material Inspection: Checking the quality and purity of the raw materials, such as plastic pellets, to ensure they meet specifications.
- Extrusion Monitoring: Monitoring the extrusion process parameters, such as temperature, pressure, and film thickness, to ensure consistent film quality.
- Printing Inspection: Inspecting the print quality, including color accuracy, registration, and legibility, to ensure the printed information is clear and accurate.
- Cutting and Sealing Checks: Verifying the accuracy of cutting and the integrity of the seals to prevent leaks and ensure bag strength.
- Performance Testing: Conducting various tests, such as tensile strength, drop tests, and leak tests, to assess the bag’s performance and durability.
- Regular Audits: Conducting regular audits of the manufacturing processes and facilities to ensure compliance with quality standards and regulations.
Sustainability and Eco-Friendliness
The environmental impact of large food bags is a significant consideration in the food industry, given the volume of these bags used globally. Choosing materials and manufacturing processes that minimize waste and pollution is crucial for promoting sustainability. This section will explore the environmental consequences of various materials, examine sustainable alternatives, and detail the lifecycle of compostable bags.
Environmental Impact of Materials
The materials used in large food bags significantly affect their environmental footprint. The production, use, and disposal of these bags can contribute to pollution and resource depletion.
- Conventional Plastics (Polyethylene, Polypropylene): These are the most common materials. Their production relies heavily on fossil fuels, contributing to greenhouse gas emissions. They are also often not readily recyclable in standard recycling streams, leading to landfill accumulation and potential leakage into the environment, where they can persist for hundreds of years.
- Paper: While paper is a renewable resource, its production requires significant water and energy, and can contribute to deforestation if not sourced sustainably. Paper bags are often treated with coatings or additives that hinder recyclability.
- Multi-Layer Materials: Bags made from multiple layers of different materials (e.g., plastic, foil, and paper) offer enhanced barrier properties but are notoriously difficult to recycle due to the complexity of separating the layers. They often end up in landfills.
- Recyclability and Biodegradability: The recyclability of a material is its ability to be processed and reused. Biodegradability refers to a material’s capacity to break down naturally into the environment. Materials like polyethylene and polypropylene are recyclable, although the infrastructure for recycling these materials, especially in the context of large food bags, is often lacking. Biodegradable materials, such as certain types of bioplastics and compostable paper, can decompose in specific environments, reducing their long-term impact.
Sustainable Alternatives to Conventional Large Food Bags
Several sustainable alternatives are emerging to reduce the environmental impact of large food bags. These options focus on using renewable resources, reducing waste, and promoting circularity.
- Bags Made from Recycled Materials: Utilizing recycled plastics, such as post-consumer recycled polyethylene (rPE) or polypropylene (rPP), reduces the demand for virgin plastics and diverts waste from landfills. These bags can be made with similar properties to virgin plastic bags, providing comparable performance. For example, a company could use recycled plastic bottles to create the bags.
- Bags Made from Biodegradable Plastics: These plastics, often derived from renewable resources like corn starch (PLA – Polylactic Acid) or other plant-based materials, are designed to break down in specific environments. It is important to distinguish between biodegradable and compostable. Biodegradable plastics may break down in landfills, but not necessarily quickly or completely. Compostable plastics are designed to break down in composting facilities.
- Compostable Bags: These bags are made from materials like compostable films or paper and are designed to break down in industrial composting facilities, returning nutrients to the soil. Compostable bags must meet specific standards, such as those set by the Biodegradable Products Institute (BPI), to ensure they break down completely and safely.
- Reusable Bags: While not always applicable to the bulk packaging of food products, reusable bags, often made from durable materials like woven polypropylene or canvas, can reduce waste in certain applications, such as for transporting bulk food items.
Lifecycle of a Compostable Large Food Bag
The lifecycle of a compostable large food bag is designed to minimize environmental impact, from production to disposal. Understanding this lifecycle helps appreciate the benefits of these bags.
- Production: The bag is manufactured from compostable materials, such as PLA derived from corn starch or other plant-based materials. The manufacturing process aims to minimize energy consumption and waste generation. The bag’s design considers the need for printing with eco-friendly inks and adhesives that do not hinder the composting process.
- Use Phase: The bag is used to store and transport food products. It’s important to note that compostable bags should be stored in a dry environment to prevent premature degradation.
- Composting: After use, the bag is disposed of in an industrial composting facility or a home composting system (if the bag is certified for home composting). In the composting environment, the bag is exposed to heat, moisture, and microorganisms, which break down the material.
- Decomposition: The microorganisms consume the compostable material, converting it into water, carbon dioxide, and nutrient-rich compost. This process typically takes a few weeks to a few months, depending on the composting conditions.
- End Product: The resulting compost can be used as a soil amendment to enrich gardens, farms, and landscaping projects. This closes the loop, returning nutrients to the soil and reducing the need for synthetic fertilizers.
Storage and Handling
Proper storage and handling are critical for maintaining the quality, safety, and shelf life of large food bags. Incorrect practices can lead to product spoilage, contamination, and significant economic losses. Implementing best practices throughout the supply chain, from the manufacturer to the end-user, is essential for ensuring food safety and minimizing waste.
Browse the multiple elements of heartland cat food reviews to gain a more broad understanding.
Best Practices for Storing Large Food Bags
Effective storage is crucial to prevent spoilage and preserve the integrity of the food product. Several factors influence the optimal storage environment, including temperature, humidity, and protection from contaminants.
- Temperature Control: Maintaining the correct temperature is paramount. The specific temperature requirements vary depending on the food product. For example, dry goods such as grains and flours should be stored in a cool, dry place, ideally below 21°C (70°F) and with a relative humidity of less than 60%. Perishable items, such as certain types of produce or prepared foods, require refrigerated or frozen storage to inhibit microbial growth and enzymatic reactions.
Temperature monitoring systems should be in place to track and record temperature fluctuations.
- Humidity Control: High humidity can lead to the growth of mold, mildew, and the deterioration of packaging materials. Storing bags in a dry environment is crucial. Desiccant packs can be used inside the bags to absorb excess moisture, particularly for products sensitive to humidity. Consider the use of dehumidifiers in storage facilities.
- Protection from Contaminants: Large food bags must be protected from pests, rodents, and other contaminants. This includes proper building maintenance, regular pest control measures, and the use of sealed storage containers or pallets. Bags should be stored off the floor to prevent moisture absorption and facilitate cleaning. Avoid storing bags near chemicals, cleaning agents, or other materials that could contaminate the food product.
- Proper Ventilation: Adequate ventilation is important to prevent moisture buildup and maintain a consistent temperature. Ensure that storage areas have sufficient airflow. Avoid overcrowding storage areas, which can restrict airflow and increase the risk of spoilage.
- First-In, First-Out (FIFO) Inventory Management: Implementing a FIFO system is essential for minimizing the risk of spoilage due to prolonged storage. This ensures that older products are used before newer ones, reducing the likelihood of exceeding the product’s shelf life. Clearly label bags with dates of production or receipt.
Safe Handling and Transportation of Large Food Bags
Safe handling and transportation practices are critical for preventing damage to the bags, product contamination, and worker injuries. This involves careful loading, unloading, and movement of the bags throughout the supply chain.
- Loading Procedures: Bags should be loaded onto pallets or into transport vehicles carefully to prevent damage. Avoid dropping, dragging, or throwing bags. Use appropriate lifting equipment, such as forklifts or pallet jacks, and ensure that operators are properly trained in their use. Consider the bag’s weight capacity and dimensions when loading. Distribute the weight evenly to maintain stability during transit.
- Unloading Procedures: Unloading procedures should mirror the loading procedures. Use appropriate equipment and trained personnel. Inspect bags for any signs of damage, such as tears, punctures, or moisture damage, during unloading. Remove damaged bags immediately and dispose of them according to food safety regulations.
- Transportation Considerations: Choose appropriate transport vehicles that are clean, dry, and free from contaminants. Ensure that the bags are properly secured during transit to prevent shifting and damage. Temperature-controlled transportation may be necessary for perishable goods. Monitor the temperature of the cargo during transport and maintain records.
- Employee Training: Provide comprehensive training to all employees involved in handling large food bags. Training should cover proper lifting techniques, the use of handling equipment, and food safety protocols. Regular refresher courses are essential to reinforce best practices and address any safety concerns.
- Equipment Maintenance: Regularly inspect and maintain all handling equipment, such as forklifts, pallet jacks, and conveyors. Ensure that equipment is in good working order and free from defects that could compromise safety or damage the bags.
Importance of Proper Storage and Handling
Proper storage and handling practices directly impact product quality, shelf life, and the overall profitability of the food supply chain. Failure to adhere to these practices can result in significant losses.
- Minimizing Waste: Proper storage and handling practices significantly reduce food waste. By preventing spoilage, damage, and contamination, companies can ensure that more product reaches consumers. This reduces the economic and environmental costs associated with food waste.
- Maximizing Shelf Life: Optimal storage conditions extend the shelf life of food products. This allows for longer distribution times, reduces the frequency of product recalls, and increases consumer satisfaction.
- Ensuring Food Safety: Proper handling and storage practices are essential for maintaining food safety. This includes preventing contamination from pests, microorganisms, and other sources. Adhering to food safety regulations and standards is crucial for protecting public health.
- Reducing Costs: By minimizing waste, extending shelf life, and preventing product recalls, proper storage and handling practices contribute to cost savings. This includes reducing the costs associated with spoilage, disposal, and potential legal liabilities.
- Maintaining Product Quality: Proper storage and handling help preserve the nutritional value, flavor, and appearance of food products. This enhances consumer satisfaction and builds brand loyalty. For example, storing fresh produce at the correct temperature and humidity can prevent wilting, bruising, and loss of nutrients.
Innovations and Future Trends
The large food bag sector is continually evolving, driven by consumer demand, environmental concerns, and technological advancements. Innovation plays a critical role in improving functionality, sustainability, and overall efficiency. Emerging technologies are reshaping the design, manufacturing, and application of these essential packaging solutions.
Emerging Technologies and Innovations in Design and Manufacturing
Several key areas are witnessing significant innovation, leading to more effective and sustainable large food bags. These advancements aim to enhance product protection, reduce environmental impact, and improve supply chain efficiency.
- Advanced Materials: Research and development focus on utilizing novel materials to enhance bag performance. This includes:
- Bio-based Polymers: The use of materials derived from renewable resources like cornstarch, sugarcane, and algae is expanding. These polymers offer biodegradability and compostability, reducing reliance on fossil fuels. For example, companies like NatureWorks produce Ingeo, a PLA (polylactic acid) bioplastic used in various packaging applications, including some food bags.
- Recycled Plastics: Incorporating recycled content into bag manufacturing is increasing. This reduces waste and lowers the carbon footprint. Advanced recycling technologies are making it possible to recycle a wider range of plastics, including those that were previously difficult to process.
- Composite Materials: Combining different materials to create bags with superior properties. For instance, layering bio-based films with barrier films can enhance protection against moisture, oxygen, and light, extending the shelf life of food products.
- Smart Packaging Technologies: Integrating technology into packaging provides real-time data and enhanced functionality. This includes:
- Printed Electronics: Applying electronic circuits directly onto the bag surface allows for features such as temperature monitoring and freshness indicators.
- RFID (Radio-Frequency Identification) Tags: Embedding RFID tags enables tracking and tracing products throughout the supply chain, improving inventory management and reducing waste.
- NFC (Near Field Communication) Technology: NFC chips can provide consumers with information about the product, including origin, ingredients, and recycling instructions, by simply tapping their smartphones on the bag.
- Manufacturing Process Optimization: Innovations in manufacturing are aimed at increasing efficiency, reducing waste, and improving the overall sustainability of production.
- 3D Printing: 3D printing is used for prototyping and customized bag designs. It can also be employed for creating specialized bag features or closures.
- Automation and Robotics: Automating manufacturing processes improves efficiency and reduces labor costs. Robots can handle tasks such as bag filling, sealing, and palletizing, increasing throughput and minimizing errors.
- Digital Printing: Digital printing offers greater flexibility and customization options compared to traditional printing methods. It allows for variable data printing, enabling personalized packaging and enhanced traceability.
Potential Impact of Innovations on the Food Industry
These innovations are poised to revolutionize the food industry, offering significant benefits to manufacturers, retailers, and consumers.
- Enhanced Product Protection and Shelf Life: Advanced materials and barrier technologies will significantly improve the protection of food products from environmental factors like moisture, oxygen, and light. This will extend shelf life, reduce food spoilage, and minimize waste.
- Improved Supply Chain Efficiency: Smart packaging technologies, such as RFID and NFC, will streamline supply chain operations. Real-time tracking and tracing will enable better inventory management, reduce losses due to damage or spoilage, and improve overall efficiency.
- Reduced Environmental Impact: The adoption of bio-based polymers, recycled plastics, and sustainable manufacturing processes will significantly reduce the environmental footprint of large food bags. This includes decreasing reliance on fossil fuels, minimizing waste, and lowering greenhouse gas emissions.
- Increased Consumer Engagement: Smart packaging provides opportunities for enhanced consumer engagement. Features like QR codes, NFC tags, and interactive packaging can provide consumers with valuable information about the product, including its origin, ingredients, and recycling instructions.
- Cost Savings: While initial investments in new technologies may be necessary, the long-term benefits, such as reduced waste, improved efficiency, and optimized supply chain operations, can lead to significant cost savings for food manufacturers and retailers.
Futuristic Large Food Bag Design with Smart Technology, Large food bags
Imagine a large food bag designed for bulk storage of grains, featuring a sleek, durable, and environmentally friendly construction. The bag would be made from a combination of bio-based polymers and recycled plastics, with integrated smart technology for enhanced functionality.
- Material Composition: The outer layer would consist of a durable, tear-resistant bio-based polymer derived from sugarcane. A middle layer made from recycled polyethylene provides a moisture barrier. An inner layer made from a compostable film ensures food safety.
- Smart Technology Integration:
- Embedded Sensors: Micro-sensors are embedded within the bag to monitor key parameters such as temperature, humidity, and oxygen levels.
- Real-time Monitoring: A built-in NFC chip transmits data from the sensors to a smartphone app or a central monitoring system.
- Freshness Indicators: Color-changing indicators provide a visual signal of food freshness.
- Automated Reporting: The system automatically generates reports on storage conditions and potential spoilage risks.
- Design Features:
- Modular Design: The bag features a modular design, allowing for easy customization of size and capacity.
- Self-Sealing Closure: A self-sealing closure mechanism ensures airtight sealing and prevents contamination.
- Integrated Handles: Ergonomic handles facilitate easy handling and transportation.
- Recycling Instructions: Clear recycling instructions are printed directly on the bag, along with a QR code linking to detailed information about recycling programs.
- Impact: This futuristic bag design would revolutionize food storage, reducing waste, enhancing food safety, and empowering consumers with real-time information about the products they purchase.
Cost Considerations
Understanding the cost implications of large food bags is crucial for businesses involved in food distribution, processing, and storage. Several factors contribute to the overall expense, impacting profitability and operational efficiency. Careful analysis of these costs allows for informed decision-making regarding bag selection, procurement, and usage.
Factors Influencing Bag Cost
Several variables directly impact the final cost of large food bags. Material selection, bag size, manufacturing processes, and order volume all play significant roles.
- Material Type: The base material is a primary cost driver. Polypropylene (PP), polyethylene (PE), and multi-layered films have varying price points. For example, virgin resins are generally more expensive than recycled materials, although the price difference can fluctuate based on market dynamics and supply chain availability.
- Bag Size and Dimensions: Larger bags require more material, directly increasing costs. Additionally, custom sizes and shapes, tailored to specific food products or packaging requirements, can add to the expense.
- Manufacturing Process: The complexity of the manufacturing process influences costs. Bags with specialized features, such as gussets, liners, or printing, require more sophisticated equipment and labor, leading to higher prices.
- Printing and Branding: Adding logos, product information, and other branding elements increases costs. The number of colors, printing method (flexographic, rotogravure, etc.), and print coverage all affect the final price.
- Order Volume: Bulk orders typically result in lower per-unit costs due to economies of scale in manufacturing and material procurement. Conversely, smaller orders usually incur higher prices.
- Regional Factors: Shipping costs, import duties, and local labor rates also contribute to the overall cost. The geographical location of the manufacturer and the end user significantly influence the final price.
Comparison of Bag Materials and Designs
Different materials and bag designs offer varying cost profiles. Choosing the most suitable option involves balancing cost with performance requirements, such as strength, barrier properties, and sustainability considerations.
- Polypropylene (PP) Bags: PP bags are a cost-effective option for dry food products like grains, seeds, and pet food. They offer good strength and barrier properties. Woven PP bags are typically less expensive than laminated PP bags.
- Polyethylene (PE) Bags: PE bags are often used for frozen foods and liquids due to their excellent moisture resistance. They can be produced in various thicknesses, affecting their cost. High-density polyethylene (HDPE) is generally more cost-effective than low-density polyethylene (LDPE).
- Multi-Layered Film Bags: These bags offer superior barrier properties, protecting food products from oxygen, moisture, and light. They are often more expensive than single-layer bags due to the complex manufacturing process and the use of multiple materials.
- Bag Designs: Different bag designs, such as gusseted bags, stand-up pouches, and valve bags, have varying cost implications. Gusseted bags, for example, can offer increased volume capacity but may be more expensive than simpler designs. Stand-up pouches often require specialized machinery, which increases their cost.
Cost Breakdown in Food Distribution
The use of large food bags in a food distribution business involves several cost components, including bag procurement, filling and sealing, storage, transportation, and waste disposal. Understanding these costs is crucial for optimizing operational efficiency and profitability.
- Bag Procurement Cost: This is the initial cost of purchasing the bags, which is influenced by the factors discussed above.
- Filling and Sealing Costs: These costs include labor, equipment, and energy expenses associated with filling the bags with food products and sealing them properly. Automated filling and sealing systems can reduce labor costs but require a significant initial investment.
- Storage Costs: The cost of storing filled bags includes warehouse space, climate control (if required), and labor for inventory management.
- Transportation Costs: Transportation costs are influenced by the weight and volume of the filled bags, the distance traveled, and the mode of transportation. Optimizing bag size and packaging efficiency can help reduce transportation costs.
- Waste Disposal Costs: The cost of disposing of used bags, including recycling or landfill fees, is a factor. The use of recyclable or compostable bags can help reduce these costs and promote sustainability.
To illustrate, consider a hypothetical food distribution company handling bulk grains. The company currently uses woven PP bags. By switching to laminated PP bags, which offer better moisture resistance, the company might experience a 15% increase in bag procurement costs. However, this investment could reduce product spoilage by 10%, potentially offsetting the increased bag cost. Furthermore, implementing a more efficient filling and sealing system could reduce labor costs by 20%, leading to overall cost savings.
Market Analysis and Trends
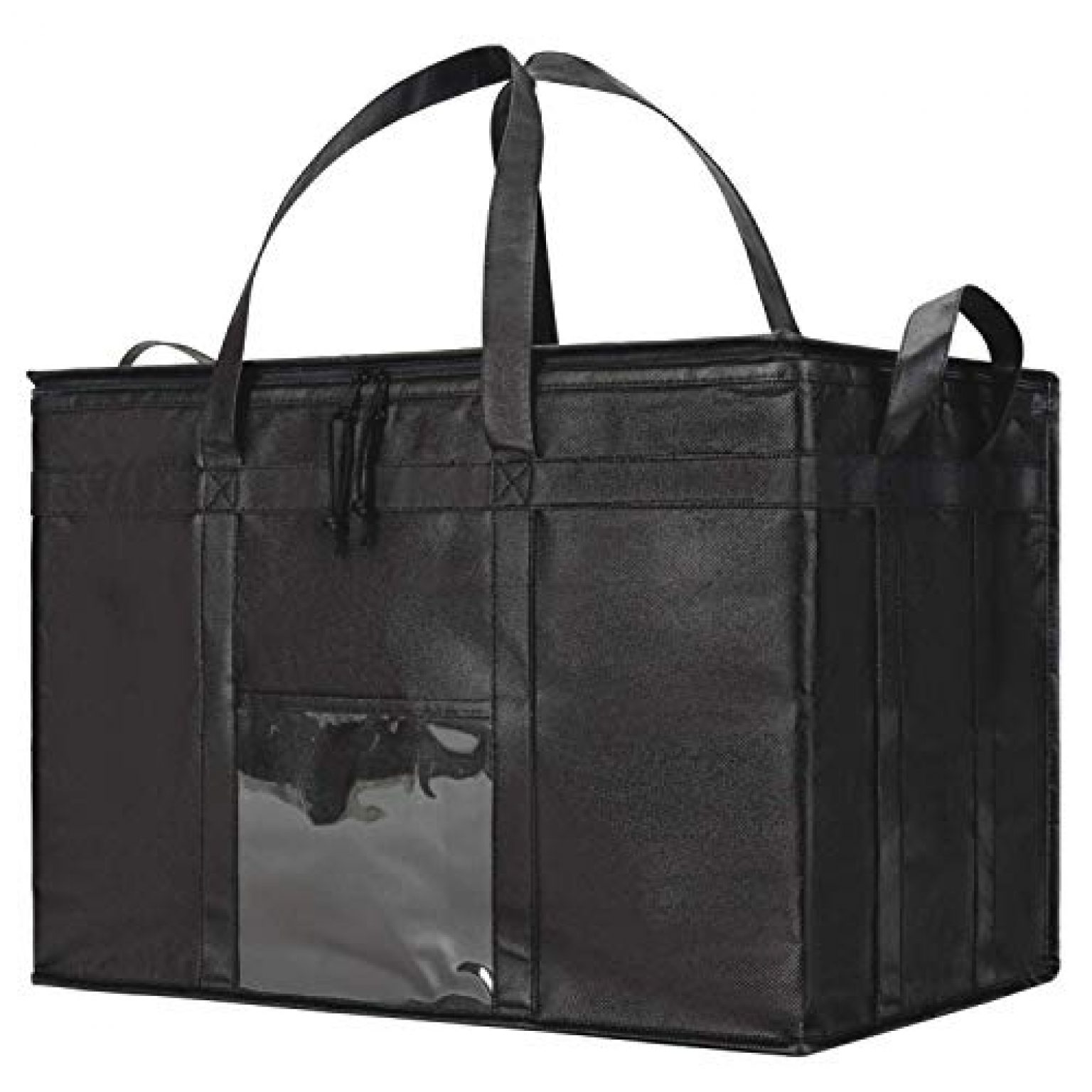
The market for large food bags is dynamic, shaped by evolving consumer preferences, supply chain complexities, and sustainability concerns. Understanding current market trends is crucial for manufacturers, distributors, and end-users to make informed decisions and capitalize on emerging opportunities. This section delves into the current landscape, examining growth segments, and global usage patterns.
Current Market Trends
Several key trends are currently driving the demand for large food bags. These trends reflect shifts in consumer behavior, technological advancements, and regulatory pressures.
- Increased Demand for Bulk Food Products: Consumers are increasingly purchasing food in bulk to save money, reduce packaging waste, and accommodate larger households. This trend is particularly noticeable in the retail and foodservice sectors.
- Growing E-commerce in Food Delivery: The expansion of online food delivery services has created a surge in demand for bags capable of safely transporting food items. Large food bags are essential for maintaining food integrity and hygiene during delivery.
- Focus on Sustainability and Eco-Friendliness: There is a rising consumer preference for environmentally friendly packaging solutions. This includes bags made from recycled materials, biodegradable options, and those designed for reusability. This has led to increased innovation in bag materials and designs.
- Supply Chain Optimization: Businesses are continually seeking ways to streamline their supply chains. Large food bags play a crucial role in efficiently storing, transporting, and distributing food products, reducing waste and improving logistics.
- Regulatory Compliance: Stringent food safety regulations are driving the adoption of high-quality, food-grade bags that meet specific standards for safety and hygiene. Compliance with these regulations is essential for market access and consumer trust.
Growth of Specific Market Segments
Certain market segments are experiencing significant growth in the utilization of large food bags. This growth is often tied to specific industry dynamics and consumer demands.
- Retail Food: The retail food sector, including supermarkets, hypermarkets, and convenience stores, is a major consumer of large food bags. Growth in this segment is fueled by bulk purchases, the expansion of private-label brands, and the increasing availability of pre-packaged food items.
- Foodservice and Catering: The foodservice and catering industries rely heavily on large food bags for transporting and storing ingredients, prepared meals, and bulk food supplies. The expansion of these sectors, driven by increased dining out and food delivery services, is boosting demand.
- Agriculture and Farming: Large food bags are essential for storing and transporting agricultural products such as grains, seeds, and animal feed. Growth in this segment is driven by increasing global food production and the need for efficient storage solutions.
- Food Processing: Food processing facilities utilize large food bags for various applications, including the storage and transportation of raw materials, ingredients, and finished products. The growth of the food processing industry is directly linked to the demand for these bags.
- Specialty Foods: The specialty food market, encompassing products such as coffee beans, spices, and dried fruits, is experiencing robust growth. Large food bags are crucial for maintaining the quality, freshness, and shelf life of these premium products.
Global Distribution of Large Food Bag Usage
The global distribution of large food bag usage across various industries varies significantly, reflecting regional economic activity, consumption patterns, and industrial infrastructure.
Illustration Description:
The illustration depicts a world map divided into several regions: North America, South America, Europe, Asia-Pacific, Africa, and the Middle East. Each region is color-coded to represent the relative usage of large food bags across different industries. The color intensity reflects the level of consumption, with darker shades indicating higher usage. Key industries, such as retail food, foodservice, agriculture, food processing, and specialty foods, are represented by distinct icons or symbols, strategically placed within each region to indicate their respective contributions to bag usage.
For example, a supermarket icon may be prominently displayed in North America and Europe, signifying the high demand from the retail sector. The illustration also includes a legend that clearly defines the color-coding and the meaning of each icon, allowing for easy interpretation of the data. Additionally, the illustration incorporates data points such as estimated annual bag consumption in each region and projected growth rates, providing a comprehensive overview of the global market landscape.
Arrows or lines illustrate trade routes, showcasing the movement of food products and bags across borders. Finally, the illustration provides a title: “Global Distribution of Large Food Bag Usage Across Various Industries.”
Detailed Regional Breakdown:
- North America: Dominated by the retail food and food processing sectors. High demand driven by large-scale supermarkets and extensive food processing operations. Strong emphasis on sustainable packaging solutions.
- Europe: Significant usage across retail, foodservice, and agriculture. Focus on stringent food safety regulations and the adoption of eco-friendly bag options.
- Asia-Pacific: Rapid growth driven by the expanding economies of China and India. High demand from the retail, agriculture, and food processing industries. Increasing adoption of advanced packaging technologies.
- South America: Moderate usage, with agriculture and food processing as key drivers. Growing demand for cost-effective and durable packaging solutions.
- Africa: Emerging market with increasing demand from the agricultural sector. Focus on improving storage and transportation infrastructure.
- Middle East: Strong demand from the foodservice and retail sectors, driven by the growth of the hospitality industry and increasing consumer spending on food.
Conclusive Thoughts: Large Food Bags
In conclusion, large food bags represent a critical component of the food supply chain, evolving to meet the demands of a changing world. From understanding the materials and design elements to appreciating the role of sustainability and future innovations, this exploration has illuminated the significant impact of these bags. As technology advances and consumer preferences shift, large food bags will continue to adapt, playing a pivotal role in ensuring food safety, efficiency, and environmental responsibility for years to come.